
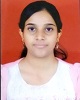
- Open Access
- Authors : Priyanka Bharat More , Dr. A. A Godbole
- Paper ID : IJERTV9IS030593
- Volume & Issue : Volume 09, Issue 03 (March 2020)
- Published (First Online): 06-04-2020
- ISSN (Online) : 2278-0181
- Publisher Name : IJERT
- License:
This work is licensed under a Creative Commons Attribution 4.0 International License
Hardware Implementation of FUZZYSMC based Speed Control of BLDC Motor
Priyanka Bharat More
Post graduate Student, Department of Electrical Engineering
AISSMS College of Engineering Pune, India
Dr. A. A. Godbole
Professor,
Department of Electrical Engineering AISSMS College of Engineering Pune, India
AbstractIn recent times, BLDC motors are most popular motors in industry due to their vast speed range, efficiency and low maintenance. There are many control methods invented to control speed of BLDC motors. Some of these are PI, SMC, PID, FUZZY, FUZZY-PID, &FUZZY-SMC etc. FUZZY SMC
control system is a control system where the speed control is obtained by sliding mode control system and its chattering and slow response is controlled by using fuzzy logic by adjusting gain of control term. This paper presents hardware implementation for the speed control of BLDC motor using FUZZYSMC controller and the efficiency of the proposed system is observed with simulated and hardware results in terms of settling time, overshoot, undershoot etc.
KeywordsBLDC motor; Sliding mode control; fuzzy logic.
I INTRODUCTION
BLDC motor is as superior as dc motor but its commutation is done electronically. Losses in the BLDC motor are less due to electronic commutation and hence this motor is gaining rapid attention in industry. Commutation is nothing but linkage between drive state and respective sensor output. BLDC motor consists of three phases connected with star or delta connection. This motor operates by energization of two phases with one phase floating. So basically main action of commutation is to sense position of rotor and accordingly energies phases which will leads to maximum torque. Maximum torque is obtained when the permanent magnet rotor is 90 degrees away from the stator magnetic field. Generally Hall Effect sensors are used and they give high and low signal for each 180 degree and they are placed 120 degree apart from each other. During running condition of motor, the permanent magnet rotor moving behind the stator coils induces an EMF in the coils called Back Electromotive Force and is directly proportional to the motor speed. If back EMF and applied voltage are equal i.e. ideal condition, then motor will draw excess current which will blow out switches in the drive circuitry Practically back EMF is always less than applied voltage. Speed of motor is directly proportional to applied voltage hence by varying PWM linearly will result in linear speed control. In this paper, section II presents drive circuitry for BLDC motor, section III presents various speed control techniques for BLDC motor. Section IV presents control algorithms used in the proposed system. Section V presents hardware setup and components used. Section VI and VII presents simulated and hardware results. Section VIII and IX presents performance comparison between control systems and conclusion respectively.
II VSI FED BLDC MOTOR
Figure 1 Inverter Circuit
Figure 1 Inverter Circuit
Fig 1 shows VSI fed BLDC motor, both high side and low side drivers should not conduct at same time because off time is more than on time so until and unless complete commutation of high side driver is done, low side driver should not conduct .No drivers in the same leg should conduct at a time to avoid short circuit which is called dead time.
III SPEED CONTROL TECHNIQUE
For speed control of BLDC motor there are many control systems developed like PI, fuzzy-PID, SMC, FUZZY etc. The suitability of any control system is depends on its response time, dynamic load conditions, robustness and cost. The system which fulfils all these conditions is said to be a good control system.
-
PI controller:
PI controller is a most commonly used controller. It increases order as well as type of the system. Steady state error decreases with increase in type and order of the system [3].The tuning of gain is the most important task in PI controller it minimizes error. PI has slower response because of integrator and there should be proper tuning of gains so as to maintain stability of system.
-
Sliding Mode Controller:
Sliding mode control system is one of the type of variable structure control which makes continuous switching of control based on present state of the system. Sliding mode control is gaining popularity due to its robustness. Sliding mode is invariant to any variations in system parameters [9]. Sliding mode reduces order of the system. In case of ideal
sliding mode, robustness property is maintained by control which brings the system close to S = 0 , But practically the system has limit cycle behavior and therefore chattering is always there.[9] Chattering is high frequency oscillation which makes system oscillate continuously. This is the biggest disadvantage of sliding mode controller.
