
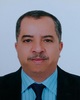
- Open Access
- Authors : Mohamed Y E Selim , Mamdouh T Ghannam , Hosam E Saleh , Moudi T Ali Alameri, Mariam G Zaghloul, Aya Mansour
- Paper ID : IJERTV9IS070368
- Volume & Issue : Volume 09, Issue 07 (July 2020)
- Published (First Online): 30-07-2020
- ISSN (Online) : 2278-0181
- Publisher Name : IJERT
- License:
This work is licensed under a Creative Commons Attribution 4.0 International License
Behavior of Water-Waste Cooking Oil Biodiesel Emulsion for Diesel Engine Performance, Engine Roughness and Exhaust Emissions
Mohamed Y E Selim a, c *, Mamdouh T Ghannam b, Hosam E Saleh c, Moudi T Ali Alameri a ,
Mariam G Zaghloul a, Aya Mansour a
a Mech. Eng. Dept.,
b Chem. and Pet. Eng. Dept.,
UAE University, PO Box 1551, Al-Ain, UAE,
c Mech Power Eng Dept., Helwan University, Cairo, Egypt
Abstract:- The current work involved the use of waste cooking oil (WCO) to produce a biofuel for diesel engine and to generate/prepare a new set of fuels, by emulsifying the WCO biofuel with different water amounts of 5%, 10% and 15%. Important conclusions about the performance of the diesel engine and its exhaust emissions as affected by the water addition have been drawn. All results have been compared with the basic case where the pure diesel fuel is used. It may be highlighted that the engine produced slightly less output torque when the WCO biofuel or its emulsions with water are used, hence the brake specific fuel consumption was slightly increased. On the positive side, the use of water in the biofuel emulsion reduced the dangerous emissions of Nitrogen Oxides gases.
-
INTRODUCTION
The dangerous exhaust gases emitted from diesel engines pollute our environment hence affects the humans health directly and indirectly. It is evident [1] that the gases / particulate matter emitted from such engines not only affects the environment but also generate green house effect. It has been a challenging goal of engineers to reduce the level of dangerous gases such as Nitrogen Oxides in the diesel exhaust by different means. The most promising method of such efforts is producing emulsion of the liquid fuel and the water (Water / Diesel emulsion). It has proved effective to reduce such dangerous gases from diesel exhaust when added to the diesel fuel [2-4].
Adding water to diesel to produce fuel emulsion is also known in other applications e.g. oil spills [5] or transporting heavy crude oil through pipelines [6] or in food production e.g. mayonnaise, or in drug emulsion and even in cosmetics industry (skin lotion). When water is added to the oil (or fuel) it shall separate after short period of time and this will not help in diesel engine fuel system and shall prevent the use of water in combustion chamber associated with the fuel to reduce the dangerous gases which form at high temperature, hence researchers found a method to keep them joining for a longer period of time. That is by adding a surface active agent with to be added within the emulsion to decrease the interfacial tension between the water and diesel phases and to form the stable emulsion. Another use of the agent is to reduce the lumping of the water droplets [7, 8] where it accumulates the film between the water and the fuel particles and make them connected to a longer period of time. The amount of the emulsified agent is critical to keep the emulsion stable [9-10].
The Nitrogen Oxides gases which formed at high temperature from the atmospheric Nitrogen and Oxygen [11] may be reduced by reduced if the maximum combustion temperature is reduced by injecting water to the combustion chamber or adding water to the diesel fuel; e.g. in numbers, adding 20% water to the diesel cuts down the NOx gases by about 57% [12].
The mechanism of water involvement in the combustion is well explained before as the layer of boiled water (at lower temperature) explodes through the outer layer of the fuel oil causing a micro-explosion behavior where the fuel droplets are further atomized in a finer droplets and mixing the fuel with more surrounding air [8]. This produces more complete combustion as well as reducing the maximum combustion temperature. These two effects both reduce the NOx and also reduce the smoke / soot significantly [13-18].
