
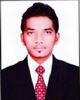
- Open Access
- Authors : Kiran Tukaram Shembade , Pradnya Pravin Hedgire , Sejal Vishwanath Chavan
- Paper ID : IJERTV9IS120046
- Volume & Issue : Volume 09, Issue 12 (December 2020)
- Published (First Online): 11-12-2020
- ISSN (Online) : 2278-0181
- Publisher Name : IJERT
- License:
This work is licensed under a Creative Commons Attribution 4.0 International License
Experimental Study on Effect of Internal Curing on Compressive Strength of Concrete using Super Absorbent Polymer
Mr. Kiran Tukaram Shembade
Lecturer (Civil Engineering Department)
A.G. Patil Polytechnic Institute, Solapur
Ms. Pradnya Pravin Hedgire
Student (Civil Engineering Department)
A.G. Patil Polytechnic Institute, Solapur
Ms. Sejal Vishwanath Chavan
Student (Civil Engineering Department)
A.G. Patil Polytechnic Institute, Solapur
Abstract:- Conventional concrete may experience a considerable amount of autogenously shrinkage leading to early age cracks and these cracks severely reduce durability
-
General
CHPATER1 INTRODUCTION
of concrete. There can be reduction in the development of cracks with the help of internal curing agents. Internal curing has proved to be an effective technique for reducing the early age shrinkage by releasing the water absorbed and maximizing the hydration process. American Concrete Institute defines internal curing (IC) as a process by which the hydration of cement continues because of the availability of internal water that is not part of the mixing water. The introduction of SAP (Super Absorbent Polymer) as a new additive for the production of concrete materials presents a number of new possibilities in respect of purposeful water absorption and water release in either fresh or hardened concrete. Proper curing of concrete structures is important to ensure they meet their intended performance and durability requirements. Internal curing is a very promising technique that can provide additional moisture in concrete for a more effective hydration of the cement and reduced self-desiccation. Internal curing implies the introduction of a curing agent into concrete that will provide this extra moisture. The super absorbent polymer absorbs large amount of water which will be in the gel and same time increases volume proportionally. These properties are found to be very useful and effective in concrete. Use of super absorbent polymer in concrete has proven many positive effects on properties of concrete. In the current study M25 grade concrete was used to cast cubes to investigate compressive strength of hardened concrete. According to mix design the proportions taken were 1:2.08:3.44. Fine aggregates were replaced with pre-soaked light weight aggregates. Cement was replaced with super absorbent polymer by 0.2%, 0.35% and 0.5%. The results of compressive strength after 28 days of pond curing indicated an increase in the strength about 14% to 29%. The optimum results were obtained with 0.35%SuperAbsorbent Polymer.
Concrete is a kind of porous, multiphase at all scales, and heterogeneous complex system. The degree of hydration of cement plays a decisive role in the strength and compactness of concrete. Optimizing the pore structure, reducing porosity and reducing macro pores are the necessary improvement measures for high strength and high durability concrete. The research on hydration mechanism of cement showed that the inner structure of concrete had fine pore size and compact structure when the water binder ratio was relatively low. However, there will be more UN hydrated cement and mineral admixture particles, which will result in the decrease of internal relative humidity and the increase of the autogenously shrinkage of concrete. Water curing is a very important technical measure for concrete in order to ensure the hydration process of cementitious materials in concrete. Effective water curing measures should ensure the enough moisture environments inside and outside the concrete which are necessary for hydration. If the moisture is not enough, it will cause early shrinkage and even the cracking of concrete, which will adversely affect the growth of strength and durability of concrete at later age. In practical engineering, manual operation and external curing are usually adopted, which is very difficult to produce timely and adequate curing.
The internal curing method has been studied for some years which may be an effective way to ensure the hydration process in concrete. Water is introduced into the concrete in advance by absorbent material like superabsorbent polymer (SAP), so that some of the water acts as internal curing water from the inside out, in order to achieve the effect of internal curing in the hydration process of the cementitious material. When the relative humidity inside the cement matrix gradually drops, the absorbent material can slowly release water to supplement the water consumption of cement hydration. The hydration process continued to generate hydration products to fill the pores of cement paste,
reduce the micro cracks in cement matrix, and relieve the autogenous shrinkage and drying shrinkage. Then the strength and durability of the concrete can be improved.