The sliding surface is designed with error term, its derivative and integration with appropriate gains.
= + 1 + 2 (1)
The control input is decided such that it will make error trajectories to converge to the sliding surface. It is given by,
= () (2)
This control law is used to reach the sliding surface.
-
FUZZY LOGIC CONTROLLER:-
Fuzzy logic is a system in which there is no need to define system parameters exactly. It has predefined boundaries up to which the output lies. Fuzzy logic system operates on three processes, fuzzification, inference and defuzzification [10].
-
Fuzzification: Fuzzy logic control is based on linguistic variable, so conversion of physical input to linguistic variables is called fuzzification.
-
Inference: Inference consists of a set of IF-Then rules which are established for decision making. Fuzzy rules are nothing but a process for control action. Control action is based on how rules are defined. By proper adjustment of membership function and fuzzy rules, controllers performances is improved.
-
Defuzzification: Defuzzification converts the fuzzy quantity into crisp one. After decision making, the output of fuzzy logic controller should be a real physical output so that we can use it in our control system.
D FUZZY SMC:
Sliding mode control is robust technique and it has faster response than other control systems but it has chattering problem which cannot be overcome easily therefore by combining sliding mode control system and fuzzy logic control system one can achieve better results [3]. Sliding surface and its derivative are given as the input to the fuzzy logic controller. Output of fuzzy controller is used to adjust gain K in control law of sliding mode control system so that chattering of the system is reduced [2].
IV.CONTROL METHOD
Figure 2 Block Diagram
Figure 2 Block Diagram
Fig 2 represents block diagram of the FUZZYSMC based speed controller.12 v power supply is given to motor through SMPS. Current sensor senses any change in current and gives equivalent voltage at its output which is then given to the controller. Drive circuit contains inverter drive circuitry which is used to change voltage across the motor based on application. BLDC motor is fed from inverter and the PWM pulses are given to inverter through controller and hence voltage across BLDC motor changes according to control action taken by the controller. Speed of motor is sensed by using IR sensor.
-
SMC Algorithm :
-
B FUZZY SMC Algorithm
V HARDWARE DESIGN
Figure 3 Hardware setup
Figure 3 Hardware setup
In the proposed system, 40watt, 12 v 100 rpm BLDC motor is used. ACS712 current sensor is used. This sensor provides economical and precise current sensing. It has linear hall sensor circuit with copper conduction band the current to be sensed flows through copper band and generates magnetic field accordingly. This magnetic field is sensed by Hall Effect sensor and equivalent voltage is produced at the output. This analog output is then given to the microcontroller. HW IR201 sensor is used to sense speed and for observing speed variations. It is nothing but infrared obstacle detection. It transmits IR signal in a direction and signal is received at the IR receiver when radiation bounce back from surface of the object. It operates on 3-5v power supply and can detect signal from 2 to 30 cm distance. Controller is the heart of the hardware system. In the proposed system, PIC18F4520 microcontroller from pic18Ffamily is chosen. It is a 40 pin IC.PWM pulses are generated from controller and given to the drive circuitry of inverter. The Pic kit 3 programmer is used in the proposed system which will program the controller.
VI SIMULATION RESULTS:
1KW, 500V BLDC motor is tested in MATLAB Simulink. Figure 5 presents simulated results for FUZZYSMC controller for 900 rpm for 50 % and 100% loading at 0.1.
Figure 6 speed response for 900 rpm on No load
Figure 6 speed response for 900 rpm on No load
Figure 4 For 900 rpm
Figure 4 For 900 rpm
From figure 4, when sudden loading is applied at 0.1 sec, speed response goes through undershoot for 50 % it is 180rpm while for 100% it is 350 rpm but it is settling to 900 rpm in less than 0.02 sec.
VII. HARDWARE RESULTS:
-
On NO load:
The proposed system is tested for 40 watt BLDC motor for various speed and load variation accordingly observation is made.
Figure 7 and 8 shows no load speed responses for 900 rpm.
