
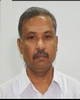
- Open Access
- Authors : N Lakshmana Swamy , B C Chudamani , Manjunatha
- Paper ID : IJERTV10IS010162
- Volume & Issue : Volume 10, Issue 01 (January 2021)
- Published (First Online): 27-01-2021
- ISSN (Online) : 2278-0181
- Publisher Name : IJERT
- License:
This work is licensed under a Creative Commons Attribution 4.0 International License
Three Body Abrasive Wear Studies on EN-8 Steel by Alumina – Zirconia – Fly Ash based Thermal Coating
N Lakshmana Swamy1, B C Chudamani2, Manjunatha3
1 Professor, Department of Mechanical Engg, University of Visvesvaraya College of Engg, Bangalore.
2 Research Scholar, Department of Mechanical Engineering, University of Visvesvaraya College of Engineering (UVCE) Bangalore, india
3 Assistant Professor, Department of Mechanical Engg, Vivekananda Institute of Technology, Bangalore.
Abstract:- An investigation was made to evaluate the effect of the incorporation of alumina, zirconia and in combination with fly ash on the abrasive wear behavior of EN8 steel. The wear behavior of plain EN8 steel and different particles like Alumina, Zirconia, and fly ash coatings studied systematically with respect to load, sliding speed. The wear volume loss increases with increasing load. However the specific wear rate decreases with thermal coating of Alumina, Zirconia and fly ash on EN8 steel. It is revealed that the better wear resistance of the EN8 steel by using thermal coating. It is also noted that weight loss increases with increase in load and speed. Meanwhile, the wear mechanisms of EN8 steel and with different coatings (like Al2O3, ZrO2, fly-ash) percentage is described and analyzed.
Key words: Three body abrasive rubber wheels, Alumina, zirconia, EN8steel, wear mechanism.
- INTRODUCTION
Three-body abrasive wear is defined as Wear triggered by free rolling and sliding of particles that are confined by two counter faces experiencing a relative sliding motion [1]. The particles involved in three-body abrasive wear could be generated by wear debris or have an external source such as sand and soot. The role of lubricant-borne debris and their deformation and fracture on three body abrasive wear was investigated in Ref. [2]. Three-body abrasive wear originated from the presence of soot particles in lubricated contacts is a key contributor to wear in diesel engines [3, 4]. Elevated operating temperatures, higher friction, and intensified wear rates in gears as a result of lubricant contamination were also investigated [5]. Reza Gheisari.et.al[6] reported on three body abrasive wear of hard coatings. They concluded that ratio of abrasive hardness to bearing surface plays an important role in three body abrasive situations. JG Alotaibi.et.al [7] studied the wear behavior and wear mechanism of different metals sliding against stainless steel counter face. They concluded that specific wear rate versus sliding distance is almost same for all metals sliding stainless steel. It is divided into two regions, running in and steady state. In the later the specific wear rate is almost steady with increase in sliding distance. Boachao zheng and Zhifa Hang [8].et.al studied the three body abrasive wear behavior of cementite with different chromium concentrations. They concluded that when Cr content less than 6.03wt% single phase cementite was obtained by MA and SPA and increase in Cr led to improve hardness and wear resistance. When Cr content less than 8.22%, Cr atoms are distributed in Cementite to form Cr-rich zones of more hardness. These zones reduces the pit dept and roughness and improves the cementite abrasive resistance.S.Das Bakshi, P.H.Shipway.et.al [9] reported on the three body abrasive wear of fine pearalite, nanostrured bainite, and marten site. They concluded that hardest phase marten site has greater wear rate, whereas Pearlite better resistance abrasion. It also concluded that bainite wears by combination of grooving and small minor pitting, whereas in marten site cutting mechanism is dominant. Kaihong zhang,Yamin gao[10] et.al studied the three body abrasive wear resistance of iron matrix composites reinforced with ceramic particles. They concluded that wear resistance of the composite is mainly related to the fracture strength and bending strength of ceramic particles.
The ZTA (55-60ZRO2) reinforced Cr25 composite exhibit good wear resistance which 6 times more than that of Cast iron matrix. A.A cenna and J.Doyle [11] et.al investigated on wear mechanisms in polymer matrix composites abraded by bulk solids. They concluded that the abrasive resistance of reinforced composite material is a micro- mechanisms process that occurs during abrasive wear. Which in turn, are strongly depend upon the hardness of wear media. Both two body and three body wear patterns are possible by bulk solids sliding across polymer matrix composites.Antoriao.et.al [12] studied on wear resistance and wear mechanism of WC-12%CO thermal sprayed coatings in threebody abrasion. They concluded that micro-polishing and gradual degradation of the lamellae was predominant wear mechanism in tests with SiO2 abrasives. The wear mechanism with Al2O3 abrasives was plastic deformation .A.P Harsha .and U.S Tiwari. [13].et.al reported on three body abrasive wear behavior of Polyaryle ether ketone composites. They concluded that abrasive wear rate is higher in composites than the neat matrix at different loads.
