
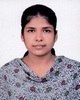
- Open Access
- Authors : Niharika Choubey , Neha Verma
- Paper ID : IJERTV10IS010153
- Volume & Issue : Volume 10, Issue 01 (January 2021)
- Published (First Online): 28-01-2021
- ISSN (Online) : 2278-0181
- Publisher Name : IJERT
- License:
This work is licensed under a Creative Commons Attribution 4.0 International License
Integration of Design of Experiment with Galvanization Process to Achieve Energy Efficient Sustainable Galvanization-A Review
Niharika Choubey
-
Tech student: Department of Mechanical Engineering SSIPMT, Raipur
Raipur, Chhattisgarh, India
Neha Verma
Assistant Professor: Department of Mechanical Engineering
SSIPMT, Raipur Raipur, Chhattisgarh, India
Abstract Galvanization is well famous & mostly used method to prevent steel or iron from corrosion especially when they are placed open to atmosphere & moisture containing environment. This is done by applying protective layer of zinc on steel or iron surface. Currently most of the galvanizing industries suffering from high zinc consumption & increase in cost due to excessive coating thickness of zinc. Industries also face increased energy consumption in galvanization and waste in the form of dross. To analyze & understand the zinc coating thickness influencing factors & their impact on coating and energy consumption, various research papers has been reviewed in this paper. There are statistical techniques such as design of experiment, which consist various methods like response surface method, factorial & Taguchi method is also studied in previous research work. Analysis of previous research work is discussed here as well as suggestions are made for future work to promote application of statistical tool to achieve environment friendly, energy efficient, sustainable galvanization & production system
Keywords Galvanization; zinc coating thickness ;energy consumption;energy savings; design of experiment, sustainable galvanization.
-
INTRODUCTION
Steel is a very popular & common material used by various industries such as construction, machinery, power transmission towers and handcrafts etc. Steels are more prone to corrosion when placed in open to atmosphere and enclosed with the moisture area. Protection and control from corrosion is essential requisite for industries to reduce chances of failure, unwanted damage as well as mechanical property damage. Hot dip batch galvanization is most popular and best suitable method to prevent steels and iron from corrosion as well as increases the life of materials. In galvanization process protective coating of zinc is applied on the surface of steel or iron. This is done on zinc pot in which iron or steel work material (such as iron angle) is immersed in to molten zinc, followed by various pre-processes of galvanization. Fig.1 shows galvanization process and its pre-process. This pre- process consist degreasing, pickling, rinsing, dipping in to flux solution and drying in to hot air dryer. After drying zinc coating is done in which zinc coating layer form on work material which is the major part of galvanization where proper attention is required. After galvanization quenching & dicromating is done.
Hot dip galvanization process is adopted by almost all type of industries where galvanization process is required in a batch. These industries are dealing with one of the major problem related with galvanization that is excessive zinc consumption, high zinc coating thickness than required & dross formation.
Fig.1. Galvanization process.
Excess zinc consumption increases production cost & too thick zinc coating causes rejection, rework & increases brittleness of coating layer that is undesirable from customers point of view. Also dross formation is hazardous as well as it contains zinc due to which large amount of zinc is wasted.
To optimize & analyze the root cause of the excessive coating, zinc consumption & dross formation, also to identify various influence factors that affects coating thickness many research work has been established. In this research work to understand concept of galvanization defects such as dross formation and investigating reasons of coating thickness & zinc consumption various research papers are reviewed. This literature survey not only focuses on zinc consumption, production cost reduction but also concern about energy consumption in galvanization process. The major objective of literature work is to adopt various statistical tools such as experimental design to optimize problems in industries and provide environment sustainable solution to promote industries toward energy savings and green production.
-
LITERATURE SURVEY
-
Galvanization coating thickness-Factors and their consequences
Henryk Kania, Jacek Mendala, Jarosaw Kozuba, and Mariola Saternus, (2020) reviewed various research papers to analyze the effects of various alloys that added into zinc bath to improve the coating characteristics, zinc consumption & waste minimization in galvanizing process. Authors elucidated positive & negative effect of these alloys, appropriate selection of chemical composition & also proper control on steel reactivity. Authors conclude that to achieve low production cost of zinc coating & high quality level it is necessary to select best suited chemical composition for zinc bath such as Al (aluminum), Ni (nickel), Bi (bismuth), Sn (tin) & Pb(lead) to control excessive coating thickness as well as reactivity of steels. Authors also suggested that development of technology for galvanizing process to enhance corrosion resistance as well as reduction in zinc consumption.
