
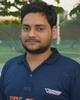
- Open Access
- Authors : Rohan Rai , Sudipto Karmakar , Sharat Anand , Shayak Choudhary
- Paper ID : IJERTV9IS070614
- Volume & Issue : Volume 09, Issue 07 (July 2020)
- Published (First Online): 04-08-2020
- ISSN (Online) : 2278-0181
- Publisher Name : IJERT
- License:
This work is licensed under a Creative Commons Attribution 4.0 International License
Performance Analysis of Multiple Intake Design Methodologies for an open Wheel Race Car Vehicle using Different Simulations
Sudipta Karmakar, Rohan Rai, Sharat Anand, Shayak Choudhary
KIIT University-Institute of Emminence
Abstract:- This paper deals with the performance characteristic comparisons and improvements achieved in the Intake Manifold designs in consecutive seasons for the development of formula style open wheel race car, by the adaptation of new methodologies to predict and control the performance characteristics as required, keeping the requirements in reference to the track and other dependent boundary conditions as well as the drivers feedback. The goal of adapting new methods was to compare how different methodology of designing the parts of the Intake system, i.e., Restrictor, Plenum, Runner and Throttle Body, influence air mass flow rate and pressure fluctuations, resulting to the obtained engine power and torque characteristics. All the previous and current designs of the parts of the Intake were flow tested by simulation using ANSYS Fluent and Simscale CFD. For performance characteristics the entire engine setup with the Intake Manifold was simulated with the help of 1-D virtual engine simulation program Ricardo Wave, to fully compare the two Intake designs between each other with the Stock engine performance characteristics to measure the amount of gain that is achieved from the previously generated design with the new design and Stock Performance characteristic of each part of the Intake was compared with different methodologies to find which one is the most effective one to gain maximum performance. In the end of the comparisons all the values were compared and tallied with the virtual performance characteristics of the Stock engine.
Keywords- Formula Student, FSAE, Intake Design Methodology, KTM RC-390, Intake Comparison, Throttle Body, Restrictor, Plenum, Runner, Ricardo Wave, ANSYS Fluent, CFD, Simscale, David Vizards Rule, Acoustic and Reflective Wave theory, Volumetric efficiency, Convergent-Divergent Nozzle, Helmholtz Resonator theory.
-
INTRODUCTION
-
Intake Manifold
The Intake Manifold is a very essential element of an Internal Combustion engine. The performance of the engine depends on a huge variety of factors; one of them being the design of Intake Manifold. The function of this is to optimally distribute equivalent amount of air to a cylinder. One of the major factors that affect the airflow inside the air Intake system is its own shape. With the use of modern-day computer aided methods like Computational Fluid Dynamics it can be simulated for understanding and studying the nature of airflow inside the Intake Manifold. In Formula SAE (FSAE here onwards), for manufacturing an open wheel race car, the rules board have adopted and mandated a rule, which is, every team has to use a type of engine restriction device with its minimum diameter of no
more than 20mm and the placement of the same should be in-between the throttle valve and the engine inlet port. Due to this restriction considerable amount of pressure drop is observed, and to minimize this loss of airflow to the engine, Plenums are used to accumulate and normalize this air so that there is least surge in the airflow to the engine.
The major idea of designing the Intake Manifold for FSAE application is to design it in such a way that the effect of the Intake restriction to the Intake airflow is minimal so as to counter the pressure drop in the Restrictor. To support this effect a Plenum or air reservoir is used which basically minimizes the pulsating airflow through the Restrictor. So, the volume of the Plenum is most important while considering the design of the Intake Manifold of the engine. Also, the design of the port and Runner of the intake is also important as it plays a crucial role in determining the torque and the nature of the power curve of the engine, with respect to the engine speed in RPM. Hence, these are the most crucial aspects of an engine Intake system to decide while designing the Intake for maximizing the performance output of the engine.
Therefore, the main motive behind this analysis is to compare the performance of the two different intake manifolds, keeping in consideration the similarity of design and method of manufacturing of both.
-
Constraints
-
20mm Restrictor should be placed between the Throttle Body and the engine Intake port.
-
Should be inside the roll envelope of the car.
-
No more than 710 cc engine can be used.
-
The engine should be a 4 Stroke engine.
