
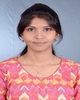
- Open Access
- Authors : Shatabdee Sonawane , P. M. Sonawane
- Paper ID : IJERTV9IS080031
- Volume & Issue : Volume 09, Issue 08 (August 2020)
- Published (First Online): 11-08-2020
- ISSN (Online) : 2278-0181
- Publisher Name : IJERT
- License:
This work is licensed under a Creative Commons Attribution 4.0 International License
Structural Analysis and Optimization of Pitman ARM
Shatabdee Sonawane Prof. P. M. Sonawane
ME Design Student, Department of Mechanical Engineering Assistant Professor, Department of Mechanical Engineering, Sinhgad Academy of Engineering, Sinhgad Academy of Engineering,
Pune, India. Pune, India.
Abstract: Now a days automotive OEM are concentrating on vehicles efficiency and cost effectiveness to reach out with competitors. In order to achieve cost effectiveness optimization of less critical components is necessary. Pitman arm seems to be an overdesigned part. Pitman arm used to steer vehicle is redesigned and modified for achieving less weight and thus cost. Reverse engineering technique is used to model existing pitman arm by CATIA V5 software. The structural optimization is done on the pitman arm using Optistruct tool. Structure of pitman arm is changed by removing the material from the surface where stress value is low. The testing of Pitman arm is carried out for static analysis and fatigue analysis and the results are compared with the experimental results. Static analysis results of existing pitman arm proved that the model is more stable and there was scope for optimization. The weight of original Pitman arm model was 974 gm and that of the new optimized model 840 gm. Weight of the Pitman arm after optimization is reduced by 14%. FEA of optimized Pitman arm has shown 1108.0 microstrain whereas that of the experimental testing shown 1024.39 microstrain. The comparison, between fatigue life results of existing and optimized pitman arm has been performed and it is observed that the pitman arm is having infinite life. The above study confirmed that optimized pitman arm is structurally stable with good fatigue life.
-
INTRODUCTION
Steering system is one of the important systems of vehicle as it directs the vehicle. Pitman Arm is one of the most important steering system components. Pitman arm is attached to steering gear box which is at the end of steering shaft at one end and other end is connected to Track Rod which is consecutively connected to Idler Arm. Pitman arm is fixed at the steering gear box end and gets its input from the same while other end is attached to track rod with ball joint. Input from the steering gear box is in angular motion. But to steer wheels one needs linear motion. This transmission of angular motion to linear motion is carried by pitman arm and wheels get steered in required direction. Two types of failures occur in Pitman Arm. In normal loading conditions no vibrations are present in pitman arm but in unexpected conditions sudden failure takes place. Pitman arm is fixed at steering gear box and other end is connected to track rod by ball joint. Therefore worning of ball joint takes place and failure occurs [1]. Earlier FEA is used to do the modal analysis, fatigue analysis and optimization of Pitman Arm [2]. CATIA V5 CAD software was used to create 3D model for steering arm. Results of FEA shown scope for material removal from regions where stresses developed are much below the limit deformation was also very less [3]. Hierarchical optimization of steering linkage was done by dividing the system into number of sub-system objective functions. Results revealed that hierarchical optimization procedure is more effective and robust as compared to the
simultaneously optimized system [4]. Researcher also studied dynamic simulation of steering mechanism by varying force with respect to time [5]. They concluded that for more safe designs of steering mechanism some importance to dynamic analysis should be given. A new material, austempered ductile material, was proposed for pitman arm. Strength of pitman arm was found to be increased with the new material [6]. New material shown homogeneous microstructure, less prone to failure during the deformation and increased the elongation of the original material making it more deformable.
All above studies indicates the scope for optimization of pitman arm. In present work the Structure of pitman arm is changed by removing the material from the surface where stress value is low. The testing of Pitman arm is carried out for static analysis and fatigue analysis and the results are compared with the experimental results.
