
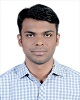
- Open Access
- Authors : Rakesh Ashok Pustode , Abhijeet Gaike , K. Phaneesh , Kedar Kanase
- Paper ID : IJERTV9IS030482
- Volume & Issue : Volume 09, Issue 03 (March 2020)
- Published (First Online): 30-03-2020
- ISSN (Online) : 2278-0181
- Publisher Name : IJERT
- License:
This work is licensed under a Creative Commons Attribution 4.0 International License
1D Analysis for Marine Application (Modelling of Ship in GT Suite for Evaluation of Performance Parameters)
Rakesh Ashok Pustode Assistant Manager, Advance Engineering Dept.
Greaves Cotton Limited Pune
Abhijeet Gaike
Assistant Manager, Industrial Engine Business
Greaves Cotton Limited Pune
K. Phaneesh Assistant General Manager, Advance Engineering Dept. Greaves Cotton Limited Pune
Kedar Kanase Senior General Manager, Advance Engineering Dept. Greaves Cotton Limited Pune
AbstractThe performance of a ship vessel is very important in deciding the kind of engine, turbine, thrust force and importantly the launch speed and cursing speed matching. There are different approach for the same and one of the approach is to define the same by 1D model approach. 1D model gives flexibility in analysis also with approach for solving complicated equations. The results can be correlated with that of test results and modifications can be done in model. This will give necessary flexibility in designing new ship and its requirements.
This work is divided in different steps; first step involves modeling the ship in GT suite which is the first time activity, second step involves the correlation of the 1D model with the real case scenario.
Main output of this analysis is knowing the proper engine size for the required thrust of the ship. This was done by studying the parameters like ship speed, engine speed, Fuel consumption, clutch engagement and disengagement, power, torque, distance travelled by the ship.
KeywordsGT suite, Thrust, Torque, Resistance, Propeller pitch.
-
INTRODUCTION
Virtual calibration is picking up its pace and used extensively in all new fields. In current world the simulation technique is used extensively from AI to calibration. This will help to carry out multiple iteration and to arrive out an optimum solution. With 1D and combination of 3D co- simulation the solution will be near to perfection and multi variables can be analysed. One such field where 1D model development is associated is in marine section. Greaves has its own marine division and its aiming to supply world class product to end customer requirements.
The key aspect ship modelling is the behavior of the propulsion system which is the crucial part while designing and optimizing it. Generally, this analysis has to be done in transient condition which can predict the acceleration, deceleration, turning events where the propulsion system is tested to its limit.
In present paper the ship is modelled with the help of 1D Tool GT suite. This is done by vast library present which can be used for building the initial blocks and defining the equations and then integrating this blocks and equations to
replicate the ship model which would predict the performance of the physical ship.
As ship can be considered similar to the on road vehicle except the medium on which it is driven, so most of the GT module which can be used for the vehicle modelling is used and the remaining part is modelled in the form of different controllers.
Current analysis is to propel a ship of 32 tons weight and to use the current engine with combination. Dual 4-cylinder engine delivering power of 170HP @ 2000rpm is modelled. The output of the analysis is correlated between test and the virtual simulation for ship speed in transient condition, distance travelled.
-
LITRATURE STUDY
This is an important step and this will give us an window of knowledge on how other team is progressing in this field. Some correlation can also be done with reference to physics of problem.
M Figari and M Altosole [1] has analytical study were they predicted the performance using analytical equations. According to them model including two non-linear differential equations of motion representing ship dynamics and propulsion plant dynamics was built. Paper shows that a ship with a GT propulsion plant and with a humped resistance curve has two types of behavior: a stable behavior and an unstable behavior, depending on the speed range. The presence of an unstable working range presents a concern from the system design point of view.
Haiyan Wang, Huiyan Tang, Jianhui Sun [2] also performed the modeling and simulation for ship Maneuvering condition. The dynamic simulation models of propeller running across four quadrants and ship longitudinal motion were given. The model concerns in all working conditions, including starting, braking, reversing, etc. Combination simulating of diesel propulsion system and ship motion was conducted. Difference between residuary resistance simulated and real residuary resistance, there were relative errors.
Thom Trentelman, Joshua Sutherland, Kazuya Oizumi, Kazuhiro Aoyama [3] describes a method for early stage boat design by creating and utilizing a library of naval architecture
based boat components in Modelica. Even without detailed domain knowledge of naval architecture a user was able to assemble and compare different models. By using Modelica s object oriented features the methodology enables radical or minor changes to a simulation model with one mouse-click. With the possibility to directly run a 3D animation of the simulation model the reaction to these changes can be reviewed immediately.
Fig. 1. Diagram view of Systems
-
SHIP MODELLING AND EQUATIONS USED Model architecture is same as the basic vehicle
architecture. Instead of vehicle ship is been model to follow the basic concept of marine engineering.
Fig. 2. Ship Model
Model has been made by using various equation for the thrust and torque which will be used to calculate the boat velocity and distance travelled.
Equation used for the modelling are:
-
Effective Thrust is given by Tp = Ktn2D4
-
Effective Torque is given by Qp = Kqn2D4
Here thrust coefficient Kt and torque coefficient Kq are functions of the advance coefficient J and propeller Pitch (or pitch diameter ratio).
