
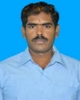
- Open Access
- Authors : Dr. S. Periyasamy , I. Mohamed Akbarali , Premkumar B
- Paper ID : IJERTV9IS060243
- Volume & Issue : Volume 09, Issue 06 (June 2020)
- Published (First Online): 12-06-2020
- ISSN (Online) : 2278-0181
- Publisher Name : IJERT
- License:
This work is licensed under a Creative Commons Attribution 4.0 International License
Numerical Investigation on Vibrational Characteristics of Glass Reinforced Polyester Composite Plate
Dr. S. Periyasamy1, Mr. I. Mohamed Akbarali2, Mr. Premkumar B3.
1Assistant Professor,
2,3PG Scholar
Department of Mechanical Engineering, Government College of Technology, Coimbatore, Tamil Nadu, India
Abstract: Composite materials are increasingly used in aerospace, naval and high performance civil engineering structures due to specific strength, stiffness, corrosion resistance large fatigue life and stealth characteristics. The reinforcement of Composites with industry driven woven fiber materials lead to improved properties of composite structures in terms of acoustical, elastic and thermal properties. Glass fibers are the most commonly used ones in low to medium performance composites because of their high tensile strength and low cost. In woven fiber composites, fibers are woven in both principal directions at right angles to each other (warp and fill Directions). To better understand any structural vibration problem, the resonant frequencies of a structure need to be identified and quantified. Today, due to the advancement in computer- aided data acquisition systems and Instrumentation, experimental modal analysis has become an extremely important tool in the hands of an experimentalist. So, the modal analysis of laminated composite plates is of tremendous importance to predict the dynamic behaviour of structures.
Keywords: Composite, Glass fiber, Modal analysis, vibration.
-
INTRODUCTION
Glass fibers were prepared using melt spinning technique. These involve melting the glass composition into platinum crown which has small holes for flow of molten glass. Continuous fibers can be drawn out through the holes and wound into spindles, while the woven fibers were produced by close arrangements of long fibers similar to the arrangement of tread in clothes. Based on their arrangement they may be classified as unidirectional and bidirectional fibers. Fiber dimensions and to some extent properties can be controlled process variables such as melts temperature and spinning rate. Glass fibre reinforced with resin always possess varying properties with the variation in the direction of plyorientation of ply and number of ply. The different types of glass fibers used based on their mixture of various materials are as follows: A GLASS – Soda lime silicate glasses were used for higher strength durability, and good electrical resistivity
as compared to other glass fiber types.
C GLASS – In the high corrosive environments, Calcium borosilicate glasses used because of its higher chemical stability.
D GLASS- Borosilicate glasses with a low dielectric constant were mainly finds the applications in electrical fields.
E GLASS – Alumina-calcium-borosilicate glasses possess maximum alkali content used as general purpose fibers where strength and high electrical resistivity are required. ECR GLASS Calcium alumino silicate glasses with a maximum alkali content used where strength, electrical resistivity, and acid corrosion resistance are required.
The main objective of this research work is to study and compare numerical result (deflection and natural frequency) on the glass reinforced polyester composite plates.
The different ply and different support is given to the composite model for analysis the vibration behaviour of the plate. The best construction of the glass fiber reinforced with polyester resin composite plate was found by comparing the results of the composite plate .different length and berth ratio is taken for another parameter in this project. The prediction of dynamic behavior of laminated composite plates plays a significant role in the future applications of structural composites. The check influence of glass fiber percentage on the mechanical properties such as tensile strength and Poisson ratio were investigated. These composite plates possess high strength to weight ratio which can be used in winds of high-speed aircraft rockets s and other related space vehicles.
PROBLEM WITH COMPOSITE MATERIAL
There are several inherent difficulties in detecting damage in composite materials as opposed to traditional engineering such as plastics. One reason is due to its non- homogeneity ty and anisotropy; most metals and plastics are formed by one Type of uniformly isotropic material with very well-known properties. On the other hand, composite material can have a widely varying set of material properties based on the chosen fibers, matrix and manufacturing process. This makes model composite complex and often a mix between materials with widely differing properties. The most difficult is the damage in composite material often occurs below the surface, which further prevents the implementation of several detection methods. The importance of damage detection for composite structures is often emphasized over that of metallic or plastic structures because of their load bearing requirements.
The analysis of vibration monitoring data to monitor the characterisic changes in rotating machinery caused by imbalance, misalignment, bent shaft, mechanical looseness, faults in gear drives, defects in rolling-element bearings and defects in sleeve bearings. Vibration Analysis used to detect early precursors to machine failure, allowing machinery to repaired or replaced before an expensive failure occurs.