Producing a biofuel may be costly and not attractive, hence it may be more interesting and attractive to reduce the cost of the production or using waste materials to produce the biofuel. One example is using waste or used frying cooking oil as compared to using raw oils [19-20].
Few studies investigated the effects of emulsifying the biofuel with water e.g. [21-22]. In these two studies, the researchers investigated the effects of adding water & alcohol (e.g. Methanol or DEE) to the biofuel. The use of neat biofuel as emulsified to the water is lacking.
Therefore, it is found important to examine the effects of emulsifying the neat biofuel derived from waste cooking oil, with different amount of water, and after stabilizing the emulsion, it was used in a diesel engine. No other additives (e.g. alcohols) was added to the emulsion before testing it in the diesel engine, nor was the diesel engine modified. The objectives of adding the water to the biofuel were to reduce the NOx exhaust emissions and show the effects on the power / specific fuel consumption of the diesel engine. This is to have double advantages of running the engine on alternative source of energy and at the same time reduce the environmental pollution problem.
-
EXPERIMENTAL WORK
-
BIOFUEL PREPARATION
The fuel used in this study is biofuel made from waste cooking oil transesterified with methanol at the ratio of 20% by volume methanol. The yield obtained was 85% of the raw waste cooking oil. The mixture of raw oil and methanol was heated at 60oC with the NaOH catalyst under continuous magnetic stirring of 300 rev/min for one hour. The mixture was left to cool down to the room temperature for 24 hours and then filtered. Diesel fuel obtained locally was used as a reference fuel for all experiments. The physical properties of the used diesel fuel, raw WCO and its biofuel are shown in Table 1.
Viscosity measurements of raw waste cooking oil and its biofuel are carried out by employing Fann Rheometer. Figures 1 and 2 display the effect of shear rate and temperature on the viscosity behavior of waste cooking oil and its biofuel. Figure 1 shows Newtonian behavior for both tested fluids since the viscosity profile does not change with shear rate as reported by Diamante et al. [23]. Heating the waste cooking oil and its biofuel is shown in Figure 2 as viscosity versus temperature at constant shear rate. Both tested fluids of waste cooking oil and its biofuel are strongly affected by temperature influence, for example the viscosity of WCO drops from 95.5 to 29.3 mPas while the biofuel declines from 8.2 to 4 mPas over the examined temperature. The diesel fuel was utilized for comparison purposes.
-
EMULSIONS PREPARATION
To produce a stabilized water-biofuel emulsion, it was necessary to add a surf-acting agent to produce immiscible fluids in the continuous phase. The water in biofuel emulsion was prepared by slow addition of water into the biofuel liquid with 0.2% by volume of surfactant agent with high speed mixing [8]. This is explained in a previous work of the authors [24] where it was done on preparing water-in-diesel emulsion.
In the current work, three samples of water / biofuel (W/B) mixture were prepared using 5%, 10% and 15% by volume water. Optimum mixing speed with mixing times were used to prepare stable emulsions [25]. The prepared samples of emulsion were placed into graduated glass cone-containers to check the stability of the sample. The main criterion for the stable emulsion is the presence of only one phase. If more than one layer is found, it must be considered as unstable emulsion as explained in previous work [25]. The complete details of the preparation of the diesel-water emulsion may be found in [24, 25].
-
EXPERIMENTAL SETUP
The waste cooking oil emulsified with water and compared to the base case is tested in a research engine which has a single cylinder variable compression diesel engine. All running parameters can be measured and stored. It was not needed to modify the engine to run with the biodiesel nor with its emulsion with water. The physical data of the engine is given in Table 2. The fuel flow is measured with an error of 0.1 Pa in measuring the pressure difference. The engine combustion pressure, torque and speed are also measured by high speed data acquisition system.