To protect & prevent steels from corrosion and other mechanical property losses, different techniques such as spraying; electroplating & hot dip galvanization are used. A A Hakim, T O Rajagukguk and S Sumardi, (2019) used hot dip galvanization method and conducts experiment to investigate effect of immersion time on low carbon steel hardness, coating thickness and microstructure and came to the conclusion that coating thickness increases with longer immersion time.
P. Saravanan and S Srikanth, (2018) reviews the common defects that originates from steel substrate, chemical cleaning, annealing furnace, zinc bath composition & dross formation in galvanized & galvannealed sheet products by metallographic techniques like SEM micrographs, energy-dispersive X-ray spectrometric (SEM-EDS) analyses & Electron probe microanalysis (EPMA); also dross particles come into zinc bath due to low Al level than required and high entry temperature. Authors conclude that high surface quality steels produced defect-free galvanized coating also these steels should be flat & smooth at microscopic level as well as mechanical damage free.
Galvanization process consist various process one of that is jigging i.e. loading materials in to loading table via wires. Shantanu Patel, Mr. Prashant khanna and Mr. K.D.Bhavsar, (2018) found that there is higher wire consumption for jigging. Jig cleaning is serious issue that increases cycle time. Here authors suggests Kaizen approach for continuous improvement and proposed idea of replacing wires with rod and claims that this will reduce cycle time of galvanization.
An experiment is conducted by the D. Kopycinski, E. Guzik and A. Szczesny, (2016) in which two parts casted with different methodologies to obtained two surface roughness parameters, to investigate the effect of surface roughness on protective coating on the ductile iron casting surface in hot dip galvanization process. Authors conclude that surface roughness has significant effect on coating thickness and coating thickness increase with high roughness parameter also with longer time of galvanizing treatment coating thickness increases with low roughness parameter.
There are different factors that affect galvanization coating hickness one of that is chemical composition of zinc bath that has an influence on coating thickness. Henryk Kania and Leszek Komorowski, (2016) conducted a test on sebisty steel with 0.18 wt % silicon content. There are 3 different alloys Zn-AlNi, Zn-AlNiPb and Zn-AlNiBiSn are used in zinc bath and corrosion resistance of coating obtained from these 3 alloys are compared with corrosion resistance of coating obtained from pure zinc bath. After conducting test authors found that alloy addition in zinc bath reduces coating thickness. AlNi and AlNiBiSn increases corrosion resistance of coating as compared to pure zinc bath coating and Zn- AlNiPb decreases coating thickness as doubled that AlNi and AlNiBiSn. Hence authors conclude that Pb (lead) addition into the bath decreases corrosion resistance of coating.
Sirli Sepper, Priidu Peetsalu, Priit Kulu, Mart Saarna, and Valdek Mikli, (2016) studied the influence of silicon in the hot dip galvanizing process. They prepared specimens by using centrifugal casting with different silicon concentration such as
<0.01, 0.06, 0.11, 0.17 & 0.30 all of these are in %. On the basis of experimental results they hypothesized that zinc solidifies on the steel surface & coating will grow in the contact surface of steel & solid zinc, they also claim that silicon affects the galvanizing reaction by zinc diffusion on steels & steel diffusion on coating. Higher Fe diffusion causes higher thickness of zinc coating.
Mr.Sanjeev Kumar and Satyendra Kumar Chaurasia, (2015) proposed idea of Mg (magnesium) addition in to zinc bath for galvanization to improve corrosion resistance of conventional hot dip galvanization process. Authors performed a coating simulation experiment on commercial quality cold rolled sheets. The galvanization process parameters are Mg level (0.25-0.75%), bath temperature (420- 460) & dipping time (2.0-4.0 sec). The coating thickness is measured after this experiment via defalsko coating thickness gauge. After conducting this experiment authors came to the results & conclude that addition of Mg ranges between 0.50- 0.75% and Sb (antimony) ~0.08% improves corrosion resistance property. Authors also addressing possibility to replace Pb with Sb which will help to overcome environmental issues related with Pb.
