
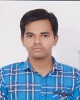
- Open Access
- Authors : Sadige Akhil Prasad , Sai Kiran Maddela
- Paper ID : IJERTV9IS090146
- Volume & Issue : Volume 09, Issue 09 (September 2020)
- Published (First Online): 17-09-2020
- ISSN (Online) : 2278-0181
- Publisher Name : IJERT
- License:
This work is licensed under a Creative Commons Attribution 4.0 International License
Design and Analysis of Chassis of Electric Solar Vehicle
Sadige Akhil Prasad
Mechanical Engineering
Sreenidhi Institute of Science and Technology Hyderabad, India
Sai Kiran Maddela
Mechanical Engineering
Sreenidhi Institute of Science and Technology Hyderabad, India
AbstractChassis act as a framework for supporting various parts of a vehicle. It needs to withstand twist, shock, vibration, and other stresses caused due to acceleration, braking, road condition, and shock initiated by other parts of a vehicle. It should carry a maximum load under all operating conditions. This paper depicts the design and scrutiny of the solar-powered car chassis. The investigation has been carried out, considering three different grades of SAE Steel grades (AISI). By utilizing data of all loads on in all possible direction are considered for designing an excellent chassis. The design and analysis are done using Solidworks and ANSYS
KeywordsSAE steel (AISI); chassis; solar-powered car; ANSYS; SOLIDWORKS
-
INTRODUCTION
A Chassis is an internal component of an automobile that supports all most all parts of an automobile. It is similar to a human skeleton. In recent years the design of chassis is drastically changed. The frame has to withstand shocks, vibrations. The design of the chassis is one of the time- consuming part of designing a vehicle. In todays world, there is great demand and advancements in the field of the automobile industry. The solar-powered vehicle is alternate for fossil fuel-powered vehicles. In todays world, renewable energy sources play a more vital role than ever before. In addition to being clean and inexhaustible, they differ from fossil fuels chiefly in their diversity, potential, and abundance for use anywhere on the planet. With increasing awareness of climate change and environmental pollution, big corporations are investing funds for research in making sustainable energies affordable and feasible. In the last decade, significant technological advancements have been made in the same direction. The world is steering toward a sustainable future.
The preliminary design was made with the view of driver ergonomics. The design was made in SOLID WORKS, and analysis is done with the help of ANSYS 16. Based on the analysis, the modification was done, and the design was finalized.
Functions of Chassis
-
To withstand the stresses acting on the car due to the bad road condition.
-
To carry the load of the goods and passengers in the body of the car.
-
To withstand the forces due to the sudden braking or acceleration by the driver.
-
-
-
SPECIFICATION OF FRAME
Based on the rule book considerations, inputs from other subsystems, and mechanical properties of the materials were considered. Hence, the design was finalized based on these parameters and made in SOLID WORKS. The analysis is done with the help of ANSYS 16. Based on the analysis, the modification was done, and the design was finalized.
The material chosen for the Chassis frame is AISI 4130 of 1inch diameter and 1.6 mm thickness based on its tensile strength, cost, density, weldability, bending strength, bending stiffness and
-
CAD MODELLING
Utilizing SOLIDWORKS software a suitable sustainable chassis model after numerous iteration and corrections.
Specification
Value(inches)
Wheel Base
58
Track Width
44
Height
48
Table 1: specification of chassis
Figure 1: chassis isometric view
Figure 2: Chassis side view
Carbon, C
0.15-0.20
0.28 – 0.33
0.17-0.23
Silicon, Si
–
0.15 0.35
–
Iron, Fe
Balance
Balance
Balance
Molybdenum, Mo
–
0.15 0.25
–
Carbon, C
0.15-0.20
0.28 – 0.33
0.17-0.23
Silicon, Si
–
0.15 0.35
–
Iron, Fe
Balance
Balance
Balance
Molybdenum, Mo
–
0.15 0.25
–
Figure 3: Chassis top view
Table 2: Chemical composition in three grades of AISI Properties of materials:
Material
AISI 4130
AISI 1018
AISI 1020
Yield strength (MPa)
365
350
460
Ultimate tensile strength (MPa)
470
420
560
Density
7.85
7.87
7.85
cost/meter
500
330
310
weight(kg/m)
0.93863
1.15651
0.93863
Table 3: Physical properties of materials
V. CALCULATIONS
-
VOLUMETRIC ANALYSIS:-
Let M/L be the mass per unit length of the cross- section.
Let A be the cross-sectional area, di, do, be the inner and outer diameter of the cross-section, and be the material density.
=
(2 2)
0
0
4
-
For AISI 1018 (1.6mm thickness) =7.85g/cc
= 7.85
(25.42 22.22) = 9.3863 /2
Figure 4: Chassis front view
4
-
For AISI 1020 (2mm thickness) =7.87g/cc
= 7.87
(25.42 22.42)
4
= 11.5651 /2
-
For AISI 4130 (1.6mm thickness)
=7.85 gm/cc
= 7.85
(25.42 22.22) = 9.3863 /2
4
Figure 5: Chassis rear view
-
-
-
MATERIALS
The selection of chassis frame material is made based on tensile strength and also other parameters like cost, density, availability, weldability, bending strength, and bending stiffness. The percentage of carbon is more significant than 0.18%.
