
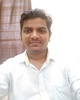
- Open Access
- Authors : Kishan Gautam , Shashikant Shrivastava
- Paper ID : IJERTV9IS060664
- Volume & Issue : Volume 09, Issue 06 (June 2020)
- Published (First Online): 26-06-2020
- ISSN (Online) : 2278-0181
- Publisher Name : IJERT
- License:
This work is licensed under a Creative Commons Attribution 4.0 International License
Skew Bridge Analysis using “ANSYS”
Kishan Gautam Rama University Kanpur, UP
Shashikant Shrivastava
Asst. Professor
Department of Civil engineering, Rama university Kanpur, Uttar Pradesh
Abstract:- This research is all about, for the analyses of skew bridges by the finite element method using eight nodded isoperimetric brick element (serendipity), shell elements and some different elements are also attempted, and has seen that brick elements give better results for shear. ANSYS software (version 7) has been used for the finite element analysis. The modeling which is done is applicable for any skew angle and aspect ratio of slab bridges. In this analysis, different types of
I.R.C. loadings (Class AA Tracked and Class A) have been built in the modeling and also variable live load positions have been considered, to obtained maximum stresses development on the slab. The parametric study and detailed analysis has given a useful understanding for analysis of skew bridges. The main parameters considered were angle of skew, width of bridge and span length.Based on this investigation certain rules for fast examination of skew slab bridges have been suggested in the ends. The consequences of this examination are valuable for configuration engineers working in the investigation of skew slab bridges.
Keywords Bending stress, torsional moment, ANSYS,Skew slab,Principle bending moment,principle moment,tortional
INTRODUCTION
-
GENERAL
Skew bridge is characterized by skewed angle, which can be defined as the angle between the normal to the centerline of the bridge and the centerline of the abutment A skew Bridge is also defined as bridge whose longitudinal axis forms an acute angle with the abutment. The arrangement of such a structure is meet several requirements which includes man-made obstacles, space limitations or mountainous terrains complex intersections, etc. Many bridge decks fabricated today have some type of skew, curve ortaper. For current long vehicles and substantial traffic it is desirable over have straight carriageway at that point to arrange the level bends. In order to optimize the requirements of high speed and safety measures of highway traffic as well as to reduce the Initial investment in the long curved approach roads, itbecame a most important to minimize the number of horizontal curves in the modern highway alignments. This requires for the construction of skew bridges at such all locations where crossings are not orthogonally. In hilly area, skew bridges are most common because road alignment cannot be changed due to topographic conditions; other cases can also be consider like road crossings and railway, which are never orthogonal. In USA nearly 40 percent of the total bridge deck area is on skew alignment and approximately 10 percent of the total area is on heavy skews that ranging between 40° to 70°. In India, present trend is toward the provision for skew bridges in order to optimize the functional requirements as well as to minimize the cost of project. The presence of skew makes the design and
analysis of bridges more difficult as compare to that of right bridge and also has a considerable effect on the structural behavior of decks and on the critical design stresses. The effect of skew in simply supported bridges can be ignore up to 15° of skew and the bridge can be designed as a right angled bridge. However, the effect of skew becomes significant at lower skew angles in integrated bridges and continuous decks, particularly in regions of intermediate supports.
Fig.1 General Description of the Skew Slab
-
OBJECTIVE OF THIS REASERCH PAPER
The main purpose of this research is to develop FEM model using software ANSYS for analysis of skew slab bridges for various IRC loading conditions and to analyze a single lane, double lane and four lane skew slab bridges for various spans (from 6.0 m to 10.0 m span) and for various skew angles (from 0° to 60° ) and to obtain the final design forces.
-
FINITE ELEMENT METHOD GENERAL
For any structural stress analysis problems the major objective is to determine stresses and displacement throughout the structure, which is in equilibrium and is subjected to applied loads. For many structures, it is difficult to determine the distribution of deformation using conventional methods, and thus the finite element method is necessarily used. The basic idea behind finite element method is to obtain the solution of complicated problems by replacing it by their individual elements or component whose behavior is readily understood. These elements are interconnected at specified joints or nodal points which possess an appropriate number of degree of freedom.
