
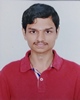
- Open Access
- Authors : Atishay. M , D. Mahesh Kumar , Nikhitha. P. Rao , Jyothi. S, Afifa Parveen
- Paper ID : IJERTV9IS040705
- Volume & Issue : Volume 09, Issue 04 (April 2020)
- Published (First Online): 07-05-2020
- ISSN (Online) : 2278-0181
- Publisher Name : IJERT
- License:
This work is licensed under a Creative Commons Attribution 4.0 International License
Development and Implementation of Real-Time Flex Sensor based Prosthetic Hand
1Atishay.M, 2D. Mahesh Kumar
2Associate Professor, Electronics & Instrumentation Engg.
JSS Academy of Technical Education Bengaluru, India
3Nikhitha.P. Rao, 4 Jyothi. S, 5Afifa Parveen
1,3,4,5Students, Electronics & Instrumentation Engg.
JSS Academy of Technical Education Bengaluru, India
Abstract Amputees are prone to physical and mental problems. Due to the loss of their body parts, they mostly rely on others to perform their daily activities. In order to facilitate and improve the quality of life with independence and freedom to the amputees, prosthesis was developed. Hence, this project intends towards the development of a real-time flex sensor based Prosthetic Hand to serve them. The proposed project involves a glove controller, a technique involving the control of the arm motion, where flex sensors are incorporated.
By measuring real-time variations of phantom mimicking, a distinctive property of human hand, the results are validated. The novel design consists of five fingers which are actuated individually. Using nRF24 transceiver a wireless communication was setup between the controller and the prosthetic arm, which enabled the user to have convenient functionality. The main purpose of the project is to demonstrate the feasibility of using 3-D printing technology in the design of a low cost, user convenient prosthetic hand for helping the amputees perform the activities in which the use of both hands is necessary. It helps the disabled in acquiring the confidence to lead an independent life by regaining the functionality of the disabled body part.
Keywords: Prosthetic hand, Flex sensors, Glove control, Phantom mimicking, Actuators, Wireless communication, 3-D printing.
-
INTRODUCTION
On a recent survey conducted in India, it is recorded that there are about 0.62 amputees per thousand population, as shown in Figure 1. Amputation refers to the loss of a body parts or a part of limb. The cause for these amputations might be due to diseases such as blood vessel diseases, diabetes, tumors, etc. and also due to injuries or accidents. Though the amputees are strong enough, the society will treat them different, making them feel alone. They are mostly dependent on others in order to perform their daily chores, hence to provide them an independent life, prosthesis was developed.
Figure 2 depicts the amputation rate based on the age of people and we can observe that the majority of the amputations occur in the middle age where people lose their limbs due to accidents, and other diseases as described earlier. Comparing with the high income countries, the amputation rate is less in India for people aged above 60 years as they are not much affected with vascular problems and diseases such as cancer.
Figure 1: Amputees in India
Figure 2: Distribution of amputees
The first prosthetic hand was the prosthetic hook hand which was developed during the Civil war, shown in Figure
3. Currently, different types of prosthetic arms with different control techniques, such as Electromyography (EMG) sensors, Electroencephalogram (EEG) sensors, etc. are developed and are available around the global market. In the above mentioned control techniques acquiring the signals and the processing of the input signals are a tedious process and also its very difficult task to obtain accurate output. The prosthesis available in the market involving the above mentioned control techniques are of high cost and are not affordable by many.
Figure 3: Prosthetic Hook Hand
Hence, the paper proposes an electronically controlled prosthesis to fulfill the loss, which performs the functionalities as that of the original limb. It would also avoid the dependency on others. The actions to be performed by the 3D printed prosthetic arms are controlled by a microcontroller. The proposed work makes use of flex sensors to obtain the movement of the fingers made by the human hand and this information is sent to the microcontroller to imitate the working of the hand, thereby the prosthetic arm will perform the operation performed by the human hand. Servo motors are present in the prosthetic hand to make the movements of the finger and a gyroscope is present to control the movements of the wrist, thereby functioning as an original hand. By the use of this, the amputee would be able to grasp objects and also in lifting of heavy objects without the help of any.