In the last few decades great advance in concrete technology have arisen to a large extent out of development and use of new chemical additives which although mix with concrete in very small quantity can dramatically increase crucial properties of concrete in fresh and harden state. One prominent example uses the plasticizers are used with the other appropriate ingredient. They unable the developments of new type of concrete like self-compacting concrete or ultra-high-performance concrete. The introduction to super absorbent polymer as a new component for the production of concrete materials these makes available number of new possibilities with respect to water control & result the control over the rheological properties of fresh in addition water absorption and water release in either fresh or harden concrete. Well control and take release of water can be fostered by the specific design of SAP material to particular practical need. Its exchange with the surroundings roots hardened concrete to shrink, swell and probably crack. Its presence in hardened concrete influences strength and creep and it plays a central role in deterioration due to the frost action or alkali silica reactions. When concrete is removed from water the moisture evaporates from the concrete surface due to this crack are form are known as shrinkage crack. The autogenously deformation of concrete is defined as the unrestrained, bulk deformation that occurs when concrete is kept sealed and a constant temperature. When the autogenous deformation is a contraction, it may be referred as autogenous shrinkage. Obviously, control of water is important to concrete by the use of super absorbent polymers (SAPs) for achieving that control. SAPs are polymeric materials that have the ability to absorb a large amount of liquid from the surroundings and retain it within its structure.
-
Super Absorbent Polymer
Super absorbent polymers (SAP) also known as slush powder are polymers which relative to their own mass, can absorb and hold extremely large amounts of liquid. Water absorbing polymers, through bonding between hydrogen and water molecules absorb aqueous solutions. An SAP may absorb 450- 500 times its weight (from 40 to 60 times its own volume) and can become up to 99.99% liquid, but when put into a 0.9% saline solution, the absorbency drops to maybe 40-50 times its weight. The main use of SAP is found under agriculture. It is also used in disposable baby sanitary products due to its water retaining property. In powdered form, they appear to be white sugar like hygroscopic material. SAP is considered to be a smart material It swells up when it is exposed to water and it reversibly shrinks and releases the entrained water, when subjected to drying. This article deals with the effects of SAP on different proprties of concrete due its own water entraining property.
-
Self Sealing Cracks with SAP
Cracking of concrete structures is a common problem due to the intrinsic brittleness of the material. This may lead to severe loss of durability and water tightness. Conventional
methods for mitigating this problem such as providing additional reinforcement or movement joints in new structures and resin injection to seal cracks in existing structures may not always be appropriate or sufficient. The aim is to investigate the potential of superabsorbent polymers (SAP) as an admixture for self-sealing cracks in concrete. SAP are unique cross-linked polymers that can absorb a vast amount of liquid and swell substantially to form a soft insoluble gel. Common types of SAP are Polycrylate and Polycrylate-co-acrylamide that are widely used in personal care products such as nappies. Other applications of SAP include biomedical bandages, agricultural soil conditioning, waste solidification and meat packaging. This unique feature of SAP is highly dependent on pH, ionic content and concentration of the solution re allows SAP to be exploited for self-sealing cracks.
Fig 1.1: Self Sealing Cracks With Super Absorbent Polymer
(SAP)
CHPATER2 LITERATURE REVIEW
-
George C. Hoff gave the consultancy report on The Use of Lightweight Fines for the Internal Curing of Concrete. (2002).
The benefits of using lightweight aggregates in concrete to help reduce cracking in slabs and bridge decks has been intuitively known for decades by the lightweight aggregate industry but the reasons as to why this occurred were not extensively examined and the benefits were not widely promoted. It was believed, and correctly so, that the lower modulus of the LWA and the improved transition zone around the LWA particles due to their generally vesicular surface, helped reduce stress concentrations between the paste and the aggregate and those reductions subsequently reduced the amount of early-age cracking in the concrete. In the 1980s, the production of high-strength concrete (HSC) became more common and, to accomplish it, came the use of higher cement contents, supplementary cementing materials such as silica fume, fly ash and blast furnace slag cement, and lower water-binder ratios as a result of the extensive use of super plasticizers. The term high-performance concrete (HPC) also emerged with a
focus on providing special properties of concrete above what would normally be expected from concrete produced for general use. Most of the HPC was directed at improved durability. The durability improvements came by reducing or eliminating the transport mechanisms of the environment into the concrete and this generally followed the same modifications of the mixture proportions that occurred for HSC.
-
PietroLura experimented with Pumice for Internal Water Curing.(2004)
A novel concept in internal curing of High Performance Concrete is based on dispersing very small, saturated lightweight aggregates (LWA) in the concrete, containing sufficient water to counteract self-desiccation. With this approach, the amount of water in the LWA can be minimized, thus economizing on the amount of the LWA. In this study, the pore structure of different size fractions of pumice aggregates was characterized by different techniques. The different size fractions show differences in porosity, sorption behaviour, and pore-size distribution. The smaller size fractions have lower water absorption, but they release a greater percentage of their absorbed water at the equilibrium relative humidity of practical interest in early- age concrete, above 90%.Additionally, early-age properties of mortars with different contents of saturated pumice were investigated: a reference mix without pumice and mixes with 4% and 8% pumice by volume of mortar. By addition of pumice, mortars with improved strength, enhanced degree of hydration and reduced autogenously shrinkage were obtained. An important obstacle for the application of this kind of pumice for actual concrete productions saturation of the particles, which can be achieved only by immersion in boiling water or by vacuum saturation.