STEPS INVOLVED IN FINITE ELEMENT METHOD ANALYSIS
The solution of general static continuum problem by the FEM always follows step by step process.
-
Discretizations and selection of element type:
This step involves dividing the body into an equivalent system of finite elements with associated nodes and choosing the most appropriate element type.
-
Selection of displacement function:
-
-
ELEMENT GEOMETRY
After discretizating the structure, the next step is to choose proper displacement Function. The approximate displacement function within the geometry of element can be given by a simple function in terms of the nodal value of that element. This function is known as shape function. The element geometry in terms of (x, y, z) co-ordinate of a point is expressed in term of nodal co-ordinates as follows:
X = Ni xi
Y=Niyi 1.1)
Z = Ni zi
where xi, yi, zi are the co-ordinate of node i
-
Ni: Shape function of node i
-
n: Number of nodes in the element
Generally for the two dimensional problem rectangle, triangle, and quadrilaterals geometric shape elements are used, which may have straight or curved sides. For the 3-D problems tetrahedron, hexahedron and parallel element are used. Over each type of elements there will be several nodal points, differing in number and location according to the element type. It is obvious and important to note that on nodal point values of the problem variables must be same in the connecting elements. Most commonly elements used for the stress analysis are tabulated in Table: 3.1
-
TYPE OF ELEMENT USED
SOLID73 is used for the three-dimensional modeling of solid structures. The element is defined by eight nodes having six degrees of freedom at each node: translations in the nodal x, y, and z directions and rotations about the nodal x, y, and z axes.
Fig: 2 Element used in the Analysis (8 noded Brick Element)
-
VALIDATION OF RESULTS AND SELECTION OF ELEMENTS TYPE
For the modeling of Slab Bridge following elements were taken and the results were verified with conventional analysis. This was done to select one particular element which is most suited for study.
The test problem taken is a 15 m wide slab of span 10 meters simply supported at both the ends. The material is taken as isotropic concrete with following properties
E (modulus of elasticity) = 28000 N/ mm2 (M30 grade concrete)
v (Poisson's ratio) = 0.152
p (density of concrete) = 0.00025 kg/ mm3
The bridge was analyzed for the self weight only.
Types of elements used as per ANSYS element library. SOLID45 SHELL63 SOLD73 SOLID186
SHELL63 has both bending and membrane capabilities, both in-plane and normal loads are permitted. At each node the element has six degrees of fredom and translations in the nodal x, y, and z directions and rotations about the nodal x, y, and z-axes. Stress stiffening and large deflection capabilities are included. A consistent tangent stiffness matrix option is available for use in large deflection (finite rotation) analyses.
SOLID186 is a higher order 3-D 20-node structural solid element. It has quadratic displacement behavior and is well suited to modeling irregular meshes. The element is defined by 20 nodes having three degrees of freedom per node: translations in the nodal x, y, and z directions. SOLID186 may have any spatial orientation. The element supports plasticity, hyper elasticity, creep, stress stiffening, large deflection, and large strain capabilities. It also has mixed formulation capability for simulating deformations of nearly incompressible elastoplastic materials, and fully incompressible hyper elastic materials.
SOLID45 is used for the three dimensional modeling of solid structures. These elements are defined by eight nodes having three degrees of freedom at each node: translations in the nodal x, y, and z directions. The elements have plasticity, creep, swelling, stress stiffening, large deflection, and large strain capabilities.
The analysis cannot capture the bending behavior with a single layer of elements; for example, in the case of a fixed-end cantilever with a lateral point load, modeled by one layer of elements laterally. Instead, four elements are usually recommended.
The slab was meshed with element size of 500×500 mm. the number of solid elements across depth is 8 layered. The results found out are given below.
The major bending stress along the span comes out to be
2.072 N/mm2, The shear stress along the supports comes out to be 1.66 N/mm2
As seen from the graph below nearly all the elements are giving the same results. However the shear stress is found to be highly distorted for elements other then SOLID73
Fig: 3 Bending Stresses in Slabs Meshed with Different Elements.