-
ANALYTICAL CALCULATION
-
Force Calculation
Force calculations are done analytically to get the magnitude of force acting on steering arm (pitman arm) while driving. Pitman arm of Mahindra Bolero vehicle is selected for analysis and optimization purpose. The total mass of the vehicle is calculated by following equation. Approximate allowed passenger weight and luggage weight for selected vehicle is approximately 360 Kg and 100 Kg respectively.
M1 = Kerb weight + Passenger weight + Luggage M1 = 1615 + 360 + 100
M1 = 2075 Kg
As we are considering the force on pitman arm front axle weight must be considered as it is subjected to higher load. From total weight, 52% of the weight is taken by front axle and 48% is taken by rare axle. Therefore mass on front axle is calculated as,
M2 = 0.52 × 2075 M2 = 1079 Kg
Load acting on single wheel is M3 = 1079 ÷ 2 = 539.5 Kg
Now from vehicle specifications,
-
Width of tire, B = 215 mm
-
Center of rotation (King pin) to wheel, E = 120 mm
-
Coefficient of friction, = 0.7
-
Distance from king pin center to tie rod center, L = 145 mm
The torque required to rotate one wheel is given by,
T = M3
× g × µ × (2) + 2
8
This gives that , pitman arm taken as test specimen will undergo failure after 6.032 ×1018 cycles. From this we can say
T = 525965.593 N
But, two front wheels are handled by single steering arm, therefore the force on it will be doubled,
F = × 2
F = 7254.767 N
-
-
Stress Calculations
Properties of material used for pitman arm are given in table
I
Table- I: material properties of SAE1022
Property
Value
Youngs Modulus (E)
210 GPa
Poissons Ratio ()
0.3
Density ()
7.9 x 10-6 kg/mm3
Yield Strength
740 MPa
Bending stress induced in the pitman arm is calculated by,
it has infinite life as it exceeds 10 lakh cycles.
-
-
FEA ANALYSIS AND OPTIMIZATION
Now to obtain the approximate numerical solution Finite Element Analysis technique is used with ANSYS software.
-
Static Analysis of Original Pitman arm
Meshed model of pitman arm is shown in fig. 1. Minimum size of mesh is 0.388140mm. Number of nodes and elements are 94019 and 28041 respectively. While applying boundary conditions, hole with larger diameter is kept fixed as it is fixed to steering rod. Other end has rotational movement with force 7254.767 N acting on it. Deformation plot, stress plot and strain plot are shown in fig. 2, fig. 3 and fig. 4 respectively. Maximum deformation of 0.27503 mm is observed whereas Maximum stress induced is 167.81 MPa.
Where,
=
= Maximum bending stress
M = Bending moment
y = Vertical distance away from the neutral axis I = Moment of inertia
Now
y = 20 mm
I = 117333.333 mm4,
And, M = F × L1= 1197036.555 N.mm, where L1 = total length of specimen
By putting all these values we get
= 204.04Mpa
-
Fatigue Life Calculations
Number of life cycles completed by ptman arm before failure is calculated by
Fig. 1 Meshing of Pitman arm model
Fig. 2 Deformation plot Pitman Arm
1
= 10 × 2
Sa = Stress amplitude b =- 1 log 0.8
3
c = log (0.8 )²
Sut = Ultimate tensile strength Se = Endurance limit
Now,
Sut= 740 Mpa = 75.51 kg/mm3
For Sa = 0.8 × Sut = 94.387kg/mm3 And Se= 0.5 × Sut = 37.755kg/mm3 b = -0.3054
c = 5.4636
Now by putting all the values in equation, we get,
N= 6.032×1018
Fig. 3 Stress plot of Pitman arm
Fig. 4 Strain plot of Pitman arm
-
Model 1
First model is developed with the radius 5 mm. Deformation plot and equivalent stress plot is shown in fig. 7 and fig. 8 respectively. Maximum deformation of 0.32136 mm is seen and Maximum stress induced is 200.69 MPa.