The aforementioned design would be able to mimic the functioning of a human hand and would be dexterous with an easy and natural control. The most important thing considered is the cost which would be as low as possible and would be affordable to everyone.
-
LITERATURE SURVEY
There are a lot of prosthetic hand designs around the world. Some prosthetic hands differ in the sensors used, some in the materials with which they are built and some the methodology. These prosthetic hands are costly, harder to use since the design, usage is very complex. There are few papers below which shows how similar or different is our paper from them.
-
On the use of 3D printing technology towards the development of a low cost robotic prosthetic arm [1]: In this paper, the proposed methodology has two ways to replicate the human hand movement one is by flex sensor which is incorporated in a glove is used sense the finger movement and the other one is by Electromyography (EMG) sensor connected to the muscles of the amputee. The main disadvantage here is that it is very difficult to sense and process an EMG signal.
-
Prosthetic hand with Biomimetic Tactile sensing and force feedback [2]: This paper proposes the use of force feedback actuation system in order to drive the motors to
control the movement of the fingers. Feedback actuation mechanism is integrated to myoelectric band on residual limb and the sensor is designed based on biomimetic strategy. 3D printed structure is integrated onto a surface. The drawbacks of this are that it exhibits only linear characteristics and is difficult to handle with non-linear motions.
-
Thumb controlled Low-Cost Prosthetic Robotic Arm [3]: In this paper, the proposed methodology has a particle board frame which has the whole circuit. This can add to the prosthetic hand being bulkier. And the prosthetic arm has a claw shaped arm, which dont serve our purpose of making it look exactly like an arm so that the amputees feel comfortable wearing it.
-
Optoelectronically innervated soft prosthetic hand via stretchable optical waveguides [4]: In this paper, the proposed methodology uses optical waveguides which very costly. Optoelectronic strain sensors used here are susceptible to interference from environmental effects. A solenoid valve is used which requires the control signal continuously which is difficult to provide.
-
Three-Dimensional Printing of Prosthetic Hands for Children [5]: This paper mainly proposes about the 3D printing technology and the materials used to develop prosthetic hand. In children, the growth period would bring a lot of physical changes which is challenging, in order to adapt to those changes, the 3D printed prosthetic hand was designed accordingly in here. So, prosthetic hand can be designed and developed faster using 3D printing technology and also to get a better quality, creative design and freedom to customize.
-
Design and Fabrication of a Soft Robotic Hand with Embedded Actuators and Sensors [6]: The proposed methodology uses a silicone rubber material or the body of the arm which is soft and recovers the shape after removing the pressure applied to it. Piezoelectric transducer is used to sense the finger movements. Fabrication process is tedious. Embedded shape memory alloy (SMA) actuator is used to provide the movement which is made of Ni-Ti strip. This Ni- Ti strip picks up false signal as they are very sensitive.
-
Use of accelerometers in the control of practical prosthetic arm [7]: The proposed methodology uses accelerometers to control the movement of the prosthetic arm and also provides the information on the orientation of limb segments. Inertial Measurement Unit (IMU) is used which is a combination of accelerometer, gyroscope and magnetometers. EMG sensor is used to sense the contractions of the muscles. But the major disadvantage is that the prosthetic arm developed is very heavy and as well as slower in operation and hard to use.
-
Voice control based prosthetic human arm [8]: In this paper, the proposed methodology contains a prosthetic arm whose movement can be controlled by voice. This is actually a big step in the advancement of technology, but it has its own disadvantages. Since the prosthetic arm is voice
controlled, it causes problems in the noisy environment. Sometimes the prosthetic arm might have delayed response than the glove controlled prosthetic arm. And the major disadvantage is that is requires constant internet connection since its using Googles API to convert voice commands into to text.
