
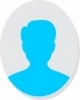
- Open Access
- Authors : Dharm Pal , Rajesh Nimmakayala
- Paper ID : IJERTV9IS090488
- Volume & Issue : Volume 09, Issue 09 (September 2020)
- Published (First Online): 07-10-2020
- ISSN (Online) : 2278-0181
- Publisher Name : IJERT
- License:
This work is licensed under a Creative Commons Attribution 4.0 International License
Influence of Shapes of Interfacial Area on Rate of Liquid-Liquid Extraction Reactions
Nimmakayala Rajesh, Dharm Pal* Department of Chemical Engineering, National Institute of Technology Raipur
Abstract: -Carboxylic acids serve as feedstock for various useful chemicals and have potential applications in various fields in our day to day life. Existing conventional production technologies are not eco-friendly as they generates huge amount of hazardous solid waste. Fermentation process is a promising alternative route, although recovery of biotechnologically produced carboxylic acids from fermentation broth is challenging bottleneck. Out of available methods to separate carboxylic acids from the fermented media reactive extraction (liquid-liquid extraction) is found to be technologically and economically viable. In this work, effect of stirring speed on available surface area of interfacial geometrical shape for liquid-liquid reactions is studied. Since, interfacial area between the phases will influence the design of a reactor, so it must be accounted for. Based on the stirring speed four pace zones were classified (slow, medium, fast and very fast) in the Lewis stirred cell. Each zone causes a different geometrical shape and theoretically correlated with rate of reaction (by complex formation) with surface area available for the specific geometrical shape.
Keywords:- Hatta number, Interfacial surface area, reactive extraction, liquid-liquid reactions, reactor design
INTRODUCTION
In our daily life we encountered variety of chemicals which are derived mostly from chemical and petrochemical routes14. Carboxylic acids (CAs) are one of those valuable chemicals which is basically an organic acids. Due to wide spectrum of applications of CAs in various fields5, demand is growing day by day. Moreover, feedstocks or raw materials used in these routes are mostly non-renewable resources which is depleting with alarming rate. Besides, these chemical and petrochemical routes are energy intensive and hazardous. Alternative for these environmental unfriendly chemical processes for the commercial production is fermentation technology10,9. Owing to the advancements in recombinant technology, we can produce almost every carboxylic acid through bio-route. However, recovery of carboxylic acids from fermentation broth is incredibly challenging8. There are different methods being used to recover carboxylic acids from fermentation broth; conventionally salt precipitation method is in practice. Recently, chromatographic methods (ion exchange and adsorption), distillation, extraction, and membrane separations, and so forth, had been reported for separation of carboxylic acids from the fermenter9, 3 &13. Some of these methods are energy intensive, few are still at R&D stage and mostly uneconomical. Among all these recovery technologies, extraction (reactive extraction) is reported a promising and viable method7. Reactive extraction is often carried out in two steps, firstly forward extraction and then second step is backward extraction3,13. There are two main studies required to understand the maximum degree of separation and separation rate; Equilibrium studies and Kinetic Studies.
In equilibrium studies, we study how much extraction efficiency is achieved by the selected diluents and extractant system along with the effect of operating parameters (like initial acid concentration, extractant concentration, temperature, pH etc.). In kinetics studies, we investigate how the chemical reaction (between carboxylic acid and extractant in the diluents phase (
)) depend on the mass transfer between phases. L.K. Doraiswamy and M.M. Sharma4 proposed a mechanism for finding the reaction regime (classified reactions in 4 types as regime 1,2,3 & 4) based on mass transfer theories and other hydrodynamic parameters. Hatta6 proposed a dimensionless number Hatta number whether the reaction occurring between the liquid-gas or liquid-liquid phase is slow or fast. Based on hatta number, Data et. al2 have classified the limiting criteria; proposed for the identification of reaction regime into two zones as shown in Table 1. If Hatta number is greater than one (Ha>>1) the reaction is fast and takes place in film and the surface area is controlling factor and it fall under regime 3 or 4.If the value of Hatta number is less than one (Ha<<1) the reaction is slow and not takes place in film and bulk phase is controlling factor and the reaction falls under regime 1 or 2. For identifying specific reaction regime, the classification was further modified based on other attributes (like initial acid concentration, initial extractant concentration, stirring speed and phase volume ratio) dependency on rate of reaction. Among all the attributes, we have focused our study on stirring speed because there is a variation of geometrical shape (available surface area for contact between ( & )) with respective to stirring speed. As such the interfacial area between the phases will influence the design of a reactor.
In this work four pace zones (slow, medium, fast and very fast) was proposed based on stirring speed in the Lewis stirred type cell. Each pace zones resulted a specific geometrical shape. Based on the geometrical shape, available contacting surface areas between ( & ) are theoretically correlated with the rate of reaction.
