
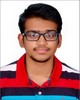
- Open Access
- Authors : Nikhil Gupta , Parv Jain , Sanika Prakash , Ayush Srivastava
- Paper ID : IJERTV11IS070241
- Volume & Issue : Volume 11, Issue 07 (July 2022)
- Published (First Online): 05-08-2022
- ISSN (Online) : 2278-0181
- Publisher Name : IJERT
- License:
This work is licensed under a Creative Commons Attribution 4.0 International License
3D Printed Prosthetic ARM
Nikhil Gupta Department of Electronics and Communication.
Parv Jain
Department of Electronics and Communication.
Sanika Prakash Department of Electronics and Communication.
Ayush Srivastava Department of Electronics and Communication
R.V. College of Engineering. R.V. College of Engineering. Bengaluru, India. Bengaluru, India.
R.V. College of Engineering. Bengaluru, India.
-
College of Engineering. Bengaluru, India.
Abstract The drive behind this project is to help patients who have lost their hands in accidents or are chronically diagnosed with a disease or birth defect. The prosthetic arm will be lightweight, with improved actuation speed, and will be capable of performing sufficient functionalities. It will be 3D printed using Polylactic Acid (PLA) filament material. The flex sensors are used to detect the motion of the hands. The signal generated from the flex sensors is transmitted and then received to drive the servo motors which causes the movement of the hand and the fingers. The final system provides relatively good performance and characteristics for a prototype 3D printed model. With the future growth of the 3D printing industry, advanced printers and materials will allow to development of more commercial-like prosthetic devices which are robust and durable systems. Carbon fiber can be used for 3D printing as well and offers significantly more strength than PLA.
-
INTRODUCTION
It can be argued that the most important thing to anyone is their body. Replacing a lost limb, especially the hand, is a daunting task it really appreciates the complexity of the human body. Well-designed prosthetics can deliver both functionality and cosmetics pleasing. Along with it, it also serves to complete the amputees sense of wholeness. The importance of the ongoing, daily use of a human hand and arm cannot be underestimated. A prosthesis provides mobility as well as emotional comfort. This enables the users to manage daily activities and provides the means to stay independent. With the help of the right prosthetic device along with a positive attitude and physical rehabilitation can improve an amputees quality of life. With the advancement in prosthetics, people now can do almost everything they could before they lost their limbs. There are many inspirational stories where amputees have achieved massive success in goals like running marathons and climbing mountains.
Innovators have been around for centuries attempting to replace lost limbs with handmade devices. Many artificial devices have been created and found in ancient societies around the world indicating continuous progress of prosthetic technology. Until recently artificial limb formation improved sparingly. Early models such as wooden legs can be considered simple artificial limbs. History shows that for long-time artificial limbs remain idle tools principles of control and movement. The goal is to
design a fully functioning 3-D printed lightweight arm, that can perform meager everyday operations. The intention is to design a machine that mimics the operation of the human arm as much as possible and to see that it is controlled to an appropriate extent by gesture control.
-
METHODOLOGY
All mechanical components have been produced using a 3D printer and a liquid 3D printer. The different parts of the prosthetic arm will be modeled in Blender and 3D printed using Cura software with Polylactic Acid (PLA) filament material. This type of 3D printer produces what is known as support material which provides support to horizontal planes during printing. Care has to be taken when removing this support material so as to not damage the component. Several features have been experimented with such as print speed, layer resolution, and extrusion temperature to produce high- quality printed components.
Assembly of this device proved to be quite challenging and required the use of several tools. Threading the tendon lines through their guide holes, tensioning the tendons, and tuning the servo/finger movements require precision and patience. A user flexing generates an analog signal which is amplified, rectified, and smoothed and the motion is detected by OpenCV which is then sent to the microcontroller which is Arduino Uno. The microcontroller uses this analog signal to generate a pulse width modulated signal. This drives servo motors which tension the tendons causing the fingers to curl up.
Fig 1: Sysytem Flow Diagram
-
IMPLEMENTATION
After researching a number of actuation methods, an artificial tendon was chosen for the prosthetic arm. Artificial tendons are an effective way to use bionic hands. These tendons can be any high-strength line that does not stretch when tension is applied. These lines connect the fingers and are tensioned by motors in the forearm. The opening and closing of the fingers are obtained by pulling on the tendons. The electric motors that run these tendons are placed completely inside the device to make it more portable and attachable to the amputated limb. Ideally, these motors should be placed as close as possible to the fingers. However, the motors cannot be placed inside the palm section due to their relatively large size. Hence, they are housed within the forearm section.
Each finger consists of three individual printed components linked together with polypropylene pins. The artificial tendons loop around the inside tip of the finger to create a tendon locking point. This tendon runs through channels inside the finger to form an enclosed loop. The thumb has also been designed in a similar fashion as that of the other fingers. The thumb provides only a single degree of freedom: it can only open/close in a single way. Polypropylene pins are used to connect each finger to the palm. The wrist rotation mechanism is incorporated at the bottom of the palm section. The wrist rotation is controlled by a gear-driven system. The gear system consists of two gears, both of which are 3Diprinted. Although the forearm section contains non-moving component sits design is still challenging as this section needs to house five servo motors.
