
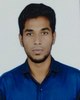
- Open Access
- Authors : Prasanna Venkatesha Sriram P , Mohanraj M , Surendhar C , Anish A
- Paper ID : IJERTV9IS070610
- Volume & Issue : Volume 09, Issue 07 (July 2020)
- Published (First Online): 04-08-2020
- ISSN (Online) : 2278-0181
- Publisher Name : IJERT
- License:
This work is licensed under a Creative Commons Attribution 4.0 International License
Multi Objective Optimization in Drilling of GFRP Composites by using the Application of Artificial Bee Colony (ABC) Algorithm
1st Prasanna Venkatesha Sriram P* Department of Mechanical Engineering Government College of Engineering Salem, India
2nd Mohanraj M
Assistant Professor, Mechanical Engineering Government College of Engineering
Salem, India
3rd Surendhar C Department of Mechanical Engineering
Government College of Engineering Salem, India
4th Anish A
Department of Mechanical Engineering Government College of Engineering Salem, India
Abstract – The purpose of this work is to evaluate the best optimum values for Glass Fiber Reinforced Plastics (GFRP) using Artificial Bee Colony Algorithm (ABC). Composites are made by using glass fiber and epoxy resin to form GFRP. Based on the drilling of GFRP the input characteristics are greatly influenced such as feed, drill speed and drill diameter by various process parameters generally torque, thrust force, delamination factors (both entry and exit) and Surface roughness are considered as output performance characteristics in composite drilling. The influence of input and output parameters is obtained to determine the best optimize values by means of ABC algorithm.
Keywords – Glass Fibre Reinforced Polymer (GFRP), Artificial Bee Colony algorithm (ABC)
I. INTRODUCTION
Drilling process is incredibly utilized for creating riveted and bolted joints during assembly operation of composites with other components. Glass Fibre Reinforced Plastic (GFRP) composite are mostly used in large areas, they were used in industrial fields such on aerospace, aero craft, electrical appliances, automobiles and sports goods due to their properties such as high specific strength, high specific modulus of elasticity, lightweight and corrosion resistance. The nature of cutting hole in a Glass Fibre Reinforced Plastics (GFRP) is effectively dependent on the appropriate decision of cutting parameters, primarily torque and thrust force expanded with feed rate and drill diameter because of increase in SR and shear area, delamination factor is strongly in need on cutting parameters, tool geometry and feed in drilling of composites. A algorithm is a program intended to play out a particular assignment this can be utilized for both straightforward and complex capacities, for example, duplicating the two numbers, entangled capacities like building up an activity in PC programming and it has an exceptional activity like change the convoluted work into basic work and furthermore done a particular undertaking. An extensive overview of all the different processes needed for Composite Materials Parts Manufacturing in current research fields and partly in current industrial applications is given in [1]. The best arrangement for executing strands
during added substance fabricating while picking between the named ideas and glass and carbon fibres, is immediate overprint with glass fibres. [2] To make contemporary composite manufacturing and address the advance composite additive manufacturing [3]. Dissect the innovation of fibre fortified polymers and executed with added substance fabricating with this innovation [4]. The machinability can be achieved by conventional machining process such as turning, drilling and this work grant the main issue, it found that low machinability for FPR Composite material to overcome this problem for conventional machining is far better than that [5]. The carbon and glass fibre composite materials are used under the procedure towards penetrating and processing, fundamentally to pick the work piece quality and planning time [6]. The comparison among regular and orbital drilling to cut unidirectional CFRP material with diamond covered tools and it principally analyses where it produce bore diameter changes, workpiece harms, tool wear just as process duration [7]. The utility of PSO and ABC algorithms to describe turning operations of CFRP composites and optimization of drilling process parameter has been studied for the harmony algorithm [8,9].SR and GFRP were enhanced by expanding cutting speed and the machining parameters like torque and thrust are incorporate with feed, cutting velocity and drill size [10]. The delamination consider under various cutting conditions and it additionally featured to set up the connection between feed rate, drill width and axle speed with the incited delamination in a CFRP [11].The analyse of the tool life during the machining of composite materials under the machining parameters of drill diameter, feed and speed and to clearing up the crack or the failure system [12]. The progression of drilling parameters with execution in dim relational thought it incorporates parameters like shaft speed, feed rate with executing the characteristics of push power surface unpleasantness and delamination factor [13]. The turning operations in GFRP is proposed with the fuzzy interference system with Taguchi approach to achieve optimal machining conditions [14].The GFRP was drilled and all the parameters were examined and the optimal
conditions found out by utilizing Taguchi and response surface methodology[15].
A. Objective
To discover the optimum value for Glass fibre reinforced plastics (GFRP) should be possible utilizing Artificial Bee Colony (ABC) algorithm. From the input parameters like speed, Diameter and Feed to gain output parameters like torque, delamination factor, thrust and SR using for the purpose of finding the optimum values.