Shi-jun Huang, Hai-feng Zhu, Tian-wen Wang and Hao Chen, (2015) presents experimental analysis of different zinc coating thickness measurement methods. They compared the results of different measuring method and proposed most accurate and practical measuring method. Authors state that method of washing off outer coating layer was accurate & practical as well as Isoamyl acetate is the most suitable reagent in the washing process with very little effect on zinc coating.
Benu Chatterjee, (2014) reviewed various papers and presented various aspects of galvanization such as pre- treatment, process application, working parameters, metallurgical characteristics, coating thickness, corrosion resistance of coatings and cost & effect of operation and environment condition to improve existing galvanization technique.
It was found that in hot dip galvanization process excess zinc is consumed and coating thickness is irregular, this is due to indisciplined manual operation in zinc coating section. Akhil P Deote, Dr. M. M. Gupta and Prof. D. R. Zanwar, (2012) analyzed and identified the relationship between dependent & independent variable via regression analysis. This helped to identify the process parameters that affect the zinc coating thickness. Regression analysis help to understand how dependent variable changes when one independent variable is varied and another is fixed.
Process based cost analysis is done by the Sappinandana Akamphona, Sittha Sukkasi and Yuttanant Boonyongmaneerat, (2012) to analyze the economic feasibility of ICG (intermediate layer controlled galvanization)-electroplate & ICG-electroless galvanization process. ICG process are intermediate layer controlled galvanized process. Authors compared the traditional galvanization process with ICG-electroplates process and analyzed that ICG-electroplate is less costly regarding zinc price & pre coating thickness. ICG process having low production cost due to zinc consumption reduction & elimination of fluxing step by nickel pre coating.
Ya Liu, Xuping Su, Jianghua Wang and Zhi Li, Hao Tu, (2012) conducted an experiment to identify and analyze the combined effect of Al & Cr in zinc bath kettle for galvanization process. The effect of Al & Cr on the coating is analyzed with the help of SEM & EDS; diffusion path theory helps to evaluate the morphology of galvanization coating. Authors conclude that a new phase T1 formed when Al & Cr reached up to solubility limit in to molten zinc.
D. Kopycinski, (2010) evaluated and analyzed the growth & formation kinetics of zinc coating on the reactive silicon- killed steels & ductile steels with the help of power law growth equation. Author used technigalva zinc bath for the galvanization of the individual steel grades. This technique helps to reduce the effect of silicon and also avoid the excessive zinc coating thickness.
Soon-Bum Kwon1, Young-Doo Kwon, Sung-Jin Lee, Seung-Young Shin, and Geun-Young Kim, (2009) had compared the experimental value of impinging jet pressure on a surface of vertical strip, in gas wiping operation of hot dip galvanizing process; with results obtained by numerical analysis. Gas wiping method helps to control the film coating thickness and provide surety of uniform coating thickness of moving steel strip. Authors claim that a use of constant expansion rate nozzle rather than conventional nozzle helps to maintain uniform coating thickness of steel strip and saves energy.
Jalel Ben nasr, Ali Snoussi, Chedly Bradai and Foued Halouani, (2008) carried out an experiment by using a response surface methodology of a Doehlert design. The aim of this experiment to analyze the effect of 3 factors namely bath temperature, immersion time & withdrawal speed on zinc coating thickness. The work piece prepared for this was made by reactive steel. Authors state that by optimizing these 3 parameters zinc consumption in galvanization process can be minimized without adding any alloy in zinc bath.
Richard Fourmentin, Marie-Noelle Avettand-Fenoel, Guy Reumont and Pierre Perrot, (2008) conducted an experiment and optimization & calculation was done with help of thermo- calc software. The experimental parameters were system temperature 460 and pressure at 0.1 MPa. Authors prepared thermodynamic model by using Gibbs energy function of pure substance. Authors found that in galvanization process presence of Cr (chromium) eliminates inhibition layer formation.