Arduino UNO has been used as the central computer for this system. This family of processors has limits on computational power but is more than adequate for this design. In order to program the microcontroller circuitry pass data through a USB connection to a laptop. It is important that this system is portable and completely powered by internal sources. Lithium Polymer (LiPo) batteries offer a high energy density and are rechargeable. There is a trade-off between battery life and battery size. Ideally, the arm is likely to be able to run for several hours without needing to be recharged.
The firmware implementation deals with the programming of the Arduino in order to control the signals. From the flex sensor and the connected circuitry, the signal is sent to the transmitting Arduino. The Arduino transmits the signal to the receiver Arduino where the processing takes place. At the transmitter end, the values are matched to the values of angle, which determine the motion of the fingers and the extent of bent in them. This is done with help of the map function. Once the values are mapped, they are sent across in the form of an array. After the values are received, they are processed and given as input to the respective servo motors. These servo motors then decide the motion of each ofthe fingers.
-
RESULT
Over the course of testing, the system has proven to be reliable and has required minimal maintenance since being assemled. Certain regions such as the wrist are at a high risk of breaking
if the device is subject to moderate forces. Although each finger has three joints these joints all rotate together when the tendons are tensioned. Furthermore, no fingers allow for abduction/adduction movement (wiggling side to side) which greatly limits the dexterity of the hand. The palm can rotate about the wrist byi180 degrees, which is similar to the movement of the human wrist. However, the lack of ability to flex the wrist forwards and backward greatly reduces the dexterity of the arm.
The developed system is only a prototype so is not expected to maintain its characteristics and performance for a long time. However, it is important to take care to develop a reliable prototype that can be used for future research. If any components of the device ever break, they can be easily replaced or reprinted. The current wrist design can rotate but cannot flex back and forth. This means there is no joint absorbing and dampening the shock from an impact on the hand.
Fig 2: Wrist Movement
Fig 3: Finger Movement controlled by Flex Sensors
-
CONCLUSION
-
Using AI in orthosis and prosthesis is in the primary stage and is not widely applied. Most AI projects have been used in prototypes that have not been marketed yet. It is possible that there will be accessible artificial limbs in the near future that have both feeling and precise motor coordination. In developing countries, amputees have limited access to prosthetic limbs. This constitutes a barrier for these people to
live normal lives. Cost-effectiveness has been achieved in this work. 3D printing is the major factor in making this device affordable.
Conventional prosthetic devices come with a number of drawbacks. The weight of the device is another major issue when it comes to conventional prosthetic devices. This work provides a prosthetic device that is lower than conventional prosthetic devices. Low actuation speed and high response time often seem to come into the picture for conventional prosthetics. The design of the device has been well-maintained to produce maximum power efficiency and better quality.
The prototype can be further advanced to perform a wide range of functionalities including lifting and grabbing objects and even carrying them in a variety of different body types.
[9] H. Hermens, S. Stramigioli, H. Rietman, P. Veltink, and S.Misra, Myoelectric forearm prostheses: State of the art from a user- centered perspective, J. Rehabil. Res. Dev., vol. 48, no. 6, p. 719, 2011.
[10] D. Peleg, E. Braiman, E. Yom-Tov, and G. Inbar, Classification of finger activation for use in a robotic prosthesis arm, IEEE Transactions on Neural Systems and Rehabilitation Engineering, vol. 10, no. 4, pp. 290 293, 2002. doi: 10.1109/TNSRE. 2002.806831.REFERENCES
[1] G. Li, Y. Liu, and Z. Li, The prosthetic arm: A dramatic improvement for the limb amputation from the humerus, in 2019 IEEE 4th International Conference on Advanced Robotics and Mechatronics (ICARM), IEEE, 2019, pp. 475480. [2] M. D. Paskett, N. R. Olsen, J. A. George, et al., A modular transradial bypass socket for surface myoelectric prosthetic control in non- amputees, IEEE Transactions on Neural Systems and Rehabilitation Engineering, vol. 27, no. 10, pp. 2070 2076, 2019. [3] M. Mohamad, M. Afandi, R. Fatin, S. Nurul, and N.Ramlee, Design and development of mechanism for prosthetic hand, part 2,
[4] J.-A. Leal-Naranjo, C.-R. T.-S. Miguel, M. Ceccarelli, andH. Rostro-Gonzalez, Mechanical design and assessment of a low-cost 7-dof prosthetic arm for shoulder disarticulation, Applied Bionics and Biomechanics, vol.
2018, 2018.
[5] [F. H. Salem, K. S. Mohamed, S. B. Mohamed, and A. A. El Gehani, The development of body-powered prosthetic hand controlled by emg signals using dsp processor with virtual prosthesis implementation, in Conference Papers in Science, Hindawi, vol. 2013, 2013. [6] M. R. Mohebbian, M. Nosouhi, F. Fazilati, et al., A comprehensive review of myoelectric prosthesis control, arXiv preprint arXiv:2112.13192, 2021. [7] A. Fleming, N. Stafford, S. Huang, X. Hu, D. P. Ferris, andH. H. Huang, Myoelectric control of robotic lower limb prostheses: A review of electromyography interfaces, control paradigms, challenges and future directions,
Journal of neural engineering, vol. 18, no. 4, p. 041 004, 2021.
[8] K. H. Ng, V. Nazari, and M. Alam, Can prosthetic hands mimic a healthy human hand? Prosthesis, vol. 3, no. 1, pp. 1123, 2021.