- EXPERIMENTAL DETAILS
-
- Materials:
In this experiment metal subtratate (EN8) plate of thickness 20mm thickness length 5m purchased from Surya steels and alloys Peenya industrial area Bangalore. The metal substrate is grinded with surface grinding machine to obtain surface
finish. The coating process is carried out in Spraymet surface technology limited Peenya, Bangalore. Coating materials like, Alumina, Zirconia, fly ash are coated on the metal substrate using plasma spray coating to get the thickness of 150 to 200 microns.
- EN8 Carbon Steel Grade Equivalents
Other steel grades in ASTM, DIN, JIS standards are similar and equivalent to EN8 steel, as follows:
BS 970-1991:080M40
AISI/ASTM A29:1038, 1040, 1045
DIN Werkstoff No.: 1.0511, 1.1186, 1.1189
- BS & DIN European: C40, CK40, C45, CK45
JIS G4051: S40C, S45C
EN8 steel having low tensile strength used for general Engineering purpose and production of lightly stressed components.
The material had properties like good wettability and much inability characteristics and has hard wearing surface.
Table.2.1 Mechanical properties of EN-8 steel
Tensile strength 430N/mm2 Yield strength 240 Elongation 18% Impact Izode J 39 Impact KCA J 35 Hardness 202 Table.2.2 Sample code designation
EN8before coating A1,A2,A3,A4,A5,A6,A7,A8,A9,A10,A11,A12,A13,A14,A15,A16 A18,A19,A20,A21,A22,A23,A24,A25,A26,A27 EN8 after coating B1,B2,B3,B4,B5,B6,B7,B8,B9,B10,B11,B12,B13,B14,B15,B17 B18,B19,B20,B21,B22,B23,B24,B25,B26,B27
- BS & DIN European: C40, CK40, C45, CK45
- Plasma spray coating and coating deposition:
- Materials:
Figure.2.1. Schematic diagram of Plasma spray coating.
It is process where molten or heated material on metal substrate to provide a coating. During the process the powder material is injected to higher temperature plasma flame where it is heated and subjected to high velocity. The higher temperature material impacted on the substrate and cools rapidly forming strong coating. The plasma spray coating sometimesalso called as cold process (relative to the substrate material being coated) as the subject temperatue can be kept lower during the process.
Table.2.3 Standard Process parameters used for Plasma spray coating
Sl.no Particulars Parameters Remarks 1 Spray Gun 3MB Plasma gun 2 Nozzle Pressure (psi) Flow rate (scfh) 3 Organ gas Pressure-100-120 80-90 4 Hydrogen gas Pressure 50psi 15-18 standard cubic feed per hour. 5 Current 500Amps 65-70V 6 Spray distance 2 to 3 inch 100mm 7 Power source 40KW Figure.2.3 shows the Optical microstructure of EN8 steel Figure.2.4 Shows the optical microstructure of EN8 steel after surface finish Before surface finish at500x Figure.2.5 Schematic diagram of abrasive material move mode during Wear process.
2.3 Abrasive wear test
Three body test were conducted as per the ASTM-G-65 standard conditions for measuring wear loss using rubber wheel test rig as shown in figure. The load applied was 39N, 59N and 79N and the time duration of 1, 2 and 3 min respectively as per the testing condition requirements. The rubber wheel diameter used is 228mm. Samples were weighed before and after test using the mass balance of accuracy 0.001kg and the weight loss is recorded. The schematic diagram used for wear test is shown in Figure.4
-
- Micro structure test results.
Figure.2.6 Schematic diagram of three body abrasive wear.
- Micro structure test results.
-
- RESULTS AND DISCUSSION
Figure.3.1 Micro structure of a test specimen.
The microstructure test is conducted by using Optical metallurgical micro scope. The test method used is IS: 7739 PART V -1976(RA 2007) ASM METALS HAND BOOK Vol.9. The final results conclude that Microstructure consists of fine grains of ferrite and pearlite. It is in normalized condition.