-
-
Consideration
Engine selection: Internal Combustion Engine
Salient features:
General Engine Details: Model – KTM 390
-
Single Cylinder- DOHC;
-
4 Stroke;
-
Liquid cooled;
-
Electronic fuel injection;
-
Spark ignition;
Engine Design Specifications:
-
Bore – 89mm;
-
Stroke – 60mm;
-
Compression Ratio – 12.88:1;
-
Effective cam duration (for Intake)- 238o
-
Throttle Body diameter – 46mm; Restrictor type- Venturi
Fig. 1: KTM 390 Engine
-
-
DESIGN METHODOLOGY
the manifolds have a Restrictor to comply with the rules, whose major motive is to cause a pressure drop so as to act as a breathing restriction to the engine. There are two approaches to the design of the Restrictor which are, either to have an orifice plate or to have a venturi type design. The vena-contracta or the throat of both the methods can be no more than 20 mm according to the rule. According to both designs a conclusion can be made on the choice of design to be implemented to the Restrictor with respect to their performance and flow characteristics as well as pressure drop characteristics. According to the design, the venturi type has much higher co-efficient of discharge than the orifice plate to a flow, also, in venturi design the pressure drop and design is gradual and more efficient than that of the flow of an orifice so due to this reason the venturi design is the most opted method for the Restrictor design. Both the Restrictors chosen are of venturi type for the same reason and multiple iterations were done for the convergent and divergent angles of the both. Finally, both had an optimized design, but differed in the mass flow rates and the pressure drop characteristics. The detailed chart for both designs has been mentioned in Table1.
Table 1: Comparison between Restrictor designs:
Title
Type-1 Restrictor
Type-2 Restrictor
Inlet Diameter
46 mm
34 mm
Throat Diameter
20 mm
20 mm
Total Length
195 mm
160 mm
C-D angles
C = 13.3o, D = 8.13o
C = 7.97o, D = 5.13o
Fig. 2: Intake Type-1 (Season 2018)
Fig. 3: Intake Type-2 (Season 2020)
-
Restrictor
It is the first and the most important restriction for manufacturing an intake of a formula style race car, without which the same is not acceptable in the competition. Both
-
Runner
This is a very important part to the whole Intake system as this decides the nature of the performance curves which the engine will produce during running. So, there are different methodologies in determining the runne dimensions which can be applicable while designing. In the Type-1 Runner, David Vizards methodology was used, according to which the runner length can be calculated out based on the max torque RPM requirement, taking the diameter of the same to be similar to the Stock diameter of the port and Throttle Body which is 46 mm. From there the length of the runner was calculated, depending upon the RPM level for which the max torque peak is to be achieved. The events of open wheel racing are fully dynamics-based event; hence it is required to get a feedback from the driver about the track suitability. It was considered to be 7000 rpm for Stock max torque rpm for Type-1, so the calculation according to this methodology resulted in a certain length. For Type-2 Intake Manifold design a different approach or methodology was considered, this time; the major topic was about the volumetric efficiency result with respect to the available air pressure Wave during inlet valve open duration, so Acoustic Wave Tuning and Reflective Wave theory was considered which deals with the Tuning of the Runner length with respect to the Reflective Wave frequency and time of its presence with respect to the inlet valve opening duration. So the diameter of the Runner was taken to be same from the last type, hence similar to the stock port opening diameter, i.e., 46 mm but this time from drivers feedback the preference for max torque was required to be tuned for 5000 rpm so that it can
aid to the torque output characteristic of the higher ratio final drive. Thus, the length was calculated out and Quarter Wave length Tuning was done to finalize the length of the Runner which can be accommodated to the chassis. So, these methods were followed for determination of the runner length of a Stock port diameter runner. Also, a trumpet type or bell mouth type collector side design was adopted to maximize and extract out more flow by minimizing the consequent wall shape restriction losses. The trumpet was placed directly at the center of the Plenum to get the full use of the velocity stack at the middle part of the flow according to boundary layer separation theory of the air flow.