Fig 4 Shear Stress Distributions along Span
Now the refinement in shear stress with increase in the number of layers across depth can be seen in the graphs below. The stress distributions are taken at supports at centerline along span.
Fig 6 Shear Stress along Span for Middle Layer for Element Solid73
Fig. 5 Shear Stresses along Depth for Solid73
-
PARAMETERS CONSIDERED
Three different lane bridges single lane (5m wide), double lane (12m wide) and four lane (19m wide) were taken in this study. The width of bridges taken was equal to the full formation width of the road for 2 and 4 lane bridges as per IRC guidelines. Following assumptions were made to make the analysis simpler.
-
Reinforced concrete has been taken as isotropic with the following material properties.
Modulus of elasticity = 28000 N/mm2, Poisons ratio = 0.152, Density of concrete = 0.000025 Kg/mm3
-
The kerb have not been considered integrated with slab, but have been replaced by equivalent self weight acting on the slab. The height and depth of the kerbs is as per IRC guidelines.
-
The modeling analysis of the slab has been done using solid73 with 8 layers across depth and size of 500×500 mm.
-
The support have been kept as simply supported and for that the translation of the middle layer nodes as been restrained in the y direction only, however to restrict secondary movements the nodes at the other support has been restrained in z and x translations also.
-
-
GEOMETRY OF BRIDGE MODEL
-
The 2 lane bridges having different spans of 6m, 8m and 10m were taken. The width of the bridges were taken as the full formation width of 10m. The side kerbs were taken as of 0.4 m wide and of 0.25 m depth. The thickness of bridge were taken as uniform depth of 0.6m for 6m span, 0.75 m for 8m span and 0.9m for 10m span. Each span was distributed into 0°, 15°, 30°, 45° and 60° skew that causes total 15 models of 2 lane bridges were made. The meshing was done by using SOLID73 element. 8 element layers were taken across the depth and 24 elements were taken across the width. The element number along the spans were 12 elements for 6m span, 16 for 8m span and 20 for 10m span. Hence for the skew bridges the element shapes were parallelogram and for right bridges they were square.
-
for single lane bridge only 8 m span was taken and 5 different skew angles 0°, 15°, 30°, 45° and 60° were considered . Hence 5 different models were considered for single lane bridges. The width of bridges was taken as 5m meters including kerbs of 0.225 m width and 0.225 depth provided on both sides. The depth of the slab was taken uniform of 0.750 m. the meshing was kept same as 8 layers of elements across depth, 10 elements along width and 16 elements along span. 3. For four lane bridges the width was
taken equal to full formation width of 19m including 0.750m wide kerbs provided on both sides. The depth of kerbs is taken as 0.3m. Only single span of 8m was considered with five different skew angles of 0°, 15°, 30°, 45° and 60°. The thickness of bridge was taken as uniform depth of 0.750 m. The meshing was kept same as 8 layers of elements across depth, 38 elements along width and 16 elements along the span. Different spans and widths were considered to achieve different aspect ratios of length/width
-
-
MAXIMUM BENDING STRESSES
The results for the normal right bridges were checked and were matched with the conventional analysis. The following three cases were used for the analysis. a) self weight b) self weight + symmetric live loading with respect to the longitudinal axis c) self weight + eccentric live loading with respect to the longitudinal axis. For convenience, the slab has been divided into 5 zones and the maximum stresses developed in those sectors were tabulated and as the stresses in the top and bottom surfaces were equal they were easily converted into bending moments.
Fig 7Skew Slab Showing Various Regions
The following bending stresses were considered for 8m 2 lane Bridge to find out the maximum design moments
-
Stresses parallel to the central line (parallel to x-axis Sx)
-
Stresses parallel to supports (Si)
-
Stresses perpendicular to supports (Sr)
-
Principle Stresses S3 and S2 given by ANSYS.
-
-
Variation of Stresses Parallel to The Central Line (SO) Sx is the stress that developed in the direction of the span length; it is the main design stress in case of right bridges. However it is not the case with the skew bridges as we can see there is a decrease in he tresses with the increase in skew angle.
