
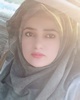
- Open Access
- Authors : Ibtesam Mohie Manee , Abdul Kareem Flaih Hassan , Emad Obaid Baji
- Paper ID : IJERTV9IS120033
- Volume & Issue : Volume 09, Issue 12 (December 2020)
- Published (First Online): 14-12-2020
- ISSN (Online) : 2278-0181
- Publisher Name : IJERT
- License:
This work is licensed under a Creative Commons Attribution 4.0 International License
Experimental and Numerical Study of Low Carbon Steel Cold Flat Rolling
Ibtesam Mohie Manee Mechanical Department University of Basrah
Abdul Kareem Flaih Hassan Mechanical Department University of Basrah
Emad Obaid Baji Mechanical Department University of Basrah
Abstract- In this, work an experimental and numerical study of cold flat rolling has performed, to investigate the effect of cold flat rolling on the mechanical properties of low carbon steel sheet and rod. The study indicated that the rolling process has a remarkable effect on the yield stress, ultimate tensile and hardness. FEM has built by ABAQUS software to study the deformation behavior of rod after rolling process, an equation derived from the numerical result to investigate the deformation of rod flat rolling in the design stage without perform an experimental test.
Index Terms Rod, Rolling, ABAQUS
-
INTRODUCTION
Rolling process consider one of the most significant cold and hot forming metal process, it is cover more than 90% of cold and hot working process for both ferrous and non – ferrous metals and alloys which processed to their final usable shape by using rolling process. Usable shapes of rolled metals are plate, sheet, strip, foil, different sections like rail, beam, channel, angle, bar, rod, and seamless pipe, etc. [1,2] The rolling process product may become thinner while passing through the roll. Because the rolling operating is fast and economical, it is used wherever possible. Rolling process covers most of metal working processes used in different industrial applications, mostly these metals has high ductility and low yield point to be possible to cold rolled [3,4].
The main principle of rolling process whereby the ingot is gripped by two rolls and squeezed between them, the rolls are identical and they are rotating so they grab the ingot between them [5,6].
M. Kazeminezhad, A. Karimi Taheri [7, 8, 9] studied experimentally the impact of rolling speed occurring on rolling force required to deform the specimen and deformation behavior after rolling. They found that rolling force decrease with increasing rolling speed and the behavior of deformation was calculated by using numerical equation to calculate the depth of contact area b=(2h h) [10].
w. ozgowicz and A.kurc, 2009[11] studies, the cold rolling impacts on mechanical and structural properties of stainless steel austenitic type (18-8) were deliberated. Likewise, to observe the function of rolling reduction, the austenitic stainless steel types (X5CrNi18-8) conversion to martensitic type were considered under the cold rolling influence. The mechanical properties during tensile test, measurement of
micro hardness and structure observations organized by Vickers Method were also investigated. On the base of cold rolling processs X-Ray studies, 10-70% thickness reduction in phase composition was also analyzed. It was found that with the increasing deformation (10-70%), the yield point of steel increased by about 98%, tensile strength increased by about 91%, hardness increased by about 76%, while the elongation deceased by about 98%[12].The conclusion indicated that the sum of martensite phase in steel type X5CrN 18-8 relies upon the plastic deformation degree. Further the 10-70% augmented deformation comprised of a martensite conversion (austinate to martensite ) and increasing part of the martensite phase from 9% to about 50%.also it was found that the metastability of austinatic stainless steel increase with the decrease of the stacking fault energy (SFE).
Mohammad. Tajally et al.,2009[13] Calculated the aluminum alloy 7075 tensile behavior and cold rolling impact on bending. The experimental series were directed for AL alloy 7075-O while comprising the 58% cold work of cold rolling. To study the mechanical properties affected by cold work, three mechanical test were carried out on the alloy before and after cold rolling process (tensile, hardness and bending test). The reduced alloy ductility and increased strength of yield were presented as a result of substantial effect of cold rolling. This research further examined the cold rolled specimens cracked surfaces. During the bending test, the conversion conduct like dimples lack from ductile to brittle was visibly presented. Subsequently to 58% of the cold work, a prompt increase in the yield power (119.25%) was established. Correspondingly, a decreased rolled materials percentage elongation and an upsurge in hardness as well as tensile strength was also perceived. Likewise, an improved yield stress about 58% for cold work bending & reduced strain and displacement at yield were also comprehended. The duet was found to be of high density dislocation in the sample of cold roll by this specific material.
