
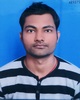
- Open Access
- Authors : Manoj Singh Yadav , Dr. R K Mandloi
- Paper ID : IJERTV9IS060758
- Volume & Issue : Volume 09, Issue 06 (June 2020)
- Published (First Online): 02-07-2020
- ISSN (Online) : 2278-0181
- Publisher Name : IJERT
- License:
This work is licensed under a Creative Commons Attribution 4.0 International License
Lubrication Film Failure Detection in Journal Bearing by Ultrasonic Technique
Dr. R K Mandloi, Manoj Singh Yadav Mechanical Engineering Department, MANIT Bhopal, 462003, India
Abstract: The results of this study would aim to reduce downtime and repair costs for machinery as used in manufacturing environment. The growing emphasis on renewable energy sources like wind, solar and hydroelectric power has resulted in industrial machinery being built in natural ecosystems. To mitigate the possible dangerous environmental effects of these devices, many owners assess and turn to new, better suited lubricants. However, lubricant change periods can surpass years and changing lubricant in large spinning machines is a major undertaking often involving replacement of packings and thorough cleaning as per lube output. With substantial variations in purchasing quality between natural and synthetic lubricants, there must be a good correlation between initial costs and operating benefits. This paper aims at oil film failure with film separation and calculation in journal bearing using ultrasonic technique (NDT), in which the action of specific bearing parameters results in sufficiently understated condition until lube film failure in journal bearing. Bearing life refers to the total number of revolutions (time period) and which working under lubrication film. Lubrication film depends upon many parameters like as; Insufficient lubricants supply; Misalignment loading of bearing on to the shaft; Viscostiy of lubricants; Roughness of surface(Asperities);Temperature; Vibration; Some debries involved in lubricants during working condition from inside the surface and its also depend upon lubricant properties. This work is aimed monitoring the lubrication film failure detection using ultrasonic wave reflection.
Keywords: Lubricant-film measurement; Reflection coefficient; Ultrasound; Fault detection; Fluid film Journal bearing; Film thickness.
INTRODUCTION
The lubricant coating is a gap in a going to lie between the races and the elements that reduces stress and tear, and ensures Smooth running and long service time cycle life for machines. The lubricant film's Thickness and integrating physical is important for the simulation and calculating. However, the lube film thickness is quite difficult to quantify precisely in industrial applications, since the load is spread by an incredibly fragile lubricant layer over a very small lubricated region. The lubricant-film thickness was calculated using both electrical and optical methods. Capacitance and resistance methods are susceptible to surface robustness and involve electrical insulation [13]. Optical methods involve transparent materials in order to be used only in the laboratory, rarely used at outside [4-5]. The ultrasonic method [68] reduces the criteria for electrical insulation and clarity as opposed to the above approaches. The coefficient of reflection of longitudinal
ultrasonic waves has been found to be highly proportional to the thickness of the lubricant film [9]. This technique has been applied to a variety of rollers including journal rollers and ball bearings [1012]. Even so, the use of the ultrasonic procedure is limited by the duration of the ultrasonic pulse being replicated. Total number of checkpoints in the lubricated contact field for a given measure is calculated by a combination of the PRR (Pattern Recognition Receptors) and the intensity of the shaft revolution. A small, quickly moving lubricated touch is formed in conditions with high shaft speeds, suggesting that only high PRR (Pattern Recognition Receptors) can be used to achieve suitable measuring points. In 2005 Zhang et al.[13], and in 2009 Drinkwater et al.[14]. Used an ultrasonic pulse receiver (Pan Metrics 5072PR) to monitor the film thickness of a 506 rpm shaft bearing at its 20 kHz mean repetition pulse frequency.
In 2012 Wan Ibrahim et al. [15] Studied impact of PRR (ranging from 1 to 10 KHz) on calculation precision, where the nominal shaft speed is just 600 rpm. The research shows that there was a higher spatial resolution for the ball profile by utilizing high PRR but only one ball could be pictured. Li et al. [16] have proved this advantage in 2014 study of oil-film in a cylindrical roller bearing showed this benefit. This thesis discusses the usage of a conventional ultrasonic transducer receiver with a set pulses repeated frequency of 100 kHz. So this method should be used for such infrared tests relative to prior studies at higher shaft velocities. In addition, the use of high PRR (Pattern Recognition Receptors) results in many more monitoring points that make for a more precise view of the bearings' lube-film thickness distributed.
Reflection coefficient of oil film (R): If the ultrasound happens between two separate instruments at a line, some energy is expressed and some transmitted. The refection and propagation operation at the limits of the displacement waves relies on the two media's acoustic properties. The proportion of any reflected incident signal (or the coefficient of reflection, R) is given by the well-known equation.
