
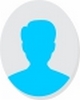
- Open Access
- Authors : Oguzhan Yavuz Bayraktar
- Paper ID : IJERTV9IS120175
- Volume & Issue : Volume 09, Issue 12 (December 2020)
- Published (First Online): 08-01-2021
- ISSN (Online) : 2278-0181
- Publisher Name : IJERT
- License:
This work is licensed under a Creative Commons Attribution 4.0 International License
Prefabricated Concrete and Waste Management
Oguzhan Yavuz Bayraktar*
Kastamonu University, Faculty of Engineering and Architecture, Department of Civil Engineering,
Kastamonu
Abstract:- The prefabricated concrete industry has reached a point by developing in the historical process. However, it is observed that this point of the sector is considerably behind when compared to the world average in terms of its share in the total construction sector. Concrete prefabrication, which is a form of industrial construction application, incorporates the characteristics of the industrial sector as well as the building sector. This feature has ensured that the sector is in constant relationship with the concept of quality and thus the concept of waste management in the development process of the sector. On the other hand, environmentally sensitive approaches that are developing around the world have started to find a place around the concept of sustainability within the framework of the construction sector, and the environmental nature of the building elements has become one of the important inputs of the design process.
Keywords: Environmental, Prefabricated concrete, Sustainable, Waste management
-
INTRODUCTION
In today's conditions where industrialization and technology are at the highest level, the previously unpredictable and uncalculated reflections of these two phenomena have begun to have a negative impact on the Earth. As a result of these developments, side effects on the environment posed an undeniable threat to the future of the earth. In the face of this threat, humanity has developed an automatic sensitivity to the environment in which it lives and has implemented various environmental protection activities. Technological development has shown its effects in the construction sector, and has taken its share from the positive and negative effects of these developments and changes, as well as other sectors. Many new industrial building materials have started to be included in the buildings and have been preferred and used by the construction sector managers with their superior and different features compared to traditional building materials. However, these new building materials, like all new industrial products, have emerged harmful to nature during production and application stages. As seen in all industrial sectors, in the face of environmentally harmful practices in the construction sector, the society has implemented environmental protection activities intensively within the framework of the definition of sustainability [1].
Shaping the building sector with the developing, changing industry and technology has started to expand the mass production system by developing both new building materials and new construction technologies especially after the Industrial Revolution. Although prefabrication attempts have been made by architects such as Le Corbusier, Walter Gropius and Auguste Perret after the Industrial Revolution, this system became widespread after the Second World War. The emergence of the Industrial Revolution did not influence how fast the world was able to keep up with concrete and cement manufacture in the world last stage of the production process. Although examples of prefabricated concrete buildings were found in the early years of the Republic, the first official structures using prefabrication technology were built in the early 1960s. Towards the end of the 1960s, prefabrication applications began to be used in the construction sector, especially in large-scale industrial buildings. However, in today's conditions, the prefabricated production system has not been able to achieve the same acceleration as the world by keeping up with the developing new technological applications. Made international and national research structures built with prefabricated systems, the proportion of all construction, according to the world's values, shows that far behind [2, 3].
-
PREFABRICATION CONCRETE
Construction activities outside the site; manufacturing, the product will be used outside the field where the product is produced by the method. As a result of the establishment of these types of production facilities and the development of assembly facilities, a construction system has many advantages compared to conventional production methods. This system is called prefabrication or precast production system [4].
Prefabricated production methods have been used in a wide range from the production of floor panels to high-rise building constructions for more than a hundred years, both for system installation and for the supply of only one part of the system. The importance of the prefabrication system shown in the Modern Methods of Construction has started to be perceived more and more in the mid-90s. These developments have been the result of the efforts of companies working on residential construction to combine light construction systems and manufacturing methods outside the construction site.
The first and most important example of standardization and mass production is the Crystal Palace building, established in London in 1850. In 1891, prefabricated reinforced concrete beams were used in a building in Biarritz, France, and in 1900, prefabricated reinforced concrete roof plates were applied for the first time in America. New Village In 1909, all components of an industrial building were realized with precast elements on the construction site. In the 1930s, prestressed prefabricated roof plates and beams were produced in Germany and prefabricated component housing was produced in Moscow. Prefabrication
developed rapidly in European countries such as France, Holland, Denmark and Russia to help solve the housing problem that emerged after the Second World War and the housing problem was easily overcome by standardization [5-7].