M. Kazeminezhad and Karimi Taheri, 2006[14,15]. Studied the application of the FSEM for analyzation of flat wire rolling method by utilizing an amalgamation of slab method and two dimensional finite element. Further, the condition for force boundary was applied as a constant factor of friction during the simulation. In comparison to the surface of roll, the direction of materials resistance force vector contrary to work pieces relative velocity was preferred. A selection of friction feature for lubrication (0.07) and non-lubrication (0.2)
condition was done. Whereas the roll speed of 42 rpm and diameter as of 150 mm were also chosen. Further it was concluded that after flat wire roll procedure at various friction condition and height reduction, the geometry as well as the effective strain fields were established while using the FSEM. The un-identical flat wire rolling found the supreme & lowest active strain at the midpoint & round edge of flat wire correspondingly. B. Wang, W. Hu, L.X. Kong and P. Hodgson .[16] Deliberated the numerical relevancy for the spinning speed of rolls with the help of ABAQUS known as a commercial FEM code. This was performed on rolling process and various number of the cases were considered. Moreover, the rigid rolls tend to have the angular velocity of 30-480 rpm (revolutions per minute). A slip was observed among the roll surface and plate as the preliminary plate feeding speed was set to be persistent. The consequences directed the similar reduction in thickness for an elastic-plastic plate toughening. As well the residual stress at it maximum value and minimizing the separating potency of the rolls was achieved by the advanced roll rotating speed. The large variance can cause a comprehensive slipping among the plate and roll surfaces which was indicated by simulations. For instance, the deformed zone showed no lines or neutral points. compete the roll surface velocitys horizontal constituent in the pathway of feeding.
-
EXPERIMENTAL WORK
In this work, the material used was low carbon steel AISI 1012 chosen to study the effect of reduction ratio by cold rolling process on the mechanical properties and microstructure also a rod of low carbon steel to predict the deformation behavior of rod after rolling. A chemical analysis done by spectrometer testing devise. The test of chemical composition was conducted in accordance with ASTM A751 standard [17] with Spector (Materials spectrometer analyzer Model SPECTROTEST TXC25, Made in Germany) as represented in the below tables (1-1).
The rolling machine used contains a pair of parallel rolls, Each roll have (102mm) radius and (75 mm) length, and connect with a series of roll takes the motion from the gearbox linked with electrical motor. A handle can adjust the gap between the roll and strip contain a scaling in millimeter fixed on macine. When the handle rotate the upper roll come down to the desired gab between the two rolls, the roll angular velocity measured by using photo contact tachometer. The angular velocity of rolls is equal to (3 RPM) according to the machine constant capacity.
For prepare the cold rolling process used ten specimens of carbon steel, five of the rod and others of the sheet. The cold rolling process was carried out at room temperature at (21º C) by passing the metal in between two rolls that rotate in the opposite directions. There is a space in between the two rolls which is less as compared to the thickness of the entrance metal (modifiable as the required quantity of reduction ratio). The friction alongside the interface behaves to push the metal in the forward direction. This is because the roll speed is greater than the incoming metal speed. The metal was modified in cross dimension and was squeeze elongate. The degree of friction alongside the interface controls the degree of deformation that is gained in a single pass between two
rolls. The reduction ratios details and number of pass through the roll required for each reduction ratio for both sheet and rod explained in tables (1.2) and (1.3).
Mechanical Tests Static Tensile Test
In this work, tensile tests were performed at room temperature using tensile test device at AL-Hassany Industrial Group. This test were conducting according to the ASTM E8/E8-13a [18] for sheet specimen. The dimension of longitudinal tensile sheet test specimen were (200×20×12.5 mm) with a gauge length of (G=50 mm) as shown in figure (3.7), five specimen were test to measure the tensile properties of each redaction ratios. For rod rolling three specimens were prepare for tensile test according to the ASTM E8/E8-13a as shown in figure (3.9) and (3.10) , to be used in the prediction of elastic and plastic behavior of rod in the FEM
-
Hardness Test
In the present work, Vickerss hardness test was carried out to estimate the effect of reduction ratio on the hardness of carbon steel, which employ a diamond ball with main load of 100 kilogram and insignificant load of 10 Kilogram. Measurement were taken on the rolling surface for both rod and sheet specimens. Three measurements were taken for each sample (for each redaction ratio), and then average hardness were calculated.
-
Metallographic Test
The following steps performed to prepare sample for this study using the grinding and polishing machine. Preparation stage started with wet grinding of sample using emery paper in grades (180, 400, 500, 800, 1000, and1200,) then a polishing process was carried out using the alumina powder suspended solution particle size (1µm, 0.3 µm, 0.05 µm), and napless cloth and then the sample were cleaned with water. Finally, etching process using the swap a few second to a minute in the solution (40 mL HCL, 5 g CuCl2, 30 mL water, 25 mL ethanol (95%) or methanol (95%)) according to ASM E 407-99[19]. After sample preparation was completed, microstructure imaging was done using an optical microscope, to investigate the microstructure before and after rolling process.
