
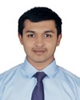
- Open Access
- Authors : Shubham Watharkar , Sandesh Dhavale , Pranav Kochrekar , Rohan Jadhav, Deepali Phadatare
- Paper ID : IJERTV9IS090239
- Volume & Issue : Volume 09, Issue 09 (September 2020)
- Published (First Online): 24-09-2020
- ISSN (Online) : 2278-0181
- Publisher Name : IJERT
- License:
This work is licensed under a Creative Commons Attribution 4.0 International License
Cellular Light Weight Concrete using Glass Fiber
Sandesh Dhavale1, Shubham Watharkar1, Pranav Kochrekar1, Rohan Jadhav1, Deepali Phadatare 2.
Department of Civil Engineering, University of Mumbai.
1 UG Student, Civil engineering, Saraswati College of Engineering, Kharghar, Navi Mumbai
2Assistant Professor, Civil engineering dept, Saraswati College of Engineering, Kharghar, Navi Mumbai.
Abstract- Foamed concrete is a material which basically consist of cement based mortar with minimum (atleast ) 20-25 % of air by volume. It has lower strength than conventional concrete. It is a non loadbearing structure element. Now a days investigation is carried out on the concrete blocks by varying density of foam in quary dust. Constro chem foaming agent is a synthetic foam which is used to vary the density of concrete. The main aim of this project is to decrease the density of concrete by using optimum amount of foam. The results are discussed in detail with respect to test conducted such as compressive strength, split tensile strength and flexural strength with varying quantity of glass fibre and foam. In civil engineering works foamed cement concrete can be used in numerous ways as it has unique characteristics which can be exploited in works. Foamed concrete will flow readily from an outlet to fill restricted and irregular cavities, it requires no compaction and it can be pumped by a significant distance or height. Therefore it can be used as a free flowing and self setting fills. This report provides a detailed summary of foam concrete with respect to constituents, production, engineering properties and use.
Key Words: Foam concrete, Flexural strength, Split tensile strength, Compressive Strength, Compaction, Foam, glass fiber.
-
INTRODUCTION
Lightweight concrete has been used on a large scale in various structural applications and its use in construction grows every year on a global basis. The reason for this is that utilizing lightweight concrete has many advantages. These include: an abbreviation in the dead load of the building, which minimizes the dimensions of structural members; the engenderment of lighter and more minuscule pre-cast elements with inexpensive casting, handling and conveyance operations; the provision of more space due to the minimization in size of the structural members; a truncation in the jeopardy of earthquake damage; and incremented thermal insulation and fire resistance.
In India, construction applications which are being used mostly, masonry structures form the most immensely colossal proportion of the utilizations of conventional burnt clay bricks, hollow concrete block, fly ash bricks, which have many drawback (like cumbersomely hefty weight, non- uniform shape and size, low thermal insulation and fire resistance etc.), that can be amended by utilizing lightweight
concrete. The utilization of lightweight concrete provides improved thermal insulation as well as fire resistance, therefore it is not only effective in fire resistance but also in decreasing U-values ( its the measure in which heat loss is measured through structural elements ) of structures. The main objective is to study the properties of cellular lightweight concrete blocks. Light weight cellular concrete blocks are casted with Fly ash and cement with foam content 50% and glass fiber 1% and 2% of total weight to increase its strength. Foam is replaced by 50% of cementitious material.
-
LITERATURE REVIEW
Tridevi Manoj , et al. (march 2015) has carried out experimental studies on strength of CLC block in comparison with the conventional bricks. Their studies showed that the cellular light weight concrete block can be used as an alternative to conventional bricks to reduce environmental pollution and global warming , the energy consumed in production of CLC block is less compared to conventional bricks and emits no pollution. This study shows that the reduction in self weight of CLC blocks is 32% compared to conventional bricks and increase in compressive strength after
21 days of curing is 36% compared to conventional clay bricks.