-
CALCULATION OF BENDING STRENGTH AND BENDING STIFFNESS
According to the bending moment equation, the Bending strength =()
Bending stiffness- E*I Material calculation: –
-
For AISI 1018 (1.6mm thickness)
365( (25442244)
The following materials are chosen for chassis:
Bending strength=
64
254
( 2 )
-
AISI 1018 circular cross-section;
-
AISI 1020 circular cross-section;
-
AISI 4130 circular cross-section;
-
-
The chemical composition of the three materials is outlined in the following table.
= 244420.71
Bending stiffness
=205 ( (25 44 22 44)) = 1743 N 2
64
-
For AISI 1020 (2mm thickness)
420( (25442144)
Element |
AISI 1018 |
AISI 4130 |
AISI 1020 |
|
Manganese, Mn |
0.60-0.90 |
0.7 – 0.9 |
0.30-0.60 |
|
Sulphur, S |
0.05 (max) |
0.04 (max) |
0.50 |
|
Phosphorous, P |
0.04 (max) |
0.035 (max) |
0.040 |
|
Chromium, Cr |
– |
0.8 – 1.1 |
– |
Element |
AISI 1018 |
AISI 4130 |
AISI 1020 |
Manganese, Mn |
0.60-0.90 |
0.7 – 0.9 |
0.30-0.60 |
Sulphur, S |
0.05 (max) |
0.04 (max) |
0.50 |
Phosphorous, P |
0.04 (max) |
0.035 (max) |
0.040 |
Chromium, Cr |
– |
0.8 – 1.1 |
– |
Bending strength =
64
254
( 2 )
= 335060.9
Bending stiffness
=190 ( (25 44 22 44))
64
= 1925.98 N 2
For AISI 4130 (1.6mm thickness)
460( (254442144)
(
(
254
254
Bending strength= 64
2 )
= 308037
Bending stiffness
=210 ( (25 444 22 244))
64
= 1785 N 2
Table 4: bending strength and bending stiffness of three materials
-
FINITE ELEMENT ANALYSIS (FEM) Meshing has been carried out for several materials in ANSYS software.
COMPONENTS
VALUE
MESH SIZE
4
MESH METHOD
Tetrahedron
NO.OF ELEMENTS
136893
NO. OF NODES
273240
IMPACT FORCE
4G,2.5G
Table 5: Summary of mesh data
A frame of the automobile assumes the most crucial role in the wellbeing of a passenger. The frame contains the operator, motor, brake system, steering mechanism, and suspension system. So, the frame must possess adequate strength to protect the passengers in the event of an impact. Static structural analysis is a FEM technique used to examine the response of real structures to internal and external loads. CAE analysis on the frame is performed to evaluate the safety offered by the chassis to drivers in the event of an accident, including rear impact, side-impact, and frontal impact.
-
FRONTAL IMPACT ANALYSIS:
It is the impact wherein there is a possibility of a vehicle crashing into another vehicle head-on during the race.
-
Assumptions and Considerations taken for the frontal impact analysis are:
-
The mass of the vehicle with drivers is 154.24 kg.
-
Constraints are like the force is applied at the front- most point in a front impact, and wheels are fixed.
-
We consider chassis is in static condition
-
-
Calculation of Impact Forces:
As mentioned, Front-impact force should be 4G. Where G force is the product of mass and gravity.
The total mass of the vehicle including driver =154.24kg F=4G=4×totalmass×gravity F=4×154.24×9.81=6052.38 N
-
-
REAR IMPACT ANALYSIS
-
Assumptions and Considerations taken for the rear impact analysis are:
-
Mass of vehicle with drivers is 154.24kg
-
Constraints are like wheels are fixed, and force is applied back most point in a rear impact.
-
We consider chassis is in static condition for rear impact, considering the worst-case collisions. The force of rear impact is less when compared to the front impact.
-
-
Calculation of Impact Forces:
For the rear impact, the force is 2.5G. F=2.5G = 2.5×Total mass ×gravity F=2.5×154.24×9.81=3782.74N
-
SIDE IMPACT ANALYSIS
The side impact analysis is carried out as there is a chance of collision with another vehicle from either direction.
-
Assumption & considerations:
-
Mass of vehicle with drivers is 154.24kg
-
Constraints are like wheels are fixed, and force is
Material
Bending strength (N- mm)
Bending stiffness (N- mm2)
AISI 1018
244420.71
1743
AISI 1020
335060.9
1925.98
AISI 4130
308037
1785
applied at side most point in a side impact.
