
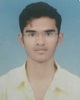
- Open Access
- Authors : Chetan S. Patel , Jitendra A. Gaikwad
- Paper ID : IJERTV9IS080315
- Volume & Issue : Volume 09, Issue 08 (August 2020)
- Published (First Online): 03-09-2020
- ISSN (Online) : 2278-0181
- Publisher Name : IJERT
- License:
This work is licensed under a Creative Commons Attribution 4.0 International License
IoT based Augmented Reality Application for Diagnostic vehicles condition using OBD-II Scanner
Chetan S. Patel(M.Tech) Dept.of Instrumentation & Control Engg. Vishwakarma Institute of Technology,
Pune, India.
Prof. Jitendra A. Gaikwad
Dept. of Instrumentation & Control Engg. Vishwakarma Institute of Technology, Pune, India.
Abstract- Transportation accident rate are still being a serious challenge in several countries .There are several factors that would because transportation accident, particularly in vehicles internal system drawback. To overcome this drawback, OBD-II scanning technology has been created to diagnostics vehicles condition. OBD-II scanner obstructed to OBD-II port or usually known as Data link Connector(DLC), and at the moment it sends the diagnostics to Raspberry Pi via Bluetooth property. These diagnostic parameters are keeping into the cloud server (like Azure, AWS, Thingspeak, Google, etc.). We tend to use a Central Event Processor (CEP) at each the smart phone and therefore the backend to detect and notify unsafe and abnormal events in real time. Lets say, CEP engine at the smart phone will alert the driving force concerning rising Engine oil temper- ature and fast fuel drops. The Augmented Reality app visualizes each real-time record from sensors and alerts. Conjointly alerts are sends to registered email id with faulty parameters. We tend to test the system on actual vehicles.
Keywords: Internet of Thing, vehicle Diagnostic, OBD-II scanner, Driver Monitoring, Augmented Reality, Vuforia.
-
INTRODUCTION
An automotive is not any additional an expensive hap- piness of someone. Its rather become associate integral a part of a contemporary family. The usage of vehicles every- where the worlds has drastically hyperbolic throughout the last decade. Over sixty million traveler cars are factory-made within the year of 2012 [1]. This speedy increase of vehicles has diode to several considerations for a spread of individuals and organizations. To Illustrate, all parties (i.e., drivers, in- surance corporations, fleet vehicle managers, and low social control authorities) are involved concerning reckless driving and driver anomalies. Moreover, those who are willing to buy and sell cars are involved concerning the condition of the vehicle and its maintenance.
OBD-II stands for, on-Board Diagnostic could be a comput- er-based system developed by Automobile makers for diag- nosing automotives. It focuses on diagnosing the perfor- mance of car's engine to check any errors in car's engine components. OBD-II connects with DLC within the vehicle. OBD-II scanner can detect almost all the problems with the vehicle. Such as engine coolant temperature, engine oil tem- perature, RPM, etc. However, OBD was only for scanning the vehicles diagnostics. ELM-327, which is used in the proposed system, is one such OBD-II adapter where the data read from the OBD-II port are transmitted via Bluetooth upon pairing. To reading, processing, and showing the data, it needs Microcontroller. Microcontroller is a microprocessor
system that installed in the chip. Microcontroller is different with microprocessor that used by PC because usually general microcontroller already filled with supporting minimal com- ponent system, such as memory and I/O interface. In another side, microprocessor usually only filled by CPU. Nowadays a lot of different tools are used that can control device digital- ly. However, we have chosen a Raspberry Pi, which is having available for both functionalities of microcontroller and a microprocessor. Raspberry Pi is a mini computer which has inbuilt CPU.
1.1 PROPOSED SYSTEM
In our work we've tried to directly retrieve values from vehicle microcontroller in vivo (i.e. throughout vehicle op- eration), using the OBD-II (on Board diagnostic version 2) protocol. As mentioned, vehicle electronic units communi- cate with one another through a network (CAN Bus or simi- lar) for observation and information transfer (errors, value adjustments).OBD could be a diagnostic and coverage capability of a vehicle permitting the vehicle operator or technician to access the standing of the engine subsystems. Vehicles typically provide an external port which allows the mechanic to retrieve values and read errors and identify the source of the error code. The access to the monitored values is achieved through OBD II scanners. In this context, we've selected a collection of key parameters, in brief discuss the operation of the sensors that are responsible for observation them and, exploitation the OBD-II proto- col, we've retrieved them in real time. In addition, they have been used for diagnosis of vehicle and gives information about fault equipment.
-
LITERATURE REVIEW
In [1] How to configure a raspberry pi and OBD-II what type of technology is used to access the values of vehicle fitted sensors.
In [2] Calculation of fuel consumption and what parameters are needed of OBD-II.
In [3] Basic understandings of vehicle diagnostic parameters.