Kaushal Kishore ,et.al said (2015)has expressed that Foamed concrete, additionally called cellular light weight concrete is engendered by the mixing of Portland cement, sand including or alone fly ash, water and preformed stable foam. The foam is engendered with the avail of a foam generator by utilizing foaming agent.Remedying of foamed concrete unit may be done as per IS: 456-2000. curing can be accelerated up by steam. Foamed light weight concrete in the form of bricks, blocks or poured in-situ is utilized in may ways such thermal insulation over flat roofs, cold storage walls, non-load bearing walls in RCC/Steel framed buildings, load bearing walls for low-rise buildings.
Kumar ,et.al (2016) has stated that light weight cellular concrete is not a new technology . Its 1st use recorded in 1920s light weight cellular concrete is type of aerated concrete having cellular structure in it which makes it lighter, good thermal and sound insulator material . It is a green product and it requires least energy. It uses the industrial waste products which is good for environment which also causes huge saving of material.
Anik,et.al (December 2016) in his paper explained the successful use of cellular light weight concrete blocks and it has gained popularity due to its lower density and comparative strength than conventional bricks. Also there studies has shown that the use of fly ash in foam concrete can greatly Improve its property.Most of the cleaner production efforts are required in India and hence CLC block can be used as a replacement of burnt clay bricks for construction purposes. Which is advantageous in many terms such as general construction properties, eco-friendlyness.
Raj Vardhan Singh, et al. (2016). This paper states that the cellular light weight concrete is a multifarious material which is composed of cement , flyash and protein based foam. They carried out studies on properties of cellular light weight concrete and also the utilization of quarry dust in the proportion of cellular light weight concrete . they found out that the dry density of CLWC increased and water absorption of CLWC decreases when quarry is partially replaced by fly ash content.
Tharakarama, et.al (2017Nov) released that foam concrete is a versatile material which consists primarily of cement based mortar mixed with atleast 20-25% of volume air. The focus of this project was to decrease the density of concrete by using optimum content of foam. Foam concrete has a unique characteristic that can be exploited in civil engineering works. Based on test results it can be observed that 1200kg/m will be optimum density where upto 40% of density can be reduced compared to conventional concrete
Chandhan et.al (2017) said ,that Foam concrete possess high drying shrinkage due to absence of aggregates i.e. upto 10 times greater than those observed on normal weight concrete .Splitting tensile strength of foam concrete are lower .Use of fly ash helps to acquire desirable strength of light weight concrete that is produced just like normal concrete under ambient conditions . It is produced by slurry of cement plus sand plus fly ash plus water which is further mixed with addition of pre formed stable foam in an ordinary concrete mixer.
-
Kavita,et.al (june 2018) , this paper states that the density of foamed concrete is inversely propotional to the percentage of foam added to the slurry and concrete is a type of porous concrete. The term foam concrete is containing no aggregate only sand, cement, wate and stable foam to perform the concrete. This process comprises tiny enclosed air bubbles within the mortar there by making the concrete lighter. There study has shown that the starting of strength gain for foamed concrete is on higher side than that of normal weight concrete and strength gained beyond 28days is faster than normal weight concrete.
Swapnil Benake,et.al ( July 2019) explained in his study that foam concrete was prepared fully replacing sand by fly ash and particularly replacing cement by silica fume. Because the foaming agent produces a stiff air void, the concrete produces is called foam concrete. From outcome of study it can be noticed that the relation between compressive strength and
flexural strength, and compression strength and split tensile strength is fullfilled by regression analysis.
-
-
MATERIAL USED
-
Cement :
It is always worth seeking to use the best cement in constructions. Therefore, the properties of a cement must be studied. Although depending upon the types of construction various cement properties may differ, Many times a good cement possesses many useful properties.
-
Fly ash:
Fly ash is finely divided residue resulting from the combustion of powdered coal, conveyed by the flue gases and amassed by electrostatic precipitators. Its felicitous disposal has been a cause of concern since long, which causes pollution of air, soil and water. Fly ash can also be referred as either pozzolanic or cementitious. A material which hardens when mixed with water is called as cementitious material.