Fig 8 Sx along the Midspan (self weight)
Fig 9 Sx along the Central Line (self weight)
-
Variation of the Stress Parallel to the Supporting Edges SZ
Similarly the stresses parallel to the supporting edges were also plotted along the central line and mid span of the 8m 21ane Bridge for the 3 different loading conditions.
The following figures explain the variation of the stress with increase in the angle of skew.
Fig 10 Sz along Midspan (self weight)
Fig 11 Sz along Central Line (self weight)
-
Variation of Principle Stress S3
Fig 12 Principal Stress S3 along Midspan (self weight)
Fig 13 Principal Stress S3 along Central Line (self weight)
-
BENDING MOMENTS
Table 1.2 MAXIMUM MOMENTS ALONG SPAN MX (SELF WEIGHT ONLY)
skew angle
0
15
30
45
60
Bending moment kNm
8m 41ane
sagging
167.15
153.13
118.84
76.44
48.63
hogging
0
0
-11.19
-25.57
-32.81
6m 21ane
sagging
74.18
70.53
54.4
36.43
20.8
hogging
0
0
0
-4.49
-11.4
8m 21ane
sagging
163.88
150.88
154.22
77
49.69
hogging
0
0
-13.19
-25.94
-27.19
10m 21ane
sagging
300.3
275.14
215.44
140.19
75.6
hogging
0
0
0
-15.85
-40.5
8m 2 lane
sagging
154.47
142.23
111.78
71.31
45.13
hogging
0
0
0
-7.5
-24.44
Table 1.3 PRINCIPAL BENDING MOMENT M1 CORRESPONDING TO
STRESSES S3 (SELF WEIGHT )
Skew angle
0
15
30
45
60
Bending Moment kNm
8m 41ane
168.54
144.52
115.36
91.02
70.52
6m 21ane
75.86
77.21
62.75
52.36
40.56
8m 21ane
163.38
143.78
131.52
89.65
68.97
10m 21ane
299.98
277.54
246.36
208.25
138.58
8m 2 lane
154.54
134.32
126.34
86.15
61.83
Table 1.4 MAXIMUM MOMENTS PERPENDICULAR TO SUPPORTS MP CORRESPONDING TO STRESSES SP (SELF WEIGHT)
Skew angle
0
15
30
45
60
Bending Moment (kNm)
8m 4lane
166.25
154.63
129.34
98.36
42.9
6m 2lane
75.36
72.21
62.63
46.37
32.12
8m 2lane
165.2
156.29
130.42
179.54
62.14
10m 2 lane
301.54
281.13
232.14
180
106.34
8m 2 lane
153.29
147.65
123.36
92.36
56.14
Skew angle
0
15
30
45
60
Bending Moment (kNm)
8m 4lane
322.26
303.15
248
124.26
112.56
6m 2lane
193.38
182.1
154.52
185
68.41
8m 2lane
324.12
284.11
252.66
116.47
115.26
10m 2
lane
490.32
462.55
396.14
310
241.26
8m 1 lane
316.14
301.16
258.19
186.16
120
Table 1.5 MAXIMUM MOMENTS PERPENDICULAR TO SUPPORTS MP CORRESPONDING TO STRESS SP(SELF WEIGHT + LIVE LOADS)
Fig 15 Maximum Sagging Moments along Span Mx (self weight)
Fig 16 Maximum Hogging Moments along Span Mx (self weight)
-
TORSIONAL STRESSES
Table 1.6 MAXIMUM TORSIONAL STRESSES AT OBTUSE CORNERS (SELF WEIGHT )
skew angle |
0 |
15 |
30 |
45 |
60 |
Torsional stress N/mm2 |
|||||
8m 4lane |
0.23 |
0.55 |
0.98 |
1.05 |
0.7 |
6m 2lane |
0.21 |
0.69 |
0.93 |
1.03 |
0.65 |
8m 2lane |
0.45 |
0.74 |
1.02 |
1.33 |
0.63 |
10m 2 lane |
0.51 |
0.79 |
1.21 |
1.24 |
0.81 |
8m 1 lane |
0.39 |
0.81 |
1.09 |
1.12 |
0.72 |
Table 1.7 MAXIMUM TORSIONAL STRESSES AT OBTUSE CORNERS (SELF WEIGHT + LIVE LOADS)
skew angle |
0 |
15 |
30 |
45 |
60 |
Torsional stress N/mm2 |
|||||
8m 4lane |
0.18 |
0.45 |
0.62 |
0.65 |
0.45 |
6m 2lane |
0.14 |
0.31 |
0.48 |
0.52 |
0.40 |
8m 2lane |
0.17 |
0.41 |
0.60 |
0.62 |
0.48 |
10m 2 lane |
0.16 |
0.48 |
0.75 |
0.78 |
0.56 |
8m 1 lane |
0.12 |
0.31 |
0.53 |
0.58 |
0.42 |
Fig 17 Maximum Torsional Stresses at Obtuse Corners (self weight)
Fig 18 Maximum Torsional Stresses at Obtuse Corners (self weight+ live loads)
1.15 CONCLUSIONS
The following conclusions are made on basis of above discussion and the results presented in the previous chapter.