R = (Z1-Z2)/(Z1+Z2) 1
Where Z is the media's acoustic impedance (given by the density and sound speed product) and where the symbol refers to all media.
Transmission coefficient (T): The proportion of the incident signal transmitted can be calculated as
T = 1 R 2
Bulk modulus (B): A liquid's bulk modulus is linked to its compressibility. It is known as the necessary pressure causing the volume of a liquid to change amount. Since most liquids are practically incompressible, very large pressures are needed to induce any substantial volume changes. The bulk modulus for most liquids is around 250,000300,000 psi. The relatively small amount indicates liquids are incompressible. Compressibility is called the inverse of the bulk modulus.
3
Where, c = velocity of sound, B = bulk modulus, = density of the medium
Stiffness of the layer: According to the theory of wave propagation, the material's stiffness or maximal shear module may be calculated by the velocity of wave propagation or shear wave.
Sommerfield number: The sommerfield number is also a dimensionless parameter widely used in journal bearing design. Mathematically,
Life of bearing: Bearing existence is generally described just when the first signs of metal fatigue appears, the amount of hours an actual bearing can work. The standard level of life for industrial applications, named life L-10. Basically placing the L-10 life is the amount of hours of operation that can withstand 90 per cent of the bearings.
Table of literature survey:
Sr. no. |
Author & year |
Title |
1. |
Beamish, S., et al. 2020 |
"Circumferential film thickness measurement in journal bearings via the ultrasonic technique." |
2. |
Xiao, Huifang, Yunyun Sun, and Jinwu Xu. 2018 |
"Investigation into the normal contact stiffness of rough surface in line contact mixed elastohydrodynamic lubrication." |
3. |
Shinde, Anil B., and Prashant M. Pawar. 2017 |
"Multi-objective optimization of surface textured journal bearing by Taguchi based Grey relational analysis." |
4. |
Cubillo, Adrian, Suresh Perinpanayagam, and Manuel Esperon-Miguez. 2016 |
"A review of physics-based models in prognostics: Application to gears an bearings of rotating machinery." |
5. |
Miranda, Gregorio do Couto. 2016 |
The Detection of Journal Bearing Cavitation with Use of Ultrasound Technology. |
6. |
Howard, Thomas Peter. 2016 |
Development of a novel bearing concept for improved wind turbine gearbox reliability. |
7. |
Zhang, Kai, et al. 2015 |
"Ultrasonic measurement of lubricant film thickness in sliding Bearings with overlapped echoes." |
Observation: I studied and brief review of related literatures. In which some research gap has to come for lubrication film failure detection in journal bearing and my consideration is some could have better. We observed that for in ultrasonic techniques for testing of lubrication film failure detection in journal bearing is using devices Transducer, Sensor, Probe, Temperature measuring device etc important role play for analysis of lubricant film failure in journal bearing and some important practical to issues arises in the experiment as transducer location, spatial resolution and focusing, curvature of the bearing shell, surface roughness and form, response time etc. Some errors come due to vibration and temperature, during running in the bearing of rotating part. So calculation point of view reading is not same as per using same lubricant in journal bearing.
Calculation parameters with graph of relations between in those parameter shows the life of lubrication characteristics with the viscosity in the journal bearing and also decided these parameters which type of lubricant can be used in a particular journal bearing it means lube can be change for material to material of journal bearing. Result reveals the
surface layer experimental system produces all kinds of lubricant film thicknesses. These calculations depends upon the Reflection coefficient, Transmission coefficient, Bulk modulus, Stiffness of the layer, sommerfield number and maintain the viscosity with load and speed variations. The continuum model is accurate for all thickness of the films and allows estimation of the lube layers' acoustic impedance across thickness. When do we experiment, the actual load that is radial load and thrust load, speed of shaft, temperature, vibration is not able to applied for comparison with actual working
Condition in the system then predict of their situation at time from using previous data that how much sustain the actual condition in journal bearing and prevention of the film failure in this situation. But prediction or we can say in other words forecasting for this situation of journal bearing is not always true as per to the working condition in journal bearing after assembling of the system. We check weekly for impurity of lubricants to the journal bearing after installation in the system. We analyze that every lubricants having different properties and characteristics, if using in the system on the basis of parameters to that applications.