-
Foaming Agent:
It made to compose light weight concrete and other concrete materials. Foam engender no reaction on concrete but it accommodates as a layer which is air trapped and forms no fumes or toxic. Protein predicated foaming agent requires comparatively more energy to make foam.
-
Water:
water plays a consequential role in the formation of concrete as it participates in chemical reaction with cement. Due to the presence of water the gel is form which avails in increase of strength. Virtually any natural water that is drinkable and has no pronounced taste or odour can be utilized as commixing water.
-
Fine sand:
The grading and maximum size of aggregates is consequential parameters in any concrete commix. They affects proportions in mix, workability, economy, porosity etc. Experiments has shown that very fine sands or very coarse sands are disagreeable as the former is uneconomical, the latter gives astringent unworkable mixes. Thus the object in this paper is to find the best fineness modulus of sand to get the optimum grading of cumulated aggregate (all-in- aggregate), which is most felicitous, and for economy. In general, the grading of aggregates, which do not have a deficiency or excess of any size of aggregate .
6) Glass fiber:
Glass fiber has roughly commensurable mechanical properties to other fibers such as polymers and carbon fiber. Albeit not as rigid as carbon fiber, it is much more frugal and significantly less brittle when utilized in composites. Glass fibers are now a days used as a reinforcing agent for many polymer products to compose a very strong and relatively, lightweight fiber reinforced polymer (FRP) composite, material called glass reinforced plastic (GRP), withal popularly kenned as "fiberglass". This material contains very little or no air (or gas), is denser, and is a much poorer thermal insulator than is glass wool.
-
-
METHODOLOGY
The addition of resin(R) and hardner is as such by replacing 50% of the cementitious material. And glass fiber(G) is added in the variation of 1% and 2% by replacing cementitious material.
By varying the percentages of resins the compressive test, Flexural test, Split tensile test are done and the results are been taken after 28days,
The variation of resins where taken to be 95%, 96%, 97%, 98%, 99%. The three variation in which we achieve greater strength will be tested or carry out study by further adding glass fiber into variation of 1% and 2%.
Fig 1. Flow chart of methodology
-
TESTS AND RESULTS 1.COMPRESSIVE TEST:-
Strength conventionally gives an overall Picture of the quality of concrete because it is directly cognate to the structure of cement-paste. Compression test of the Concrete specimen is mosts used test to quantify its compressive strength.
This concrete is poured in the mould and tampered opportunely so as not to have any voids. After 24 hours these moulds are abstracted and test specimens are put in water for remedying. The upper surface of these specimen should be made smooth. This is done by putting cement paste and spreading smoothly on over all area of specimen.
These specimens are tested by compression testing machine after 7 days remedying or 28 days remedying. The Load of 140 kg/cm2 per minute should be applied gradually till the specimens fails or breaks. Compressive strength of concrete is calculated by dividing the load by area of specimen.
Compressive strength of concrete depends on many factors such as cement strength, quality of concrete material, water cement ratio etc. The average of three cubes are used to determine the compressive strength of each age of test. Compressive strength increase as the percentage of glass fiber increases.
The results of compressive strength using different variations of resins and glass fiber are presented in Table 1.
For finding out the compression strength of foam concrete we casted moulds of 150x150x150 mm. After casting 24 hours removing the mould and allowing for curing in a curing tank for period of 28 days. After 28 days of curing of cube we carried out test on UTM .
According to the results the strength achieved by the trial having 2% glass fiber (R95G2) is 21.16 MPa which is approximately equal to strength of conventional mix i.e 22 MPa. Therefore it can be used as a replacement of conventional concrete bricks with cellular light weight concrete having glass fiber.