-
Prefabrication Concrete Classifications
Prefabricated building elements are basically divided into four according to the building material used. This building materials: [8]
-
Reinforced concrete
-
Steel
-
Wood
-
Mixed building materials are used in the systems. In the light of the structural system, prefabricated systems;
-
Rod – Systems formed with rod elements,
-
Systems formed with bar – panel elements,
-
Panel – Systems formed with panel elements,
-
Systems with cell elements.
-
-
-
MATERIAL AND METHODS
From large-scale constructions such as precast concrete elements, bridges and stadiums to modest residential constructions; Structural, decorative and infrastructure elements are applied extensively all over the world. Concrete prefabrication system is the most widely used prefabricated production technique in the world. Prefabricated concrete production plants produce 35 million tons of building elements annually. These products are mainly used in building constructions with the functions listed below: [9]
-
Residential constructions (especially floor plates)
-
Stadium construction
-
Art structures (roads, railways, bridges, waste water systems)
-
High-rise buildings
-
Hospital construction
-
Commercial and industrial plant constructions
Unlike other prefabricated production methods, the prefabricated concrete manufacturing system is based on the use of specially designed standard molds. Importance of standardization; As in hollow floor panels, it is possible to manufacture different projects by using the same mold by methods such as cutting the dimensioned elements according to the project in different cross-sections or adjusting the door dimensions in ready-made standard molds such as bridge beams. Increases in standardization and repetition of the elements lead to a reduction in the cost of the project by decreasing the mold and labor costs [10].
Like other prefabrication methods, concrete prefabrication; more efficient construction process, improved construction work program, better cost control and better quality product manufacturing. In addition, due to the structure of the production process, the concrete prefabrication system offers advantages such as reducing the amount of material consumption and reducing the amount of waste on the construction site.
The main advantages of the prefabricated concrete manufacturing system are summarized below: [11]
-
Industrialization is ensured by the use of standard and repeated elements.
-
Prefabricated production system saves material and energy and enables the structure to be opened to the operation in a faster time.
-
Geographical and topographic conditions are less effective than the conventional methods in the construction process of the building. Since the production and installation can be done without being affected by the seasonal conditions, the construction period is very short.
-
Production time is reduced thanks to the use of experienced labor and technological equipment and the advantages of mass production applications.
-
If desired, patterned and embroidered surfaces can be manufactured in a short time and economically as smooth surfaces.
-
Prefabrication is a system that guarantees to provide more quality conditions in the construction site compared to classical methods. Prefabricated elements can be subjected to a strict quality control and possible errors can be minimized.
-
Through the quality procedures of industrial plants, the basic raw materials used are subjected to various quality tests. In this way, the use of high-strength steel and cement is provided and high-strength reinforced concrete elements can be formed.
-
DISCUSSION
Manufacturing methods performed outside the construction site are becoming increasingly demanded in the construction sector. This manufacturing method; In addition to its advantages such as high construction quality, cost control and short manufacturing process, it is an environmentally sensitive method due to the nature of the system. As mentioned in the previous chapters, one of the most important advantages of the concrete prefabrication system is that it has the habit of manufacturing according to quality procedures since it is an industrial building system and thus incorporates waste management applications. In addition to this advantage, thanks to the properties of the prefabricated concrete production process, it is suitable to use the recycled material as raw material or to recover its waste [12-17]. Structural and decorative elements produced by concrete
prefabrication method, from railway sleepers to bridge construction elements; It has intensive usage opportunities in many areas from residential projects to stadium constructions [18].
It is a fact that the prefabricated production system contributes to the reduction of the amount of waste in the construction site by its nature. The Waste Reduction Action Program (WRAP) in the UK is a state-run environmental protection program in the UK. Research in the UK under WRAP has shown that the use of precast concrete products reduces the amount of waste on site by up to 50% compared to conventional constructions [19, 20]. The properties of precast concrete and prefabricated construction methods often enable manufacturers to standardize and thus, thanks to the special molds prepared previously, the possibility of producing an infinite number of building elements by only maintaining the molds. In addition, the prefabricated production process eliminates the need for scaffolding, formwork and formwork support systems in the construction site and prevents wastes, waste of time, health and safety problems that may arise as a result of the use of these methods [21].
