
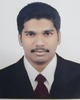
- Open Access
- Authors : Raut Shubham B , Gawade Karan D. , Mane Vinay N. , More Shubham N, Suryavanshi Amol V
- Paper ID : IJERTV9IS040673
- Volume & Issue : Volume 09, Issue 04 (April 2020)
- Published (First Online): 02-05-2020
- ISSN (Online) : 2278-0181
- Publisher Name : IJERT
- License:
This work is licensed under a Creative Commons Attribution 4.0 International License
Design of Electric Forklift used in Small industrial Warehouses and Workshops
Gawade Karan D
UG Department of Mechanical Engineering, PCCOE Savitribai Phule Pune University, Pune, India
Mane Vinay N
UG Department of Mechanical Engineering, PCCOE Savitribai Phule Pune University, Pune, India
More Shubham N
UG Department of Mechanical Engineering, PCCOE Savitribai Phule Pune University, Pune, India
Raut Shubham B
UG Department of Mechanical Engineering, PCCOE Savitribai Phule Pune University, Pune, India
Prof. Suryavanshi Amol V
Faculty of Department of Mechanical Engineering, PCCOE Savitribai Phule
Pune University
Abstract – We describe forklift powered by an electric motor instead of the IC engine using rechargeable batteries the main objective of this project is to design electrically powered forklift for material handling in industrial warehouses and workshops. Nowadays in industries, the forklift operates on an IC engine for transportation and hydraulic system for lifting and lowering of materials. Due to this mode of operation, there are many adverse environmental impacts such as emission of carbon dioxide and leakage of hydraulic fluid. This paper discusses how to integrate the electric system into a forklift truck to make it electrically powered which lift to 200 kg and elevate up to 6 feet.
Keywords – Forklift, Rechargeable Batteries, Electric Motor, IC Engine
- INTRODUCTION
In general the forklift can be defined as a tool capable of lifting hundreds of kilograms. A forklift has two metal forks on the front used to lift cargo. Forklifts have revolutionized warehouse work. The forklift operator drives the forklift forward until the forks push under the cargo, and can then lift the cargo several feet in the air by operating the forks. The forks, also known as blades or tines, are usually made out of steel and can lift up to tons.
- MARKET SURVEY
The market survey lets to understand and realize the real demand and potential for the product under consideration. First and foremost, it is necessary to establish that the proposed product will fulfill the required specifications, what is supposed to do, and the service it can offer to the consumers.
We surveyed in our institute and small industrial workshop where we found that the educational engineering apparatus and industrial equipment up to 200 Kg is not easy to move from one place to another place. So the miniature forklift is required to design that can utilized for lifting load up to 150Kg.
- FIELD OF USE
Forklifts are also immensely essential in warehouse operations. Forklifts are mainly used for loading and unloading trucks and for carrying goods. They can be used to stack material both the small and the more massive ones in places that cannot easily be accessed by humans. Aside from carrying goods and materials, forklifts can also be used to transport large and hefty equipment. Theyre used as a substitute tool to aerial lifts and cranes to hoist people to higher places, especially when these people need to perform a variety of tasks, such as: Inventory of stocks, and Maintenance purposes.
- LITERATURE SURVEY
From the references actual Industrial forklift we have designed our miniature and cost effective forklift. The structure is constructed by using square tubes, C-channels, Metal frames, Chain- sprocket, bearings, etc.(1) These materials are easily available into market. From literature survey we got important information regarding design procedures and manufacturing of Forklift. It provides information related to design consideration and battery selection methods.(6) The advantage of using this technology is to increase productivity in small scale industries by better material handling availability and enhancing safety majors.(3)
- WORKING
Electric Forklifts derive power from Lead Acid Batteries. The carriage serves as the base to the forklift. The Carriage is fixed on mast rails so that it can be easily moved upward and downward. The Mast is a vertical part that lifts up and pushes down the loads. A motor is a device that converts electro-chemical energy, provided by an industrial rechargeable battery, into mechanical energy. The Electric motors are attached to the two main vertical structures called the “masts.” However, the actual forks that carry the load are attached to the main body of the forklift
through a pair of roller chain pulleys whose fulcrum is a gear at the top of the mast. Thus, the Electric motor pushes the masts up, the gears on the masts push against the roller chain.
