
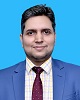
- Open Access
- Authors : Naveen Kumar , Vaibhav Chittoria , Utkarsh Upadhyay
- Paper ID : IJERTV9IS030422
- Volume & Issue : Volume 09, Issue 03 (March 2020)
- Published (First Online): 30-03-2020
- ISSN (Online) : 2278-0181
- Publisher Name : IJERT
- License:
This work is licensed under a Creative Commons Attribution 4.0 International License
Spur Gear Designing and Weight Optimization
Mr. Naveen Kumar¹, Mr. Vaibhav Chittoria², Mr. Utkarsh Upadhyay²
¹Assistant Professor, ²Student,
Department of Mechanical Engineering, ABES Engineering College, Ghaziabad, U.P., India.
Abstract :- In this paper, we are designing and optimizing of gear for event SAE BAJA Transmission. The given values of forces, torque and factor of safety of gear are calculated in accordance to custom vehicle. The gear is designed using SOLIDWORKS Toolbox. Gear weight is optimized by material removal from specific region. After it, simulation on SOLIDWORKS and ANSYS is done giving input values from calculation. The result shows the difference in weight and factor of safety between optimized and un-optimized gear models.
INTRODUCTION :-
Gear is used gain mechanical advantage in power transmission. Gears of different types: Spur Gear, Helical Gear, Bevel Gear, Worm and Wheel Gear. Gears are commonly used in Transmission of Automobiles via Gearbox. Transmission assembly are stated: Simple Gear train, Compound Gear train, Planetary, etc. Weight of gears in gearbox becomes a constant factor of vehicle weight as whole. In college projects like SAE BAJA, SUPERA, etc. the basic knowledge of transmission is seen by an engineer skill to design a gearbox of required strength and maintain lightweight. The vehicle this gear is designed for uses a Engine power source with CVT.
OBJECTIVE:-
-
To choose material of high strength.
-
To calculate the theoretical forces on spur gear by conventional formulas.
-
To model the spur gears on SOLIDWORKS using toolbox spur gear.
-
To remove material and optimize weight of spur gear.
-
To simulate gear on SOLIDWORKS and ANSYS.
ANALYSIS:-
THEORETICAL ANALYSIS
Gear Material
Material for Gear is chosen based on yield strength of material. Materials commonly used are AISI 4340, EN 353, etc. We have taken AISI 4340 for its high strength. The properties are as in Table 1.
Table 1
AISI 4340 Properties
Density |
7.8gm/cm3 |
||
Hardness(BH) |
320 |
||
Youngs modulus |
200GPa |
||
Poissons ratio |
0.30 |
||
Yield strength |
710MPa |
||
Ultimate tensile strength |
1110MPa |
Engine
Engine used here is Briggs and Stratton engine, Model 19(Fig. 1). Its specifications are given in Table 2.
Fig. 1 B&S Power Graph
Table 2 Input Engine
Model |
19L232-0054 G1 |
Compression ratio |
8.1 to 1 |
Bore/Stroke |
3.12 / 2.44 |
HP(Gross) |
10.0 Hp |
Max. RPM |
3800 rpm |
Max. Torque |
19.6 Nm at 2800 rpm |
Continuous Variable Transmission (CVT) is used as constant reduction between engine output and gearbox input. Specifications are given in Table 3.
Table 3
CVT Specifications
CVT |
Polaris |
Max. ratio |
3:1 |
Min. ratio |
0.7:1 |
Calculation Torque on gear
Torque is transferred from engine to gearbox after reduction from CVT. The final torque on gear is:- Mt torque input at gear
Mt = max. torque of engine * max. CVT ratio * Gear reduction ratio Mt = 19.6 * 3 * 7.54
Mt = 443 450 Nm
Spur Gear nomenclature
Basic dimensions of Gear are given:- Module(m)=2.5
Number of Teeth(z)=59
Pitch Circle Diameter(d)= m*z = 147.5mm Width of Gear(b)=20mm
Output Shaft Diameter=36mm
Calculation of Tangential Force
The two components of net force on gear tooth are: Radial force(Fr), Tangential force(Ft). The only force responsible of gear rotation is Ft, calculated below:-
Ft Tangential force applied on gear tooth/teeth
Ft = 2*Mt / d [1]
Ft = 2*450*1000 / 147.5 Ft = 6101.6949 N
Calculation of Beam Strength of Gear Teeth
The resistive force offered by gear tooth is calculated below:-
Fen Resistive force of Gear tooth
en Allowable permissible stress of material ut Ultimate tensile stress of material
en = ut /3 [2]
Fen = en * b*Y*m
Fen = (1110/3) *20*[*(0.175 0.95 / 59)]*2.5 Fen = 9235.0843 N
Calculated Factor of Safety(FOS)
Factor of Safety is calculated:- FOS = Fen / Ft
FOS = 9235.0843 / 6101.6949
FOS = 1.51
GEAR DESIGNING
For Gear model, we take a standard spur gear from SOLIDWORKS Toolbox. Assign the Module and Teeth number. The software will generate a gear using Global Equations. We optimize it according to design using Static Simulation.
For simulation the center hub is fixed fixture and tangential force is applied on teeth for worst condition possible. Simulation of Gear on SOLIDWORKS Fig. 2, 3.
Fig. 2 Stess
Fig. 3 Factor of Safety
Simulation of Gear on ANSYS Fig. 4, 5.
Fig. 4 Stress
Fig. 5 Factor of Safety
RESULT :-
After simulations, we got the following results give in Table 4.
Table 4 Comparison Result
Normal Gear |
Optimized Gear |
FOS=2.24 |
FOS=2.01 |
Mass=2505.51gm |
Mass=888.86gm |
REFRENCE
-
K. Mahadevan, K. Balaveera Reddy; Design Data Handbook, Fourth Edition(2019)
-
V. N. Bhandari; Design of Machine Elements, Third Edition.
-
Raja. S, Ramaswamy. K and Lokesh. M; WEIGHT OPTIMIZATION OF HELICAL GEAR UNDER STATIC ANALYSIS, International Journal of Mechanical Engineering and Technology (Volume 9, Issue 9, September 2018).
-
Chinmay Shah, Swapnil Thigale, Rathin Shah; OPTIMIZATION WEIGHT OF A GEAR USING TOPOLOGY OPTIMIZATION, International Journal of Science, Engineering and Technology Research (Volume 7, Issue 6, June 2018).
-
Mr. Dattatray A. Patil, Prof. Dalwe D.M.; DESIGN AND WEIGHT OPTIMIZATION OF PINION BY USING FEA METHOD, International Research Journal of Engineering and Technology (Volume 4, Issue 6, June -2017).
-
Mahesh. Badhite, Srimanthula Srikanth, Jithendra Bodapali; STRESS REDUCTION AND ANALYSIS OF A SPUR GEAR TOOTH, International Journal of Emerging Technology and Advanced Engineering (Volume 4, Issue 3, March 2014).
-
Amit Patil, BENDING STRESS ANALYSIS OF SPUR GEAR, International Journal for Research in Applied Science & Engineering Technology (Volume 5, Issue 6, June 2017).