Thanks to its features such as prefabricated concrete manufacturing technique, the external environment is not damaged due to climatic nature effects and there is no distance between the concrete batching plant and the production area; When compared with the productions to be made at the site, it provides a significant reduction in the amount of waste and waste material to be generated. Although most of the construction elements are made in a production facility outside the construction site, some productions must also be made at the construction site. These applications; basic production (in some cases also can be produced as prefabricated), the placement of prefabricated elements by crane, to connect the elements to each other in a way that can be transferred to the load of steel joints and special mortars and cavity fillings are limited. Due to the low level of productions on the construction site, the amount of waste generated at the site gives significantly lower values compared to conventional construction methods [22].
Prefabricated concrete production system is a simple and mature production method over time. This allows firms to concentrate their research and development (R & D) work and budgets on waste management and sustainable approaches.The prefabricated concrete manufacturing system permits the design of pre-stressed iron reinforcements and the amount of iron reinforcement to be used in the prefabricated concrete elements produced in this way is reduced. This can be considered as a waste management application to minimize the use of raw materials [23]. Within the scope of WRAP, the case study on Bison Concrete Products Limited (BISON), a high-tech prefabricated concrete production facility, has revealed the advantages of environmental and waste management of the off-site production applications in detail.
For example, it was calculated that less concrete and less steel were used in the hollow floor panels produced compared to floor plates produced by conventional methods. According to the floor design made according to the same aperture and load values, 63 m2 flooring can be produced with conventional construction system using 8 m³ concrete, while 808 m² can be produced from prefabricated hollow floor elements with the same amount of concrete. In addition to the savings in the use of the material in this way, the prefabricated hollow-floor system; is a system that simplifies manufacturing and assembly, eliminates expensive formwork and time-consuming floor formwork and reduces waste emission to almost zero [24].
-
CONCLUSION
With its 150 years of application history, prefabricated concrete construction system has reached equal production values with ready-mixed concrete production when the world average is considered. When these values are analyzed within the framework of our country, it is observed that the prefabricated concrete industry is far behind compared to conventional construction methods. However, prefabricated concrete production methods have advantages that can be preferred in many respects compared to conventional methods with both the positive features it contains and the potential of the production system structure.
Prefabricated concrete construction applications produce 50% less construction waste emissions compared to conventional systems. The main reasons for this situation; As prefabrication is an industrial construction method, the quality of the industrial sector is being implemented and therefore it is implementing waste management applications, requiring less amount of building materials during manufacturing and using these materials in a relatively controlled environment. Since prefabricated concrete production is a matured production system due to its long history, it can direct its resources on R & D, waste management and sustainable approaches. As stated in the thesis content, this type of R & D studies can enable many environmentally sensitive applications to be implemented in all processes from the project stage to the assembly stage. The prefabricated concrete building industry does not need temporary formwork, scaffolding, etc. equipments used in construction sites. Thus, environmental pollution, waste of time and safety problems resulting from the use of these equipments are eliminated.
-
REFERENCES
-
-
Chen, Y., Okudan, G. E., & Riley, D. R. (2010). Decision support for construction method selection in concrete buildings: Prefabrication adoption and optimization. Automation in Construction, 19(6), 665-675.
-
Brühwiler, E., & Denarié, E. (2008). Rehabilitation of concrete structures using ultra-high performance fibre reinforced concrete (No. CONF). University of Kassel.
-
Chen, Y., Okudan, G. E., & Riley, D. R. (2010). Sustainable performance criteria for construction method selection in concrete buildings. Automation in construction, 19(2), 235-244.
-
Ingrao, C., Giudice, A. L., Tricase, C., Mbohwa, C., & Rana, R. (2014). The use of basalt aggregates in the production of concrete for the prefabrication industry: environmental impact assessment, interpretation and improvement. Journal of Cleaner Production, 75, 195-204.