3.2 Scanning Electron Microscopy (SEM) test results. Figure.3.2 Test specimen Figure.3.3 Graphical representation of test results Table.3.1 Test results shows weight and atomic percentage of constituents
Element Weight % Atomic % C K 6.71 21.47 O K 8.08 19.40 SiK 0.75 1.02 CrK 0.38 0.28 MnK 0.78 0.54 FeK 82.95 57.05 NiK 0.35 0.23 Using scanning electron microscope (SEM) the electrons interact with atoms in the sample, producing various signals that contain information about the surface topography and composition of the sample. For the test specimen using electron beam is scanned in a raster scan pattern, and the position of the beam is combined with the intensity of the detected signal to produce an image. The SEM analysis is done for different EN8 steel specimen coated by Alumina Zirconia Fly Ash in various range(10µm, 20 µm, 50µm and 100µm). From the test it shows weight and atomic percentage of constituents various by by increasing the nano coating on test specimen. From the SEM investigation observed that ploughing mechanism is seen on the worn out surfaces with groves and voids.
- CONCLUSION
It is found that weight loss increases with increase in speed and load before and after coating. But wear performance is improved after coating as compared to before coating. It is also observed that wear performance is improved with lower speed and lower load as compared to higher load and higher speed. From the SEM investigation observed that ploughing mechanism is seen on the worn out surfaces with groves and voids.
REFERENCES
-
-
- Hutchings, P.shipway, Tribology: Friction and Wear of polymeric materials, Butt worth- Heinemann, 2017
- R.S. Dwyerjoyce, R.S. Sayles, E. Ioannides, An investigation into the mechanisms of closed 3-body abrasive wear, Wear 175 (1994) 133142, https://doi.org/10.1016/0043-1648(94)901767
- D.A. Green, R. Lewis, R.S. Dwyer-Joyce, Wear effects and mechanisms of soot contaminated automotive lubricants, Proc. Inst. Mech. Eng.
Part J J. Eng. Tribol.220 (2006) 159169 https://doi.org/10.1243/13506501JET140
- D.A. Green, R. Lewis, The effects of soot-contaminated engine oil on wear and friction: a review,Proc.Inst.Mech.Eng.PartDJ.Automobile.Eng.222(2008)166911689,https:/doe-org/10.1243/9544070JAUTO468.
- M.R. Sari, A. Haiahem, L. Flamand, Effect of lubricant contamination on gear wear, Tribol. Lett. 27 (2007) 119126, https://doi.org/10.1007/s11249-007-9215-z.
- Reza Gheisari, Andreas A. Polycarpou, Three-body abrasive wear of hard coatings: Effects of hardness and roughness, Thin solid films,666(2018)66-75.
- JG Alotaibi, BF Yousif and TF Yusaf, Wear behavior and mechanism of different metals sliding agains stainless steel counter face, Proc I Mech E Part J.J Engineering Tribology2014, Vol. 228(6) 692704.
- Baochao, zhifu Huang, Jiandong Xing, Three body Abrasive Wear behavior of cementite with different Chromium Concentrations, Tribology letter(2016) 61:13.
- S. DasBakshi P.H.Shipway H.K.D.H.Bhadeshia a, Three-body abrasive wear of fine pearlite, nanostructure bainite and martensite, Wear308(2013)4653.
- Kaihong zheng, Yimin Gao,Yefi Li, Three body abrasive wear resistance of iron matrix composites reinforced with ceramic particles, Institution of Mechanical engineers, 2014,vol-228(1), 3-10.
- A.A. Cenna , J. Doyle N.W. Page A. Beehag P. Dastoor, Wear mechanisms in polymer matrix composites abraded by bulk solids, Wear 240 _2000. 207214.
- Antonio Ce´sar Bozzi, Jose´ Daniel Biasoli de Mello, Wear resistance and wear mechanisms of WC12%Co thermal sprayed coatings in three-body abrasion, Wear 233235 _1999. 575587.
- A.P. Harshaa, U.S. Tewari, B. Venkatraman, Three-body abrasive wear behavior of polyaryletherketone composites, Wear 254 (2003) 680-692.
- Aigbodion Vs Hassan SB , Aguunsoya, Effect of bagasse ash reinforcement on the dry sliding wear behavior of polymer matrix composites, Materiales Des 2010:33:322-7.
- N. Krishnamurthy,M.S Prashanthareddy, H.P Raju, A study of Parameters Affecting wear resistance of Alumina and Yttria stabilized zirconia coating on Al-6061 subtrate, International scholarly research network, Vol-2012,Article ID 585892, 13pages.
- JG Alotaibi, BF Yousif and TF Yusaf, Wear behavior and mechanism of different metals sliding agains stainless steel counter face, Proc I Mech E Part J:J Engineering Tribology2014, Vol. 228(6) 692704.
- David culliton, Tonny Betts, improving Tribological properties of cast Al-Si Alloys Through Application of Wear resistant Thermal spray coatings,Technological university Dublin,journal of thermal spray technology vol-22,no-4 2013-491-501.
-