
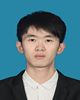
- Open Access
- Authors : Ren-Ren Xu , Ji-Fu Zhang , Zhuang Li , Shi-Yong Zhang, Ya-Qian Zhang
- Paper ID : IJERTV9IS120115
- Volume & Issue : Volume 09, Issue 12 (December 2020)
- Published (First Online): 17-12-2020
- ISSN (Online) : 2278-0181
- Publisher Name : IJERT
- License:
This work is licensed under a Creative Commons Attribution 4.0 International License
Research Status of Metal Boride Hard Coatings
Ren-Ren Xu*, Ji-Fu Zhang, Zhuang Li, Shi-Yong Zhang, Ya-Qian Zhang
Tianjin Key Laboratory of High Speed Cutting and Precision Machining, Tianjin University of Technology and Education, Tianjin 300222, China
Abstract With the rapid development of modern manufacturing industry, the emergence of all kinds of difficult to machine materials and the continuous improvement of cutting
accuracy demand, the tool coating gradually evolves from binary
to diversified nanocomposite coating, and the demand for superhard coating with high hardness is also increasing. Among them, titanium alloy materials are widely used in aerospace and other military fields. Therefore, higher and higher requirements are put forward for the heat resistance of coated tools. In many coating systems, metal boride coatings have attracted much attention due to their good wear resistance and high temperature thermal stability.
Key wordsMilitary application, metal boride coating, high temperature thermal stability
-
PREPARATION TECHNOLOGY OF HARD COATING Coating technology refers to the use of thermal spraying,
laser cladding, vapor deposition and other preparation technologies to coat a coating on the surface of the substrate with corrosion resistance, oxidation resistance, good conductivity and other strengthening effects, which can protect the matrix material and improve its service life. At present, chemical vapor deposition (CVD) and physical vapor deposition (PVD) are commonly used to prepare hard coatings. At first, CVD technology developed rapidly due to the advantages of low internal stress, dense structure and tight membrane / substrate bonding [1]. However, with the passage of time, the disadvantages such as high deposition temperature and high roughness of coating surface are becoming more and more obvious, which limits the application of CVD technology on tool surface. Moreover, the exhaust gas from CVD technology will pollute the environment, which further restricts the application and development of CVD technology.
-
Physical vapor deposition (PVD)
Physical vapor deposition technology refers to the evaporation / sputtering of solid targets into vapor phase atoms or ions by physical processes such as high-temperature evaporation, glow discharge, ion bombardment sputtering in vacuum environment, and re aggregation of these particles on the surface of the substrate, so as to realize the controllable transfer of material atoms [2]. This highly closed vacuum environment can reduce the content of reactive gas (O2) in the chamber and reduce the damage of oxygen impurities on the microstructure of the coating. In addition, higher vacuum will reduce the collision between gas molecules and the porosity of the film, which will affect the deposition rate, grain growth and phase distribution of the coating. Compared with CVD technology, PVD technology has lower preparation temperature (200~600), which can reduce the influence of temperature on the bending strength of the substrate and improve the stability of the coating [3]. In addition, the coating prepared by PVD technology also has the advantages of dense
structure, high strength, adjustable internal stress and smooth surface. Compared with CVD technology, PVD is more suitable for the preparation of precision and complex tool coating [4]. With the successful application of this technology in the field of high-speed cutting, the hardness, wear resistance, high-temperature stability and service life of the tool are effectively improved, and the further development of PVD tool coating technology is promoted. At present, the most commonly used physical vapor deposition technologies are vacuum evaporation, sputtering and ion plating.