THEORY
Separation of carboxylic acid (HA)from aqueous phase( ) to organic phase( )is achieved by complexation between acid and extractant in the organic phase. The discussion case is for Hatta number (Ha 1) and the complex formation reaction takes place at the film interface as shown in Figure 1. Also, it is assumed that the reaction is irreversible and it is
occurring in organic phase ( )-film interface. The rate of reaction for liquid-liquid reactions (heterogeneous reactions) based on interfacial surface area is shown in Figure 1and may be represented by Eq(1)11.
[HA.E] [E]-phase
S
-phase
[HA]Figure 1 complex formation at the interface of aqueous and organic phase for Ha 1.
Table 1 Table for discerning the reaction regime based on various attributes.
S.no |
Regime |
Hatta number |
Reaction |
Controlling factor |
Geometrical shape |
Phase volume ratio (: ) |
1 |
1 (Very slow) |
Ha<<1 |
Not at film interface |
Bulk phase |
No affect |
Affect |
2 |
2 (Slow) |
No affect |
||||
3 |
3 (Fast) |
Ha>>1 |
at film interface |
Surface area |
Affect |
|
4 |
4 (Instantaneous) |
1 =
(1)
[]So, the rate of disapperance ( ) of carboxylic acid (HA) on surface of the film interface (S) is
=
(2)
[]Based on stirring speed four pace zones (slow, medium, fast and very fast) was classified in the Lewis type cell as shown in Figure 2. In each zone there is a formation of a different geometrical interfacial surface area in the container. These geometrical shapes (available surface area fo contact between ( & ) were classified as:
-
Circle (cross-sectional)
-
Parabola/forced vortex (surface)
-
Gabriels horn / free vortex (surface)
-
Cylinder (surface)
Based on concept of surfaces of revolution12, surface area of the geometrical shapes was proposed except for circle. The surface area of shape was represented as deduced by equation (3) for abscissa (X-axis) and equation (4) for ordinate (Y-axis) and given in Table 2.
2 (3)
2 (3)
= 2 (1 + () )
2 (4)
2 (4)
= 2 (1 + ( ) )
RESULTS & DISCUSSION
While studying effect of stirring speed on rate of reaction for determining reaction regime; change in the geometrical shape of the interface between the & phases were observed. The observed geometrical shapes are catagorized in four pace zones with respect to the stirring speed as shown in Table 1. Complex formation between carboxylic acid (HA) and extractant (E) takes
place at the surface (area) available for contact between ( & ). Therefore, the rate of disapperance of carboxylic acid (HA) on different geometrical surface of the film interfaces (S) in the organic phase ( )could be given as follows:
-
Based on circular crossectional surface area
[ ]=
(5)
[] -
Based on parabolic surface area
[ ]=
(6)
[] -
Based on Gabriels horn (vortex ) surface area
[ ]=
(7)
[] -
Based on cylindrical surface area
=
(8)
[]Interfacial surface area of the geometrical shapes follows the order < < < . Accordingly the order of rate of disapperance of carboxylic acid (HA) with respective to the avilable interfacial surface area is as follows:
[ ]< [ ]
< [ ]
< [ ]
(9)
2
2
The cross sectional surface area of a circle is always lesser than the surface area of a parabola with the same radius. Also, surface area of a cylinder is always greater than the vortex or Gabriels horn shape when the dimension of length (depth) and radius are same. But surface area of parabola is greater than surface area of vortex when dimensions are same (i.e. radius and depth). It will never be the case, because surface area of a parabola is proportional to the depth of the parabola. The depth of the parabola increases with increasing stirring speed as shown in Figure 3.The relation between stirring speed and the geometrical
shape is given by Eq (10)1. The general relation between depth of the parabola ( ) and the parabola function ( ) where ( ) is
depth factor is given by Eq(11) and as shown in Figure 3(a). Figure 3(a) shows parabola with different depths (i. e. i =
, , & ) and the relevant depth factors are shown in Figure 3(b).The depth of the parabola is inversely proportional to depth factor Eq(12). Therefore, the low value of depth factor having large depth and more surface area avilable as given in Eq(14). It will never reach case IV as shown in Figure 3(b) instead it may turns into vortex at the stirring speed where (=1) and the geometrical shape with stirring speed is given by Eq(15)1. At very high speeds the interfacial area between phases turn into cylindrical.
2 2
2 2
=
(10)
2
pressure at the free surface
pressure at the depth ()
gravitational constant
density of the fluid
speed of rotation
radius of the geometrical shape
= =
2
2
(11)
1
(12)
< < (13)
< < (14)
2
2
= ( )
(15)
2 1 2
22
angular mmentum
(1 2) depth of the vortex
CONCLUSION
Separation of biotechnologically produced carboxylic acids (from fermenter) using reactive extraction involves the complex formation reaction between acid and extractant. In this work, the rate of reaction (liquid-liquid extraction) was theoretically correlated with interfacial area between the aqueous and organic phases and its variations with stirring speed. Based on ranges of stirring speed, four pace zones (slow, medium, fast and very fast) were classified in the Lewis type cell. Interfacial surface area of different geometrical shapes follow the order of < < < . Therefore, Hatta number (Ha1) rate of reaction is increasing with increasing stirrring speed by interfacial area which increase mass transfer coefficient.