-
Ryan Henkensiefken, studied Internal Curing in Cementitious Systems Made Using Saturated lightweight Aggregate.(2008).
-
Low water-cement ratio concrete mixtures have been increasingly promoted for use in civil engineering infrastructure due to potential improvements in strength and durability. Despite their increased strength and reduced permeability, these mixtures are susceptible to early-age cracking caused by autogenously shrinkage. Methods have been developed to reduce the cracking susceptibility of these mixtures. One such method is internal curing. Internal curing uses water-filled lightweight aggregate to supply water to counteract the effect of self-desiccation after the initial pore structure of the paste has formed. This project evaluated the shrinkage cracking performance and fluid transport properties of mixtures containing internal curing. This thesis describes how chemical shrinkage results in internal vapor-filled void creation which leads to self-desiccation. The use of internal curing agents can provide a sufficient volume of water in the lightweight aggregate (LWA) to counteract the effects of self-desiccation. In addition to the volume of water provided by the LWA, the distribution of the LWA plays an integral role in the effectiveness of
internal curing. X-ray absorption measurements indicate that the water can travel up to 1.8 mm during the first 75 hours. These results are combined with a hard core soft shell model developed at NIST to determine the spacing between lightweight aggregate particles to indicate an efficient aggregate size and grading. The cracking potential of sealed and unsealed mixtures is presented when the mixtures are restrained from shrinking freely using the restrained ring test. The results indicate that if a sufficient volume and an appropriate spacing of lightweight aggregate are used, shrinkage cracking can be significantly reduced or eliminated for both sealed and unsealed curing conditions.^ The results of this study indicate that when internal curing is used, the overall water absorption and electrical conductivity is reduced. This is shown to be due to the increased degree of hydration and a DE percolation of the interfacial zones around the aggregate. As a result, mixtures with internal curing may have a w/c of 0.30 but exhibit the performance of a concrete with a lower w/c (e.g., 0.23).
CHAPTER 3
PROBLEM STATEMEMNT AND OBJECTIVES
-
Problem Statement
Primary focus of this experimental study is to investigate changes in compressive strength of concrete when it is cured internally by addition of super absorbent polymer for internal curing over the traditional way of curing. This study also identifies the optimum quantity of Super Absorbent Polymer added to get Maximum Compressive Strength of Concrete.
-
Objectives
-
Analyse adoption of alternative materials as an aspect of sustainable concrete mix design.
-
Study effect of internal curing as a complement to traditional curing in conventional concrete.
-
Casting of specimens with aggregate replacement and
inclusion of SAP (Super Absorbent Polymer) with varying proportion as an internal curing agent and testing them for Compressive Strength.
-
Study the effect of reduced shrinkage on properties of
internally cured concrete over conventionally cured concrete through test for strength.
CHAPTER 4 THEORETICAL CONTENTS
-
Superabsorbent Polymer (SAP)
Superabsorbent polymers (SAPs) (also called slush powder) can absorb and retain extremely large amounts of a liquid relative to their own mass. Water-absorbing polymers, which are classified as hydro gels when cross-linked, absorb aqueous solutions through hydrogen bondingwith water molecules. An SAP's ability to absorb water depends on the ionic concentration of the aqueous solution. In de-ionized and distilled water, a SAP may absorb 300 times its weight (from 30 to 60 times its own volume) and can become up to 99.9% liquid, but when put into a 0.9% saline solution, the absorbency drops to approximately 50 times its weight. The
presence of valence cations in the solution impedes the polymer's ability to bond with the water molecule.
The total absorbency and swelling capacity are controlled by the type and degree of cross-linkers used to make the gel. Low-density cross-linked SAPs generally have a higher absorbent capacity and swell to a larger degree. These types of SAPs also have a softer and stickier gel formation. High cross-link density polymers exhibit lower absorbent capacity and swell, but the gel strength is firmer and can maintain particle shape even under modest pressure.
An SAP can ensure very efficient internal water curing, which is defined as incorporation of a curing agent serving as an internal reservoir of water, gradually releasing it as the concrete dries out. Internal water curing has been used for decades to promote hydration of cement and to control the shrinkage of concrete during hardening. Saturated lightweight aggregate was previously the only material used as an internal curing agent. But there are some major problems connected to the use of lightweight aggregates for internal water curing, including difficulties in controlling consistency and significant reductions in strength and elastic modulus. These difficulties are minimized with the use of SAPs.