Stress plot of pitman arm shows that the induced stress (162MPa) is well within the limit and deformation is less (Maximum strain = 0.00079987 mm/ mm ) hence scope for optimization of pitman arm exists.
-
Fatigue Analysis
-
-
Figure 5 shows the fatigue cycle of pitman arm above 1 million cycles. The factor of safety obtained under load conditions is shown in fig. 6. The factor of safety is maximum at center of pitman arm. It is between 10 to15. In automobile industry the maximum factor of safety required is 2. Therefore the scope of removal of material at the center of pitman arm exists.
-
Model 2
Fig. 7 Total Deformation plot for model 1
Fig. 8 Equivalent Stress Plot for Model 1
Fig. 5: Fatigue life above 1 million cycles
Fig. 6: Factor of Safety
-
-
OPTIMIZATION OF PITMAN ARM
Size of shape of Pitman arm to be machined is decided by trial and error method with the help of ANSYS. Three models have been studied as shown below.
Second model is developed with the radius 6 mm. Deformation plot and equivalent stress plot is shown in fig. 9 and fig. 10 respectively. Maximum deformation of 0.34252 mm is seen and Maximum stress induced is 232.25 MPa
Fig. 9 Total Deformation plot for model 2
Fig. 10 Equivalent Stress Plot for Model 2
-
Model 3
Third model is developed with the radius 6.25 mm. Deformation plot and equivalent stress plot is shown in fig. 11 and fig. 12 respectively. Maximum deformation of 0.35423 mm is seen and Maximum stress induced is 255.23 MPa
Fig. 11 Total Deformation plot for model 1
Fig. 12 Equivalent Stress Plot for Model 2
When the results of model 1, model 2 and model 3 are compared it is observed that the equivalent stress for model 3 is
255.23 MPa which exceeds design stress limit i.e. 246.666 MPa. So the size of model is not suitable. So model 2 having slot size with Radius 6 mm gives for optimum results. Structural analysis is done for equivalent strain and fatigue life of Modal 2 as shown below. Maximum strain of 0.001108 is observed in model 2.
Fig. 13 Equivalent Strain plot for Model 2
Fig. 14 Fatigue life For Model 2
FEA results of original Pitman arm and optimized model are shown in table II. Comparison is done on the basis of deformation, stress, strain and fatigue cycle.
Table II: FEA results of original Pitman arm and optimized model.
Parameters
Original pitman arm
Optimized model with 6 mm radius and thick slot
Deformation (mm)
0.27503
0.34252
Stress (MPa)
161.87
232.25
Strain (mm/mm)
0.00079987
0.001108
Fatigue life (cycles)
48803 x 106
15110 x 106
Though the deformation, stress and strain of optimized model is increased however it is still in the permissible limit. Also the number of cycles to be completed by Pitman arm is more than 1 million cycle.
-
EXPERIMENTAL VALIDATIONS
Manufacturing
Machining of optimized pitman arm is done by using re-machining original arm. On vertical drilling machine required shape and size slot was created and then finishing is done by using grinder. Drilling slot is developed by using vertical drilling machine. For drilling direct speed of 525 RPM and gear speed of 105 RPM is used. And drill tool of diameter 12 mm made up of Carbide Centre material is used to drill required size of hole. After this for applying boundary conditions fixture was manufactured. Fig. 15 shows the Pitman arm with fixture. Pitman arm with strain gauge is shown in Figure 17.
Fig. 15 Pitman arm with fixture applying boundary conditions
Fig. 16 Pitman arm with strain gauge
Experimental Testing:
Universal testing machine was used to apply required load (.7254.767N) at free end of pitman arm. Strain gauge was mounted on Pitman arm. When load was acting on arm strain gauge measured strain induced in the arm using strain logger. Then from these readings strain against stress graph was obtained. And stress is calculated and verified.