Table 2: Comparison between Runner design:
Title
Type-1 Runner
Type-2 Runner
Runner Design Method
David Vizards Rule
Acoustic Wave Tuning and Reflection Wave theory
Runner Diameter
46 mm
46 mm
Runner Length
307 mm
381.77 mm
-
Plenum
Plenum can be considered to be a big expansion volume or container which basically reduces the negative effects caused due to the Restrictor to regain some of the naturally aspirated characteristic of the air to the engine. As the considered engine is a single cylinder unit hence its air flow characteristic is pulsating type so while this pulsating air comes in through the restrictor and enters the Plenum, it minimizes and normalizes the nature to make it near stable before entering into the Runner and hence to the engine. It is hard to accurately determine the volume and shape of the Plenum, but approximate volumes can be found out by both physically and through software tests and the shapes can be optimized and perfected through iteration, simulation and analysis done in modern computer based fluid dynamics simulation tools (CFD) in software like ANSYS, Simscale, Ricardo Wave Vectis etc,. In Type-1 Intake the Stock air box volume was taken as the base volume of the plenum and tests/simulations were done both virtually and physically to optimize the performance of the Intake and also the ECU Fuel Look up tables according to the performance desired by the driver. In Type-2 of the Intake the volume was considered to be roughly 3-10 times of the engine cylinder volume and then to iterate all different volumes possible within this range in a controlled step, sectional volume increase till the desired power characteristic and maximum possible volumetric efficiency was achieved using virtual engine simulation software Ricardo Wave. After this different shape had to be considered and each shape was iterated and simulated for both packaging and Flow characteristics in SolidWorks Assembly and Simscale CFD respectively to reach a point where both parameters are considerable. Finally, this was used to optimize the ECU fuel as per the fuel characteristics of the plenum chamber to find a good balance and desired performance output.
Table 3: Comparison between Plenum designs:
Title
Type-1 Plenum
Type-2 Plenum
Total Volume
3000 cc
3150 cc
Volume Determination Method
Stock Air-box Volume
Iterative method with respect to Volumetric Efficiency
Validation Method
ANSYS Fluent for flow Characteristic and Simscale CFD
Simscale CFD and Ricardo Wave for flow characteristics, Pressure Maximization and Volumetric Efficiency- Maximization
-
Throttle Body
It is the most neglected part of an Intake system which turns out to be the most crucial part of it, especially, in FSAE. The Throttle Body is the most upstream part of the intake system and it determines the flow characteristics that the intake will have. So, the diameter of the throat near the butterfly valve of the Throttle Body is the most important point that determines the flow that will be achieved by that intake system. There are no well-defined methodologies to define the diameter of the intake Throttle Body but by a small calculation and simple simulations we can make a close approximation of how much it should be to suffice and not choke the air flow as well as big enough to not cause flow velocity losses in air. A CFD test can be carried out of the internal flow path of the Throttle Body to determine the characteristic and flow velocity that it develops and to iterate and find out the approximate diameter outlet that should be enough to achieve it. So, in Type-1 Intake to keep things simple and to overcome cost and assembly problems a modified version of the Stock Throttle Body was used where the modification was removal and sealing of the idle motor and shutting the TMAP sensor hole, so its just a simple Throttle Body with only TPS output. In Type-2 of the Intake Manifold the Throttle Body outlet diameter was calculated out by the Reference rpm method and similar dimension or close to similar Throttle Body was found and its internal structure was studied in CFD tool and also it was virtually simulated in Ricardo Wave with the already constrained Manifold to find out the characteristic of the performance curve. Practically, Type-1 Throttle Body has enough diameter to saturate the Restrictor within 50% of throttle opening. But in Type-2 Throttle Body the diameter at the throat is 30mm which is a lower diameter and this allows using the designed Restrictor to the maximum before it reaches full saturation to get a near linear torque band.
Table-4: Comparison between Throttle Bodies:
Title
Type-1 Throttle Body
Type-2 Throttle Body
OEM Manufacturer
KTM 390 Dellorto 46 mm FI Throttle Body
TATA NANO
Dellorto 34 mm FI Throttle Body
Outlet Diameter
46 mm
34 mm
Throttle Body length
86 mm
82 mm
Fig. 4: KTM 390 Stock Throttle Body
Fig. 5: TATA NANO Stock Throttle Body
-
-
CALCULATIONS AND DEPENDENT DECISIONS
-
Restrictor
Mass flow rate calculation is one of the good way to determine the efficiency and performance of a C-D (Convergent Divergent) type nozze design used here as the Restrictor design.
Other way is the pressure achieved at the throat of the Restrictor, which plays a massive role not only for the recovery pressure that will be inside the whole Intake system due to it, but also this data is also very useful for the Mass flow rate determination of the Restrictor.
So, the general mass flow rate formula for this type of design is:
Where,
Q = Mass Flow Rate; A1 = Area at inlet; A2 = Area at throat; p1 = Pressure at inlet;
p2 = Pressure at throat; = Density of air;
So, for Type-1 Intake Restrictor design the opening being of a KTM Stock Throttle Body, its inlet diameter of 46 mm and the throat diameter of 20 mm forms up the diameter for the restrictor. Now, after simulation, at an inlet pressure of 1 bar, the throat pressure was found out to be 56742 Pa and the density of air was 1.225 kg/m3.