The main use of SAP is found under agriculture. It is also used in disposable baby sanitary products due to its water retaining property. In powdered form, they appear to be white sugar like hygroscopic material. SAP is considered to be a smart material It swells up when it is exposed to water and it reversibly shrinks and releases the entrained water, when subjected to drying.
Superabsorbent are cross-linked networks of hydrophilic polymers with a high capacity for water uptake. They have a variety of valuable applications in medicine, agriculture and industry in general. Early superabsorbent ate were made from chemically modified starch and cellulose and other polymers like polyvinyl alcohol, polyethylene oxide, all of which are hydrophilic and have a high affinity for water. When lightly cross-linked, chemically or physically, these polymers became water-swell able but not water soluble.
Fig. 4.1: Sodium Polyacrylate
Todays superabsorbent polymers are made from partially neutralized, lightly cross-linked acrylic acid and acryl amide
and their modifications. The polymers are manufactured at low solids levels for both quality and economic reasons, and are dried and milled into granular white solids. In water they swell to a rubbery gel that up to 99 wt. % water.
The super absorbent polymer used is Sodium Polyacrylate, also known as water-lock, which is a sodium salt of polyacrylic acid with the chemical formula [-CH2- CH(COONa)]n and broad application in consumer products. Sodium polyacrylate is anionic polyelectrolytes with negatively charged carboxylic groups in the main chain.
For their application in concrete, the following properties of SAP are of particular relevance:
-
Chemical stability in ionic solutions;
-
Absorption and desorption behaviour in concrete (or, alternatively, in cement paste filtrate), under pressure and at different temperatures;
-
Particle size (distribution).
The incorporation of SAP increases the porosity of concrete which may affect the durability of concrete. However, SAP with the absorption and desorption properties can change the water distribution in concrete. So that the process of cement hydration is promoted, the microstructure of cement matrix is improved, and the adverse effects of voids released by SAP can be offset.
The use of superabsorbent polymer in concrete is also useful in frequent freeing-thawing cycle environment, by providing the concrete frost protection. The superabsorbent polymers particles shrink during the hydration process leaving voids in the concrete similar to the voids created by adding air entrainment agent to the concrete. The air bubbles left in the concrete are critical to absorb the hydraulic pressure due the water freezing. Water expands upon freezing about ten percent in volume generating hydraulic pressure in the concrete that has the potential to cause the concrete to crack. Providing voids in the concrete absorb the hydraulic pressure and provide addition space for the water to expand. The same can be said about the osmotic pressure in the concrete. The osmotic pressure is usually generated due to the difference in salt concentration in the water. This difference in salt concentration can be created by adding deicer to the concrete top surface, for the purpose of melting the ice on the concrete. Also, these voids can be useful to absorb other kinds of internal pressures in concrete including alkali reactivity pressure.
Sodium polyacrylate is a chemical polymer that is widely used in a variety of consumer products for its ability to absorb several hundred times its mass in water. Sodium polyacrylate is made up of multiple chains of acrylate compounds that possess a positive anionic charge, which attracts water-based molecules to combine with it, making sodium polyacrylate a super-absorbent compound. Sodium polyacrylate is used extensively in the agricultural industry and is infused in the soil of many potted plants to help them retain moisture, behaving as a type of water reservoir. Florists commonly use sodium polyacrylate to help keep flowers fresh.
-
-
Advantages of SAP
-
Super absorbent polymer has been successfully used as internal curing agents & it should be minimize whole curing which necessary for gaining the strength.
-
SAP also helps to increase the strength of concrete compare with the normal concrete.
-
Due to lack of sufficient quantity of water shrinkage is observed in concrete as a results SAP helps for reducing such problem of shrinkage.
-
Water Stored in SAP Pores is available for internal curing which may cause a denser structure of cement matrix.
-
As the Addition of SAP, it results very effective in reducing the cracking in bonded mortar overlays.
-
-
Internal curing of concrete
Internal curing was originally defined by the American Concrete Institute (ACI) as "suspplying water throughout a freshly placed cementitious mixture using reservoirs, via pre-wetted lightweight aggregates, that readily release water as needed for hydration or to replace moisture lost through evaporation or self-desiccation." Internal curing helps concrete realize its maximum potential in a simple, economical and sustainable way. IC improves hydration, reduces early cracking, reduces chloride ingress, reduces curling and improves durability, all of which extend the concrete's service life.