Peng Bicao, Wang Jianhua, Su Xuping, Li Zhi and Yin Fucheng, (2007) carried out an experiment to study the influence of zinc bath temperature on coating thickness of galvanization process. Authors used pure iron sample whose temperature ranges between 450 to 500 and immersion time was 1, 2, 3, 5 & 8 min. SEM & EDS method was used to analyze the coating thickness of sample. Authors conclude that at 480 coating grows at fastest rate at the same time of immersion.
Saher Shawki and Z. Abdel Hamid, (2003) performed an experiment to study the effect of aluminum % in coating structure of galvanization process and dross formation. They used 5 to 90% Al content in zinc bath and came to the results. Authors found that when Al was less than 20% coating was under control & when Al was 35 to 90 % then process changes from galvanizing to aluminizing. There were two types of dross found. Authors claim that both are insoluble in zinc bath due to higher melting point within an operating temperature.
Hong Lin Liu and Ping Wu, (2000) studied the behavior of effective & non-effective additives in galvanization process by using density functional theory & cluster model. Authors optimized various factors such as total energy, electroic density, & electronic charge distribution of different additives. Authors proposed a mechanism of coating thickness formation due to the effect of additives addition. Also conclude that stronger bonding in effective additive and zinc restricts diffusion of zinc on Fe grain boundaries.
-
Design of Experiment (DOE)- A statistical approach in galvanization process
J. R. Smith and C. Larson, (2019) presented various statistical and experimental design tools such as full & fractional design, response surface method, Taguchi method, central composite design & different plots like Pareto chart and normal plot showed. Authors used 24 full factorial methods for coating thickness analysis in galvanization and provide comprehensive understanding about different DOE techniques.
Lucas Sonego Fernandes, Jose Demetrio Leite de Figueiredo, Oscar Olimpio de Araujo Filho and Edval Goncalves de Araujo, (2018) stated that increasing industrial competitiveness, advancement in globalization, creates high pressure to run a plant at low operational cost and also optimization of resources, forces industries to adopt statistical tools to improve process & product. Hence to analyze the coating thickness of galvanized wire, authors used factorial experiments with blocking method and conclude that using blocking with ANOVA (analysis of variance) analysis allows
nuisance factors to not disturb response. This increases productivity and competitiveness in industrial world.
Yi Wang, (2018) studied the influence factor such as air pressure, strip velocity & air-knife distance of air knife, which is the key apparatus to measure the coating thickness of zinc in galvanization process by using various experimental design methods. Author used response surface method, Taguchi method and genetic algorithm to optimize coating thickness. Author analyzed robustness by Taguchi method. He stated that air pressure & range of air knife are dispersion factor & position factor respectively. Response surface method & Taguchi method provide fitness function and genetic algorithm is a good tool that helps to identify optimal combination of parameter for coating thickness.
Sanjeev Kumar Shukla, Anup Kumar Sadhukhan and Parthapratim Gupta, (2017) used artificial neural network (ANN) model to predict galvanizing zinc coating thickness by developing an offline model. Sensitivity analysis is done on Taguchi Orthogonal Array technique. 6 factors are considered with the help of ANN model such that bath temperature, Al content, wiping gas flow rate, holding time, distance between nozzle & residence time. Authors conclude that ANN is a powerful tool to identify coating thickness.
Michal Peter, Gombar Miroslav, Vagaska Alena, Pitel Jan and Kmec Jan, (2013) performed an experiment on surface alloy EN 355 to examine thickness of acid zinc plating process. Authors developed a mathematical model with the help of DOE to obtain coating thickness. They select 6 factors to develop this model such that amount of zinc, Cl (chlorine), & boric acid (H3BO3), applied voltage, electrolyte temperature & zinc plating time. Authors claim that mathematical model helps to identify coating thickness as well as optimize operational cost of the process.
-
Energy efficient galvanization- An opportunity to achieve sutainability.
Guillermo Valenciaa, Erni Ramosa and Lourdes Merino, (2017) used energy management system & energy performance indicator to reduce the consumption of gases in hot dip galvanization process. The objective of the research is to reduce gas consumption, good manufacturing practices & production planning. This energy management method helps to reduce greenhouse gas emission & operational cost of the plant. Authors conclude that these methods also helped to identify energy consumption indicator and source of inefficiencies in overall process.