-
-
NUMERICAL WORK:
This study employs to study the geometry of final product in cold rod flat rolling, numerous reductions have been simulated. The general analysis by using ABAQUS / Explicit has eight distinct steps that are the finite element software (ABAQUS/Explicit, 2016) to model the rod flattening technique, the creation of model that indicates the physical method to be analyzed is the primary stage in explicit dynamic analysis. Five reduction ratios were done by experimental work. The roll and rod diameters used in simulated are (204 mm and 8 mm) respectively. However to simulate the cold rolling process, five three dimensional models were created by ABAQUS software each pass through the gab represented a one reduction ratio in experimental work as shown in figure (1-1).
Figure (1-1) Full model by using ABAQUS
To defining materials properties in this work bilinear kinematic materials model has been used for the rod materials to be rolled. While the rolls are modeled as rigid bodies. The bilinear kinematic hardened model employs two slops (plastic and elastic) to denote the stress strain behavior of materials. Input elastic modulus, density, poisons ratio, yield stress are required for the model. Strain-stress curve for rod material taken from experimental work. The mesh family is of the (Solid) continuum element, kind for a 3D model, is needed for the current analysis. This mesh element contains six faces and
8 nodes at the corners as represented in Fig (1-2). After drawing the geometry of the cold rolling process the element type chosen is C3D8R.an 8-node linear brick element with nine degree of freedom at each nod, translation, velocities, and acceleration (UX, UY, UZ, VX, VY, VZ, AX, AY, AZ). The reduce integration hourglass control is used by default for faster element formulation. One point integration is beneficial because of saving robustness time and computer time in situation of huge deformation [20].
Figure (1-2) Type element (C3D8R)
After the construction of model, the next stage is to apply loads, it is to be noted that the loading is applied to the structure over a definite time interval in an explicit dynamic analysis. The purpose is to detect the transient behavior of models for applied loads over the particular time interval. The boundary condition of this cold rolling is the initial step the rod is given an initial velocity so that the rod touches the roll. In the rod constrained in the z, direction initial velocity is given to the rod in the x direction and the roller rotate gives an angular velocity with respect to its reference point. Angular velocity in the z direction about the center point of the roller, finally displacement in the z direction [15.21].
After the construction of model, the next stage is to apply loads, it is to be noted that the loading is applied to the structure over a definite time interval in an explicit dynamic
analysis. The purpose is to detect the transient behavior of models for applied loads over the particular time interval. The boundary condition of this cold rolling is the initial step the rod is given an initial velocity so that the rod touches the roll. In the rod constrained in the z, direction initial velocity is given to the rod in the x direction and the roller rotate gives an angular velocity with respect to its reference point. Angular velocity in the z direction about the center point of the roller, finally displacement in the z direction [15.21].
-
RESULTS AND DISCUSSION:
-
Percentage reduction effect on hardness properties
Figure (1-3) and (1-4) show the change in the material hardness with respect to the amount of cold working. It was found that the hardness amount increases with increasing the percentage reduction ratio. The total percentage increases in hardness number reached (23.3%) for rod rolling at 56.25% reduction in thickness and (37.7%) for plate rolling at 50% reduction.
Figure: (1-3) effect of reduction ratio on hardness of sheet.
Figure: (1-4) Percentage reduction ratio effect on hardness of rod.
-
Percentage reduction effect on tensile properties
Figure (1-5) and (1-6) show the effect of the reduction percentage in cold flat rolling on the yield and ultimate point of AISI1012 sheets.
Figure (1-5) effect of reduction ratio on ultimate stress
Figure (1-6) effect of reduction ratio on yield stress of AISI1012
-
Calculation of Contact Area Width
One of the most parameter can showing the deformation performance of rod is the widths of contacting area .Which is denoted by (b) contact, numerical and F.E show a good agreement with the found experimental element result as shown In figure (1-7). Width of contact area can be calculated from the relation b=2h
From figure (1-8) and (1-9) it is clear to detected that with an increase of o/rh lead to decrease in the amount of ln(wf / wo) and the below relation may be used to for the calculating the width spread for carbon steel A 36 rod.
The value for R-squared curve fitting of equation (1-9) is 0.955 thus; the deformation can be calculating by use the same equation above on the flat rolling as well as with the same degree of accuracy because the results indicated which are matching with the experimental result.
Figure (1.7) Reduction ratio effect on the width of contact of A36.
Figure (1-8) dependence of ln(wf / wo) on wo/ experimental.
Figure (1-9) Relation of depend ln(wf / wo) on wo/ finite element.