It is needed to scrutinize the effects of adding water to the biodiesel on the engine perfroamcne, roughness and emission. To carry out this objective, it was needed to do the following tests:
-
Effect of engine speed over the range of 20 to 30 rev/s. During these tests other parameters of the engine were kept constant e.g. injection timing (IT) was kept at 35 oBTDC, and the compression ratio was kept constant (during all experiments) at 22.
-
Effect of load over the range of 0.1 Nm to 15 Nm. During these tests, the engine speed of 20 rps and IT of 35oBTDC were kept constants.
-
Effect of fuel injection timing over the range of 20 to 45 oBTDC. During these tests, the engine speed of 20 rps was kept constant.
-
The engine output brake power (BP) and brake specific fuel consumption (bsfc) are calculated from the measured output torque, engine speed and fuel flow rate [26].
The NOx emission is measured using a gas analyzer known as VARIO plus SE instrumentation which is manufactured by MRU Instruments which have accuracy of 1 ppm. Other experimental errors are listed in Table 3. The exhaust gasses opacity is measured by AVL Opacimeter which can get the opacity continuously.
-
-
RESULTS AND DISCUSSION
The exhaust emission results of the effect of adding water to the biofuel in the three ratios of 5%, 10% and 15% on the NOx gases are shown in Figs. 3, 4 and 5 as a function of the engine speed, load and fuel injection timing. Figure 3 shows the increase in the NOx with the engine speed as expected trend as the fuel burned flow rate increases and the energy released per unit time increases, hence all the cycle temperatures and the NOx go up. Using the biodiesel derived from the WCO reduced the NOx emission as compared to pure diesel as shown in Figs. 3, 4 and 5. The main reason for this reduction in the NOx level may be the lower heating value of the WCO biofuel; see Table 1 for properties; which means less heat is released under the same conditions compared to diesel fuel and less maximum combustion temperature and NOx levels. Also, the WCO biofuel may have a bit more water content as shown in Table 1 which tends to decrease the maximum combustion temperature and the Nitrogen Oxides level.
Figures 3, 4 and 5 also show the effect of adding 5%, 10% and 15% water to the WCO biofuel at different speeds, loads and injection timings. The general trend for all conditions that adding more water reduces the NOx level in the exhaust gasses as shown in Figures 3-5, as reported before in all previous works for diesel water emulsified fuel (e.g. Lin et al. [12]). At all engine
speeds, all injection timings and at most loads, adding more water reduced the NOx level compared to pure biofuel case as well as to pure diesel fuel case. This is due to lower combustion temperature when water is added.
Adding more water, did not increase the exhaust gasses opacity, as shown in Fig. 6. The exhaust gasses opacity did not change much in case of biofuel and its emulsions compared to the diesel case, nor when water was added at 5, 10, or 15%. This is agreement to previous findings for pure diesel fuel case. Some previous works reported a reduction in the soot emissions as water is added to the diesel fuel combustion [27-30].
Figures 7 and 8 show the brake specific fuel consumption and output torque for the WCO biofuel and its emulsions compared to pure diesel. It may be seen that the WCO biofuel produced less output torque (at the same mass flow rate of fuel) and hence higher brake specific fuel consumption. This may be due to the lower heating value of the WCO biofuel; see Table 1 for properties. Adding more water to the WCO biofuel, reduced the output torque and hence increased the bsfc. It has reported by
-
that the micro-explosion phenomena and the associated reduction in the reaction time may improve the combustion in terms of brake specific fuel consumption or thermal efficiency. This was proved valid for low amounts of water e.g. at 10% water in the diesel emulsion. However, for higher water contents, the brake specific fuel consumption was increased.