Figure 7 speed response for 50 % loading
Figure 7 speed response for 50 % loading
-
On load with sliding mode controller: For 900 rpm:
Figure 5 ON time response for 900 rpm on No load
Figure 5 ON time response for 900 rpm on No load
Figure 8 speed response for 100% loading
Figure 8 speed response for 100% loading
Figure 7 and 8 shows speed responses for 50 and 100% loading respectively for SMC controller.
-
ON load with FUZZYSMC controller: For 900 rpm
Figure 9 and 10 shows speed responses for 50 % and 100 % loading for FUZZYSMC controller. It is observed that in FUZZYSMC controller is better than sliding mode controller in terms of settling time, overshoot, undershoot etc.
VIII.PERFORMANCE COMPARISON OF SMC AND FUZZYSMC CONTROLLER
Figure 9 speed response for 50% loading
Figure 9 speed response for 50% loading
SMC and FUZZYSMC both systems are tested for sudden load variations and comparison is done in terms of settling time, overshoot, undershoot etc. Table I represents performance comparison of SMC and FUZZYSMC controller.
Table 1
Table 1
IX CONCLUSION:
Figure 10 speed response for 100 % loading
Figure 10 speed response for 100 % loading
Simulation model and hardware implementation of FUZZYSMC controller is developed. Performance of both the systems are observed for different loading conditions. Conclusion is made that FUZZYSMC controller required less settling time than SMC controller. Overshoot and Undershoot values are less in FUZZYSMC controller. In both cases value of K plays important role in control. It is preferred to change K dynamically itself to have better control and reduce chattering.
REFERENCES
-
Pillay, P., and Krishnan, R. Modeling, Simulation, and Analysis of Permanent-Magnet Motor Drives, Part II:The Brushless DC Motor Drive, IEEE Trans. of Industry Applications, vol. 25, no. 2, pp. 274 279,March/April 1989
-
Arun Prasad K.M, Usha Nair An intelligent fuzzy sliding mode controller for a BLDC motor. International Conference on Innovative Mechanisms for Industry Applications(ICIMIA 2017).
-
Priyanka B. More,Dr.A.A.Godbole FUZZYSMC BASED SPEED CONTROL OF BLDC MOTOR.International Journal of Engineering Research & Technology (IJERT) ISSN: 2278-0181 Vol. 8 Issue 12, December-2019
-
K.S.Krishna Veni, Dr.N.Senthil Kumar J.Gnanavadivel Low Cost Fuzzy Logic Based Speed Control of BLDC Motor Drives Ieee International Conference On Advances In Electrical Technology For Green Energy 2017 (Icaetgt 2k17)
-
Vimal Nigam, Shoeb Hussain Satya Narayan Agarwal A Hybrid Fuzzy Sliding Mode Controller for a BLDC Motor Drive 1st IEEE International Conference on Power Electronics, Intelligent Control and Energy Systems (ICPEICES-2016)
-
Kanaiya Bhatt, Sandip Dhoranwala, Ajay Bosamiya SIMULATION OF BRUSHLESS DC MOTOR SPEED CONTROL IN MATLAB. International Journal of Advance Engineering and Research Development Volume 4, Issue 12,
December -2017
-
Shivraj Sdudhe, Archana G Thosar. Mathematical Modelling And Simulation Of Three Phase Bldc motor Using
Matlab/Simulink.International Journal of Advances in Engineering & Technology, Vol. 7, Issue 5, Nov., 2014.
-
Pramod Pal, TM Shubhum and Dr.Amit Ojha, Simulation Of Brushless Dc Motor For Performance Analysis Using Matlab/Simulink Environment International Journal on Recent and Innovation Trends in Computing and Communication Volume: 2 Issue 6
-
V.I.Utkin, Sliding mode control design principles and applications to Electric drives,IEEE Transactions on Industrial Electronics, vol.40, no.1, pp.23-26, February 1993.
-
Digital control and state variable methodsby Mr.M Gopal.
-
Fundamentals of electric drives by G.K.Dubey
-
Ali Mousmi, Yassine el Houm, Ahmed Abbou Implementation of a Fuzzy logic controller for a BLDC motor
-
Electrical drives by Mr.S.K.Pillai.
-
K.S.krishna Veni,Dr.N.Senthil Kumar,J Gnanavadivel Low Cost Fuzzy Logic Based Speed Control of BLDC Motor DrivesIEEE International Conference on advances in electrical technology for green energy 2017.