-
The effect of skew can be considered as a reducing factor for the maximum sagging moments along the span. The maximum sagging moments decrease with increase in the angle of skew and reduce to about one third of the value at right span. However there is a development of hogging
moments at the obtuse corners of the slab and it increases with the angle of skew.
-
With the increase in the angle of skew there is increase in the moments parallel to the supporting edges (MZ)
-
The Maximum principal bending moment (MI) and the moments perpendicular to the supports (Mr) follow the same trend as the moments parallel to the span direction (My), however their magnitudes are higher than the Mx values.
-
Torsion stresses is also development at obtuse corners of the slab and it increases with the increase in skew angles and reaches its maximum value at about 40° and then it decreases.
-
The uplifting of the acute corners can be prevented by providing heavy kerbs or footpaths along the supports as no uplifting was observed in the present study. However there is concentration of shear stresses at Supports near to the placement of live loads in bridges of higher skew. There is also increase of reaction forces at the obtuse corners.
-
There is variation of shear stress distribution across the width of the slab, and it increase tremendously at the obtuse corners of the slab.
At last, it can be concluded that this analysis has produced results which will be useful to the designers and also by analysis using 8 noded brick elements in several layers, it can give accurate results for reactions, shears , moments and torsion. Use of shell elements is simpler and requires less computer time but it gives accurate results for moments and torsions only, and its shear values are not accurate, hence it has limited use to designers.
REFERENCES
[1.] ANSYS manual: A general finite-element program, version 7.0. [2.] Alaa Helba and Kennedy, John B. (1994) "Collapse loads ofContinuous Skew Composite Bridges." Journal of Structural Engineering, ASCE, 120 (5), pp 1395-1414
[3.] Bakht, B. (1988). "Analysis of Some Skew Bridges as Right Bridges." Journal of Structural Engineering, 114(10), pp 2307- 2322. [4.] Bhatt P., L. M. Abdel Hafiz and Green, D. R.(1998). "Direct Design of Concrete Skew Slabs." Computers and Structures. Vol. 30, No. 3, pp 477-484 [5.] Cheung, Y.K., King, I.P. and Zeinkiwicz. (1968) "Slab Bridges with Arbitrary Shape and Support Conditions" Proceedings Institution of Civil Engineering, Vol. 40. No.1, May pp 9-36. [6.] Clark, L.A., (1970)."The Provisions of reinforcement in Simply Supported Skew Bridge Slabs in accordance with Elastic Moment Fields." Cement and Concrete Association, Technical Report No.42.450, Nov. [7.] Chandrakant, A.(1995) "Analysis of Skew Slab Bridges." M.E Thesis University of Roorkee. [8.] Cook, R.D., (2002), "Concepts and Application of Finite Element Analysis" John Wiley & Sons (Asia) Pvt. Ltd., Singapore [9.] Dar, A.K (1986) "Skew Girder Bridge Analysis." M.E Thesis University of Roorkee. [10.] Davis, J.D., S.P.K, and Cheung, Y.K. (1968) "Analysis of Corner Supported Skew Slabs." Building Science, Vol. 3, pp. 81-92.