Figures 9 and 10 illustrate the maximum combustion pressure and maximum combustion pressure rate (which are related to diesel engine roughness [26]) at different fuel injection timings and for different fuels (pure diesel and WCO biofuel and its emulsion). Advancing the injection timing causes the maximum combustion pressure rise rate as the fuel would be injected at lower pressure and temperature which have been shown before to increase the ignition delay period and increases the combustion pressure rise rate. Increasing the combustion pressure rise rate tends to increase the maximum combustion pressure especially before the top dead center point in the compression stroke. Figure 10 shows the WCO biofuel produced less maximum combustion pressure rise rate compared to the pure diesel case. This may be due the lower heating value of the WCO biofuel compared to the pure diesel fuel. However, adding more water (from 5 to 15%) produced higher pressure rise rates compared to the pure WCO biofuel. This is in agreement to the concept of micro-explosions of water-diesel emulsion which tends to increase the reaction rate and reduce the reaction time [31].
CONCLUSIONS
The WCO biofuel and its emulsions with 5%, 10% and 15% water have been used in a diesel engine which was tested under different engine speeds, loads and injection timings. The following conclusions may be summarized:
-
The engine ran very smoothly with WCO biofuel and at the three emulsions with water up to 15% by mass, with no modifications to the engine.
-
The WCO biofuel is comparable to diesel in terms of combustion, engine efficiency and exhaust missions.
-
Adding more water (from 5% to 15%) to the WCO biofuel reduces NOx emissions under all testing parameters.
-
Adding more water to the WCO biofuel did not increase the smoke but increased the rate of combustion pressure rise which leads to increasing the combustion noise too. It increases bsfc as well.
-
Using WCO biofuel and its water emulsions didnt cause the power to be reduced much. Therefore, the biofuel (out of waste cooking oil) and its emulsions may be considered as promising renewable fuel.
ACKNOWLEDGMENT
The authors would like to thank the UAE University for funding the project through the SURE-2018 Projects under the fund code: G00002757. Eng. M El-Said is also acknowledged with his help during the project.
REFERENCES
-
Lin, C.; Pan, J. Corrosion Characteristics of Furnaces Burning with Emulsified Diesel Oil Contained Sodium Sulfate. Corros Prev Control 2001, 47 (3): 83.
-
Nicholls, J.; El-Messiri, I.; Newhall, H. Inlet Manifold Water Injection for Control of Nitrogen Oxides-Theory and Experiment. SAE paper number
690018.
-
Lestz, S.; Melton, R.; Rambi, E. Feasibility of Cooling Diesel Engines by Introducing Water Into the Combustion Chamber. SAE paper number 750129.
-
Andrews, G.; Bartle, K.; Pang, S.; Nurein, A.; Williams, P. The Reduction in Diesel Particulate Emissions Using Emulsified Fuels. SAE paper number
880348.
-
Mingyuan, L.; Christy, A.; Sjoblom, J. In: Sjoblom Ed. Emulsions a Fundamental and Practical Approach; Kluwer Academic Pulishers: Dordrecht, V363, 1992.
-
Pilehvari, A.; Saadevandi, B.; Halvaci, M.; Clark, D. In: Roco MC Ed. Pipeline Transportation of Heavy Crude as Emulsions. Proc. 3rd Int. Symp. Liquid Solid Flows; ASME V75: New York, 1988.
-
Sherman, P. In: Becher Ed. Encyclopedia of Emulsion Technology; Dekker: New York, 1983.
-
Mohamed Y. E. Selim, Mamdouh T. Ghannam, Adel MM Hussien, Effects of Di-Ethyl-Ether Addition on the Water-Diesel Emulsion Fuel Combustion Pressures and Pressure Rise Rates, American Journal of Modern Energy, 2017; 3(6): 146-152.
-
Bobra, M. In: Proceeding of Arctic and Marine Oil Spill Program; Environmental Canada – Minister of Supply and Services: Ottawa, 1990.
-
Eley, D.; Hey, M.; Symonds, J.; Willison, J. Electron Micrograph of Emulsions of Water in Crude Petroleum. J Colloid Int Sci 1976, 54: 462.
-
Muzio, L.; Quartucy, G. Implementing NOx Control: Research to Application. Prog. Energy Combustion Sci. 1997, 23 (3), 233.