Table 1. Test Results of Compressive Strength of Concrete
sr.no |
code |
compressive strength |
||
28d |
||||
load |
MPA |
AVG |
||
1 |
CM |
456 |
20.27 |
22.44 |
490 |
21.78 |
|||
569 |
25.29 |
|||
2 |
R99 |
256 |
11.38 |
12.22 |
305 |
13.56 |
|||
264 |
11.73 |
|||
3 |
R98 |
270 |
12.00 |
12.80 |
315 |
14.00 |
|||
279 |
12.40 |
|||
4 |
R97 |
305 |
13.56 |
13.82 |
333 |
14.80 |
|||
295 |
13.11 |
|||
5 |
R96 |
305 |
13.56 |
15.24 |
357 |
15.87 |
|||
367 |
16.31 |
|||
6 |
R95 |
356 |
15.82 |
16.49 |
405 |
18.00 |
|||
352 |
15.64 |
|||
7 |
R97G1 |
335 |
14.89 |
15.33 |
356 |
15.82 |
|||
344 |
15.29 |
|||
8 |
R97G2 |
395 |
17.56 |
18.84 |
456 |
20.27 |
|||
421 |
18.71 |
|||
9 |
R96G1 |
395 |
17.56 |
17.16 |
425 |
18.89 |
|||
338 |
15.02 |
|||
10 |
R96G2 |
496 |
22.04 |
20.40 |
510 |
22.67 |
|||
371 |
16.49 |
|||
11 |
R95G1 |
426 |
18.93 |
18.71 |
465 |
20.67 |
|||
372 |
16.53 |
|||
12 |
R95G2 |
486 |
21.60 |
21.16 |
524 |
23.29 |
|||
418 |
18.58 |
-
FLEXURAL STRENGTH:
Flexural strength is one of the measure of the tensile strength of concrete. It is a quantification of an unreinforced concrete beam or slab to resist failure in bending. It is quantified by loading 6 x 6-inch (150 x 150-mm) concrete beams with a span length at least three times the depth.
The results of Flexural strength using different variations of resins and glass fiber are presented in Table 2.
For finding out Flexural strength of foam concrete we casted mould 150x150x700 mm. After casting 24 hours removing the mould and allowing for curing in a curing tank for period of 28 days. After 28 days of curing of cube we carried out test on Electro-hyraulic closed loop machine. According to the results the strength achieved by the trial having 2% glass fiber
(R95G2) is 3.53 MPa which is approximately equal to strength of conventional mix i.e 3.84MPa. Therefore it can be used as a replacement of conventional concrete bricks with cellular light weight concrete having glass fiber.
Table 2. Test Results of Flexural Strength of foam Concrete
sr.no
code
FLEXURAL
28d
load
MPA
AVG
1
CM
11
3.42
3.53
12
3.73
11
3.42
2
R99
6
1.87
1.87
6
1.87
6
1.87
3
R98
7
2.18
2.07
7
2.18
6
1.87
4
R97
7
2.18
2.39
8
2.49
8
2.49
5
R96
8
2.49
2.70
9
2.80
9
2.80
6
R95
10
3.11
3.11
11
3.42
9
2.80
7
R97G1
8
2.49
2.49
8
2.49
8
2.49
8
R97G2
9
2.80
3.01
10
3.11
10
3.11
9
R96G1
9
2.80
3.08
10
3.11
10.7
3.33
10
R96G2
11
3.42
3.63
12
3.73
12
3.73
11
R95G1
9
2.80
2.80
9
2.80
9
2.80
12
R95G2
12
3.73
3.84
13
4.04
12
3.73
-
SPLIT TENSILE STRENGTH:
A method of determining the tensile strength of concrete is carried out by casting a cylinder which splits across the vertical diameter. This method of testing split tensile strength is an indirect method. The Split Tensile strength test was carried out according to IS 5816-1999. The results of Split Tensile strength using different variations of resins and glass fiber are presented in Table 3.
For finding out Flexural strength of foam concrete we casted mould 150×300 mm. After casting 24 hours removing the mould and allowing for curing in a curing tank for period of 28 days. After 28 days of curing of cube we carried out test on UTM. According to the results the strength achieved by the trial having 2% glass fiber (R95G2) is 1.88 MPa which is approximately equal to strength of conventional mix i.e 1.77 MPa. Therefore it can be used as a replacement of conventional concrete bricks with cellular light weight concrete having glass fiber.