Figure 17: Testing of Pitman arm under UTM
Obtained results of experimental testing are compared with the FEA results.
It is shown in table III
-
RESULTS
Table III: FEA result for original and optimized model
Model
Original model
Optimized model with 6 mm radius and thickness slot
Deformation (mm)
0.27503
0.34252
Stress (MPa)
161.87
232.25
Strain (mm/mm)
0.00079987
0.001108
Fatigue life (cycles)
48803 – 16
15110 – 16
From Table 4 we can see that, total deformation values for original model and optimized model in ANSYS analysis is negligible. And maximum life is also same.
FEA and Experimental results for Strain:
Now after going for machining and Strain Gauge Testing using UTM as shown in figure 36 we got results for strain induced in the arm as shown in figure 36. Strain induced in pitman arm is 0.001204, form which stress is calculated as 215.04 which is below the design stress limit.
Table IV: FEA and Experimental strain Results
974 gm and that of the optimized model is 840 gm. Therefore weight of the component is reduced successfully upto 14% after optimization.
-
CONCLUSION
-
-
Static analysis results of existing pitman arm proved that the model is more stable and there was scope for optimization The Pitman arm is optimized. The weight of original model is 974 gm and that of the optimized model is 840 gm. Weight of the component is reduced successfully upto 14% after optimization.
-
This optimized model is when tested, the strain value after the analysis using ANSYS is 1108.0 microstrain and that of the experimental testing is 1024.39 microstrain.
-
The comparison, between fatigue life results of existing and optimized pitman arm has been performed and it is observed that the pitman arm is having infinite life.
-
The above study confirmed that optimized pitman arm is structurally stable with good fatigue life.
ACKNOWLEDGEMENT
The research support provided by the Sinhgad Academy of Engineering is greatly appreciated. Also, special thanks to the Yogeshwar steels and NDT testing laboratory, pune for providing machining and testing support respectively.
REFERENCES
-
Cristina Elena Popa, Steering System and Suspension Design for 2005 Formula SAE-A Racer Car.
-
Pradeep B Patil, P. D. Darade, K. R. Jagtap, D. N. Korade, Modal Analysis, Fatigue Analysis and Optimization of Pitman Arm Using FEM, International Journal of Research and ScientificInnovation (IJRSI) | Volume V, Issue IX, September 2018 | ISSN 23212705.
-
Sijith PM ShashankGawade S.S Kelkar CAE Analysis and Structural Optimization of PitmanArm International Engineering Research Journal, March 2018,1-5
-
Gang Qin, Ying Sun, Yunqing Zhang and Liping Chen, Analysis and Optimization of the Double-Axle Steering Mechanism with Dynamic Loads, The Open Mechanical Engineering Journal, 2012, 6, (Suppl 1-M2) 26-39.
-
V.D.Thorat, S.P.Deshmukh, Rigid Body Dynamic Simulation of Steering Mechanism, International Journal of Research in Engineering & Advanced Technology, Volume 3, Issue 1, Feb-Mar, 2015, ISSN: 2320 8791.
-
Lizbeth Huerta Larumbe, Eduardo Hurtado Delgado, M. Alvarez-Vera, Pedro Pérez Villanueva, Forming process using austempered ductile iron (ADI) in an automotive Pitman arm, Int J AdvManufTechnol (2017) 91:569575.
-
Model |
FEA Strain (mm/mm) |
Experimental Strain gauge testing strain (mm/mm) |
Optimized model with 6 mm radius slot |
0.001108 |
0.001204 |
Weight reduction:
Table V: Weight comparison of original and optimized model
Model |
Original Model |
Optimized Model |
Weight (gms) |
974 |
890 |
From table 4 it can observe that FEA strain results and experimental strain gauge testing results are nearly same and equal. So optimized pitman arm is safe under normal loading conditions. Also the weight of original pitman arm model was