II EXPERIMENTATION
Glass fibre is fundamentally a common type of fibre reinforced plastics and it is cheaper and flexible than any other fibre it is most commonly used in the application of, tanks, aircraft, roofing, pipes and boats. Here Epoxy resin LY556 and Hardener is added to make a GFRP composites epoxy resin have high strength and excellent environmental resistance. The pattern is prepared with a 15 X 10 mm rectangular plate to make GFRP material. Composition and preparation of GFRP are 70:30 (Glass fibre: Resin + Hardener), 500g of glass fibre with 150g of Resin and Hardener after the preparation of GFRP it is pressed with the help of compression Moulding to get high strength glass fibre material. Hereafter the GFRP plate has been drilled using Vertical Milling Centre (VMC) with that Drill Tool Dynamometer has been attached to find out thrust, torque. Taguchi Orthogonal Array (L27) method are used for designing the experiments and 6mm 8mm and 10mm drill bits are used for drill the composites. Feed, Diameter and Speed are given as an input and output such as thrust, SR, delamination factor and torque, calculated from readings taken from Drill tool dynamometer and SR Tester readings are given as an input to Artificial Bee Colony (ABC) Algorithm to get the best optimal machining parameters
Fig 1 Drill bit range
TABLE I INPUT READINGS
17 |
1800 |
300 |
10 |
18 |
1800 |
350 |
10 |
19 |
2700 |
250 |
6 |
20 |
2700 |
300 |
6 |
21 |
2700 |
350 |
6 |
22 |
2700 |
250 |
8 |
23 |
2700 |
300 |
8 |
24 |
2700 |
350 |
8 |
25 |
2700 |
250 |
10 |
26 |
2700 |
300 |
10 |
27 |
2700 |
350 |
10 |
Fig 2 Drilled GFRP Specimens
6mm 8mm 10mm
-
Drill Tool Dynamometer
A Multi Tool dynamometer is used to measure torque, thrust force during the use of machine tools and for accurate measurements of forces. The forces during machining are reliant on the depth of cut, feed rate, cutting speed, workpiece material, tool material and other factors.
-
Delamination Factor
The level of delamination could be identified by delamination variable as a proportion of extreme diameter, D of the damage zone around the gap to the hole diameter d.
Fd = D/d
Fig 3 Delamination observed through an optical microscope
SL.NO |
N (rpm) |
F(mm/min) |
D(mm) |
1 |
1000 |
250 |
6 |
2 |
1000 |
300 |
6 |
3 |
1000 |
350 |
6 |
4 |
1000 |
250 |
8 |
5 |
1000 |
300 |
8 |
6 |
1000 |
350 |
8 |
7 |
1000 |
250 |
10 |
8 |
1000 |
300 |
10 |
9 |
1000 |
350 |
10 |
10 |
1800 |
250 |
6 |
11 |
1800 |
300 |
6 |
12 |
1800 |
350 |
6 |
13 |
1800 |
250 |
8 |
14 |
1800 |
300 |
8 |
15 |
1800 |
350 |
8 |
16 |
1800 |
250 |
10 |
TABLE 2 PERFORMANCE CHARACTERISTICS OBSERVED DURING EXPERIMENT
SL.NO |
Thrust |
Torque |
Ra |
Fd (in) |
Fd (out) |
1 |
0.039 |
0.45 |
4.81 |
1.3935 |
1.4421 |
2 |
0.032 |
0.42 |
4.77 |
1.3329 |
1.3782 |
3 |
0.045 |
0.33 |
4.52 |
1.4435 |
1.4723 |
4 |
0.04 |
0.85 |
4.21 |
1.4331 |
1.4967 |
5 |
0.064 |
0.74 |
4.15 |
1.4596 |
1.4893 |
6 |
0.019 |
0.9 |
4.09 |
1.3142 |
1.4057 |
7 |
0.085 |
0.76 |
3.59 |
1.4598 |
1.4994 |
8 |
0.051 |
0.79 |
3.43 |
1.4247 |
1.4851 |
9 |
0.095 |
0.49 |
3.35 |
1.4495 |
1.478 |
10 |
0.092 |
0.72 |
3.32 |
1.3835 |
1.4241 |
11 |
0.02 |
0.96 |
3.29 |
1.3389 |
1.3728 |
12 |
0.082 |
0.75 |
3.27 |
1.4135 |
1.4823 |
13 |
0.029 |
0.47 |
3.25 |
1.4321 |
1.4697 |
14 |
0.076 |
0.69 |
3.23 |
1.4136 |
1.4912 |
15 |
0.024 |
0.39 |
3.19 |
1.3941 |
1.4157 |
16 |
0.036 |
0.25 |
3.13 |
1.4268 |
1.4554 |
17 |
0.061 |
0.81 |
3.09 |
1.4647 |
1.4681 |
18 |
0.079 |
0.71 |
2.97 |
1.4395 |
1.4718 |
19 |
0.058 |
0.67 |
2.91 |
1.4578 |
1.4994 |
20 |
0.063 |
0.7 |
2.86 |
1.4237 |
1.4851 |
21 |
0.21 |
0.44 |
2.82 |
1.4625 |
1.4778 |
22 |
0.048 |
0.32 |
2.74 |
1.3725 |
1.4321 |
23 |
0.091 |
0.53 |
2.69 |
1.3989 |
1.3628 |
24 |
0.041 |
0.29 |
2.62 |
1.4145 |
1.4523 |
25 |
0.066 |
0.83 |
2.58 |
1.4121 |
1.4197 |
26 |
0.032 |
0.22 |
2.46 |
1.4126 |
1.4912 |
27 |
0.046 |
0.31 |
2.41 |
1.4561 |
1.4657 |
III. ARTIFICIAL BEE COLONY ALGORITHM
