
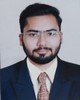
- Open Access
- Authors : Yash Gandhi , Dipam Modh , Nyee Kishan , Rajan Parmar, Nihar Panchal
- Paper ID : IJERTV10IS010198
- Volume & Issue : Volume 10, Issue 01 (January 2021)
- Published (First Online): 29-01-2021
- ISSN (Online) : 2278-0181
- Publisher Name : IJERT
- License:
This work is licensed under a Creative Commons Attribution 4.0 International License
Review Paper on Eddy Current and Electromagnetic Brake
Yash Gandhi¹ Dipam Modh²
Student Student
Department of Mechanical Engineering, Department of Mechanical Engineering, LDRP-ITR Gandhinagar, India. LDRP-ITR Gandhinagar, India.
Nyee Kishan3 Rajan Parmar4
Student Student
Department of Mechanical Engineering Department of Mechanical Engineering LDRP-ITR Gandhinagar, India. LDRP-ITR Gandhinagar, India.
Nihar Panchal5
Student
Department of Mechanical Engineering, LDRP-ITR Gandhinagar, India.
Abstract: – Most of the braking systems utilize friction forces to transform the kinetic energy of a moving body into heat that is dissipated by the braking pads. The overuse of friction-type braking systems causes the temperature of the braking pads to rise, reducing the effectiveness of the system. The eddy-current is created by the relative motion between a magnet and a metal (or alloy) conductor. The current induces the reverse magnetic field and results in the deceleration of motion. The changing magnetic field will induce eddy currents in the conductor. The proposed mechanism implements this phenomenon in developing a braking system. It is found that the larger thickness of disc, a greater number of turns of electromagnet and higher electrical conductivity of conductor influences the generation of greater braking torque. Greater the speed greater the efficiency.
Keywords: – Electromagnet, auxiliary brake, contact less braking, Friction, Eddy Current
INTRODUCTION
BRAKE
A brake is a mechanical device that inhibits motion by absorbing energy from a moving system. It is used for slowing or stopping a moving vehicle, wheel, axle, or to prevent its motion, most often accomplished by means of friction. Most brakes commonly use friction between two surfaces pressed together to convert the kinetic energy of the moving object into heat, though other methods of energy conversion may be employed.
BRAKING
Braking is the process of controlling the velocity of an object by inhibiting its motion. An object in motion possesses kinetic energy and to bring the object to a stop this kinetic energy must
be removed. Removing the kinetic energy can be accomplished by dissipating the energy to the atmosphere through friction or by converting into another form of energy. The most common
type of braking is a mechanical brake which inhibits motion through friction brake pads. A mechanical brake applies a
friction force to convert the kinetic energy of the vehicle into thermal energy which then dissipates into the atmosphere.
WORKING
Eddy current is the swirling current produced in a conductor which is subjected to change in magnetic field. Because of the tendency of the eddy current to oppose, it causes energy to be lost. It converts kinetic energy in to heat. These are simple magnetic devices that consists of non-ferromagnetic conductor that moves through a magnetic field. An example is shown in fig. where magnetic field is created in the gap of magnet with diameter =D When a conductive disc rotates eddy current is induced at a average distance R from axis of rotation.
Fig-1: Eddy current brake or magnetic brake
WORKING PRINCIPLE
it works according to faradays law of electromagnetic induction. According to this law whenever a conductor cuts magnetic lines of forces a emf is induced in it. Magnitude of EMF is proportional to strength of magnetic field and speed of the conductor. According to Lenzs law the direction of current is in such a way that it opposes movement of the disc. In magnetic brake by using strong magnet which are connected on lever and when we need to apply brake new can move the lever by moving the lever magnet also move and magnetic field is produce around the disc now this magnetic field is cut by rotor and the eddy current produce in disc which is oppose the movement of the disc and hence kinetic energy of rotor converted into heat disc is slow down and finally the disc is stop and wheels of vehicle are connected to disc and hence vehicle is stop. In electromagnetic brake by using armature coil we can set the armature coil near the rotating disc now when we need to stop or reduce the speed of disc or apply the brake we can flow the current in the wire due to flowing of current in wire the armature is act as a magnet and it is produce magnetic field and this magnetic field is cut by rotating disc now due to this action eddy current induce in the disc and which is oppose the movement of the disc here also kinetic energy is converted into the heat and finally the disc is stop and wheels of vehicle are connected to disc and hence the vehicle is stop.
Fig-2: Electromagnetic brake
LITERATURE REVIEW
Out team goes through various different review papers so we can know about other peoples work on different brakes. We find some very useful papers that are listed below.
-
Literature review on Design Study in Single Disk Axial Eddy Current Brake. 2018 5th International Conference on Electric Vehicular Technology (ICEVT) October 30-31, 2018, Surakarta, Indonesia.
