
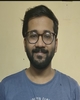
- Open Access
- Authors : Arunaditya P Singh , Dhruvin D Shah
- Paper ID : IJERTV9IS090464
- Volume & Issue : Volume 09, Issue 09 (September 2020)
- Published (First Online): 30-09-2020
- ISSN (Online) : 2278-0181
- Publisher Name : IJERT
- License:
This work is licensed under a Creative Commons Attribution 4.0 International License
Experimental Study on Geopolymer Concrete with PET Fiber
Arunaditya P Singh, Dhruvin D Shah
B.E. Civil Engineer, Babaria Institute of Technology, Vadodara, Gujarat, India.
Abstract – Concrete is the world's most durable, versatile and dependable construction material. After water, concrete is the most used material which required large quantities of Portland Cement. Ordinary Portland Cement production ranks second in generation of carbon dioxide, which pollutes the atmosphere. Geopolymer concrete is an ecofriendly and innovative construction material which is a possible alternative to Portland cement concrete. Increase in use of geopolymer will eventually reduce the demand of Portland cement. Geopolymer concrete consists of basic waste material such as fly ash, GGBS and alkaline activators. Geopolymer concrete with PET fibers offers better compressive strength, tensile strength and resistance against acid attack. In this study fly-ash and GGBS (50% each) are used in equal proportion. PET fiber (0.25 & 0.5% of weight of cube) is used mainly for two reasons one is that, it provides great flexibility which reduces the causes of crack. Another is, plastic bottle which is a main source of PET fiber are being disposed in huge quantity, in oceans and land. This affects the aquatic life and creates imbalance in ecosystem. Geopolymer concrete with PET fiber are cured in ambient conditions. Cubes are then tested for compression and split tensile tests.
Key Words: Geopolymer concrete, fly-ash, Ground-Granulated Blast-Furnace Slag (GGBS), alkaline solution (Sodium hydroxide, Sodium silicate), PET fiber (polyethylene tera phthalate fiber)
1.INTRODUCTION
-
GEO-POLYMER CONCRETE
Geopolymer was invented by Joseph Daidovits in 1978. Conventional concretes similar ingredients are used in Geopolymer concrete except that the cement is fully replaced by by-products of industries such as GGBS and flue ash. Geopolymer concrete is a more environmentally sustainable product as it uses Fly ash and GGBS which helps in reducing carbon emissions by some 40 % to 80 % without affecting the structural properties of conventional concrete. Instead of the conventional hydration reaction the chemical reaction in geopolymer concrete is promoted by a concentrated solution of alkali-based chemicals such as sodium hydroxide and sodium silicate. Two types of curing are used on geopolymer concrete namely ambient curing and oven curing. Several innovators have already studied geopolymer concrete and concluded that geopolymer concrete provides a significant advantage in high early and later age strength and better resistance to acid attack. Innovators consider geopolymer concrete as a practical alternative to Portland cement. It is a more environmentally friendly alternative to conventionally Portland cement. It has been discovered to be used in many Hindu temples. Some of which are more than a thousand-year- old.
Geopolymer concrete categories
-
Slag based geopolymer concrete
-
Rock based geopolymer concrete
-
Fly ash based geopolymer concrete
-
Type 1: Fly ash geopolymer concrete activated by alkaline.
-
Type 2: slag/fly ash based geopolymer concrete.
-
-
Ferro sialate based geopolymer concrete.
-
-
COMPOSITION OF GEO-POLYMER CONCRETE
-
Fly ash
Power plants fuelled by coal produce a material which is comprised of the non-combustible mineral portion of coal. This by-product is fast becoming a vital ingredient for improving the performance of a wide range of concrete products. That material is fly ash.
-
Ground-granulated blast-furnace slag (GGBS)
Ground-granulated blast-furnace slag is acquired by quenching molten iron slag. A glassy substance as a by- product is produce, then it is dried and gr into a fine powder. GGBS is a hydraulic binder, which has been found to be used for more than 150 years.
-
Fine aggregate and coarse aggregate
Fine aggregate is the particle which passes from 4.75 mm sieve and retains on 75 microns whereas Coarse aggregate is particle which passes from 20mm and retain on 4.75mm
-
Sodium Hydroxide and Sodium Silicate
Sodium silicate is a colorless liquid which can be found in three different forms i.e. neutral acidic and basic Sodium hydroxide is a highly mordant base and alkali that deteriorate proteins at ordinary ambient condition and may cause serious chemical burns.