-
Design of multi grip patterns, prosthetic hand with single actuator [9]: In this paper, the proposed methodology has only one actuator to control the prosthetic hand with five finger multi grip pattern which helps to perform daily activities. But the size of the actuator is very big. The grasp of the fingers is not stable.
-
User friendly LabVIEW GUI for prosthetic hand control using Emotive EEG headset [10]: In this paper, controlling of the prosthetic hand is done through Brain Computer Interface (BCI). The signals are recorded through the emotive Electroencephalograph (EEG) headset. EEG is integrated with Graphical User Interface (GUI) and designed using LabVIEW. It has a lot of disadvantages as the range of functions performed is limited and has to be trained to perform the required functions and a lot of disturbances occur in data due to artifacts.
-
A Prosthetic hand control interface using ESP8266 Wi-Fi module and android application [11]: In the proposed project, logic functions are developed in order to set angle of rotation. Servo motors are used to determine the finger movements, that are controlled via Wi-Fi module. Android application is developed for the control of prosthetic arm and the system is controlled manually using mobile control framework. The proposed work, makes use of android application to choose gesture. The disadvantage here is that it is restricted to specific angles and entire unit should be connected to Wi-Fi network.
-
Data for benchmarking low-cost, 3D printed prosthetic hands [12]: This paper deals with the grasp, finite element modeling and the tensile test performed on ABS and PLA materials (3D printing). Comparison between human hand and prosthetic hand is done to see grasp of fingers on the spherical, cylindrical and cubic objects. Finite element model is a tool used to analyze the contact between prosthetic fingers and the objects. The mechanical properties of the materials used for 3D printing like ABS and PLA were checked by applying load. The disadvantage of the proposed work is that it is limited to perform only 3 functions and there is failure in analysis of the functioning of the arm.
-
Design of a robotic hand using Flex sensor [13]: In the work proposed, servo motors are used for rotation which generates constant pulse width modulations (PWM). Flex sensors are used to sense the motion of finger and an ATmega8 microcontroller is used to analyze bend of finger. Four channel oscilloscope is used to obtain the waveform. Servo driver and servo module are connected via serial communication. Power transistor in emitter follower is used to deliver current. The disadvantage is that sensors with high
degrees of repeatability, precision and reliability should be used.
-
A method for 3D printing patient specific prosthetic arm with high accuracy shape and size [14]: In the work proposed, design of prosthetic arm is done by capturing tomographic images using CAD software. Blender software is used to compare affected and not affected arm and functions are performed accordingly. The disadvantage is that obtaining the same replica of the functional hand is difficult and requires excess material deposition.
-
Gesture controlled prosthetic arm with sensation sensors [15]: In the proposed paper, flex sensors in the glove gives the input signal. Servo motors are the actuators used for movement of fingers and Peltier plates are used to give cooling effect. LM35 is used to obtain the surroundings temperature. The disadvantages are that it has lesser degrees of freedom and very low grip force necessary for holding objects.
-
-
METHODOLOGY AND WORK FLOW
The project proposes a wearable glove controller, to control the movements in the prosthetic arm. The prototype consists of two main parts the glove and the prosthetic arm. Two nRF24L01 wireless transceiver modules are used to establish wireless communication link between the glove controller and the prosthetic arm.
Figure 4: Block Diagram
Glove controller: Figure 5 is the picture of the glove controller used in the project. This controller is a form of wearable Human machine Interface, where the machine (prosthetic arm) follows the control signals from human via the glove controller. As we can see from the Figure 5, the glove controller has five flex sensors embedded to each finger to gather the information of the finger positions respectively. Flex sensors used gives the change in the resistance over bending or deflection action which is read in terms of voltage in voltage divider. A gyroscope module is located at the wrist to measure the angular variations and mimic the same in the prosthetic arm. An Arduino Mega microcontroller is used in the glove controller, which
processes the input data from the flex sensors by the Analog to digital converter (ADC) pin present and sends the digital output to the Arduino Nano with
The help of nRF24L01 wireless communication module to get the output at the prosthetic hand.