-
Composite high power pulsed magnetron sputtering technology
High power pulsed magnetron sputtering (HiPIMS) is a high ionization rate physical vapor deposition (PVD) technology developed in recent years. In order to improve the low metal ionization rate (< 10%) of traditional magnetron sputtering, Kouznetsov et al. [5] of Sweden first proposed the high power pulsed magnetron sputtering technology in 1999. HiPIMS uses 2~3 orders of magnitude higher pulse peak power and lower pulse duty cycle (0.1%) than traditional magnetron sputtering technology to obtain higher metal ionization rate (>50%) [6]. The high ionization rate makes it ionize a large number of high-energy metal ions during discharge, which helps to promote the diffusion of deposited particles on the coating surface and the repeated nucleation and recrystallization of nanocrystals, thus improving the uniformity and density of the coating surface [7]. The high- density plasma produced by HiPIMS impacts the substrate surface under bias voltage, which can clean the surface impurities and etch the substrate surface, so that the local epitaxial growth of the coating can be achieved, and the film / substrate bonding strength can be improved obviously. In addition, HiPIMS technology also has the advantages of good diffraction, low temperature deposition and adjustable internal stress [8]. However, there are still some defects such as easy arc striking and low deposition rate when the coating has poor conductivity, and the low deposition rate is the main reason limiting its industrial application. Mishra et al. [9] considered that the lower deposition rate of HiPIMS was related to the negative high potential cathode target which has certain desorption effect on ions. According to the Research Report of Christie et al. [10] during deposition sputtering, due to the low potential of the target, some metal cations (M+) with low kinetic energy near the target are absorbed by the cathode target with low potential, resulting in the decrease of the number of film-forming particles reaching the substrate surface, thus reducing the deposition rate of HiPIMS technology.
In order to make full use of the advantages of high power pulsed magnetron sputtering technology, the application range of HiPIMS technology is expanded. Many scholars began to combine HiPIMS technology with traditional PVD technology.
For example, HiPIMS technology was combined with arc ion plating, DC magnetron sputtering, pulsed DC magnetron sputtering and other technologies, and their respective technical advantages were given full play according to the principle of complementary advantages. Paulitsch et al. [11] prepared CrN/TiN multilayer films by combining high-power pulsed magnetron sputtering with unbalanced magnetron sputtering (UBMS). High ion density can be obtained at a lower deposition rate in plasma by HiPIMS, which makes up for the defect of serious hole phenomenon in unbalanced magnetron sputtering coating, improves the density of the coating, and improves the hardness of the coating from 12 GPa to 26 GPa. In addition, Paulitsch et al. [12] found that the addition of DC magnetron sputtering technology can greatly improve the deposition rate of the coating, while other properties are still equivalent to pure HiPIMS coating. This discovery will undoubtedly make up for the defect of low deposition rate of HiPIMS technology. In order to make full use of the advantages of DC pulsed magnetron sputtering, the researchers focused on the DC pulse technology. For example, Kang et al. [13] and Wang et al. [14] respectively deposited Cr-Al-Si-N and Cr-Si-N nanocomposite coatings by high- power pulsed (HiPIMS) and pulsed DC co magnetron sputtering, respectively. Finally, hard wear-resistant coatings with high hardness (29.4 GPa) or low wear rate (3.24 m3/(N·m)) were obtained. Compared wth HiPIMS technology, pulsed DC magnetron sputtering technology can provide a stable deposition rate for the coating, and can inhibit the accumulation of surface charges on the target and suppress the arc discharge phenomenon. The combination of these two preparation technologies is expected to produce high-quality coatings with excellent performance and adjustable composition.
-
-
RESEARCH STATUS OF TRANSITION METAL BORIDE
-
Research status of binary metal boride coating
At the beginning of the development of tool coating technology, transition metal boride and nitride coatings have attracted wide attention due to their high hardness and high wear resistance. ZrB2 and TiB2, as one of the ultra-high temperature ceramic materials, have high melting temperature (Tmelt >3040), good conductivity and corrosion resistance, which are widely used in the preparation of high-temperature structural materials and functional materials [15]. Parthasarathy et al. [16] established ZrB2, TiB2 and HfB2 material models, and evaluated the oxidation behavior of the models using existing thermodynamic data in the range of 1000~1800. It is found that when the deposition temperature exceeds 1400, boron gradually evaporates, and the oxidation rate is mainly limited by the columnar block spacing between MO2 oxides. Zhao Dan et al. [17] prepared ZrB2 coating on C/SiC surface by reaction sintering method, which provided good ablation protection for C/SiC composites. The whole preparation process of the coating was carried out in the high temperature environment of 1200~1600. The sintering resistance of the substrate was improved by oxidation of the coating to B2O3 and ZrO2 fusion layers. Because of its high hardness, ZrB2 coating can also be used as a protective coating on the surface of precision tools. In order to ensure the purity of the coating and reduce the doping of impurity elements in the coating, the ZrB2 coating is usually prepared by physical vapor deposition (PVD) in a
vacuum sealed environment. Samuelsson et al. [18] deposited ZrB2 coating on Si substrate by high power pulsed magnetron sputtering (HiPIMS). The variation of the micro properties and resistivity of the coating was discussed by changing the pulse repetition frequency, current and ionization degree while keeping the sputtering power of the target unchanged. The results show that the higher atomic mobility makes the coating show stronger (0001) texture, and it is found that the residual stress state in the coating can be changed by changing the ionization degree.