Jacek Szymczyk and Aldona Kluczek, (2017) identified that most industrial plants focuses on production cost, profit, efficient & continuous production but they ignore energy efficient production, pollution reduction & waste minimization or these are on second priority. Authors concerned on environmental sustainable & energy efficient production. They suggest energy efficiency improvement in terms of modern technological improvement. Authors confirmed that in galvanization process cogeneration is very effective to flow of energy as well as flame combustion is also used to achieve energy efficiency.
Senthil Sundaramoorthy, Quang Phuong, Bhaskaran Gopalakrishnan and Hasan H. Latif, (2015) used heat balance analysis to identify specific energy consumption in galvanization process and developed enhanced galvanizing energy profiler decision support system (E-GEPDSS) model. There are various factors whose influence on heat losses such as pot temperature, emissivity, and steel temperature at entry & exit etc. Authors found that this model provide potential energy efficiency opportunities, reduce energy losses and saves energy.
Subhasis Bhadra, Bhaskaran Gopalakrishnan and Subodh Chaudhari, (2013) presented a paper to analyze the different parameters of galvanizing line by using DSS (decision support system), this is called as GEPDSS for galvanization. Authors analyzed the energy consumption for both production time and down time. They suggested that a new pot hardware with increased life helps to achieve cost savings and study of potential energy. Authors state that by comparing result of DSS with actual electricity bill the effectiveness of GEPDSS system verified.
S G Blakey and S B M Beck, (2004) presented an energy efficiency method by using dimension less explicit equation, which is applicable for any type and size of furnace also for any type of fuel. Authors claim that increase in burner turndown to reduce energy consumption, deteriorated the thermal efficiency of furnace. Hence this dimensionless model and SEC(specific energy consumption) in terms of SECdemand and SECsupply to describe thermal efficiency, reduces dependencies on production rates and helps to reduce energy consumption in galvanizing as well as any other furnace.
-
-
ANALYSIS OF LITERATURE SURVEY
This literature survey is categorized in to 3 categories. First one is galvanization coating thickness factors and their consequences; second type is application of statistical approach such as design of experiment in galvanization and the third type is energy efficient galvanization to achieve sustainability. From literature survey the concept of design of experiment and energy efficient production, in terms of galvanization process studied thoroughly as well as analyzed the suggestion to overcome excess zinc coating thickness and their effects.
-
Root cause analysis
Analyzing literatures various problems are identified. The major problem which occurs in galvanization process is massive zinc consumption due to thick layer of zinc coating. This thick layer cause shows various effects in terms of cost, product quality, process capabilities and energy losses. To analyze root cause of this effects root cause analysis is done. The tool selected for this analysis is fishbone diagram. Fishbone diagram is also named as cause-effect diagram.
Fig.2 shows fishbone diagram for galvanization process. This diagram is divided in to 3 parts, effects, root cause of effects and causes of root cause. The long straight arrow in middle considered as fishbone that indicates towards root cause of effects that is excessive zinc coating thickness. There are various causes of excessive coating that is termed as
Fig.2. Fishbone diagram.
causes of root cause. These causes are comes from many sources that discussed below:
-
Zinc pot: – From examining literatures it is identified that the major cause of zinc thickness originates from zinc pot also called as zinc bath. The influencing factors are zinc bath temperature, immersion time, alloy addition and zinc bath chemitry etc. There are various literature work has been studied in review section regarding alloy addition, zinc bath chemistry and their effects.
-
Men: – Mostly hot dip batch galvanization is done manually. Lack of training, coordination and less skilled workers affects galvanization. This is due to because maintaining a standard working temperature with a required immersion time is difficult manually as well as lack of knowledge about how a minute delay in immersion time and improper temperature affects coating thickness.
-
Material: – The coating thickness varies due to reactivity of steel or iron work material, presence of silicon and also the size of work material.
-
Method: – Another problem arises from method of galvanization process. Lack of planning about dipping weight standard especially in case of dipping in to zinc pot where number of work material is to be standardized according to size, dimension and weight.
-
-
Effect analysis
A comprehensive study of root cause analysis regarding excess coating thickness provides its effects on galvanization process & product parameter. These effects are mentioned here in terms of cost, quality and energy:
-
Quality: – Quality of end product affected by thick coating which causes brittleness, which is unacceptable from customers. Rejection by customers causes need of
rework which creates obstacle in a smooth flow of production process.