ABCA is attracted by the foraging behavior of honey bees, it follows a collective intelligent manner while searching the food. It has many qualities like communicate with other bees, sharing the information, store and take decisions based on that. The behavior of real honey bees can be precise in the heads name, food sources, employed and unemployed bees. Here, SR, torque, delamination factor and Thrust force are considered as a honey, to select the best optimal parameters from the given parameters TOPSIS method is used, it convert multi objective variables into single objective variable. The single objective variable are considered as best optimal values, it shows the behavior of honey bees by selecting the particular and best machining parameters.
-
Flow Chart for ABC Algorithm
Determining the coefficient Determining upper and lower limit
Enter number of sample particles Enter number of iteration
Initialization Evaluation
Multi objective to single objective using TOPSIS Selecting the best one and store it in variable
Display
Selection of the best bees Calculation of new employed bees
Unemployed bees Re- Initialization
-
Observing Graphs from ABC Algorithm
Fig 4 Graph comparison of given readings
This graph shows that comparisons of thrust force, torque, SR (Ra), Delamination factor (Fdin) (Fdout) with the help of number of iterations (sample) as we compared the results, minimum values of torque, thrust force, SR, Delamination factor are considered as a best optimal values or best optimal machining parameters. The first graph shows the connection between surface harshness and number of tests, it shows the minimal increment of surface unpleasantness when it moves to most extreme examples and next chart shows the connection among speed and number of tests, it shows the steady change in speed and next chart shows the connection among push and number of tests the current diagram shows slow diminishing in push as indicated by increment in tests, last diagram shows the connection among torque and number of tests it shows the abrupt abatement in torque toward the finish of the examples.
IV RESULTS AND CONCLUSION
In the current examination dependent on the information investigation and exploratory outcomes, the accompanying
ends can be drawn. The approach is utilized to change over the multi reactions (push, torque, Delamination Factor (both section and exit) and surface harshness into a solitary reaction. Presently the ideal mixes of procedure parameters acquired from the Artificial Bee Colony Algorithm.
Optimal Combinations of process parameters are
TABLE 3 OPTIMAL INPUT PARAMETERS
Factors |
Spindle Speed(N) |
Feed(F) |
Drill Diameter(D) |
LEVEL |
2600rpm |
250mm/min |
8mm |
TABLE 4 OPTIMAL OUTPUT PARAMETERS
Thrust(Kn) |
Torque (Kn- Mm) |
Surface Roughness Ra (µm) |
Fd (In) |
Fd (Out) |
0.01678 |
0.06158 |
2.349 |
1.4683 |
1.4974 |
In the Experimental result, the maximum thrust force obtained is 0.21 for the combination of speed 2700rpm, feed rate 350, drill diameter is 6mm and the minimum thrust force obtained is 0.016 for the combination of speed 1800rpm, feed rate 300, drill diameter is 6mm. The maximum torque obtained is 0.96 for the combination of speed 1800rpm, feed rate 300, drill diameter is 6mm and the minimum torque obtained is 0.062 for the combination of speed 2700rpm, feed rate 300, drill diameter is 10mm. The maximum SR obtained is 4.81 for the combination of speed 1000rpm, feed rate 250, drill diameter 6mm and the minimum SR obtained is 2.34 for the combination of speed 2700rpm, feed rate 350, Drill diameter 10mm. The maximum delamination factor at the entry obtained is 1.4749 for the combination of speed 1800rpm, feed rate 300, drill diameter 10mm and the minimum delamination factor at the entry obtained is 1.4683 for the combination of speed 1000rpm, feed rate. The maximum delamination factor at the exit obtained is 1.4912 for the combination of speed 2700rpm, feed rate 300, drill diameter 10mm and the minimum delamination factor at the exit obtained is 1.3728 for the combination of speed 1800rpm, feed rate 300, Drill diameter 6mm.