-
SYSTEM ARCHITECTURE
The proposed system is capable of collecting, storing, and analyzing vehicular data for a long period of time. As shown in Fig. 1 the Raspberry Pi pulls the vehicular data us- ing an OBD-II scanner to Bluetooth interface. The collected data is then preprocessed and sent to cloud servers (like az-
ure, aws, thingspeak, etc.) using the Internet connection. To pull data in cloud server for performing analytics of detecting a vehicles engine condition, detects fault occurs in a specific part of vehicle which affects in a vehicle. And all these diag- nostic parameters are displays in augmented reality mobile application. System performs two major roles throughout the diagnosis-
-
Receiving data from OBD-II (ELM327) adapter- The OBD-II adapter is connected to vehicles DCL. Another side Raspberry Pi Nano Bluetooth Dongle is connected to raspberry pi then connecting Raspberry pi and OBD-II via Bluetooth and communicating with the vehicle using OBD2 Parameter IDs (PIDs). Each PID provides certain information about the vehicle, e.g., speed, engine rpm, fuel consumption, and error codes. The received data are sent to cloud server.
-
Monitor Vehicle- The augmented reality based mobile app consists of a Complex Event Processor (CEP). Com- plex event processing can be regarded as a service that receives and matches lower-level events and generates higher-level events in real time. In this application, pulls the vehicle diagnostic data which is stores in cloud serv- er.CEP has the capability to detect relevant events in in- coming data streams according to a predefined set of queries. For example, queries will be additional to
System monitor parameters which are used for diagnose the vehicle for maintenance. Parameters are as follows:
-
Engine Coolant Temperature: Coolant temperature is queried from the OBD2 adapter sporadically and is for- warded to the CEP engine on the mobile app. Received temperature readings are averaged over a pair of minutes employing a time window. If the aver- aged worth is larger than the given temperature threshold (we used 104°C). The driver is alerted immediately about the possible overheating.
-
Engine Oil Temperature: Engine oil temperature can be retrieved using OBD2 Mode 01 PID 5C If the oil temperature is simply too low whilst the engine rpm is high the produced water and Sulfur as by-products of the combustion system can form acids and harm the engine bearings. System generates an alert, if the engine oil temperatre is not within the desired operating range when the average engine rpm is greater than a certain threshold. As the operating range and the rpm threshold differ from vehicle to vehicle it is configurable within the app along with the time window for the average rpm.
-
Fuel Consumption: The following equations were used to calculate certain parameters:
Air Mass(grams) Fuel(grams) = × AFR
alert the driver, for vehicle is required to servicing or
Where:
(stoich)
not. And also gives a protection of drivers safety. It will gives a parameters are- Engine Coolant Temperature, Calculated Engine load, Engine oil temperature, Fuel pressure, Engine RPM, Vehicle speed, vehicle battery voltage.
SYSTEM CONFIGURATION:
-
is the lambda value computed by the OBD-II Scanner
-
AFR(stoich) is the stoichiometric ratio (14.7)
-
Air Mass in g/s by MAF Sensor
According to Meseguer et al. [9], to calculate the fuel flow, the following equation is used:
Fuel(g) × 360s Fuel Flow = s
Where is the gasolines density and according to AA mo- toring, 770 g/l was chosen as an approach.
To calculate fuel consumption at l/100 km:
Fuel Flow
Fuel consumption 1
(100 km)
=
Vehicle speed
× 100
FIG. 1 SYSTEM CONFIGURATION
Above figure 1 shows a system configuration of applica- tion. LM327 OBD-II scanner is connected to DCL of vehicle. Raspberry pi nano Bluetooth dongle is connected to raspber-
-
-
Fuel Economy: The fuel rate, beside the speed can be used to calculate the fuel economy. for a certain time duration, the average fuel rate and the average speed are calculated, then using these values a average fuel econo- my is calculated by the formula-
Avg. fuel consumption
ry pi and configure a communication to OBD-II scanner
Fuel Economy =
Avg. Speed
through Raspberry Pi. For establishing communication and accessing commands of OBD-II scanner to get values of sen- sors of vehicle a pyOBD python library is used in raspbian operating system. And using HTTP protocol sends data to a cloud server (Thingspeak) through Raspberry Pi 3. Another side an Augmented Reality unity android application is de- veloped. Dashboard is displayed using a thingspeak data and do some analytics for detecting a vehicle fault. Vuforia is used for object tracking. If object is detected then only dash- board will displayed.
-
VEHICLE DIAGNOSIS:
An alert is generated, if avg. of fuel economy is lower than a threshold.
-
-
Vehicle Battery Voltage: Battery voltage will be retrieved from the OBD2 adapter using the AT com- mands AT RV [2]. If this goes below a pre- cise threshold. Then an alert is generated that there is pos- sibility to battery charging failure.