The process of curing involves maintaining satisfactory moisture content and temperature after concrete is placed in order to hydrate the cement particles and produce the desired hardened concrete properties. Proper curing can improve strength, durability, abrasion resistance, resistance to freeze-thaw cycles, deicer scaling resistance and reduce concrete shrinkage. Traditionally, concrete has been cured externally either through the use of water curing or sealed curing. Curing either supplies additional moisture from the original mixing water or minimizes moisture loss from the concrete. Water may be bonded directly on the concrete surface or may use other methods like wet burlap bags or fogging near the surface of the concrete to prevent evaporation of water from the fresh concrete. Internal curing can be divided into two categories. The first category is internal watr curing in which an internal curing agent stores water during mixing which is gradually released as hydration processes. The second category is internal sealing which is very similar to external sealed curing in that its goal is to prevent the loss of moisture from the concrete.
Concrete curing is necessary for one reason: cement hydration. Cement hydration is a series of chemical reactions that require an adequate water supply and proper temperatures over an extended time period. Curing is defined as action taken to maintain moisture and temperature conditions in a freshly placed cementitious mixture to allow hydraulic cement hydration and (if applicable) pozzolanic reactions to occur so that the potential properties of the mixture may develop.
Conventional concrete is typically cured using external methods. External curing prevents drying of the surface, allows the mixture to stay warm and moist, and results in continued cement hydration. Internal curing is a relatively recent technique that has been developed to
prolong cement hydration by providing internal water reservoirs in a concrete mixture that do not adversely affect the concrete mixtures fresh or hardened physical properties. Internal curing grew out of the need for more durable structural concretes that were resistant to shrinkage cracking. Internal curing decreases the risk of cracking by providing additional water to a concrete mixture for the purpose of prolonged cement hydration without affecting the w/cm ratio. Internal curing can be provided by highly absorptive materials that will readily desorb water into the cement pore structure. This will reduce capillary stresses and provide additional water for cement hydration. Materials that may be used for internal curing include LWA, super
absorbent particles (SAP), perlite, and wood pulp.
Internally cured concrete is not a new concept; some might even say it is ancient since it can be considered to date back to concrete constructed during the Roman Empire. Internal curing provides something that most concrete needs and conventional curing cannot provide: additional internal water that helps prevent early age shrinkage (reducing early age cracking) and increases hydration of cementitious materials throughout the concrete. Once concrete sets, hydration creates partially-filled pores in the cement paste which causes stress that result in shrinkage. IC provides readily available additional water throughout the concrete, so hydration can continue while more of the pores in the cement paste remain saturated. This reduces shrinkage, cracking, early age curling/warping, increases strength and lowers the permeability of the concrete, making it more resistant to chloride penetration.
Internal curing does not replace conventional surface curing, but works with it to make concrete more robust. Internal curing can also help compensate for less than ideal weather conditions and poor conventional curing that is often seen in the real world. ACI defines internal curing (IC) as a process by which the hydration of cement continues because of the availability of internal water that is not part of the mixing water.
CHAPTER 5 EXPERIMENTAL WORK
-
Methodology
Fig 5.1: Methodology Chart
-
Material Used:
-
Super Absorbent Polymer (SAP)
Super absorbent polymers (SAP) also known as slush powder are polymers which relative to their own mass, can absorb and hold extremely large amounts of liquid. Water absorbing polymers, through bonding between hydrogen and water molecules absorb aqueous solutions. An SAP may absorb 450- 500 times its weight (from 40 to 60 times its own volume) and can become up to 99.99% liquid, but when put into a 0.9% saline solution, the absorbency drops to maybe 40-50 times its weight. The main use of SAP is found under agriculture. It is also used in disposable baby sanitary products due to its water retaining property. In
powdered form, they appear to be white sugar like hygroscopic material. SAP is considered to be a smart material It swells up when it is exposed to water and it reversibly shrinks and releases the entrained water, when subjected to drying. This article deals with the effects of SAP on different properties of concrete due its own water entraining property.
Fig.5.2: Powdered form of Super Absorbent Polymer (SAP)
-
Cement
-
Cement is a binder, a substance used for construction that sets, hardens and adheres to other materials, binding them together. Cement is seldom used on its own, but rather to bind sand and gravel (aggregate) together. Cement is used with fine aggregate to produce mortar for masonry, or with sand and gravel aggregates to produce concrete. Cements used in construction are usually inorganic, often lime or calcium silicate based, and can be characterized as being either hydraulic or non-hydraulic, depending upon the ability of the cement to set in the presence of water. Cement is a fine mineral powder manufactured with very precise processes. Mixed with water, this powder transforms into a paste that binds and hardens when submerged in water. Because the composition and fineness of the powder may vary, cement has different properties depending upon its makeup. Cement is the main component of concrete. It's an economical, high-quality construction material used in construction projects worldwide.