-
Polyethylene Terephthalate Fiber (PET)
Poly Ethylene Terephthalate commonly abbreviated PET. PET fiber is one of the most prominent fiber used in production of plastic. Most of PET is used in manufacturing of plastic bottles, beverage containers, food and other packaging. Most of PET bottles thrown away after single usage and disposed by authorities. This PET bottles are treated by landfill and burning, which creates serious environmental problems. It is one of the major environmental, economic and social issues. PET bottles in fiber form can be used to get better the mechanical properties of geopolymer concrete. The compressive strength, tensile strength and flexural strength behavior of geopolymer concrete can be improved. The PET fibers addition in geopolymer
concrete is an innovative material that can be promoted in construction field. In 2017 estimated production of 38 million tons of waste PET was found in world. As per the estimates India produces around 5 million tons of PET waste every year. It has increased at the much fast rate which resulted in the accumulation of the enormous quantities of the non-biodegradable waste, which have to dispose using landfill or burning.
-
(ii)
Fig -1: PET fiber
-
-
-
MATERIALS USED IN EXPERIMENT
The fly ash a11nd GGBS was obtained from Conash infrastructure. The specific gravity of fly ash was calculated as 2.1 g/cc while the fineness was 350 m2/kg and the specific gravity of GGBS was calculated as 2.89 g/cc whereas the fineness was 450 m2/kg. Sodium silicate was used in neutral grade was obtained from Shree Saibaba Chemical Industries, Ankleshwar. Sodium Hydroxide was obtained from Ghanshyam trading company, Vadodara. For PET Fiber, plastic bottles were obtained from local scrap dealer. Then Plastic bottles were manually shaded in aspect ratio of AR-
22.5. Coarse aggregate is obtained from local dealer. Coarse aggregate was passing from 20mm, and retaining from 4.35 mm. Fine aggregate is obtained from local dealer. fine aggregate was passing from 4.35mm, and retaining from 75
After the molds were fitted and lubricated. The geopolymer concrete was poured in three equal layers by compacting them with equal number of blows. Then the mold filled with concrete are placed on vibration machine for 5-10 min for further compaction & removal of air void. Then after the cubes & cylinders were set, they were unmolded and kept in direct sunlight for ambient curing for 24 hrs.
Fig -2: GEOPOLYMER CUBES
3. TEST PERFORMED
-
COMPRESSION TEST
Compression strength is one of the most important property of concrete. It is used for basic calculation and analysis. 21 no of Geopolymer cubes of different proportion of size 150x150x150mm were casted. than they were allowed to rest in sunlight for 24 hr (ambient curing). The test was conducted for 3 cubes each after 7 and 28 days. In this test cubes are placed in the compression machine and load applied was 140 kg/cm2/min as per IS-516. Failure loads were noted. Average of three cubes were considered.
<>Compression Strength (7 Days)
46
44
42
40
38
36
micron.
-
MATERIAL PROPOERTION RATIO AND MIXING
GPC GPC with PET (0.5%)
GPC with PET (0.25%)
PROCEDURE
Material
Proportion
Fly ash
1
NaOH + Na2SiO3
0.3
Sand
1.68
Aggregate
3.12
Total Water
0.27
Extra Water
0.05
Material
Proportion
Fly ash
1
NaOH + Na2SiO3
0.3
Sand
1.68
Aggregate
3.12
Total Water
0.27
Extra Water
0.05
Table -1: material proportion for each structure
Cube 1 Cube2 Cube3
Chart -1: COMPRESSION STRENGTH TEST (7 DAYS)
First, we measured the required quantity of fly ash, G.G.B.S, and PET fiber (0.25% of weight of concrete cube). then we measured quantity of sodium silicate in a beaker. Then in another beaker we mixed sodium hydroxide pallets with water. First spread out the measured quantity of sand uniformly on the mixing platform. Then the measured quantity of aggregate was Dumped on the sand and distributed uniformly. Then sand and aggregate were mixed with the shovels, uniformly. Spread out the fly ash, GGBS & PET Fibers on the mixing platform over the mixture of sand and aggregate. Measured quantity of Sodium hydroxide was mixed with water in a glass beaker. Sodium silicate was taken in measured quantity. First, we added the water to the dry mix then we add sodium hydroxide and sodium silicate evenly.