-
METHODOLOGY
Problem Identification
Material Selection
Selection of modeling dimensions
modeling of composites.
Modal analysis of composite model.
Comparison of Analysis.
Results and conclusions
Fig 1: Methodology flow chart
-
MATERIAL SELECTION
MECHANICAL PROPERTIES POISSON RATIO
The characteristics of fiber Glass composite plate which can be determined completely by four material constants: E1, E2 G12, and u12 where the suffixes 1 and 2 indicate principal material directions. For material characterization of composites, laminate having different layers was manufactured to evaluate the material constants.
. The dimension of the specimen was taken as specified in ASTM D638 is represented in table 3.1 below:
Table 1: Size of the specimen for tensile test.
LENGTH
(mm)
WIDTH
(mm)
THICKNESS
(mm)
165
13
4
PROPERTIES OF GLASS REINFORCED POLYESTER:
The mechanical properties of polyester composite plate are given below,
-
Length of the composite =150 mm
-
Breadth of the composite =75 mm
-
Youngs modulus= 2 x E11 pa
-
Poisson ratio = 0.3
-
Bulk modulus= 1.6667 E11 pa
-
-
MODELLING OF COMPOSITE PLATE
The below figure shows the composite plate with different aspect ratios.
Fig 2: Model of composite plate with 1:1 aspect ratio
Fig 3: Model of composite plate with 1:1 aspect ratio
-
RESULTS AND DISCUSSION
MODAL ANALYSIS
Natural frequencies of the composite plate of 5 ply composite plate with aspect ratio of 1:1 and 2:1 are calculated using Numerical Analysis -ANSYS.
Fig 4: Modal shape of first deformation for aspect ratio 1:1.
Fig 5: Modal shape of second deformation for aspect ratio 1:1.
Fig 9: Modal hape of sixth deformation for aspect ratio 1:1.
Fig 6: Modal shape of third deformation for aspect ratio 1:1.
Fig 4: Modal shape of first deformation for aspect ratio 1:1.
Fig 5: Modal shape of second deformation for aspect ratio 1:1.
Fig 9: Modal shape of sixth deformation for aspect ratio 1:1.
Fig 6: Modal shape of third deformation for aspect ratio 1:1.
Fig 8: Modal shape of fivth deformation for aspect ratio 1:1.
Fig 7: Modal shape of fourth deformation for aspect ratio 1:1.
Fig 7: Modal shape of fourth deformation for aspect ratio 1:1.
Fig 10: Modal shape of third deformation for aspect ratio 2:1.
Fig 11: Modal shape of third deformation for aspect ratio 2:1.
Fig 14: Modal shape of third deformation for aspect ratio 2:1.
Fig 12: Modal shape of third deformation for aspect ratio 2:1.
Fig 15: Modal shape of third deformation for aspect ratio 2:1.
Fig 13: Modal shape of third deformation for aspect ratio 2:1.
Table 2: Natural frequencies in Hertz of 5 ply composite plate
Mode no
5 plies
Length berth ratio = 1:1
Length berth ratio = 2:1
SSSS
CFFF
CCCF
SSSS
CFFF
CCCF
1
594.83
566.63
508.05
388.99
160.44
247.7
2
1232.5
70.92
840.91
541.16
378.24
17.542
3
1232.6
172.83
1461.2
529.91
557.24
74.956
4
2016.7
447.31
1699.9
1029
743.75
111.31
5
2553.8
645.91
1802.9
1280.6
776.02
247.7
6
2713.6
1135.6
2611.3
1284.2
1141.6
324.11
Table 3 Deformation in mm of 5 ply composite plate
Mode no
5 plies
Length berth ratio = 1:1
Length berth ratio = 2:1
SSSS
CFFF
CCCF
SSSS
CFFF
CCCF
1
719
1151
958
506
677
690
2
705
635
1016
503
649
447
3
705
926
888
527
688
598
4
720
804
1036
441
634
460
5
742
989
937
400
714
690
6
1044
1010
1043
506
712
519
NATURAL FREQUENCY OF 5 PLIES MODEL- ASPECT RATIO 1:1
3000
2500
2000
1500
1000
500
0
1 2 3 4 5 6
SSSS CFFF CCCF
Fig 16: NATURAL FREQUENCY OF 5 PLIES MODEL- ASPECT RATIO 1:1
NATURAL FREQUENCY OF 5 PLIES MODEL ASPECT RATIO 2:1
1400
1200
1000
800
600
400
200
0
1 2 3 4 5 6
SSSS CFFF CCCF
Fig 17: NATURAL FREQUENCY OF 5 PLIES MODEL -ASPECT RATIO 2:1
From table 5.2, for l/b ratio 1:1 and 2:1 minimum frequency occurs at all side simply supported and for l/b ratio 1:1 maximum frequency occurs in three side cantilever and one side fixed and for l/b ratio 2:1 maximum frequency occurs in one side cantilever support and three side fixed support.