So, the mass flow rate for the Type-1 Restrictor came to be 0.0863 m3/s.
Now, for Type-2 Intake Restrictor design the opening being of a TATA NANO Stock Throttle Body so the inlet diameter is 34 mm and the throat diameter is 20 mm. Now, the simulated Restrictor generated a throat pressure of 63652 Pa at 1 bar inlet pressure, with the air density being 1.225 kg/m3.
So, the mass flow rate for the Type-2 Restrictor comes out to be 0.0837 m3/s.
Table 5: Comparison between Restrictor Outputs:
Title
Type-1 Restrictor
Type-2 Restrictor
Throttle pressure
56742Pa
63652 Pa
Inlet Pressure
1 bar
1 bar
Mass Flow Rate
0.0863 m3/s
0.0837 m3/s.
-
Plenum
Engine swept volume – 373 cc (common for both)
Type-1 Intake Plenum volume – equivalent to Stock air box value of the bike = 3000 cc = 8 times the engine swept volume.
Type-2 Intake Plenum volume – 3150 cc = 8.4 times engine swept volume.
Reason- Runner selection methodology was based on Quarter Wave Tuning and inlet valve open duration. Considering the maximum volumetric efficiency of the Stock engine which is 96%, by this volume it is later validated that this volume was ensured for 91.43% volumetric efficiency capability, ensuring a near to Stock like engine performance of the engine with restrictions.
Table 6: Comparison between Plenum Outputs:
Title
Type-1 Plenum
Type-2 Plenum
Volume
3000 cc
3150 cc
Volumetric efficiency range
85.20 %
91.43 %
( )
-
Runner
=
Parameters common for both types of Runners:
{ () }
-
Runner diameter was taken same for both which is also equal to = 44 mm;
-
Stock Throttle Body case for better engine to Runner adaptation (P1) = 90 mm;
-
Inlet port length which adds to the overall calculated Runner length (P2) = 80 mm;
Type-1 Intake Runner calculation methodology: David Vizards rule:
Tuning Rpm = 7000 rpm for max Stock torque;
So, by the rule = 17.8 + {(10 – 7.0) x 4.3} = 30.7cm =
307mm
The actual Runner length that is to be added to the Intake during manufacturing:
Calculated length= P1-P2 = 307-90-80= 137 mm
So, the actual manufacturing Runner length is= 137 mm
Type-2 Intake Runner calculation methodology:
Acoustic Wave Tuning and Reflective Wave theory: Tuning rpm = 5000 rpm (according to the driver requirement for endurance track);
Formula: L = (EVCD*0.25*V*2) / (RPM*RV) – 0.5D
Table 7: Comparison between Runners
Title
Type-1 Runner
Type-2 Runner
Runner length
307mm
381.77
Runner diameter
46mm
46mm
Methodology
David Vizards Rule
Acoustic Wave Tuning and Reflective Wave theory
-
-
-
Throttle Body
So, in Type-1 Intake the Stock Throttle Body was used upstream of the Restrictor for ease of adaptability and sensor retain-ability.
In Type-2 Intake the actual requirement size of the Throttle Body diameter was calculated to get a greater mass flow rate through the Intake system which increases the volumetric efficiency of the engine coupled to this intake. Also, restrictor saturation is at the near end of the band to use all of the restrictor potential.
Formula used:
D = {(154 * No. of Cylinders * Stroke * Bore2 * Max.
Power RPM)1/2 / 67547}
Where,
EVCD = Effective valve closed duration= (ECD)= (720o 238o) + 20o = 502o
V = pressure Wave speed = 1152 ft/s;
D = Runner diameter = 44 mm= 1.73228 inch; RPM = Rotation per minute = 5000 rpm;
RV = Reflective value; L = Length of Runner;
So, from this the length comes out to be = 1527 mm which is too big a length to accommodate in the overall packaging of the car so the forth order Reflective wave is used to get the desired length of the Runner to be able to accommodate in the car which comes to be 381.77mm.
Hence, the manufacture able length is 381.77-P1-P2
= 381.77-90-80= 211.77 mm
This way the exact Runner length was found out for the max toque at that tuned rpm.
Now the resonance frequency was found out by Helmholtz Resonator theory:
Where,
Stroke = 60 mm; Bore = 89 mm;
Max. Power RPM = 9000 rpm; D = Throttle Body Diameter;
So, the required diameter of Throttle Body outlet is= 25 mm.