-
Cost: – Increase in production cost, zinc consumption cost, due to excess zinc coating. There are dross formation in zinc pot occurs due to various chemical reactions. This dross contains zinc and a large amount of zinc is wasted via this dross. Rejection and rework process also increase cost and delays in various operations.
-
Energy: – High amount of energy is consumed due to excess coating as well as rejection and rework, in which high amount of energy is wasted. Generally in galvanization process electricity or gas like liquefied petroleum gas (LPG) is used, wastage of these non- renewable energy sources causes environment degradation.
-
-
-
DISCUSSION
This literature survey provides huge information regarding galvanization process. It imparts all important knowledge about galvanization process parameter. This survey helps to understand major issues with respect to galvanization. One the major problem is thickening of zinc coating layer, whose causes such as influencing factors & their effect, Zinc pot chemistry, alloy addition such as Ni, Al, Bi etc. and their impact on coating thickness, reactivity of steels and many other factors are identified with the help of root cause and effect analysis. Authors proposed various techniques such as ICG techniques, technigalva zinc bath etc. but the applicability of these techniques according to product and process for different galvanizing industry is needs to be analyzed.
There are some literatures in which statistical approach such as design of experiments and its techniques like Taguchi method, artificial neural network, response surface method etc. are used to predict coating thickness and their influencing
factors. This approach is an effective tool to analyze, interpret and improve the any process.
Fig.3. Integration of DOE with energy efficient galvanization process
Concerning about energy efficiency, planning and to reduce consumption of energy in galvanization few literature are found and reviewed. It is observed that heat balance analysis, GEPDSS (Galvanizing energy profiler decision support system) & energy management system techniques are used to reduce losses and energy savings.
-
RESEARCH GAP
There are many research work has been done to study on galvanization coating characteristics, coating layer formation, coating thickness influencing factors & their effects, but a suitable & statistical validation of remedial solution is absent.
There is only few research work has been established in terms of energy saving and adaptability of statistical tool DOE, even many literature having similarities in objectives and methodologies such as effects of alloy addition on coating thickness, zinc bath chemical composition and GEPDSS (Galvanizing energy profiler decision support system). Experimental design is also applied to analyze various factors but there is a gap that is a statistical validation of these factors and solution to reduce coating thickness & energy savings is required.
-
RESEARCH TO BE EXPLORED Integration of statistical tools such as design of experiment
with any process or in manufacturing process such as galvanization to achieve energy efficient sustainable galvanization process is an opportunity and new idea for future work. Fig.3 shows an idea of integration of DOE with energy efficient galvanization process.
It is found that statistical analysis & tools are required in manufacturing industries to achieve a good quality level for both product & process. To proof any result a validation is required that can be achieved with the help of various techniques such as experimental design that provides various methods like Taguchi method, response surface method & full factorial method etc.
All of these tools are required to be explored in practical problems which occur in industry. Application & exploration
of statistical tools should be in such a way that so any process can become energy efficient, produce sustainable products as well as provide statistically proofed solution to reduce various problems such as coating thickness reduction, energy savings in galvanization or any other type of process.
-
CONCLUSION
-
Considering the impact of excessive coating thickness of galvanization process on production cost, increased zinc consumption cost, brittleness of coating and excessive energy losses for galvanization in the form of LPG or electric energy; this review paper is presented. The principal objective of this review is to analyze & identify all the related parameters that cause energy consumption in galvanization & increases coating thickness. Also promotes the adaption of Statistical method, Design of experiment (DOE) for process & product improvement as well as energy savings. There are analysis of previous research work related with galvanization is discussed. Root cause analysis and effect analysis is also performed and future research that needs to be explored is also discussed. Being environmentally responsible to make defect free, energy efficient, pollution free & high quality level of production it is important to integrate various statistical approaches and tools with manufacturing process practically in industries.