Film failure has induced when the rotation started then according to prediction analyzing the past experienced that how much pressure, temperature tolerated by lubricants, Reconditioning of journal bearing using same lubricants for operation. My opinion for that to remove this situation of prediction to lubrication film failure detection in journal bearing. We can be used to some software like as either COMSOL multiphysics or ANYSYS, from in which COMSOL is easiest to learn. In COMSOL multiphysics software are many complex phenomenon involved in bearings and their movement. Application of lubrication for these problems is important. In COMSOL software the detection of lube film failure in journal bearing can be predicted under the simulation of different parameters. Evaluation of the key parameter of film failure like load, temperature, vibration and rotation of the speed. As per lube film failure detect we can either resize of journal bearing or change the lubrication for that particular parameters consideration. COMSOL multiphysics using for the simulation of fluid structure interaction (FSI). The applications of the FSI are having many types for example FSI coupling and Laminar flow and turbulent flow etc. Lube film failure in journal bearing inside the condition of lube film failure in which we can also use CFD software for analysis of those parameters. Therefore I will not use any type of model to distinguish thin and thick film when shall be using the software. When did I study the literature, I studied that the first is the spring model and the second is the continuum process model for the processing of lube using two methods. The spring model solution is ideally suited for thin-lube films where the ultrasonic frequency is much greater than the film thickness. The continuum model is accurate and suitable for all film thickness and makes predictions of the acoustic impedance of the lube surfaces across the thickness. So using the software according to the journal bearing researcher obtained and used for lube testing we can easily fix the prediction problem.
CONCLUSION
The study and analysis of many other literatures, my subject concludes that lube film failure in journal bearing is mostly depends upon the four parameters. These parameters are Temperature, Speed of rotation, Load, Vibration of machine. Journal bearing failure is a catastrophic failure, or in other words essential failure in the machine component. The results found are mostly in keeping with theoretical prediction and take into account increased slightly increases sound speed through the lube while under high and low pressure. Ultrasound between journal bearing surfaces is reflected from the lube film. The method has been used to test transient cases in which stage changes in speed and load have been applied. The response time is quick and transient fluctuation in film thickness measured. The ultrasonic wave is mirrored in the pockets of vapor in the cavitation field. The thickness of the oil film in this area cant be determined with sufficient precision using this measurement. This technique has been shown to be a feasible and robust way to calculate the oil film in the bearing of a lube journal. It should have applications with
some reasonable execution in many other kinds of boundary lubrication interaction. Whenever prediction of fault arises than detection of lube film failure can be concentrate on applying the computational methods to forecast the aspects of dynamic system maintenance and breakdown. Precise estimation of failure period of the machinery may help to create more efficient replacement of bearing lube and spare parts.
Future needs and research gaps: With ever-increasing demands imposed on electrical power networks by the large-scale deployment of intermittent power sources (wind, solar, etc.) the demands put on electrical generators are anticipated to only escalate. Furthermore, these variable power sources put undesirable demands on the journal bearings which help them by their nature of variability. Some of these requirements might include higher loading, increased start and stop, wider operating ranges, faster acceleration and thermal cycling. Better understanding of the support bearings is therefore essential in order to allow the new uses of power generation machines. Although current dynamic characteristics of bearings are usually measured within 50%, better precision is strongly sought. Ultimately, the function of journal bearings and lubricants in the operational characteristics is largely unknown and needs to be well established for its wider adoption and adaptation
REFERENCES
-
Beamish, S., et al. "Circumferential film thickness measurement in journal bearings via the ultrasonic technique." Tribology International (2020): 106295.
-
Xiao, Huifang, Yunyun Sun, and Jinwu Xu. "Investigation into the normal contact stiffness of rough surface in line contact mixed elastohydrodynamic lubrication.quot; Tribology Transactions 61.4 (2018): 742-753.
-
Shinde, Anil B., and Prashant M. Pawar. "Multi-objective optimization of surface textured journal bearing by Taguchi based Grey relational analysis." Tribology International 114 (2017): 349-357.
-
Cubillo, Adrian, Suresh Perinpanayagam, and Manuel Esperon- Miguez. "A review of physics-based models in prognostics: Application to gears and bearings of rotating machinery." Advances in Mechanical Engineering 8.8 (2016): 1687814016664660.
-
Miranda, Gregorio do Couto. The Detection of Journal Bearing Cavitation with Use of Ultrasound Technology. Diss. Case Western Reserve University, 2016.
-
Howard, Thomas Peter. Development of a novel bearing concept for improved wind turbine gearbox reliability. Diss. University of Sheffield, 2016.
-
Zhang, Kai, et al. "Ultrasonic measurement of lubricant film thickness in sliding Bearings with overlapped echoes." Tribology International 88 (2015): 89-94.
Nice under working of journal