Figure 5: Glove Controller
Prosthetic hand: Figure 6 is the picture of the 3-D printed Prosthetic Hand created in this project. The digital data from the Arduino Mega is converted into corresponding Pulse width Modulation (PWM) signal. These signals in-turn serve as the guide for controlling the rotation of the servomotors accordingly.
There are six servo motors, five for fingers and one for the wrist motion. The wrist motion is restricted to 45degree. KK- 77 strings were used to connect the fingers to the servos to act as artificial tendons, present in the fingers. Synchronous movement of each finger is obtained with the given input data and the servo pulleys. The Arduino nano board is the microcontroller used for processing in the prosthetic arm.
Figure 6: 3-D printed Prosthetic Hand
The parts of the prosthetic arm were 3-D printed. The design of the hand was sketched using the CAD software.
Programming of the microcontroller is done based on the flowchart as shown in figure 7 and figure 8.
Figure 7: Transmitter Flow Chart
Figure 7 shows the Work flow or the flow chart of the transmitter or in other words of the glove controller, as to how the input signals from the glove is transmitted to the receiver that is the prosthetic arm. These input signals from the glove controller control the movements of the prosthetic arm.
As seen in figure 7, as soon as the Arduino is powered up, the variable flex sensors ouput according to the action or movement in the glove is sensed and the output obtained is converted into corresponding voltage values with the voltage divider circuit setup.
These outputs from the five flex sensors along with the gyroscopes output i.e., x, y & z axis alignments are converted into digital values. These digital values are then transmitted using the nRF24 transceiver module.
The output from the sensors is transmitted continuously and uninterruptedly. The output changes with the change in gloves action, which changes flex sensors and gyroscopes output in-turn. The process stops with the loss of power.
Figure 8: Receiver Flow Chart
Figure 8 depicts the Work flow or the flow chart of the receiver or in other words of the prosthetic hand, as to how the output signals are received from the transmitter or the glove controller and is processed to obtain the required actions accordingly.
The Arduino is first powered up for the entire process to happen. The digital output obtained is in the form of PWM waves. Based on the digital values of the flex sensors at two extremities two Threshold values, Threshold 1 and Threshold 2 was set accordingly.
When the digital values varies between the Threshold 1 and the Threshold 2 values the servo motors are aligned accordingly, as seen in the flow chart. The gyroscopes output determines the wrist motion of the prosthetic hand, the angle of rotation of the wrist is restricted to 45 degrees.
The prosthetic arm remains in one position until the output values obtained is changed. In the actions where the grasping of certain objects is required, the prosthetic hand developed as the ability to align then according to the shape of the object due to their flexible movements.
-
RESULT AND DISCUSSION
A deep analysis was made on the flexing and rotational movements of the normal human hand and accordingly a prosthetic arm was designed and developed using 3-D printing technology. A glove controller, embedded with flex
sensors and gyroscope for motion control of prosthetic arm was accordingly designed and set up to control the prosthetic arm movements.
In order to determine the functionality of the developed prosthetic arm, different actions and motions of the prosthetic arm was conducted, the same can be witnessed in the Table I. It was possible to capture different actions of the prosthetic arm with few certainties. Since nRF24L01 wireless transceiver modules are used for input signal transmission from glove to prosthetic arm, there was delay seen at the output end and the same has been recorded accordingly in the Table I below.
Lets take a closer look at Table I,
In the action 1 we can see that; the index finger of the glove controller wore to right hand is the only pointing finger with the closed grip of rest of the finger. The output obtained was desired as it was the exact replica action of the given input from the controller but the delay of 3 seconds to obtain the output.
In the action 2 (ok symbol) we can see that; the index finger of the glove controller has been flexed completely along with the thumb finger with other fingers having no flex action. Although we were able to see a fast bend/ flexing of the index finger, the output obtained was desired as it was the exact replica action of the given input from the controller with a delay of 3 seconds to obtain the output.