-
Engine Load Monitor: Load is a vital issue for the vehi- cle operation. Once the automotive isn't fast, engine load- ing comes from forces are acting against the motion of the engine. Internal friction (pistons, crankshaft, transmis- sion), external friction (tires on road surface), drag, gravi-
ty (when going uphill). Load means how much power is required from the engine for the car to have some speed and acceleration. When a vehicle is running on the highway, it needs a small percentage of its total available power output to maintain a speed.
Formula of calculation of engine load-
Current Air flow
Engine load are Fuel economy are most important in any vehicle. So if fault is detected anyone of these two parame- ters then Emergency alert is generated. The above figure shows that a pop up message of Emergency alert is generat- ed. This window tells that need to servicing a vehicle.
5. CONCLUSION
Engine load =
Baro 298
Our proposed system is truly based on IoT based augmented
Tamb
Tamb
Max Air flow(Rpm) × 29.92 ×
+ 273
reality application which is suitable for anyone can handle this application and is related to Industry 4.0. In this work we tend to selected and retrieved values for key parame-
-
HARDWARE AND SOFTWARE REQUIREMENT
In this system, OBD-II (ELM327) scanner, Raspberry pi 4, Raspberry pi Bluetooth Nano dongle, this hardware is used. The python3 and C# programming languages are used for developing android AR application; Vuforia model detection application is used for detection of model and integration of OBD-II to raspberry pi 4.
4. RESULT
After connecting an OBD-II scanner to ECU of vehicle, Bluetooth connection is setup to raspberry pi through raspber- ry pi Nano Bluetooth dongle which is connected to raspberry pi. Using python programming in raspberry pi, communication is occurred to OBD-II scanner.
FIG. 2 AUGMENTED REALITY ANDROID APPLICATION DASH- BOARD
In the above figure, a real time dashboard is displayed. Once a mobile application is started Vuforia camera will turn ON in mobile, camera starts searching a target object, when a target object is detected in a mobile camera dashboard are displayed in mobile and application starts diagnosing a vehi- cle doing analytics operations and displayed faults in red color with a fault name i.e. need to service and green color with no need to service equipment. Red and Green color are indicating alerts of vehicle through system.
FIG. 3 AUGMENTED REALITY ANDROID APPLICATION DASH- BOARD WITH EMERGENCY ALERT
ters concerning road vehicle operation. In terms of the equipments and tools used, the work has preceded seam- lessly collateral collaboration of the underlying vehicle plat- form with the OBD-II scanner and software. Using this sys- tem operator will easily understand vehicle maintenance and able to knows about what will be the problem and get some basic understanding of faulty part. And also get information of basic maintenance. Composite parame- ters are calculated, as well as the load and also the fuel con- sumption.
-
Future Scope we can add more parameters like oxy- gen, etc. so that we can also develop voice-controlled wireless technology that connects drivers to numer- ous health-monitoring technologies and services for things like Web-based substance alerts, bronchial asth- ma management tools and polygenic disor- der management. And also do real time faults diagnosis instructions.
-
REFERENCE
-
J V Moniaga, S R Manalu, D A Hadipurnawan and F Sa- hidi,Diagnostic vehicles condition using obd-ii and raspberry pi tech- nology: study literature, 2nd International Conference on Computing and Applied Informatics 2017.
-
Dimitrios Rimpas, Andreas Papadakis, Maria Samarakou,OBD-II sensor diagnostic for monitoring vehicle operation and consumption .
-
Dilum Bandara Sasikala Kottegoda , cloud based driver monitoring and vehicle diagnostic with OBD2 Telematics, International Journal of Handheld Computing Research · August 2015.
-
Adriano Alessandrini, Fernando Ortenzi, Consumption calculation of vehicles using OBD data,2012.
-
M.Jyothi kiran, S.Ravi teja, VEHICLE HEALTH MONITORING SYSTEM. International Journal of Engineering Research and Appli- cations, vol 2, issue 5, 2012.
-
J. Siegel_, R. Bhattacharyya_, A. Deshpande_y, S. Sarma, Vehicular Engine Oil Service Life Characterization Using On-Board Diagnostic (OBD) Sensor Data, ICSENS.2014.
-
R. Rajamani, A. S. Howell, C. Chen, J. K. Hedrick, and M. Tomizuka,
A complete fault diagnostic system for automated vehicles operating in a platoon, IEEE Transactions on Control System Technology, vol. 9, no. 4, pp. 553564, July 2001.
-
W. H. Chung, Fault Detection and Identification with Application to Advanced Vehicle Control Systems. California PATH Research Report UCB-ITS-PRR-96-25, 1996.
-
Meseguer J, Calafate C, Cano J, Manzoni P. Assessing the impact of driving behavior on instantaneous fuel onsumption. In: 12th annual IEEE consumer communications and networking conference (CCNC). Las Vegas, U.S.A; 2015.