REFERENCES
-
A A Hakim, T O Rajagukguk, and S Sumardi, The effect of immersion time to low carbon steel hardness and microstructure with hot dip galvanizing coating method, [Mineral Processing and Technology International Conference 2017, IOP Conf. Series: Materials Science and Engineering 285 (2017) 012019], doi:10.1088/1757-899X/285/1/012019
-
Akhil P Deote, Dr. M. M. Gupta and Prof. D. R. Zanwar, Process parameter optimization for zinc coating weight control in continuous galvanizing line, International Journal of Scientific and Engineering Research, Volume 3, Issue 11, November-2012, ISSN 2229-5518
-
Benu Chatterjee, Hot dip galvanizing, Eugen G. Leuze Verlag, Jahrbuch Oberfl achentechnik Band 70, 2014.
-
D. Kopycinski, The shaping of zinc coating on surface steels and ductile iron casting, Archives of Foundry Engineering, Volume 10, Issue Special1/2010 463-468, ISSN (1897-3310).
-
D. Kopycinski, E. Guzik and A. Szczesny, Effect of the surface layer of iron casting on the growth of protective coating during hot-dip galvanizing, Archives of Foundry Engineering, Volume 16, Issue 1/2016, ISSN (2299-2944), DOI: 10.1515/afe-2015-0097
-
Henryk Kania and Leszek Komorowski, The Influence of the chemical composition of a zinc bath upon corrosion resistance of coatings obtained on sebisty steel, Trans Tech Publications, Switzerland, 2016, ISSN: 1662-9779, Vol. 246, pp 85-90, doi:10.4028/www.scientific.net/SSP.246.85
-
Henryk Kania, Jacek Mendala, Jarosaw Kozuba and Mariola Saternus, Development of bath chemical composition for batch hot-dip galvanizingA Review, Materials 2020, 13, 4168; doi:10.3390/ma13184168
-
Hong Mei Jin, Yi Li, Hong Lin Liu and Ping Wu, Study on the behavior of additives in steel hot-dip galvanizing by DFT calculations, Chem. Mater. 2000, 12, 1879-1883,
-
J. R. Smith and C. Larson, Statistical approaches in surface finishing. Part 3. Design-of-experiments, Transaction of the IMF, 2019, VOL. 97, NO. 6, 289294, https://doi.org/10.1080/00202967.2019.1673530
-
Jacek Szymczyka and Aldona Kluczek, Increasing the energy efficiency of a hot-dip galvanizing plant and reducing its environmental impact, Journal of Power Technologies, 97 (5) (2017) 349358
-
Jalel Ben nasr, Ali Snoussi, Chedly Bradai and Foued Halouani, Optimization of hot-dip galvanizing process of reactive steels: Minimizing zinc consumption without alloy additions, Materials Letters, 62 (2008) 33283330, doi:10.1016/j.matlet.2008.02.067
-
Lucas Sonego Fernandes, Jose Demetrio Leite de Figueiredo, Oscar Olimpio de Araujo Filho, Edval Gonc and alves de Araujo, Blocking of factorial experiments in galvanized wire zinc weight test, Journal of Materials Research and Technology, https://doi.org/10.1016/j.jmrt.2017.10.009
-
Michal Peter, Gombar Miroslav, Vagaska Alena, Pitel Jan and Kmec Jan, Experimental study and modeling of the zinc coating thickness, Advanced Materials Research, Vols 712-715, (2013), pp 382-386, Trans Tech Publications, Switzerland, doi:10.4028/www.scientific.net/AMR.712-715.382
-
Mr.Sanjeev Kumar and Satyendra Kumar Chaurasia, Effect of Mg addition (in zinc bath) on galvanized sheet quality, International Journal of Scientific Engineering and Applied Science (IJSEAS),
Volume-1, Issue-4, July 2015, ISSN: 2395-3470
-
P. Saravanan and S Srikanth, Surface defects and their control in hot dip galvanized and galvannealed sheets, International Journal of Advanced Research in Chemical Science, Volume 5, Issue 11, 2018, PP 11-23, ISSN No. (Online) 2349-0403, DOI: http://dx.doi.org/10.20431/2349-0403.0511002
-