Fig.5.3: Cement
5.2.3. Aggregates and their tests
Aggregates are inert granular materials such as sand, gravel or crushed stone that are an end product in their own right. They are also the raw materials that are an essential ingredient in concrete. For a good concrete mix, aggregates need to be clean, hard, strong particles free of absorbed chemicals or coatings of clay and other fine materials that could cause the deterioration of concrete.
-
Coarse Aggregate
Aggregates which are greater than 4.75 mm and retained in
4.75 mm I.S. sieve is considered as coarse aggregates. In the present study locally available crushed stone aggregate of size 20 mm and 10 mm has been used. The aggregates have been tested as per IS: 2386-1963(Part -1&3) IS: 383-2016. Properties of coarse aggregate are as below.
-
Specific Gravity of Coarse aggregates
The coarse aggregate specific gravity is determined by obtaining the ratio of the weight of a given volume of aggregate to the weight of a given volume of aggregate to the weight of an equal volume of water. The coarse aggregate specific gravity test measures coarse aggregate weight under three different sample conditions viz, oven dry, saturated surface dry and submerged in water.
Weight of aggregate with bucket immersed in water (W1)
= 3383.2 gm
Weight of bucket immersed in water (W2) = 2756.5 gm Weight of saturated surface dried aggregates (W3) = 992 gm Weight of oven dried aggregates (W4) = 970.9 gm Specific gravity (S)
= (W4) / (W3-(W1-W2))
=(970.9)/(992-(3383.2-2756.5))
Specific gravity (S) = 2.66
-
Water Absorption
Water absorption = ((W3-W4) / (W4)) x 100
= ((992-970.9) / (970.9)) x 100
Water absorption = 1.58%
-
-
Fine Aggregates
Aggregate most of which passes through 4.75 mm IS sieve is known as fine aggregate. Fine aggregate shall consist of natural sand, crushed stone sand. It shall be hard, durable, chemically inert, cleaned free from adherent coatings, organic matter etc. and shall not contain any appreciable
amount of clay balls or pellets and harmful impurities e.g. iron pyrites, alkalis, salts, coal, similar laminated materials in such form or in such quantities as to cause corrosion of metal or affect adversely the hardening, the strength, the durability or the appearance of mortar, plaster or concrete. The sum of the percentages of all deleterious material shall not exceed 5%. Fine aggregate must be checked for organic impurities such as decayed vegetation humps, coal dust etc.
- Specific Gravity of fine aggregates
Weight of Pycnometer, sand and water (W1) = 1820 gm Weight of Pycnometer and water (W2) = 1504.90 gm Weight of saturated surface dried aggregate (W3) = 506.7 gm Weight of oven dried aggregate = 500.1 gm Specific gravity (S)
= (W4) / (W3-(W1-W2))
= (500.1)/(506.7-(1820-1504.9)
= 2.62
-
Water Absorption
= ((W3-W4) / (W4)) x 100
= ((506.7-500.1) / (500.1)) x 100
= 1.31%
-
Mix Design of Concrete
-
Type of cement PPC
-
Max nominal size of aggregate 20mm
-
Exposure condition – Moderate
-
Types of aggregates crushed angular aggregate
-
Target strength for mix proportion:
Fck = fck + 1.65S
Fck= compressive strength at 28 days =25 N/mm2
S Standard deviation = 4 (Table No.1 IS 10262:2009) Fck= 25+1.65 X 4 = 31.60 N/mm2
-
Selection of w/c ratio
For moderate exposure conditions and maximum nominal size of aggregate 20mm Max w/c ratio = 0.6 (IS 456 (2000)
Adopting w/c ratio = 0.55
-
Selection of Water content
For maximum nominal size of aggregate 20mm, maximum water content is 186 liters
Desired slump is 75 mm Required water content = 186 kg
-
Calculation of Cement Content
w/c ratio = water content / cement content cement content = water content / w/c ratio Therefore,
Total cement content = 186/0.55 = 338.1818 kg/m3
Check for minimum cement content as per IS 456 (2000) From table No.5 of IS 456(2000) minimum cement content for moderate exposure conditions = 300kg/m3
338.1818 kg/m3> 300kg/m3
-
Proportion of volume of coarse aggregate and fine aggregate content
From table 3 of IS 10261:2009, Volume of coarse aggregates corresponding to 20mm nominal maximum size of aggregate and fine aggregate Zone II and w/c ratio 0.5 = 0.62
Therefore proportion of volume of coarse aggregates = 0.62 Proportion of volume of fine aggregate = 1-0.62 = 0.38
-
Mix Calculation:
-
Volume of concrete 1m3
-
Volume of cement = (Mass of cement/ S.G. of cement) x (1/1000)
= (338.1818/3.15) x (1/1000)
= 0.107m3
(c) Volume of Water = 186 x (1/1000) = 0.186m3
-
Volume of all aggregates (a)-(b+c) = 1-(0.107+0.186) = 0.707m3
-