According to the availability and part price in market survey, TATA NANOs Throttle Body was used which had a throat diameter of 30 mm which is the closest to the calculated value, due to a slight increase of the diameter the max power curve also shifts to the 10000 to 11000 rpm band which was achieved by changing the rpm limiter in the standalone ECU. So, it is proven that for the flow requirement in the manifold the diameter of the Stock Throttle Body provides to be quite big which is good for larger volume of air causing lesser chocking but on the other hand it reduces the saturation requirement which the restrictor requires to keep it in par with the stock performance, hence, the Type-2 Throttle Body being of the approximate correct diameter not only delivers the required flow velocity but also is large enough for air volume requirement to not choke the flow this way the Throttle Body in Type-2 is a better choice out of the two.
Where,
fH =
Title
Type-1 Throttle Body
Type-2 Throttle Body
Outlet diameter
43mm
30mm
Reason
For ease of design
For flatter and long ranging torque curve
Title
Type-1 Throttle Body
Type-2 Throttle Body
Outlet diameter
43mm
30mm
Reason
For ease of design
For flatter and long ranging torque curve
Table 8: Comparison between Throttle Bodies
fH = Resonant frequency for the max torque oscillation of air Wave;
C = Speed of sound = 340 m/s;
S = Area of the Runner = 1520.5308 mm2; L = Length of the Runner = 381.77 mm; V = Cubic capacity of the engine = 373 cc; fH = 176.824 Hz;
-
-
SIMULATIONS AND RESULTS
-
Restrictor
Simulation result of each Restrictor:
Fig. 6: Type-1 Restrictor Simulation
Fig. 8: Restrictor Pressure Comparison
Fig. 7: Type-2Restrictor Simulation
Pressure recovered at the divergent end of Restrictor in Intake Type-1= 70740 Pa
Pressure recovered at the divergent end of Restrictor in Intake Type-2= 92690 Pa
Hence, the Mass flow rate was calculated by the use of venturi-meter formula to actualize the maximum Mass flow rate through the Restrictor.
Boundary common to both types of Intake:
-
Inlet pressure of both type of Intakes was same = 101325 Pa, or 1 bar (as normal atmospheric pressure)
-
Temperature for simulation = 35oC (considering event atmospheric temperature)
Throat pressure of Type-1 Restrictor = 56742Pa; Throat pressure of Type-2 Restrictor = 63652 Pa;
Mass flow rate generated out of Type-1 Restrictor= 0.0856 m3/s.
Mass flow rate generated out of Type-2 Restrictor= 0.0837 m3/s.
Also, from the above pressure contours it is clear that the Type-2 Restrictor is more efficient in pressure regeneration and lesser pressure drop.
Title
Type-1 Restrictor
Type-2 Restrictor
Throttle pressure
56742 Pa
63652 Pa
Inlet Pressure
1 bar
1 bar
Mass flow through it
0.0863 m3/s
0.0837m3/s
Title
Type-1 Restrictor
Type-2 Restrictor
Throttle pressure
56742 Pa
63652 Pa
Inlet Pressure
1 bar
1 bar
Mass flow through it
0.0863 m3/s
0.0837m3/s
Table 9: Comparison between Restrictor Outputs
Fig. 9: Restrictor Flow Rate Comparison
-
-
Plenum
Simulation and result of the whole Manifolds:
Fig. 10: Type-1 Plenum Pressure Simulation
Fig. 11: Type-2 Plenum Pressure Simulation
Maximum pressure at the outlet of Type-1 Plenum= 77043 Pa
Maximum pressure at the outlet of Type-2 Plenum= 93774 Pa
This proves that the air pressure generation inside the Plenum of the Type-2 Intake is much better than the Type-1 Plenum, which in turn proves to be better in the higher volumetric efficiency regions of the ECU Look up table to extract more performance out of the mid to high rpm range of the engine. This volume proves to be good till 91.43% volumetric efficiency of the engine which is more than enough to extract out nearly the full potential of the engine closest to that of the Stock performance out of the engine.
Table 10: Comparison between Restrictor Simulation Outputs
Title
Type-1 Plenum
Type-2 Plenum
Volume
3000 cc
3150 cc
Volumetric efficiency range
85.20 %
91.43 %
Outlet Pressure
77043 Pa
93774 Pa
compared to the Stock engine performance characteristics to really understand the gains that were achieved, as a result of the upgradation of design methodologies that were adopted by the team. So, a comparison has been made between the power and torque characteristics achieved in each of the three cases form the 1-D virtual Engine Simulation Software Ricardo Wave.