Table 4: Natural frequencies in Hertz of 10 ply composite plate
Mode no
10 plies
Length berth ratio = 1:1
Length berth ratio = 2:1
SSSS
CFFF
CCCF
SSSS
CFFF
CCCF
1
81.751
2220.9
6667.4
81.749
6179.6
734.32
2
81.751
2969.6
8076
81.751
6883.8
1482.4
3
81.752
5319.3
10822
81.751
7489
2653
4
8249.3
5518.3
11245
3479
9660.3
2727.9
5
8441.7
6007.2
12327
5221..2
10248
2821.1
6
8831.4
6667.9
12527
5858.3
11038
2824.5
Table 5: Deformation in mm of 10 ply composite plate
Mode no
10 plies
Length berth ratio = 1:1
Length berth ratio = 2:1
SSSS
CFFF
CCCF
SSSS
CFFF
CCCF
1
2*E-4
0.16
14.28
8.94*E-4
10.18
0.14
2
2.06*E-4
9.97
0.16
1.61*E-4
0.28
7.05
3
1.12*E-4
0.14
14.65
1.04*E-4
10.31
0.20
4
2.7*E-3
20.25
0.21
5.57*E-3
10.60
14.31
5
14.42
0.47
0.38
7.39*E-2
0.32
13.47
6
2.4*E-2
14.27
14.83
5.06*E-3
0.14
15.18
NATURAL FREQUENCY OF 10 PLIES MODEL -ASPECT RATIO-1:1
14000
12000
10000
8000
6000
4000
2000
0
1 2 3 4 5 6
SSSS CFFF CCCF
Fig 18: NATURAL FREQUENCY OF 10 PLIES MODEL -ASPECT RATIO1:1
NATURAL FREQUENCY OF 10 PLIES MODEL -ASPECT RATIO 2:1
12000
10000
8000
6000
4000
2000
0
1 2 3 4 5 6
SSSS CFFF CCCF
Fig 19: NATURAL FREQUENCY OF 10 PLIES MODEL -ASPECT RATIO 2:1
From table 5.3, for l/b ratio 1:1 and 2:1 minimum frequency occurs at all side simply supported and for l/b ratio 1:1 maximum frequency occurs in three side cantilever and one side fixed and for l/b ratio 2:1 maximum frequency occurs in one side cantilever support and three side fixed support.
Table 6 Natural frequencies in Hertz of 15 ply composite plate
Mode no
15 plies
Length berth ratio = 1:1
Length berth ratio = 2:1
SSSS
CFFF
CCCF
SSSS
CFFF
CCCF
1
54.501
2220.6
6667.5
54.5
6179.7
2756.1
2
54.501
2970
8075.9
54.501
6883.8
2973.7
3
54.501
5319.2
10821
54.501
7488.8
4206.9
4
8249.1
5534
11245
3478.5
9660.6
5109.7
5
8441.9
6007.3
12327
5220.9
10248
5555.8
6
8831.2
6667.8
12527
5858
11038
5687.5
Table 7: Deformation in mm of 15 ply composite plate
Mode no
15 plies
Length berth ratio = 1:1
Length berth ratio = 2:1
SSSS
CFFF
CCCF
SSSS
CFFF
CCCF
1
3.47*E-5
8.96*E-2
11.66
2.29*E-4
8.316
0.11
2
3.475*E-5
8.14
0.09
1.93*E-5
0.15
5.77
3
2.14*E-6
7.61*E-2
11.96
2.67*E-5
8.42
8.21
4
1.48*E-3
16.45
0.11
3.03*E-3
8.65
9.91*E-2
5
11.77
0.26
0.20
0.04
0.17
11.69
6
1.32*E-2
11.65
12.11
2.73*E-3
0.07
9.68*E-2
NATURAL FREQUENCY OF 15 PLIES MODEL -ASPECT RATIO 1:1
14000
12000
10000
8000
6000
4000
2000
0
1 2 3 4 5
SSSS CFFF CCCF
Fig 20: NATURAL FREQUENCY OF 15 PLIES MODEL -ASPECT RATIO 1:1
NATURAL FREQUENCY OF 15 PLIES MODEL- ASPECT RATIO 2:1
12000
10000
8000
6000
4000
2000
0
1 2 3 4 5
SSSS CFFF CCCF
Fig 21: NATURAL FREQUENCY OF 15 PLIES MODEL- ASPECT RATIO 2:1
Glass reinforced polyester composite plate with varying number of plies and different length to width ratio were numerically analyzed and compared. The effect of different parameter like number of layers, aspect ratio and boundary conditions including cantilever, simply supported and fully clamped was investigated. For simply supported boundary there is decrease in natural frequency as well as deformation with increase in number of plies. Thus, the dynamic behavior of the composite plate is greatly influenced by the number of the composite layers. There is 5 to 10 % of reduction in natural frequencies in between 5 plies and 10 plies model. This natural frequency is used to determine the frequency at which resonance occurs.