-
Lin, C.; Wang, K. Diesel Engine Performance and Emission Characteristics Using Three-Phase Emulsions as Fuel. Fuel 2004, 83, 537.
-
Adiga, K.; Shah, D. On the Vaporization Behavior of water-in-Oil Microemulsions. Combust Flame 1990, 80, 412.
-
Wang, C. Law C. Microexplosion of droplets Under High Pressure. Combust Flame 1985, 59, 53.
-
Crookes, R.; Kiannejad, F.; Nazha, M. Systematic Assessment of Combustion Characteristics of Biofuels and Emulsions with Water for Use as Diesel Engine Fuels. Energy Convers Manage 1997, 38, 1785.
-
Crookes, R.; Kiannejad, F.; Nazha, M. Seed Oil Biofuel of Low Cetane Number: The Effect of Water Emulsification on Diesel Engine Operation and Emissions. J Inst Energy 1995, 68, 142.
-
Crookes, R.; Nazha, M.; Kiannejad, F. Single and Multi Cylinder Diesel Engine Tests with Vegetable Oil Emulsions. SAE paper number 922230.
-
Sheng, H.; Chen, L.; Wu, C. The Drolet Group Micro-Explosions in W/O Diesel Fuel emulsion Sprays. SAE paper number 950855.
-
M. Rakib Uddin, Kaniz Ferdous, M. Rahim Uddin, Maksudur R. Khan, M. A. Islam, Synthesis of Biodiesel from Waste Cooking Oil, Chemical Engineering and Science, 2013, Vol. 1, No. 2, 22-26.
-
Zheng, S., Kates, M., Dube, M.A. and McLean, D.D., Acid-catalyzed production of biodiesel from waste frying oil, Biomass & Bioenergy, 30, 267- 272, Jan.2006.
-
P. Dinesha, Shiva Kumar, Marc A. Rosen, Combined effects of water emulsion and diethyl ether additive on combustion performance and emissions of a compression ignition engine using biodiesel blends, , Energy, 179, pp 928-937, 2019.
-
Kerihuel, M. Senthil Kumar, J. Bellettre, M. Tazerout, Investigations on a CI Engine Using Animal Fat and Its Emulsions With Water and Methanol as Fuel, SAE 2005-01-1729, 2005. SAE 2005 World Congress & Exhibition
-
Lemuel M. Diamante and Tianying Lan, Absolute Viscosities of Vegetable Oils at Different Temperatures and Shear Rate Range of 64.5 to 4835s1, Journal of Food Processing, Volume 2014, Article ID 234583, 6 pages, Published 3 August 2014.
-
MT Ghannam, MYE Selim, Stability behavior of water-in-diesel fuel emulsion, Petroleum Science and Technology 27 (4), 396-411, 2009.
-
Mamdouh T Ghannam, Mohamed Y.E. Selim, Rheological properties of water-in-diesel fuel emulsions, International Journal of Ambient Energy, Volume 36, Issue 1, pages 24-28, 2014.
-
C F Taylor, The internal combustion engine in Theory and practice, Volume II, Combustion, Fuels, Materials, Design, revised ed., The MIT Press, 1985.
-
Raj Kumar Gupta, K.A. Sankeerth, T. Karthikeya Sharma, G. Amba Prasad Rao and K. Madhu Murthy, Effects of Water-Diesel Emulsion on the Emission Characteristics of Single Cylinder Direct Injection Diesel engine – A Review, Applied Mechanics and Materials, Vols. 592-594, pp 1526-1533, 2014.
-
Armas, Ballesteros, Martos, Agudelo: Characterization of light duty diesel engine pollutant emissions using water-emulsified fuel. Fuel, Vol.84 (2005), p.10111018.
-
Niko Samec, Breda Kegl, Robert W. Dibble.: Numerical and experimental study of water/oil emulsified fuel combustion in a diesel engine. Fuel, vol. 81, issue 16, p. 20352044, 2002.