-
KTM 390 Stock Performance
Fig. 14: Ricardo Wave Stock KTM 390 Engine
S
Fig. 12: Plenum Result Volumetric Efficiency Comparison
Fig. 13: Plenum Result Pressure Comparison
-
-
OUTPUT COMPARISON
After performing the calculations, simulations and results that were found during comparison the values were
Fig. 15: KTM 390 Stock engine Power curve
Fig. 16: KTM 390 Stock engine Torque curve
Table 11: KTM 390 Stock Engine Performance
Title
Performance achieved
Stock Engine Power output
31.47 kW @ 9000 rpm
Stock Engine Torque Output
31.92 Nm @7000 rpm
-
Type-1 Intake Performance Curves
Fig. 17: Ricardo Wave Type-1 Intake Engine
Fig. 18: Type-1 Intake engine Power curve
Fig. 19: Type-1 Intake engine Torque curve
Table 12: Type-1 Intake Engine Performance
Title
Performance achieved
Type-1 Intake Maximum Power Output
26.58 kW @ 8000 rpm
Type-2 Intake Maximum Torque Output
30.32 Nm @ 7000 rpm
-
Type-2 Intake Performance Curves
Fig. 20: Ricardo Wave Type-2 Intake Engine
Fig. 21: Type-2 Intake engine Power curve
Fig. 22: Type-2 Intake engine Torque curve
Table 13: Type-2 Intake Engine Performance
Title
Performance achieved
Type-2 Intake Maximum Power Output
30.20kW @ 9000 rpm
Type-2 Intake Maximum Torque Output
31.67Nm @ 5000 rpm
Title
Type-1 Intake Manifold
Type-2 Intake Manifold
Throttle Body
KTM 390, 43 mm
Throat
TATA NANO, 30 mm
Throat
Restrictor
46 mm-20 mm, 195 mm Length
34 mm-20 mm,160 mm Length
Plenum
3000 cc Volume
3150 cc Volume
Title
Type-1 Intake Manifold
Type-2 Intake Manifold
Throttle Body
KTM 390, 43 mm
Throat
TATA NANO, 30 mm
Throat
Restrictor
46 mm-20 mm, 195 mm Length
34 mm-20 mm,160 mm Length
Plenum
3000 cc Volume
3150 cc Volume
Table 14: Comparison for all Types final details
Runner length
307 mm
381.77 mm
Runner diameter
46 mm
46 mm
Methodology
David Vizards Rule
Acoustic Wave Tuning and Reflective Wave theory
Performance
26.58 kW @ 8000 rpm and 30.32 Nm @ 7000
rpm
30.20 kW @ 9000 rpm and 31.67 Nm @ 5000
rpm
Runner length
307 mm
381.77 mm
Runner diameter
46 mm
46 mm
Methodology
David Vizards Rule
Acoustic Wave Tuning and Reflective Wave theory
Performance
26.58 kW @ 8000 rpm and 30.32 Nm @ 7000
rpm
30.20 kW @ 9000 rpm and 31.67 Nm @ 5000
rpm
Fig. 23: All Power curve comparison
Fig. 24: All Torque curve comparison
-
-
CONCLUSION
The above-mentioned comparisons are not about the shortcomings of one type of Manifold to the other but the development in the methodologies adapted to achieve better results and performance out of the same engine with lesser losses for overall betterment of the collaborated success of the team. So, these are the performance gains that were achieved by the Type-2 Intake used, in this years scrutineering event, which helped towards achieving better results in the design competition of the open wheel race-car. In this way not only, the desired targets were achieved but also the performance expectatios were fully met.
-
FUTURE SCOPE
Hope that these comparisons and methodology discussion with possible results are helpful as a one place everything paper for gaining knowledge about FSAE type Intake design for the overall betterment of the entire community interested in developing a formula style race car vehicle.
-
REFERENCE
-
Documental Repositories, Team Hermes Racing, KIIT University, Retrieved from: http://hermesracing.in/index.html.
-
Delaney Michael, Intake manifold design for single TV IMs with a plenum, Retrieved from: http://hred.free.fr/Download/Articles%20Techniques/Runner%20 Size%20Calculations.pdf
-
Pratiksha Nallawar, Vinayak Narwade, Palash Patole, Vaibhav Lokhande, Alok Apte (2017), Design and analysis of Intake Manifold using 3-d CFD analysis
-
Luka Lenik 1R, Nejc Mlakar1, Ignacijo Bilu1, Breda Kegl1 (2017), The Optimization of a Race Car Intake System