Compression Strength (28 Days)
50
48
46
44
42
40
38
36
GPC GPC with PET (0.25%)
Cube 1 Cube2 Cube3
Chart -2: COMPRESSION STRENGTH TEST (28 DAYS)
Split Tensile Strength (28 Days)
Split Tensile Strength (28 Days)
12
10
8
6
4
2
0
12
10
8
6
4
2
0
GPC with PET (0.25)
GPC with PET (0.25)
(i)
Fig -3: COMPRESSION STRENGTH TESTING MACHINE
-
-
SPLIT-TENSILE TEST
Split tensile strength is another one of the most important properties of concrete. It is used for basic calculation and analysis. 12 no of Geopolymer cylinders of different proportion of size 150mm dia x 300mm length were casted. than they were allowed to rest in sunlight for 24 hr (ambient curing). The test was conducted for 3 cylinders each after 7 and 28 days. In this test cylinders are placed horizontally in the compression machine. Failure loads were noted. Average of three cubes were considered.
Split Tensile Strength (7 Days)
8
7
6
5
4
3
2
1
0
GPC GPC with PET (0.25%)
Cylinder 1 Cylinder 2 Cylinder 3
Chart -3: SPLIT-TENSILE STRENGTH TEST (7 DAYS)
Cylinder 2
Cylinder 3
Cylinder 2
Cylinder 3
GPC
Cylinder 1
GPC
Cylinder 1
Chart -4: SPLIT-TENSILE STRENGTH TEST (28 DAYS)
-
CONCLUSIONS
-
In the manufacturing process of Ordinary Portland Cement, almost 92.7% CO2 of total weight is produced. It is very harmful for environment and causes global warming.
-
To reduce CO2 emission, we used geopolymer concrete which mainly consist Fly Ash and GGBS which are replacement of cement.
-
The chemical reaction is promoted by a concentrated solution of alkali-based chemicals such as sodium hydroxide and sodium silicate instead of the conventional hydration reaction.
-
for further increase in strength of geopolymer concrete we added PET Fiber in geopolymer concrete.
-
We decided to add 0.25% & 0.5% of PET Fiber of total weight and compared it with normal geopolymer concrete.
-
We obtained PET fibers from the waste bottles from the local scrap dealer.
-
We casted 9 normal geopolymer concrete cube, 3 geopolymer cubes with PET Fiber of 0.5% of total weight. 6 geopolymer cubes with PET Fiber of 0.25% of total weight for compression test.
-
We casted 6 normal geopolymer concrete cylinder and 6 geopolymer cylinder with PET Fiber of 0.25% of total weight for split tensile test.
-
The compression strength of geopolymer concrete with 0.5% PET fiber increased by 7.3% after 7 days
-
The compression strength of geopolymer concrete with 0.25% PET fiber increased by 9.03% after 7 days
-
The compression strength of geopolymer concrete with 0.25% PET fiber increased by 12.7% after 28 days
-
The split tensile strength of geopolymer concrete with 0.25% PET fiber increased by 6.08% after 7 days
-
The split tensile strength of geopolymer concrete with 0.25% PET fiber increased by 9.56% after 28 days
-
In this experimental study we found that addition of pet fiber in geopolymer concrete acts as a crack arrester for the concrete during the loading. It helps to delay the propagation of crack.
-
In this experimental study we found that usage of PET Fiber in geopolymer concrete has been proved to be
advantageous. It can be used for construction of pavement retaining wall water tank precast bridge decks.
-
-
REFERENCES
-
Davidovits J (1995) Global warming impact on the cement and aggregate industries. WorldRes Rev 6(2):263278
-
Hardjito D, Wallah SE, Sumjouw DMJ, Rangan BV (2004) On the development of y ashbased geopolymer concrete. ACI Mater J 101:467472
-
Mullick AK (2005) Use of y ash in structural concrete: part I why? Indian Conc J 79:1322
-
Kumar V, Mathur M, Sinha SS, Dhatrak S (2005) Fly Ash: an environmental savior. Fly AshUtilisation Programme (FAUP), TIFAC, DST, Fly Ash India, New Delhi, IV, pp 1.11.4
BIOGRAPHIES
-
Arunaditya P Singh
B.E. Civil Engineer
Babaria Institute of Technology 170053106041
-
Dhruvin D Shah
B.E. Civil Engineer
Babaria Institute of Technology 170053106041