Forklifts have two sets of controls: one for steering and one for lifting. The steering controls work much like those of a golf cart: acceleration pedal, brake, steering wheel, forward gear and reverse gear. Front-wheel steering allows the driver a greater degree of rotation and precision when handling a load.
F(normal) = 1324.35N
F (frictional) = 0.75*1324.35 = 993.26N
Now, Torque required for moving forklift vehicle T = F* Radius of wheel
= 993.26*120
= 119191.5Nmm = 119.19 Nm
Selection of Lifting Motor
Total Load (W) = Mass (m) × Acceleration due to gravity (g) = 150 ×9.81 = 1471.5 N
Required torque of motor () = 5668.96 Nmm Required motor specification N=100 rpm
Torque required raising maximum load in Kg-cm
= = 5668.96 =57.787 kg-cm=5.88Nm
9.81×10 9.81×10
Required speed of motor shaft in rpm = 100 rpm
Fig 1 Detailed design of electric forklift.
Chain design –
Selecting standard chain used in cycle as Chain – 06 B From V.B.Bhandari page no. 14.3
Pitch -9.525mm
Roller diameter,d1=6.35 mm Transverse pitch pt=10.24 mm Width b1=5.72 mm
Z1= 18, Z2= 18
Approximate centre distance,
a = 40×P —————-nominal a = 40×9.525
a = 381 mm No of links
Ln=2() + (1+2) + (12)2 × ( )
- COMPONENTS
381
2
18 + 18
2
18 18
9.525
- Chain drive
= 2(
) + (
) + (
)2 × ( )
It helps to drive the system in both side (one at a time)
= 98
9.525 2
2 ×
381
using electric motor. Standard chain of no. 6B is selected.
Corrected centre distance
a= {[Ln ((1 + 2)/2)] + ( [Ln ((1 +
- Lifting D.C. Motor 4 2
The D.C. motor is act as prime mover which drives the sprocket to raise the load. We select 12V, 2.5A, 100 rpm, and 6Nm motor
- Driving D.C. Motor
The D.C. motor is act as prime mover which drives the sprocket for transportation purpose. We select 12V, 2.5A, 300 rpm, and 120Nm motor
- Wheels
R8 wheels are used. The wheels rolls and moves the forklift from one place to another place. We use four wheels two at front side attached at bottom at support legs and two are at rear side.
- Battery
The battery acts as power source for driving of motor.
2)/2) ]2 8 × (12) )}1÷2
2
a=191.68 mm a = 192 mm
Length of the chain
L = Ln×p = 98×9.525 = 933.45 mm
Design of sprocket – Used chain no.06B For Z = 18
Pitch, P = 9.525 mm
Width between inner plates, b1 = 5.72 mm Roller diameter, d1 = 6.35 mm Transverse pitch pt = 10.24 mm
Pitch circle diameter
We use two batteries of capacities 12V, 7.2 Ah
- Lifting Forks
The dimensions of lifting fork L600, A=40x40x10mm. The lifting fork directly lifts the load fro its position.
D1 =
sin (180/1)
= 9.525
( )
( )
sin 180
18
D2 = sin (180/2)
= 9.525
( )
( )
sin 180
18
- Chain drive
- DESIGN
Selection of Driving Motor
Mass of forklift vehicle with driver = 270 kg Acceleration assumed as = 1G F= 270*9.81 = 2648.7N
D1 = 54.85 mm D2 = 54.85 mm
Roller seating radius (ri)
rimax = 0.505d1 + 0.069× (d1)1/3
rimax = 3.33mm
rimin = 0.505 d1 = 3.2mm Tooth Flank Radius (re)
4 4
4 4
remax = 0.008× (z2+180) =16.928mm
= ( ) = (2.45×600 )
remin = 0.12×d1(z+2) = 15.24mm
8
8×210×103
Root Diameter (Df)
Df = D 2× ri = 88.47mm
Tooth height above pitch polygon (ha)
hamax = 0.625×p 0.5×d1 +0.8× = 2.9513mm
hamin = 0.5× (p-d1) = 1.5875mm Tooth Width (bf)
bf = 0.93 ×b1 = 5.3196mm
Tooth Side Relief (ba)
ba = 0.1p to 0.15p = 1.1907mm
Design of Fork
Outer face height (D) = 50.8 mm Outer face width (B) = 50.8 mm Inner ace height (d) = 44.8 mm Inner face width (b) = 44.8 mm Length of fork (L) = 600 mm Moment of Inertia of fork (I)
= 0.43 mm
Fig 3- Uniformly distributed load
Selection of bearing
Bearing life = 12000-20000 Hrs. Radial load (P) = 2450 N
Speed (n) = 50 rpm
Assume L_10h = 12000 hrs.