As a transition metal element of the same family as Zr, TiB2 and ZrB2 coatings have similar crystal structure and mechanical properties. Sanchez et al. [19] prepared a series of TiB2 coatings by DC magnetron sputtering. With the increase of coating density and compressive stress, the hardness of the coatings gradually increased, and finally reached 23 GPa. It is found that the oxygen pollution is serious in the low-density coating, which is mainly caused by the reaction of oxygen adsorbed on the surface of the coating to form TiO2. With the popularization of HiPIMS preparation technology, Nedfors et al. [20] sputtered TiB2 composite target with high power pulse magnetron sputtering technology, and successfully prepared superhard TiB2 coating with the highest hardness up to 49 GPa. Compared with pulsed DC, the high ionization rate of HiPIMS leads to the transition from polycrystalline structure to (001) textured nano columnar structure. With the decrease of pulse frequency, the increase of matrix ion flux leads to the increase of residual compressive stress and the density of coating structure, which makes the hardness of coating increase.
-
Research status of ZrB2 based boron nitride coating
Although ZrB2 coating has many excellent physical and chemical properties, the columnar crystal structure of (001) crystal plane in the coating is anisotropic, and transgranular fracture occurs easily under the action of complex external stress, resulting in low fracture toughness and bending strength of the coating. Therefore, it is necessary to toughen the coating. Element doping is one of the most effective and commonly used methods to improve the performance of coatings. At present, some scholars have incorporated non- metallic elements such as N, C, O, Si into ZrB2 coating to improve the mechanical properties of ZrB2 coating. In many toughening methods, doping N element into ZrB2 coating to form amorphous BN coated nanocrystalline nanocomposite structure can play a good toughening effect. Mitterer et al. [21] used reactive magnetron sputtering to prepare the Zr-B-N coating for the first time in 1991 and found that the performance of the Zr-B-N coating is similar to that of the Ti- B-N coating. The results show that a very wide weak intensity diffraction peak appears in the XRD spectrum after adding N element. The grain size is refined gradually with the increase of reaction gas flow rate, and then amorphous structure is formed, which makes the hardness of the coating decrease. The presence of amorphous BN phase also improves the transmittance of Zr-B-N coating, which can maintain good corrosion resistance and wear resistance of the coating, and improve the optical performance of the coating [22]. Zhang et al. [23] prepared Zr-B-N coatings on Si wafers and cemented carbide substrates using composite magnetron sputtering technology to change the target power of ZrB2. The results show that a large amount of amorphous BN phase easily hinders the crystallization of ZrB2 hard phase, and the hardness of the coating decreases rapidly to 16.1 GPa.
However, the toughness of the coating is improved. When the sputtering power is 0.6 kW, the critical load of the coating reaches the maximum value of 43.85 N, and it has good tribological properties. Different from ZrB2 doped N element, Yu et al. [24] explored the influence of different B content on the properties of Zr-B-N coating by doping B element into ZrN coating. The doping of B element makes the grain size decrease rapidly and inhibits the growth of nanocrystalline. Due to the different radii of different atoms, the B atoms added later are easy to dissolve into the original lattice, causing lattice distortion, which can play the role of solution strengthening, and the hardness of the coating reaches the maximum value of 29.3 GPa at 24 W. However, with the increase of B target power, the hardness decreases to 13.8 GPa. This is mainly due to the decrease of hard fcc- ZrN phase content and the increase of amorphous BN phase content in the coating.