REFERENCE
-
Backhurst, J.M; Harker, J.H.. Coulson and Richardsons Chemical Engineering:: Fluid Flow: Fundamentals and Applications.vol-1(6th ed.) (2004).
-
Datta, D.; Kumar, S. Equilibrium and Kinetic Studies of the Reactive Extraction of Nicotinic Acid with Tri-n-octylamine Dissolved in MIBK. Ind. Eng. Chem. Res. 52(41), 468014686 (2013).
-
Datta, D.; Kumar, S.;, Uslu, H. Status of the Reactive Extraction as a Method of Separation. Journal of Chemistry. 2015, 1-16 ( 2014).
-
Doraiswamy, L. K.; Sharma, M. M. Heterogeneous Reactions: Analysis, Examples, and Reactor Design; John Wiley & Sons: New York (1984).
-
Galindo, A. S.; Lluvia, I. L.L; Fabiola, N. C. D.; Adali, O. C. F.; Leticia A. R. M.; Karla C. C. C.; Denisse, L. C. Applications of Carboxylic Acids in Organic Synthesis, Nanotechnology and Polymers. (2018).
-
Hanna, G. J.; Noble, R. D. Measurement of LiquidLiquid Interfacial Kinetics. Chem. Rev. 85, 583 (1985).
-
Jarvinen, M., Myllykoski, L., Keiski, R., & Sohlo, J. Separation of lactic acid from fermented broth by reactive extraction. Bioseparations, 163166 (2000).
-
Kertest, A. S; King, C. J. Extraction Chemistry of Fermentation Product Carboxylic Acids. Biotechnol. Bioeng. XXVIII, 269282 (1986).
-
López-Garzón, C.S.; Straathof, A.J.J. Recovery of carboxylic acids produced by fermentation, Biotechnol Adv. (2014).
-
Nimmakayala, R; Pal.D. Effect of Diluents on Extraction Equilibrium of trans -Aconitic Acid. J. Chem. Eng. Data, 64, 2985 2996 (2019).
-
Octave, L. Chemical Reaction Engineering (3rd ed.). John Wiley & Sons (1999).
-
Swokowski, Earl W. Calculus with analytic geometry (1983).
-
Wasewar, Kailas L. Reactive extraction: an intensifying approach for carboxylic acid separation. Int. J. Chem. Eng. Appl. 3.4 249 (2012).
-
Yang, S.-T., Huang, H., Tay, A., Qin, W., De Guzman, L., & Nicolas, E. C. S. Extractive Fermentation for the Production of Carboxylic Acids. Bioprocessing for Value-Added Products from Renewable Resources, 421446 (2007).
-phase |
-phase |
-phase |
-phase |
Slow (a)
Medium (b)
x1
x1
-phase -phase
-phase
-phase
x2
x2
Fast (c)
Very fast (d)
parabola shape
parabola shape
Figure 2Effect of stirring speed on geometrical shape of interfacil surface area (a), circular; (b), parabola/ forced vortex; (c), free vortex; (d), cylindrical
d1 I d2 II d3 III (a) |
25 20 15 IV 20 factor 10 10 factor 5 factor 5 1 factor 0 -5 -3 -1 1 3 5 Diameter of the cell (b) |
|
Figure 3Transition of parabolic surface area with increasing speed (a), depth variation ;(b),depth variation with respect to vessel diameter; |
Pace zone Geometrical shape Surface area formula
Y-axis
Circle:
=
Slow
r
r-axis
[0, 2] [0, ]= 2
2
2
x=f(x)=
Y-axis
Parabola:
2
=
2 2 2
= 2 (1 + ( ) )
1
Medium
X-axis y1
2
= 1 + 4 ( )
8
=
2
y2
2
= 8
=
6
1
[(1 + 4 (2 32
) )
1
1
2
]
]
1
Y-axis
Vortex:
=
1
= 2
a
a
y=f(x)=1/x
y
y
= 2 (1 + (
1
1
2
2
)2)
X-axis
= 2
4 + 1
3
Fast
2
4 + 1
1
2
4
1 3
1
4
3
x1 =1 x2
2
1 3
= 2
1
1
1
1
= 2 [log()]
Very fast |
Y-axis x=r X-axis y2 y1 |
Cylinder: = (constant) = 0 2 = 2 (1 + (0)2) 1 = 2 (2 1) = 2 1 = 2 |