1
=
12
[3 3]Bearing life (L_10)
I= 1
12
[6659702.81 4028209.56]L_10= (60 × n × L_10h)/10^6
= 219291.10 4
1] Consider Two Fork with Point Load Moment of Inertia for two fork (I)
I = I1+I2 = 219291.10 + 219291.10 I = 438582.2 4
Bending Moment ()
= -W × L = -1470 × 600 M_A
= – 882000 N-mm
3 3
3 3
3. Deflection ( )
L_10=(60 ×50×12000)/10^6
L_10 = 36 million rev.
Load capacity (C)
C = P(L_10)^(1/3)
C = 2450(36)^(1/3) C = 8089.72 N
Using standard table of bearing selection,
= ( )= 1470×600
= 1.149 mm
C = 9950 N
3
3×210×103438582.2
C_0 = 4150 N
d = 12mm, D = 37mm, B = 12mm
But, from available bearing range in market, we are assuming suitable bearing
d = 12mm, D = 28mm, B = 8mm Designation DGBB 60012 Z
Fig 2- Point load
II] Consider Two Fork with Uniform Distributed Load Moment of Inertia for two fork (I)
I = I1+I2 = 219291.10 + 219291.10 I = 438582.2 4
Find W/mm W/mm = = 1470
600
2 2
2 2
W/mm = 2.45 N/mm Bending Moment ()
= × =- 2.45×600
2 2
- CONCLUSION
The main boon of using the technology is to reduce the impact of fuel-based forklift also it lessons human efforts and their misconceptions. Its not only user friendly but also environment friendly. It is highly affordable at a lower cost.
- FUTURE SCOPE
In the era of interconnectivity every device, machine and person will start talking to each other, and this includes lift trucks. The introduction of automated decision-making into forklift technology will make operations safer. Next generation of environmentally friendly Forklift has an electric-powered core which combines with rechargeable battery-capacity technology to clear even the strictest environmental standards. By removing unnecessary processes and extended routes, forklift operators around the world can reduce man hours, emissions and costs significantly.
= – 441000 Nmm
Deflection( )
ACKNOWLEDGEMENT
We would like to thank Prof. Suryavanshi Amol V. for his guidance. His enthusiasms as well as his technical expertise were essential in helping us overcome many obstacles. Under his guidance we got know about industrial and economic aspects required for developing any product.
REFERENCES
- FAN Jie et al, Design of an Electric Forklift, Computer-Aided Drafting and Manufacturing, Vol. 25, No. 3, September 2015, pp 39-42
- Juan M. Massone, Failure of forklift forks, Engineering Failure Analysis, Elsevier Ltd., January 2010
- Sachin Ugale et al, Design, Development, and Modelling of Forklift, International Journal of EngineeringResearch & Tech
1238
- Khebude Karan N. et al, Design and Development of Mechanical Forklift, International Research Journal of Engineering and Technology, e-ISSN: 2395-0056, p-ISSN: 2395-0072, Vol. 5,
Issue:03, March 2018, pp-1125-1136
- Wang, Lili & Zhao, Dingxuan & Wang, Yao & Wang, Lei & Li, Yilei & Du, Miaomiao & Chen, Hanzhe, 2017. “Energy management strategy development of forklift with electric lifting device,” Energy,Elsevier,vol.128