In the aspect of multi-element doping of ZrB2 coating, Li et al. [25] enhanced the mechanical properties and thermal stability of the nanocomposite coating by adding NB into the Zr-B-N coating. Wu et al. [26] found that the toughness, wear resistance and heat resistance of ZrB2 coating can be improved by adding O and N elements to ZrB2 coating. When the N2 flow rate is 5%, the wear rate is the lowest (1.65 m3/(N·m)), but the hardness is only 15 GPa. After that, Wan et al. [27] found that the Zr-B-O-N coating was mainly composed of ZrO2 and Zr3N4 phases, showing a nanocomposite structure of nc-(ZrO2, Zr3N4) nanocrystals wrapped in a-(BN, B2O3) amorphous layer. With the increase of O2 flow ratio from 2% to 8%, the hardness of the coating decreases from 16.11 GPa to 10.37 GPa, which is mainly due to the transformation of ZrO2 crystal from hard face centered cubic structure to orthogonal structure.
-
-
SUMMARY AND PROSPECT
High power pulsed composite magnetron sputtering technology is one of the effective methods to prepare hard coatings, but the technology is still in development and needs further research and exploration. At the same time, the difficulty of low hardness of metal boron nitride coating caused by excessive content of amorphous BN phase has not been solved, and the research on ZrB2 based boron nitride coating at home and abroad is relatively small, which is still in the exploratory stage. It is belieed that with the further development of the research, the metal boride hard coating will have a broader application prospect in the fields of cutting tools, dies and aerospace.
REFERENCES
-
R. Yan, F. Chen, X.D. Chen, Y.D. Zhou, Technical development of CVD diamond film coated tools, J. Mechanical design and manufacturing engineering, 2016, pp. 11-15.
-
Q. He, J.M. Paiva, J. Kohlscheen, B.D. Beake, S.C. Veldhuis, An integrative approach to coating/carbide substrate design of CVD and PVD coated cutting tools during the machining of austenitic stainless steel, J. Ceramics International, 2020, pp. 5149-5158.
-
J. Zhao and Z. Liu, Influences of coating thickness on cutting temperature for dry hard turning Inconel 718 with PVD TiAlN coated carbide tools in initial tool wear stage, J. Journal of Manufacturing Processes, 2020, pp. 1155-1165.
-
T.G. Wang, J.J. Zhang, B. Yan, Latest Progress in Surface Modification of Cutting Tools with Coatings, J. Chinese Journal of Vacuum Science and Technology, 2017, pp. 727-738.
-
V. Kouznetsov, Karol Macák, J.M. Schneider, Ulf Helmersson, Ivan
Petrov, A novel pulsed magnetron sputter technique utilizing very high target power densities, J. Surface & Coatings Technology, 1999, pp. 290-293.
-
André Anders, Discharge physics of high power impulse magnetron sputtering, J. Surface and Coatings Technology, 2011, pp. S1-S9.
-
André Anders, André, A review comparing cathodic arcs and high power impulse magnetron sputtering (HiPIMS) , J. Surface & Coatings Technology, 2014, pp. 308-325.
-
K.A. Aissa, A. Achour, J. Camus, et al, Comparison of the structural properties and residual stress of AlN films deposited by dc magnetron sputtering and high power impulse magnetron sputtering at different working pressures, J. Thin Solid Films, 2014, pp. 264-267.
-
N. Brenning, C. Huo, D. Lundin, M.A. Raadu, C. Vitelaru, G.D. Stancu, Understanding deposition rate loss in high power impulse magnetron sputtering: I. Ionization-driven electric fields, J. Plasma Sources Science and Technology, 2012, pp. 025005.
-
D.J. Christie, Target material pathways model for high power pulsed magnetron sputtering, J. Journal of Vacuum Science & Technology A: Vacuum, Surfaces, and Films, 2005, p. 330.
-
J. Paulitsch, P.H. Mayrhofer, W.-D. Münz, M. Schenkel, Structure and mechanical properties of CrN/TiN multilayer coatings prepared by a combined HIPIMS/UBMS deposition technique, J. Thin Solid Films, 2008, pp. 1239-1244.
-
J. Paulitsch, M. Schenkel, A. Schintlmeister, H. Hutter, P.H. Mayrhofer, Low friction CrN/TiN multilayer coatings prepared by a hybrid high power impulse magnetron sputtering/DC magnetron sputtering deposition technique, J. Thin Solid Films, 2010, pp. 5553-5557.