Peng Bicao, Wang Jianhua, Su Xuping, Li Zhi, and Yin Fucheng, Effects of zinc bath temperature on the coatings of hot-dip galvanizing, Surface and Coatings Technology, 202 (2008), 1785 1788, doi:10.1016/j.surfcoat.2007.07.044
-
Richard Fourmentin, Marie-Noelle, Avettand-Fenoel, Guy Reumont and Pierre Perro, The FeZnAlCr system and its impact on the galvanizing process in chromium-added zinc baths, J Mater Sci
,(2008), 43:68726880, DOI 10.1007/s10853-008-3011-5
-
S G Blakey and S B M Beck, Energy consumption and capacity utilization of galvanizing furnaces, Journal of Process Mechanical Engineering, 2004, DOI: 10.1243/0954408042466927
-
Saher Shawki and Z. Abdel Hamid, Effect of aluminium content on the coating structure and dross formation in the hot-dip galvanizing process, Surface and Interface Analysis. 2003; 35: 943947, DOI: 10.1002/sia.1608
-
Sanjeev Kumar Shukla, Anup Kumar Sadhukhan and Parthapratim Gupta, Development of ANN model for prediction of coating thickness in hot dip galvanizing process, International Journal of Materials Science and Engineering, Volume 5, Number 2, June 2017, doi: 10.17706/ijmse.2017.5.2.60-68
-
Sappinandana Akamphona, Sittha Sukkasi, and Yuttanant Boonyongmaneerat, Reduction of zinc consumption with enhanced corrosion protection in hot-dip galvanized coatings: A process-based cost analysis, Resources, Conservation and Recycling, 2012, doi:10.1016/j.resconrec.2011.10.001
-
Senthil Sundaramoorthy, Quang Phuong, Bhaskaran Gopalakrishnan, and Hasan H. Latif, Heat balance analysis of annealing furnaces and zinc pot in continuous hot dip galvanizing Lines, Energy Engineering, Vol. 113, No. 2, 2016, ISSN: 0199-8595 (Print) 1546-0118.
-
Shantanu Patel, Mr. Prashant khanna, and Mr. K.D.Bhavsar, Reduce the cycle time of galvanizing by applying Kaizen approach, International Journal for Research in Applied Science and Engineering Technology (IJRASET), Volume 6 Issue V, May 2018, ISSN: 2321- 9653.
-
Shi-jun Huang, Hai-feng Zhu, Tian-wen Wang and Hao Chen, Practical measuring method of thickness for zinc-coating in steel transmission towers, 3rd International Conference on Mechatronics, Robotics and Automation (ICMRA 2015).
-
Sirli Sepper, Priidu Peetsalu, Priit Kulu, Mart Saarna, and Valdek Mikli, The role of silicon in the hot dip galvanizing process, Proceedings of the Estonian Academy of Sciences, 2016, 65, 2, 159 165, doi: 10.3176/proc.2016.2.11
-
Soon-Bum Kwon, Young-Doo Kwon, Sung-Jin Lee, Seung-Young Shin, and Geun-Young Kim, Numerical analysis for the coating thickness prediction in continuous hot-dip galvanizing, Journal of Mechanical Science and Technology, 23 (2009) 3471~3478, DOI 10.1007/s12206-009-1008-x
-
Subhasis Bhadra, Bhaskaran Gopalakrishnan, and Subodh Chaudhari, Energy efficiency In continuous galvanizing Lines, International Renewable and Sustainable Energy conference (IRSEC), March 2013,
DOI: 10.1109/IRSEC.2013.6529723
-
Ya Liu, Xuping Su, Jianghua Wang, Zhi Li and Hao Tu, The hybrid effect of Al and Cr in zinc bath on galvanizing coatings, Advanced Materials Research, Vols 538-541 (2012) pp 306-310, Trans Tech Publications, Switzerland, doi:10.4028/www.scientific.net/AMR.538- 541.306
-
Yi Wang, Study on Influence Factors of zinc layer thickness via Response Surface Method, Taguchi Method and Genetic Algorithm, Industrial Engineering and Management, Wang, Ind Eng Manage 2018, 7:1, ISSN: 2169-0316, DOI: 10.4172/2169-0316.1000245
li>
Guillermo Valencia, Erni Ramos and Lourdes Merino, Energy planning for gas consumption reduction in a hot dip galvanizing plant, Chemical Engineering Transactions, VOL. 57, 2017, ISBN 978-88- 95608- 48-8, ISSN 2283-9216, DOI: 10.3303/CET1757117