Mass of coarse aggregates = volume of all aggregates x proportion volume of coarse aggregate x mass density of coarse aggregates
= 0.707 x 0.62 x 2.66 x 1000 = 1165.98kg
-
Mass of Fine Aggregates = volume of all aggregates x proportion volume of fine aggregate x mass density of fine aggregates
= 0.707 x 0.38 x 2.62x 1000 = 703.88kg
-
-
Mix Proportion for 1m3 Concrete
Cement = 338.1818 kg
Fine Aggregate = 703.88 kg Coarse Aggregate = 1165.98 kg Therefore
C:FA:CA = 1: 2.08: 3.44
(By Weight) C: FA: CA = 1: 2.51: 4.09
(By Volume)
-
Materials required for 24 cubes
0.15 × 0.15 × 0.15 × 24 = 0.081m3
Cement = Mass of Cement × Volume of 24 cubes
= 338.1818 × 0.081
= 27.392 kg
Proportion for 24 cubes,
C: FA: CA = 27.392: 56.976: 94.228
Proportion for 6 cubes,
C: FA: CA = 6848: 14.243: 23.557
Proportion for 6 cubes (Including Wastage),
C: FA: CA = 7.989: 16.616: 27.482
-
-
SLUMP CONE TEST
-
Introduction
Slump test is the most commonly used method of measuring consistency of concrete which can be employed either in laboratory or at site of work. It is not a suitable method for very wet or very dry concrete. It does not measure all factors contributing to workability, nor is it always representative of the place ability of the concrete.
It indicates the characteristic of concrete in addition to the slump value. If the concrete slumps evenly it is called true slump. If one half of the cone slides down, it is called
shear slump. In case of a shear slump, the slump value is measured as the difference in height between the height of the mould and the average value of the subsidence.
-
Resources Used
Table No. 5.1 Resources Used
S
r.
No.
Particu lars
Specificatio n
Qua ntity
Rem ark
0
1
Slump Cone
Apparatus
As per IS 7320-1974, Top
diameter100mm, Bottom diameter 200mm and Height 300mm having metal
thickness of 1.6mm
01
—
0
2
Tampin g Rod
16mm dia., 600mm length and having one bullet end.
01
—
-
Procedure Followed
-
Take slump cone of height of 30cm and dia. 20cm, apply oil to its inner surface.
-
Prepare the concrete mixture of 20 grade required and the admixture which is to be used is super plasticizer by proportion.
-
After mixing fill it in the slump cone mould in 4 layers and compact each layer 25 times with 16 mm dia. Steel rod
-
Then After the filling give some finishing then at a time pick up the slump cone mould vertically using mould handle.
-
Note down the reading by tamping rod in cm.
Fig. 5.4: Slump Cone Apparatus with Sketch
Fig.5.5: Slump Cone Test
-
-
-
COMPRESIVE STRENGTH OF CONCRETE
-
Introduction
Concrete mix can be designed to provide a wide range of mechanical and durability properties to meet the design requirements of a structure. The compressive strength of concrete is the most common performance measure used by the engineer in designing buildings and other structure. A compression test is a test in which a material experiences opposing forces that push inward upon specimen from opposite sides or is otherwise compressed, crushed. The test sample is generally placed in two plates that distribute the applied load across the entire surface area of two opposite faces of test sample and the plates are pushed together by compressive test machine. Compressive strength of concrete depends on many factors such as water-cement ratio, cement strength, quality of concrete material, quality control during production of concrete. Compressive strength test is conducted on hardened concrete after 7, 14, & 28 days.
-
Resources Used
Table No. 5.2 Resources Used
Sr.
No.
Particulars
Specification
Quantity
Remark
0
1
Compressi on Testing Machine
Compression Testing Machine 2000KN capacity
01
—
0
2
Moulds
Cast Iron: for 150 mm cube with
ISI certification mark IS:10086
06
—
0
3
Vibrating Table
Vibrating Table top 500mm
× 500mm with edges
01
—
0
4
Tamping Rod
16mm dia., 600mm length and having one bullet
end.
01
—
-
Procedure Followed
-
Prepare a sample of concrete mix and cast cubes of 150mm × 150mm ×150mm.
-
The concrete shall be filled into the moulds in layers approximately 50mm deep. It would be disturbed evenly and compacted by hand tamping. After the top layer has been compacted, the surface of concrete shall be finished level with the top of the mould using a trowel; and covered with a glass plate to prevent evaporation.
-
The specimen shall be stored 24 hours under damp matting or sack. After that the samples shall be stored in clean wate at 27+2C; until the time of test.
-
Specimen shall be tested immediately on removal from water and while they are still in wet condition.