In the action 3 (Yo symbol), the middle and the ring finger of the glove controller has been flexed completely and rest of the finger are made open or is not been flexed. The middle and the ring fingers smooth flexing action was observed and the final output was synchronous to the given input signal. The delay seen was again 3 seconds to obtain the output.
In the action 4 (closed fist), all the fingers have been flexed and a tight grip can be observed in the glove controller, the same kind of action was observed in the prosthetic arm, a closed grip with considerable tight grip. The delay was almost 3 seconds for this action.
In order to check the griping ability of the arm the action 5 was done, the glove controller had a closed grip with moderate pressure of the fingers in order to not have chaos with the object. The prosthetic arm could grab the object accordingly aligning its fingers to the shape of the object in picture and a firm grip on the object by the prosthetic arm was established. The delay was 3 seconds to obtain output.
The delays obtained above was reduced to the maximum with the baud rate management, furthermore on research we found that it can be even more reduced with the use of high- end transceiver modules to almost <0.5 seconds.
The fast flexing of the index finger can also be fixed with the connecting wire adjustment, which is in process. It was possible to obtain desired outputs with certain delays.
Table I- Few different actions obtained in prosthetic arm governed by the glove controller and corresponding error in allignment and delay observed.
Action Number
Glove controller (Right hand movement)
Prosthetic Hand
(Left Prosthetic hand movement)
Error % & Delay
1.
No error observed. Delay of 3 seconds seen.
2.
Fast bend/flex action observed of Index finger. Delay of 3 seconds seen.
3.
No error observed. Delay of 3 seconds seen.
4.
No error observed. Delay of 3 seconds seen.
5.
Moderate grip on the object was obtained with less than 3 second delay.
-
CONCLUSION
The project proposes a mechanical completely active and multifunctional 3-D printed prosthetic arm imitating a normal human hand structurally and functionally. The aim of being able to perform general actions and activities as the normal human hand was met. A functional glove controller with prosthetic arm was successfully built. The glove controller was able to control the actions of the prosthetic arm in most appropriate way, not only the flexing action but the wrist motion was an added advantage for the gripping action of the object. The prototype built is a cost-effective model which can aid prosthesis is most efficient way. Thus, an anthropomorphic 3-D printed prosthetic arm was designed and developed meeting the aim of the project.
REFERENCES
-
Alejandro Canizares, Jean Pazos and Diego Ben´tez, On the use of 3D printing technology towards the development of a low cost robotic prosthetic arm, 2017 IEEE International Autumn Meeting on Power, Electronics and Computing (ROPEC 2017), Ixtapa, Mexico.
-
William Taube Navaraj, Habib Nassar and Ravinder Dahiya, Prosthetic hand with Biomimetic Tactile sensing and force feedback, 2019 IEEE International Symposium on Circuits and Systems (ISCAS), Sapporo, Japan, Japan.
-
Amit Hasan Khan, Fairoz Nower Khan, Lamiah Israt and Md. Saiful Islam, Abdulla Samy, Thumb Controlled Low-Cost Prosthetic Robotic, 2019 IEEE International Conference on Electrical, Computer and Communication Technologies (ICECCT), Coimbatore, India.
-
Huichan Zhao, Kevin OBrien, Shuo Li and Robert F. Shepherd, Optoelectronically innervated soft prosthetic hand via stretchable optical waveguides, December 2016, Science Robotics, Vol. 1, Issue 1, eaai7529.
-
Matthew B. Burn, Anderson Ta and Gloria R. Gogola, Three- Dimensional Printing of Prosthetic Hands, March 2016, The Journal of Hand Surgery.
-
Yu She, Chang Li, Jonathon Cleary and Hai-Jun Su, Design and Fabrication of a Soft Robotic Hand with Embedded Actuators and Sensors, May 2015, Journal od Mechanisms and Robotics.