-
Coefficient J is calculated as Va/nD
Generally, this should be available from the open water propeller test but here as the testing data was not available so the value taken from the literature example.
Where:
Tp = Propulsor Thrust (N) Tq = Torque (N)
Kt = Thrust Coefficient
Kq = Torque Coefficient N = Shaft speed (r/min)
D = Propeller diameter (m)
Va = Advance velocity = V (1- ) (m/s) = Sea water density (kg/m3)
Once the Ship has been Dynamics has been modelled next part is velocity and distance calculation.
This is calculated from the available thrust, resistance and mass of the ship.
We know that,
-
Force = mass * acceleration
-
Acceleration =Force/ Mass
-
Force = (Thrust- Resistance)
-
Resistance is available for the example model, as per the assumption the resistance is divided 2 times to match with the current ship condition
-
Acceleration = (Thrust Resistance)/ Ship mass (m/s2)
-
Integrating Acceleration will give the Velocity in m/s.
-
Integrating the velocity further will give distance travelled by the ship in m.
-
Inputs Used
-
Gear box Reduction Ratio = 2.06
-
Engine Inertia = 1.61 kg/m3
-
Ship weight = 32000 kg
-
Propeller Diameter = 620 mm
-
FTP data available for Torque
-
2 engines are present of same configuration
-
Engine: 4GTA_170HP@2000RPM Inline
-
-
Assumptions
-
Resistance map is scaled downas the data available was for bigger ship.
-
Fuel map used is dummy map
-
Resistance data is based on the example model
-
-
Input Graph
Fig. 3. Resistance Graph
Fig. 4. Thrust Coefficient Graph
Fig. 5. Torque Coefficient Graph
Fig. 6. Target Ship Speed
Fig. 7. Torque Map
-
Since the full load data was available so the torque data at 0% load is assumed.
-
Fuel consumption Graph is dummy graph taken from GT example model, so the fuel consumption results cannot be correlated with the actual results.
-
FMEP data was not available so it was ignored while building the model
-
-
GT suite Model
Fig. 9. Detail GT Model
Modelling in GT suite is done by using various controller and switches. Since GT has a vast library of different controls the modelling of equation is easy part.
Once this equation is modelled in GT then connection has to be established to make a flow path. Flow should start from the engine and the feedback should to given back to the engine. Feedback signal receives the signal from the thrust and the input velocity profile given to the driver controls.
Here only forward cursing of the ship has been modelled.
Accelerator input is based on the speed input given.
-
-
RESULTS
-
Velocity
Fig. 8. GT Model
-
Test Data is in Correlation with the Simulation Data
-
-
Ship speed and Engine speed
-
Here the engine speed is below the idle condition, idling speed is above 600rpm, but after 300sec we can see that engine is responding in reference to the vehicle speed.
-
-
Ship Speed and Fuel Consumption
-
This graph is only for reference purpose as the Fuel consumption map used is dummy map as referred from Ricardo model. Once test fuel data is available so fuel consumption can be predicted accurately.
-
-
Clutch Engagment
-
Clutch is Engaged through-out the cycle.
-
-
Power
-
Max power obtained is 122Hp @600sec for 1527rpm
-
-
Torque
-
Max torque obtained is 570Nm @600sec for 1527rpm
-
-
Torque
-
Max Thrust obtained is 45561 N.
-
-
Distance Travelled
-
Distance covered for the given ship travel is 2Km
-
-
-
CONCLUSION
-
Able to perform ship modelling in GT suite, results are comparable with real case scenario.
-
From the results is can be observed that the results variation for Thrust, Velocity and Distance are within
±5% range.
-
With proper engine map and measured ship resistance data the results can be improved which will result in less error in simulation result, hence if
proper fuel economy map is provided it also can be predicted properly.
-
PID Controllers are used to convert the equations to the executable format.
-
Literature study has helped in this simulation for modelling of different equation used to control the ship architecture.
ACKNOWLEDGMENT
The Author would like to thank 1) Dr. Ravi Damodaran, Chief technical officer, Research and development, Greaves cotton for his guidance throughout the project and his vision in building team with simulation capability 2) Mr. Amol Relkar (Sr. GM) Power and Industrial Engine department, Greaves cotton limited, 3) Mr. Rajendra Chandola (AGM)
Application Engineering, Greaves cotton limited for giving the opportunity to work on this project.
REFERENCES
-
M Figari and M Altosole, Dynamic behaviour and stability of marine propulsion systems, Naval Architecture and Marine Engineering (DINAV), Universita` di Genova, Genova, Italy, 22 June 2007.pp 187- 209
-
Haiyan Wang, Huiyan Tang, Jianhui Sun, Modeling and Simulation of Marine Diesel Propulsion System in Ship Maneuvering Condition, Advanced Materials Research Vols 354-355 (2012) pp 472-477.
-
Thom Trentelman, Joshua Sutherland, Kazuya Oizumi, Kazuhiro Aoyama, Modelica Based Naval Architecture Library for Small Autonomous Boat Design, Proceedings of the 12th International Modelica Conference May 15-17, 2017, Prague, Czech Republic, pp. 643-652.
-
M. Altosole and M. Figari, Effective simple methods for numerical modelling of marine engines in ship propulsion control systems design, Journal of Naval Architecture and Marine Engineering,December, 2011.