-
M.S. Kang, T.G. Wang, J.H. Shin, R. Nowar, K.H. Kim, Synthesis and properties of Cr-Al-Si-N films deposited by hybrid coating system with high power impulse magnetron sputtering (HIPIMS) and DC pulse sputtering, J. Transactions of Nonferrous Metals Society of China, 2012, pp. 729-734.
-
T.G. Wang, Y. Dong, B.A. Gebrekidan, Y.M. Liu, Q.X. Fan, K.H. Kim, Microstructure and Properties of the Cr-Si-N Coatings Deposited by Combining High-Power Impulse Magnetron Sputtering (HiPIMS) and Pulsed DC Magnetron Sputtering, J. Acta Metallurgica Sinica(English Letters), 2017, pp. 688-696.
-
Y. Sun, X. Xiao, G. Chai, Microstructure, optical properties and thermal stability of ZrB2 and Zr-B-N thin films as high-temperature solar selective absorbers, J. Materials Express, 2014, pp. 205-212.
-
T.A. Parthasarathy, R.A. Rapp, M. Opeka, R.J. Kerans, Amodel for the oxidation of ZrB2, HfB2 and TiB2, J. Acta Materialia, 2007, pp. 5999- 6010.
-
D. Zhao, C.R. Zhang, Y.D. Zhang, S.A. Chen, H.F. HU, Reactive Preparation and Properties of ZrB2 Coating, J. Journal of inorganic materials, 2011, pp. 902-906.
-
M. Samuelsson, J. Jensen, U. Helmersson, L. Hultman, H. Högberg, ZrB2 thin films grown by high power impulse magnetron sputtering from a compound target, J. Thin Solid Films, 2012, pp. 163-167.
-
C.M.T. Sanchez, B.R. Plata, M.E.H. Maia da Costa, F.L. Freire, Titanium diboride thin films produced by dc-magnetron sputtering: Structural and mechanical properties, J. Surface and Coatings Technology, 2011, pp. 3698-3702.
-
N. Nedfors, A. Mockute, J. Palisaitis, Per O.Å. Persson, Lars-Åke Näslund, Johanna Rosen, Influence of pulse frequency and bias on microstructure and mechanical properties of TiB2 coatings deposited by high power impulse magnetron sputtering, J. Surface & Coatings Technology, 2016, pp. 203-210.
-
C. Mitterer, A. Übleis, R. Ebner, Sputter deposition of wear-resistant coatings within the system Zr-B-N, J. Materials science & Engineering A, 1991, pp. 670-675.
-
Kiryukhantsev Korneev PV, E.A. Levashov, Transparency Effect in Zr- B-N Coatings Obtained by Magnetron Sputtering of ZrB2 Target, J. Technical Physics Letters, 2020, pp. 179-181.
-
J.J. Zhao, T.G. Wang, B. Yan, Synthesis and Troblogical Properties of Zr-B-N Coatings by High Power Impulse and Pulsed DC Magnetron Sputtering, J. Chinese Journal of Vacuum Science and Technology, 2018, pp. 479-486.
-
L.H. Yu, Q. Zhao, B.Y. Ma, J.H. Ma, Effect of B target power on microstructure, mechanical properties and friction properties of ZrBN composite films, J. Materials Science and Engineering of Powder Metallurgy, 2013, pp. 748-753.
-
C. Li, L. Dong, J.G. Yu, Y.P. Yu, X.H. Sun, D.J. Li, Influence of sputtering power on structure and mechanical properties of Zr-B-Nb-N nanocomposite films, J. Journal of Tianjin Normal University (Natural Science Edition), 2016, pp. 13-18.
-
L.G. Wu, T.G. Wang, Y.Y. Guo, Z.B. Yang, Y.M. Liu, K.Y. Tang, Influence of Nitrogen Flow-rate on Tribological Behavior of Magnetron Sputtered Zr-B-O-N Coatings, J. Chinese Journal of Vacuum Science and Technology, 2018, pp. 894-900.
-
W.Y. Wan, T.G. Wang, Z.B. Yang, J.F. Zhang, D.Q. Meng, X. Hou, Tribological Properties of O-Doped Zr-B-N Coatings Grown by Pulsed Magnetron Sputtering, J. Chinese Journal of Vacuum Science and Technology, 2020, pp. 708-713.