-
Peter J Kyberd and Adrian Poulton, Use of accelerometers in the control of pactical prosthetic arm,October 2017, IEEE Transactions on Neural Systems and Rehabilitation Engineering, Volume: 25, Issue: 10.
-
Ujwal, Rakshith Narun, Harshell Surana, Naga Surya and Ch Preetham Dheeraj, Voice control based prosthetic human arm, July 2018, International Research Journal of Engineering and Technology (IRJET), Volume: 05 Issue: 07.
-
Panipat Wattanasiri, Pairat Tangpornprasert, and Chanyaphan Virulsri, Design of multi grip patterns, prosthetic hand with single actuator, June 2018, IEEE Transactions on Neural Systems and Rehabilitation Engineering, Volume: 26, Issue: 6 .
-
Mohamad Amlie Abu Kasima, Cheng Yee Lowb, Muhammad Azmi Ayuba, Noor Ayuni Che Zakariaa, Muhammad Haszerul Mohd Salleha, Khairunnisa Johara and Hizzul Hamlia, User friendly LabVIEW GUI for prosthetic hand control using Emotiv EEG headset, 2016 IEEE International Symposium on Robotics and Intelligent Sensors, IRIS 2016, Tokyo, Japan.
-
Shiva Subhashini Pakalapati, G. Govardhana Chary, Atul K. Yadaw, Sushil Kumar, Hitesh K. Phulawariya and Rahul Kumar, A Prosthetic hand control interface using ESP8266 Wi-Fi module and android application, 2017 International Conference on Innovations in Information, Embedded and Communication Systems (ICIIECS), Coimbatore, India.
-
Farah Alkhatib, John-John Cabibihan and Elsadig Mahadi, Data for benchmarking low-cost, 3D printed prosthetic hands, Data in Brief, Volume 25, August 2019, 104163.
-
Jayant Y. Hande, Niket Malusare, SubodhSawarbandhe and HarshalDarbhe, Design of a robotic hand using Flex sensor, December 2015, International Journal of Advanced Research in Electronics and Communication Engineering (IJARECE) Volume 4, Issue 12, .
-
John-John Cabibihan, M. Khaleel Abubasha, and Nitish Thakor, A method for 3D printing patient specific prosthetic arm with high accuracy shape and size, 2018 IEEE Access, Volume 6, 2018.
-
Mohammed Fattah Saqib, Aurnab Islam, MD Labib Arefin Bari, Mir Sadif Ahmed and MD. Arif Abdulla Samy, Gesture controlled prosthetic arm with sensation sensors, 2018 3rd International Conference for Convergence in Technology (I2CT), Pune, India.
-
SR Yadhuraj, BG Sudarshan, SCP Kumar, DM Kumar, Analysis of Linear and Non-linear parameters of HRV for opting optimum parameters in wearable device, materials today: proceedings.
-
Dinesh Mohan, A Report on Amputees in India,The American Orthotic and Prosthetic Association.
AUTHOR PEOFILE
Mr. Atishay M is currently pursuing Bachelors of Engineering (Electronics and Instrumentation) from JSS Academy of Technical Education. He is currently recruited by Accenture. |
|
Dr. D. Mahesh Kumar is presently working as Associate Professor and Head of the Department of Electronics and Instrumentation Engineering, JSS Academy of Technical Education. He is working in teaching field from past 19 years and has published more than 16 publications in journals, national and international conferences. |
|
Ms. Nikhitha P Rao is currently pursuing Bachelors of Engineering (Electronics and Instrumentation) from JSS Academy of Technical Education. She is currently recruited by TCS. |
|
Ms. Jyothi S is currently pursuing Bachelors of Engineering (Electronics and Instrumentation) from JSS Academy of Technical Education. She is currently recruited by TCS. |
|
Ms. Afifa Parveen is currently pursuing Bachelors of Engineering (Electronics and Instrumentation) from JSS Academy of Technical Education. She is currently recruited by Accenture. |