-
We consider chassis is in static condition
-
-
Calculation of Impact Forces:
The impact force is given as 4G. F=2.5G=4× total mass × gravity F=2.5×154.24×9.81=3782.74 N
-
-
RESULTS AND DISCUSSION
-
FRONTAL IMPACT ANALYSIS
-
AISI 4130, Circular Cross-section (25.4*22.2*1.6mm)
Figure 6: Factor of safety
Figure 7: Equivalent stress
Figure 8: Total deformation
3. AISI 1020; Circular cross-section (25.4*21.4*2mm)
Total deformation (T.D)
1.7731 mm
Equivalent stress (Eq. Stress)
377.03 MPa
Total deformation (T.D)
1.7731 mm
Equivalent stress (Eq. Stress)
377.03 MPa
Factor of safety (FOS)
RESULTS:
1.5118
Figure 12: Factor of Safety
Table 6: Frontal impact results for AISI 4130
-
AISI 1018; Circular cross section (25.4*22.2*1.6mm)
Figure 9: Factor of safety
Figure 10: Equivalent stress
Figure 11: Total deformation
RESULTS:
Factor of safety
0.98134
Total deformation
1.7731mm
Equivalent stress
377.03MPa
Table 7: Frontal impact results for AISI 1018
Figure 13: Total deformation
Figure 14: Equivalent stress
Results:
Factor of safety
0.76916
Total deformation
1.7731 mm
Equivalent stress
377.03 MPa
Table 8: Frontal impact results for AISI 1020
-
-
REAR IMPACT ANALYSIS
-
AISI 4130; Circular cross-section (25.4*22.2*1.6mm)
Figure 15: Factor of safety
Figure 16: Total deformation
Figure 17: Equivalent stress
Results:
Factor of safety
2.8095
Total deformation
0.32492mm
Equivalent stress
202.88MPa
Table 9: Rear impact results for AISI 4130
-
AISI 1018; Circular cross-section (25.4*22.2*1.6 mm)
Figure 18: Factor of safety Figure 19: Total deformation
Figure 20: Equivalent stress
Results:
Factor of safety
1.8237
Total deformation
0.32492 mm
Equivalent stress
202.88 MPa
Table 9: Rear impact results for AISI 1018
-
AISI 1020; Circular cross-section (25.4*21.4*2mm)
Figure 21: Factor of safety
Figure 22: Total deformation
Fig-22: Equivalent stress
Results:
Factor of safety
1.4294
Total deformation
0.32492mm
Equivalent stress
202.88
Table 10 Rear impact results for AISI 1020
-
-
SIDE IMPACT ANALYSIS
-
AISI 4130; Circular cross-section (25.4*22.2 *1.6 mm)
Figure 23: Factor of safety
Figure 24: Total deformation
Figure 25: Equivalent stress
Results:
Factor of safety
2.7845
Total deformation
0.82876 mm
Equivalent stress
204.71 MPa
Table 11: Side impact results for AISI 4130
-
AISI 1018; Circular cross section (25.4*22.2 *1.6 mm)
Figure 26: Factor of safety
Figure 27: Total Deformation
Figure 28: Equivalent stress
Results:
Factor of safety
2.7845
Total deformation
0.82876 mm
Equivalent stress
204.71 MPa
Table 12: Side impact results for AISI 1018
-
AISI 1020; Circular cross-section (25.4*21.4 *2 mm)
Figure 29: Factor of safety
Figure 30: Total deformation
Figure 31: Equivalent stress
Result:
Factor of safety
2.7845
Total deformation
0.82876 mm
Equivalent stress
204.71 MPa
Table 13: Side impact results for AISI 1020
-
-
CONCLUSIONS
-
Static analysis investigation is done effectively utilizing finite element analysis technique to find the maximum deformations and stresses and its position on the chassis. We had effectively analyzed the chassis strength against the collision from the front, side, as well as from rear directions.
Material
Impact
FOS
T.D
(mm)
Eq. stress (MPa)
AISI 4130
Front
1.5118
1.7731
377.03
Rear
2.8095
0.32492
202.88
Side
2.7845
0.82876
204.71
AISI 1018
Front
0.98134
1.7731
377.03
Rear
1.8237
0.32496
202.88
Side
2.7845
0.828
204.00
AISI 1020
Front
0.76916
1.7731
377.03
Rear
1.4294
0.32492
202.88
Side
2.74845
0.82976
204.71
Table 14: Summary of analysis results
-
The deformation & stresses are under the limit. The factor of safety (FOS) is under the safety limit for all the subsystems
-
Based on the above CAE results and other parameters like cost, weight, and availability, we have decided to go with AISI 4130 upon considering the various factors, including the factor of safety, total deformation, equivalent stress, and also the availability of the materials compared to other metal.
-
The total deformation is least for AISI 4130 is better when compared to other grades.
-
The factor of safety is more for AISI 4130 for given loading conditions.
-
Appreciable ergonomics has been accomplished in the design with a base weight of Solar Vehicle.
-
Reducing weight improves the fuel efficiency of the solar car.
-
-
REFERENCES
-
Rules and Regulation of ISIEs Electric Solar Vehicle Championship 2016.
-
Mohd Azizi Muhammad Nora, Helmi Rashida, Wan Mohd Faizul Wan Mahyuddin, Mohd Azuan Mohd Azlanc, Jamaluddin Mahmud, Stress analysis of a low loader chassis, International Symposium on Robotics and Intelligent Sensors 2012 (IRIS 2012)