-
Jaillon, L., & Poon, C. S. (2008). Sustainable construction aspects of using prefabrication in dense urban environment: a Hong Kong case study. Construction management and Economics, 26(9), 953-966.
-
Pacheco-Torgal, F., & Jalali, S. (2010). Reusing ceramic wastes in concrete. Construction and Building Materials, 24(5), 832-838.
-
Lu, W., & Yuan, H. (2013). Investigating waste reduction potential in the upstream processes of offshore prefabrication construction. Renewable and Sustainable Energy Reviews, 28, 804-811.
-
Aguado, A., Caño, A. D., de la Cruz, M. P., Gomez, D., & Josa, A. (2011). Sustainability assessment of concrete structures within the Spanish structural concrete code. Journal of Construction Engineering and Management, 138(2), 268-276.
-
del Caño, A., Gómez, D., & de la Cruz, M. P. (2012). Uncertainty analysis in the sustainable design of concrete structures: A probabilistic method. Construction and Building Materials, 37, 865-873.
-
Lo, T. Y., & Cui, H. Z. (2004). Properties of green lightweight aggregate concrete. InternationalWokshopon Sustainable Development and Concrete Technology. Beijing, PRC, 113-118.
-
Den Hartog, E. (2008). Prefabrication of concrete shells.
-
Jaillon, L., Poon, C. S., & Chiang, Y. H. (2009). Quantifying the waste reduction potential of using prefabrication in building construction in Hong Kong. Waste management, 29(1), 309-320.
-
Kaplan, G., Gulcan, A., Cagdas, B., Bayraktar, O. Y. (2021). Impact of recycled coarse aggregates obtained from waste concretes on the lightweight pervious concrete properties. Environmental Science and Pollution Research, DOI: 10.1007/s11356-020-11881-y (In press)
-
Bayraktar, O.Y. (2021). Possibilities of disposing silica fume and waste glass powder, which are environmental wastes, by using as a substitute for portland cement. Environmental Science and Pollution Research, (In press)
-
Bayraktar, O.Y. (2019). The possibility of fly ash and blast furnace slag disposal by using these environmental wastes as substitutes in portland cement. Environmental monitoring and assessment, 191(9), 560. https://doi.org/10.1007/s10661-019-7741-4.
-
Bayraktar, O. Y., Saglam-Citoglu, G., Belgin, C. M., Cetin, S., & Cetin, M. (2019). Investigation of effect of brick dust and silica fume on the properties of portland cement mortar. Fresenius Environmental Bulletin, 28(11), 7823-7832.
-
Bayraktar, O. Y., Saglam-Citoglu, G., Belgin, C. M., & Cetin, M. (2019). Investigation of the mechanical properties of marble dust and silica fume substituted portland cement samples under high temperature effect. Fresenius Environmental Bulletin, 28(5), 38653875.
-
Lo, T. Y., Cui, H. Z., Nadeem, A., & Li, Z. G. (2006). The effects of air content on permeability of lightweight concrete. Cement and concrete research, 36(10), 1874-1878.
-
Huang, B., Wang, X., Kua, H., Geng, Y., Bleischwitz, R., & Ren, J. (2018). Construction and demolition waste management in China through the 3R principle. Resources, Conservation and Recycling, 129, 36-44.
-
Tam, V. W., Tam, C. M., Chan, J. K., & Ng, W. C. (2006). Cutting construction wastes by prefabrication. International Journal of Construction Management, 6(1), 15-25.
-
Tam, V. W. (2008). On the effectiveness in implementing a waste-management-plan method in construction. Waste management, 28(6), 1072-1080.
-
Cheng, J. C., Won, J., & Das, M. (2015, July). Construction and demolition waste management using BIM technology. In 23rd Ann. Conf. of the International Group for Lean Construction, Perth, Australia (pp. 381-390).
-
Li, Z., Shen, G. Q., & Alshawi, M. (2014). Measuring the impact of prefabrication on construction waste reduction: An empirical study in China. Resources, Conservation and Recycling, 91, 27-39.
-
Mokhtar, S. N., & Mahmood, N. Z. (2008, May). Approach in construction industry: A study on prefabrication method as a tool for waste minimization. In International Conference on Environmental Research and Technology (ICERT. 2008). doi (Vol. 10).