-
The bearing surface of the testing specimen shall be wiped clean and any loose material removed from the surface. In the case of cubes, the specimen shall be placed in the machine on sides of cubes and not to the top and bottom.
-
The load shall be applied slowly without shock and increased continuously at a rate of approximately 140kg/sq.cm/min until the resistance of the specimen of increased load breaks down and no greater load can be sustained. The maximum load applied to the specimen shall then be recorded and any unusual features noted at the time of failure brought out in the report.
Fig.5.5: Compression Test on Concrete Cube
-
-
Precautions Followed
-
-
After test switch off the machine.
-
Keep all the exposed metal parts greased.
-
Keep the guide rods firmly to the base and top plate.
-
Equipment should be cleaned thoroughly before and after testing.
-
Petroleum jelly or oil should be applied to the mould.
CHAPTER 6 RESULTS AND DISCUSSIONS
-
Results obtained for Traditionally CuredConcrete
Sr.
No.
Compressive test taken after days
Compressive Strength
(N/mm2)
Average Compressive
Strength (N/mm2)
0
1
7
17.24
17.48
17.72
0
2
14
23.54
23.88
24.22
0
3
28
26.80
27.10
27.40
Table No.6.1 Compressive Strength of Traditionally Cured Concrete
-
Results obtained for Super Absorbent Polymer added concrete
Table No.6.2 Compressive Strength of Concrete on 7th Day (SAP)
Sr. No. |
% of SAP |
Compressive Strength (N/mm2) |
Average Compressive Strength (N/mm2) |
01 |
0.20 |
18.28 |
18.73 |
19.18 |
|||
02 |
0.35 |
23.85 |
24.00 |
24.12 |
|||
03 |
0.50 |
16.23 |
15.70 |
15.18 |
Table No.6.2 Compressive Strength of Concrete on 14th
Day(SAP)
Sr. No. |
% of SAP |
Compressive Strength (N/mm2) |
Average Compressive Strength (N/mm2) |
01 |
0.20 |
26.90 |
27.35 |
27.81 |
|||
02 |
0.35 |
30.05 |
30.32 |
30.59 |
|||
03 |
0.50 |
24.73 |
25.18 |
25.64 |
Table No. 6.3 Compressive Strength of Concrete on 28th
Sr. No. |
% of SAP |
Compressive Strength (N/mm2) |
Average Compressive Strength (N/mm2) |
01 |
0.20 |
29.55 |
29.87 |
30.20 |
|||
02 |
0.35 |
34.42 |
34.36 |
34.30 |
|||
03 |
0.50 |
27.75 |
27.83 |
27.92 |
Sr. No. |
% of SAP |
Compressive Strength (N/mm2) |
Average Compressive Strength (N/mm2) |
01 |
0.20 |
29.55 |
29.87 |
30.20 |
|||
02 |
0.35 |
34.42 |
34.36 |
34.30 |
|||
03 |
0.50 |
27.75 |
27.83 |
27.92 |
(SAP)
6.2 Comparison of Compressive Strength of Concrete
test taken after days |
M25 |
0.2% SAP |
0.35% SAP |
0.5% SAP |
7 |
17.48 |
18.73 |
24.00 |
15.70 |
14 |
23.88 |
27.35 |
30.32 |
25.18 |
28 |
27.10 |
29.87 |
34.36 |
27.83 |
Table No.6.4Compression Strength Results (N/mm2)
Graph No.6.1 Compressive Strength Results (N/mm2)
CHAPTER 7 CONCLISIONS
From experimental work and testing of specimen following conclusions have been concluded:
-
After 28 days concrete compressive strength when 0.2% of super absorbent polymer is added with increased compressive strength up to 10%.
-
After 28 days concrete attaining highest compressive strength when 0.35% of super absorbent polymer is added with increased compressive strength up to 29%.
-
After 28 days concrete compressive strength when 0.5% of super absorbent polymer is added with increased compressive strength up to 2.5%.
-
From These results we conclude that when 0.35% of Super Absorbent Polymer is added gives the highest compressive strength i.e. 34.36 N/mm2.
REFERENCES
-
Dale P. Bentz, Internal Curing and Microstructure of High- Performance Mortars, ACI Mat. Jl., Vol. 108, (6), 2010, pp 638644.
-
PietroLura. Pumice for Internal Water Curing, Proc. of Intl. RILEM Symposium on Conc. Sci. and Engng.,2004, pp 137151.
-
K Ramamurthy, The influence of super absorbent polymer beds used as internal curing agents on compressive strength of mortar, IRJET, Vol.03 Issue 02, Feb 2016.
-
IS 1199:1959 Methods of Sampling and Analysis of Concrete. Reaffirmed- Dec 2013.
-