-
REFERENCE
-
Begum K. and Islam M.A., "Natural Fiber as a substitute to Synthetic Fiber in Polymer Composites: " Research Journal of Engineering Sciences, vol. 2, pp. 46-53, 2013.
-
S.V. Joshi, L.T. Drzal, A.K. Mohanty and S. Arora, "Are natural fiber composites environmentally superior to glass fiber," Composites Part: A, vol. 35, pp. 371-376, 2004.
-
Eberle R and Franze H., "Modeling the use phase of passenger cars in LCI," in SAE Total Life-cycle Conference, Graz Austria, 1998.
-
R. Bhoopathi, M. Ramesh and C. Deepa, "Fabrication and Property Evaluation of Banana-Hemp-Glass Fiber Reinforced Composites,"
in 12th Global Congress on Manufacturing and Management, 2014.
-
M. Ramesh, K. Palanikumar and K. Hemachandra Reddy, "reinforced, Mechanical property evaluation of sisaljuteglass fiber," Composite: Part B, vol. 48, pp. 1-9, 2013.
-
Ebrahim Sadeghpour, Mojtaba Sadighi, Abdolreza Ohadi, 2016 Free Vibration Analysis of a Debonded Curved Sandwich Beam,
European Journal of Mechanics – A/Solids, 57, pp. 71-84
-
Shi Cheng, Pizhong Qiao, Fangliang Chen, Wei Fan, Zhende Zhu, 2015 Journal of Sandwich Structures and Materials, 18, 2, pp 1- 19.
-
Yong-Bae Cho & Ronald C. Averill, 1997 An improved theory and finite-element model for laminated composite and sandwich beams using first-order zig-zag sub laminate approximations, Composite Structure, 37, pp. 281-298.
-
S. Seren Akavci, Huseyin R. Yerli and Ali Dogan, 2007 The first order shear deformation theory for symmetrically laminated composite plates on elastic foundation, The Arabian Journal for Science and Engineering, 32, pp 2B.
-
I. Ergatoudis, B. M. Irons and C. Zienkiewicz, 1968 Curved, isoparametric, quadrilateral elements for finite element analysis, Solids Structures, 4, pp 31-42.
-
Dipak Kr. Maiti & P. K. Sinha. Bending and free vibration analysis of shear deformable laminated composite beams by finite element method. Composite Structures, 29 (1994): 421- 431.
-
R.A. Jafari-Talookolaei and M.T.Ahmadian.Free Vibration Analysis of a Cross-Ply Laminated Composite Beam on Pasternak Foundation. Journal of Computer Science, 3 (2007): 51-56.
-
Kapania RK, Raciti S. Recent advances in analysis of laminated beams and plates: Part I. Shear effects and buckling; Part II. Vibrations and wave propagation. AIAA Journal, 27 (1989): 923 46.
-
Teboub Y, Hajela P. Free vibration of generally layered composite beams using symbolic computations. Composite Structures, 33 (1995): 12334.
-
Bassiouni AS, Gad-Elrab RM, Elmahdy TH. Dynamic analysis for laminated composite beams. Composite Structures, 44 (1999): 81 7.
-
Banerjee, J.R. Free vibration of axially loaded composite Timoshenko beams using the dynamic stiffness matrix method. Computers & Structures, 69 (1998): 197-208.
-
Yuan, F.G. and R.E. Miller. A higher order finite element for laminated composite beams. Computers & Structures, 14 (1990): 125-150. References National Institute of Technology, Rourkela Page 45
-
Krishnaswamy, S., K. Chandrashekhara and W.Z.B. Wu. Analytical solutions to vibration of generally layered composite beams. J. Sound and Vibration, 159 (1992):85-99.
-
Chandrashekhara, K., K. Krishnamurthy and S. Roy. Free vibration of composite beams including rotary inertia and shear deformation. Composite Structures, 14 (1990): 269-279.
-
Reddy JN. Introduction to the finite element method 2nd ed. New York: McGraw Hill, 1993.
-
S. S. Rao, The Finite Element Method In Engineering, 2011.