-
United States Environmental Protection Agency: Impacts of Lubrizols PuriNOx water/diesel emulsion on exhaust emissions from heavy-duty engines. EPA report no 420-P-02-007, December (2002)
-
Saif Yoseif Salih, WATER-DIESEL EMULSION: A REVIEW, International Journal of Advances in Engineering & Technology, Vol. 10, Issue 3, pp. 429-436, June, 2017.
-
Morshed, Mahbub, Ferdous, Kaniz, Khan, Maksudur R, Mazumder, M.S.I, Islam, M.A. and Uddin, Md.T., Rubber seed oil as a potential source for biodiesel production in Bangladesh, Fuel, 90, 2981-2986, Jun.2011.
-
Joshi, R.M. and Pegg, M.J. Flow properties of biodiesel fuel blends at low temperatures, Fuel, 86, 143-151, 2007.
-
Table 1 Basic properties of diesel / biodiesel fuels
Properties |
Diesel fuel No. 2 |
Raw WCO |
WCO Biofuel |
Diesel Standard [33] |
Biodiesel Standard [32, 33] |
Density at 25 oC, kg / m3 |
833 |
902 |
792/910 |
850 (at 15.5oC) |
0.88 (at 15.5oC) |
Mass high heating value, MJ / kg |
51.76 |
41.4 |
42.65 |
42.64 |
|
Kinematic viscosity at 40 oC, mm2 / s |
4.16 |
54.53 |
3.29 / 4.2 |
1.3-4.1 |
1.9-6 |
Calculated cetane number |
55/56 |
49 |
54 |
41-60 |
Min 40-51 |
Cloud point, o C |
8 |
12 |
0 |
-15 to 5 |
-3 to12 |
Pour point, o C |
-34 |
6 |
-3 |
-35 to -15 |
-15 to 10 |
Moisture content, % |
0.161 |
0.02 |
0.12 / 1.9 |
0.161 |
0.05 |
Flash point, o C |
>52 |
164 |
150 |
60-80 |
100-170 |
Table 2 Physical data of the research engine at UAE University
Number of cylinders |
1 |
Bore |
76.2 mm |
Stroke |
111.1 mm |
Swept Volume |
0.607 liters |
Max. Speed |
60 rev/sec (3000 rpm) |
Max. Power, Diesel (CR = 20.93) |
9.0 kW, Naturally Aspirated |
Compression Ratio (CR) |
Max. 22 |
Injection Timing |
Variable, 20°- 46° BTDC |
Table 3 Experimental errors
Parameter |
Max Error |
Torque |
±0.1 Nm |
Opacity |
± 1% |
NOx |
±1 ppm |
Speed |
± 0.1 rps |
Volume |
± 1 ml |
Time |
± 1 sec |
Figure 1 Viscosity of waste cooking oil and its biofuel Figure 2 Viscosity of waste cooking oil and its versus shear rate
biofuel versus temperature
Figure 3 Effect of engine speeds and water amounts on Nitrogen Oxides, IT=35o BTDC |
Figure 4 Effect of engine load and water amounts on Nitrogen Oxides, N = 20 rev/s, I = 35o BTDC |
Figure 5 Effect of fuel injection timing and water amounts on Nitrogen oxides, N = 20 rev/s
Figure 6 Effect of engine load and water amounts on exhaust gas opacity, N = 20 rev/s, IT = 35o BTDC
Figure 7 Effect of engine load wand water amounts on brake specific fuel consumption, N = 20 rev/s, IT = 35o BTDC
Figure 8 Effect of fuel mass flow rates and water amounts on engine torque produced, N = 20 rev/s, IT = 35o BTDC
Figure 9 Effect of fuel injection timing and water amounts on maximum combustion pressure, N = 20 rev/s |
Figure 10 Effect of fuel injection timing and water amounts on maximum combustion pressure rise rate, N = 20 rev/s |