From the present work, the following conclusions can be drawn:
-
Comparison of experimental and finite element results shows that there is a good agreement with maximum error, there for the ABAQUS model is reliable and can be used precisely to simulate of cold flat rod rolling process of low carbon steel.
-
It is possible to predict wire distribution at the design stage without performing experiment, one can monitor and control the deformation behavior of low carbon steel of wire
in design stage during relations between the width of wire before rolling, the reduction ratio and roll radius for all deformation ratios follow the relation bellow:
-
Effect of hardness for sheet rolled was more remarkable than wire rolled because of the effect of contact area. Which is very wide for sheet than that for wire as a result amount of deformation for sheet was larger than that for wire.
-
Tensile test for sheet show very remarkable change, which indicate the benefit of rolling process.
-
-
REFERENCES
-
Principle and application of metal rolling, 'cambirdge university press' siddhart ray (2016).
-
N. zabaras "Mechanical Properties and Processing of Engineering Materials" Carnell University .2000
-
C. Vallellano , P.A. Cabanillas, F.J. Garc´a-Lomas journal of materials processing technology 1 9 5 ( 2 0 0 8 ) 6371
-
Hengcheng Liao, Mingdong Cai, Qiumin Jing, and Ke Ding Effect of Cold-rolling on Mechanical Properties and Microstructure of an Al-12%Si-0.2%Mg Alloy ASM International 2011
-
G. W. Rowe' principle of industrial metal working processes' Edward Amold Ltd. 1997
-
Betzalel Avitzur 'metal forming process and analysis" Mc Graw Hill 1983
-
M. Kazeminezhad, A. Karimi Taheri, An experimental investigation on the deformation behavior during wire flat rolling process, Journal of Materials Processing Technology, 160, 2005, 313-320.
-
M. Kazeminezhad, A. Karimi Taheri, A theoretical and experimental investigation on wire flat rolling process using deformation pattern, Journal of Materials and Design 26 (2005) 99103.
-
M. Kazeminezhad *, A. Karimi Taheri Calculation of the rolling pressure distribution and force in wire flat rolling process Journal of Materials Processing Technology 171 (2006) 253258
-
Carlson B. contact pressure distribution in flat rolling of wire" J. M Proc. Technol. 73, 1-6
-
W. Ozgowicz, and A. Kurc, " The Effect of The Cold Rolling on The Structure and Mechanical Properties in Austenitic Stainless Steels Type 18-8 ", World Academy of Materials and Manufacturing Engineering, International Scientific Journal, Vol. 38, No. 1, pp. 26- 33, 2009.
-
Hengcheng Liao, Mingdong Cai, Qiumin Jing, and Ke Ding, " Effect of Cold-rolling on Mechanical Properties and Microstructure of an Al-12%Si-0.2%Mg Alloy ", Journal of Materials Engineering and Performance, Vol. 20, No. 8, pp. 1364-1369, 2011.
-
Mohammad Tajally, Zainul Huda, and H.H. Masjuki, " A Comparative Analysis of Tensile and Impact-Toughness Behavior of Cold-Worked and Annealed 7075 Aluminum Alloy ", Elsevier International Journal of Impact Engineering ", Vol. 37, No. 4, pp. 425-432, 2010
-
M. Kazemizehad A. Karimi Taheri, Deformation inhomogeneity in flattened copper wire material and design , 28, 2007 ,PP 2047-2053
-
B.Wang, W. Hu, L.X. Kong and P. Hodgson, The Influence of Roll Speed on the Rolling of Metal Plates, Journal of metals and materials, Vol. 4, No. 4, Pp. 919-919,1998.
-
B.Wang, W. Hu, L.X. Kong and P. Hodgson, The Influence of Roll Speed on the Rolling of Metal Plates, Journal of metals and materials, Vol. 4, No. 4, Pp. 919-919,1998.
-
ASTM "Standard Test Methods, Practices, and Terminology for Chemical Analysis of Steel Products", Annual Book of ASTM Standard, A751-14a ASTM International, 2014.
-
ASTM "Standard Test Methods for Tension Testing of Metallic Materials", Annual Book of ASTM Standard, E8/E8M-13a ASTM International, 2015
-
Standard Practice for Micro etching Metals and Alloys ASM E 407- 99
-
ABAQUS online documentation, http://130.149.89.49:2080/v2016/index.html
-
Shulun Liao1,2), Liwen Zhang1,2), Siyu Yuan1,2), Yu Zhen3), and Shuqi Guo3)" Modeling and finite element analysis of rod and wire steel rolling process " Journal of University of Science and Technology Beijing Volume 15, Number 4, August 2008, Page 412