Table 3. Test Results of Split Tensile Strength of foam Concrete
sr.no |
code |
SPLIT TENSILE TEST |
||
28d |
||||
load |
MPA |
AVG |
||
1 |
CM |
112 |
1.59 |
1.77 |
125 |
1.77 |
|||
138 |
1.95 |
|||
2 |
R99 |
66 |
0.93 |
1.00 |
74 |
1.05 |
|||
72 |
1.02 |
|||
3 |
R98 |
69 |
0.98 |
1.10 |
78 |
1.10 |
|||
86 |
1.22 |
|||
4 |
R97 |
72 |
1.02 |
1.16 |
85 |
1.20 |
|||
89 |
1.26 |
|||
5 |
R96 |
85 |
1.20 |
1.35 |
96 |
1.36 |
|||
105 |
1.49 |
|||
6 |
R95 |
96 |
1.36 |
1.53 |
110 |
1.56 |
|||
118 |
1.67 |
|||
7 |
R97G1 |
93 |
1.32 |
1.46 |
106 |
1.50 |
|||
110 |
1.56 |
|||
8 |
R97G2 |
115 |
1.63 |
1.75 |
126 |
1.78 |
|||
130 |
1.84 |
|||
9 |
R96G1 |
90 |
1.27 |
1.47 |
105 |
1.49 |
|||
117 |
1.66 |
|||
10 |
R96G2 |
105 |
1.49 |
1.82 |
126 |
1.78 |
|||
155 |
2.19 |
|||
11 |
R95G1 |
106 |
1.50 |
1.64 |
115 |
1.63 |
|||
127 |
1.80 |
|||
12 |
R95G2 |
125 |
1.77 |
1.88 |
147 |
2.08 |
|||
126 |
1.78 |
-
CONCLUSION
-
Density is not directly proportional to water absorption. As there is increase in density there is a decrease in water absorption..
-
Foam concrete is more cost efficacious besides eco- amicable.
-
The compressive strength of foamed concrete increases when there is increase in the density.
-
This study has shown that the utilization of fly ash in foam concrete, can be greatly ameliorates its properties.
-
This CLC is even a better alternative t mundane clay bricks for walling masonry.
-
Above all, it is an environment amicable and energy efficient material, which is the desideratum of the day. It is ergo, no surprise that more and more builders are progressively opting for this material in their constructions.
-
It can be concluded that the light weight concrete has the desirable strength and can be used as a industrialized building system.
-
This type of concrete can be utilized in wall panels for precast building.
-
Compressive strength value is compared with the normal value of conventional concrete and the
replacement of coarse aggregate at different percentage(50,60,70).
-
The flexural strength increases with the increase in glass fiber percentage in the mixes without using superplasticizers.
-
-
REFERENCES
-
Manoj, (2015)- An experimental work on cellular light weight concrete, volume-02, issue-03, march-2015.
-
Kishore,et.al(2016)- Foamed cellular Light concrete.
-
Kumar, et.al (2016)- Study of Light Weight Cellular Block in – International Journal for Scientific Research & Development| Vol. 4, Issue 03, 2016.
-
Anik, et.al (2016) Comparative study of performance of light weight concrete in: https://www.researchgate.com.
-
Vardhan, et.al (2016)- Study of Cellular Light Weight Concrete in IJSRD – International Journal for Scientific Research & Development| Vol. 4, Issue 07, 2016.
-
Tharakarama, et.al (2017)- An experimental investigation on light weight foam cement blocks with quarry dust replacement for fine aggregate in International Research Journal of Engineering and Technology (IRJET), Volume: 04 Issue: 11 | Nov -2017.
-
Chandan, et.al (2017)- Cellular lightweight concrete by UG, students, department of civil engineering, IIMT College, Greater Noida.
-
Kavitha,et.al (2018) – Design and Analysis of Foam Concrete in International Journal of Engineering Trends and Applications (IJETA) Volume 5 Issue 3, May-Jun 2018.
-
Beneke, et.al (2018) – Use of high strength cement in hybrid fibre foam concrete with fly ash and silica fume in International Research Journal of Engineering and Technology (IRJET) Volume: 05 Issue: 07 | July 2018.