Based on the ABC Algorithm the best optimized value (Thrust- 0.01678, Torque- 0.06158, SR- 2.349,
Delamination Factor Fin 1.4683 and Fout 1.4974) obtained by the range of 2600rpm speed and 250mm/min feed rate for 8mm drill. And the values achieved from the algorithm are again experimented, from that experiment the values are thrust 0.01782, Torque- 0.06481, SR- 2.458, Delamination Factor Fin- 1.4723 and Fout -1.5147. The both experimental and algorithm values are similar therefore the best optimal values are gotten from this experiment for better machining.
REFERENCES
-
Jürgen Fleischer, Roberto Teti, Gisela Lanza, Paul Mativenga, Hans-Christian Möhring, Alessandra Caggiano. Composite materials parts manufacturing – Manufacturing Technology (2018), DOI 10.1016/j.cirp.2018.05.005.
-
Florian Baumanna, M.Sc. Julian Scholzb , Prof. Dr.-Ing. Jürgen Fleischer Investigation of a new approach for additively manufactured continuous fiber-reinforced polymers Composite Materials Parts Manufacturing(2017), DOI 10.1016/j.procir.2017.03.276
-
Jolie Breaux Frketic, Tarik J. Dickens, Subramani Ramakrishnan Computerized manufacturing and processing of fiber-reinforced polymer (FRP) composites: An preservative review of existing and recent techniques for unconventional materials manufacturing (2017), DOI 10.1016/j.addma.2017.01.003
-
Thomas Hofstatter, David B Pederson, Guido Tosello, Hans N Hansen State-of-the-art of fiber-reinforced polymers in additive manufacturing technologies (2017), DOI 10.1177%2F0731684417695648
-
Fritz Klockea , Anton Shirobokova, Sophie Kerchnaweb, Martin Wahlc , Robby Mannensa , Andreas Feuerhacka , Patrick Mattfelda Experimental investigation of the hole accuracy, delamination, and cutting force in piercing of carbon fiber reinforced plastics, Composite Materials Parts Manufacturing (2017) DOI 10.1016/j.procir.2017.03.297
-
Alexsandra Caggino, Fransco Napolittano, Luigi Nele, Roberto Teti Multi Sensor Monitoring For Tool Wear Forecast In Drilling Of CFRP/CFRP Stacks With Traditional And Innovative Drill Bits, Computation In Manufacturing Engineering (2017) DOI 10.1016/J.Procir.2017.12.233
-
E. Uhlmann, F.Protz, B.Stawiszynski, S. Heldler Ultrasonic Assisted Mlling Of Reinforced Plastics Composite Materials Parts Manufacturing(2017) Doi 10.1016/J.Procir.2017.03.278
-
Robert Voss, Marcel Henerichs, David Harsch, Friedrich Kuster, Konrad Wegener Enhanced Approach For Classification Of Cutting Edge Micro-Geometry In Drilling Carbon Fibre Reinforced Plastics(CFRP), International Journal Of Advanced Manufacturing Technology (2016) DOI 10.1016/S0007- 8506(07)61703-X
-
Stephen Rupp, Robert Voss, Marcel Henerichs, David Harsch, Friedrich Kuster, Konrad Wegener Evaluation of bore exit quality for fibre reinforced plastics as well as delamination and complete fibres (2016) DOI 10.1016/j.cirpj.2015.09.003
-
Xichang Wang , Joseph Ahn, Junyi Lee , Bamber R.K. Blackman , investigation on failure modes and mechanical properties of CFRP- Ti6Al4V hybrid joints with different interface patterns using digital image correlation, Materials and Design (2016),DOI 10.1016/j.matdes.2016.04.005
-
Rahul; Kumar Abhishek; Saurav Datta; Bibhuti Bhusan Biswal; Siba Sankar Mahapatra, Machining piece optimisation during EDM of Inconel 718: a case experimental investigation International Journal of Productivity and Quality Management (IJPQM), Vol. 21, No. 4, 2017
-
H. Malik, R. Sharma, and S. Mishra, "Fuzzy reinforcement learning based intelligent classifier for power transformer faults" (2017)
-
Kumar Abhishek, Saurav Datta, Siba Sankar Mahapatra, Multi- objective optimization in drilling of CFRP (polyester) composites: Application of a fuzzy embedded harmony search (HS) algorithm (2016) , Vol 77
-
H.Hocheng, C.C.Tsao, H.T.chen Utilizing internal icing force to reduce delamination in drilling composite tubes (2016), DOI 10.1016/j.compstruct.2015.11.043
-
T Srinivasan, K Palanikumar, K Rajagopal, B Latha Optimzation of Delamination Factor In Drilling GFR-Polyproplene Composites (2017), Material and manufacturing Vol 32 2.