In daily life the role of brake is very important. In generally vehicle is used conventional braking like disc brake drum brake etc. Eddy current brake can be alternative for conventional brake ECB is an electromagnetic brake which use the principle of eddy current brake. This research aim to investigate the relationship between braking torque with the amount of coil and the air gap in single disc axial brake ECB. FEM is used in ECB performance modelling. The eddy current brake has many parameters that need to be developed. In this paper by changing the air gap and number of conductors the torque is also changed. by using FEM, we can find this. The
braking torque is strongly affected by the parameter of eddy current brake. By result of this research we can conclude that smaller air gap increases the braking torque and also number of conductors is improving the performance of eddy current brake also by change in design the braking torque is also change. Better braking performance is obtain when using 0.5mm air gap and 360 conductors.
-
Literature review on Enhancement of Braking System in Automobile Using Electromagnetic Braking. Akshaya S. Putt war and Nagnath U. published in IOSR Journal of Mechanical and Civil Engineering (IOSR- JMCE), in 2009
Two main functions of a braking system are to maintain control of the car/vehicle at a vertiginous inclination or a declination and to stop the vehicle in the shortest distance possible. Electromagnetic brake is a new idea. Itis discovered that electromagnetic brakes can build up a power which is almost double the most extreme power yield of a normal motor, and no less than three times the braking energy of a fume brake to stop the vehicle. These results of electromagnetic brakes make them essentially more focused possibility for elective hindrance hardware's contrasted and different retarders. This project expects to limit the brake inability to stay away from the street mis happenings. It additionally diminishes the support of stopping mechanism. Preference for this mechanism is that it can be used in any vehicle and is less problematic. Mr. Akshaya S. Putt war and Nagnath U. Et al analyses that Electromagnetic braking system is found to be more reliable as compared to other braking systems. In oil braking system or air braking system even, a small leakage may lead to complete failure of brakes. While in electromagnetic braking system as four-disc plates, coils and firing circuits are attached individually on each wheel, even ny coil fails the brake does not completely fails remaining three coil works properly. This enhanced braking system not only helps in effective braking but also helps in avoiding the accidents and reducing the frequency of accidents to a minimum. the electromagnetic brakes can be used as an auxiliary braking system along with the friction braking system to avoid overheating and brake failure. ABS usage can be neglected by simply using a micro controlled electromagnetic disk brake system. When these brakes are combined with mechanical brakes, it increases the life of brake and act like fully loaded brakes. These electromagnetic brakes can be used in wet conditions which eliminate the anti-skidding equipment. Hence, the braking force produced in this is less than the disc brakes if can be used as a secondary or emergency braking system in the automobiles
-
Literature review on electromagnetic brake. Inventors: Lindberg; Teppo (Nuppulinna, FI) Assignee: Kone Oy (Helsinki, FI) United States Patent 5,186,286. Lindberg February 16, 1993
A vehicle braking system having a Brake disk structure defining an annular surface and having axis, annular magnet support assembly, an annular pole piece support assembly the system is an adjustment mechanism for producing relative angular movement between the magnet support and the pole
piece support assembly, so as to change the circumferential alignment between each of the pole pieces and the pair of permanent magnets adjacent there to. The invention is a vehicle braking system including a brake disk structure defining an annular surface means and having an axis, an annular magnet support assembly disposed adjacent to the annular surface means in the direction of the axis, a plurality of circumferentially spaced apart pairs of circumferentially spaced apart permanent magnets mounted on the magnet support and circumferentially spaced apart thereon, each pair Arranged with like polarities facing the annular surface means and the polarities of the pairs of permanent mag nets facing the annular surface means alternating circumferentially, an annular pole piece support assembly, and a plurality of ferromagnetic pole pieces mounted on the pole piece support assembly and circumferentially spaced apart in positions between the annular surface means and the permanent magnets, each pole piece disposed adjacent to a pair of the permanent magnets and having a circumferential length substantially greater than the circumferential length of either of the adjacent pair of permanent magnets. Also included in the system is an adjustment mechanism for producing relative angular movement between the magnet support and the pole piece support assembly so as to change the circumferential alignment between each of the pole pieces and the pair of permanent magnets adjacent thereto. Selective braking and non-braking periods are established by changing the alignment between the pole pieces and magnets. eddy braking can be used as a safety brake. Eddy braking also find application in high-speed vehicles as braking force is proportional to speed of vehicle.
-
Literature review on contactless eddy current brake for cars. United States Patent, US 6,286,637B1, Kwangju Institute of Science & Technology (KR): Sep. 11, 2001
A contactless eddy current brake for car is disclosed in the brake two cores are arranged the edge of the brake disc while being spaced apart from each other at an angle of 90 each of the cores is wound with a coil thus forming and electric magnet A control units calculates Dc or Ac control in response to a speed signal output from the sensor thus outputting control current value to the coils, while the AC current is variable in the frequency in accordance with the pedalling force As well known to those skilled in a art known contact brakes for cars are designed to be operated by hydraulic or pneumatic pressure thus pressing against the brake disc of a wheel using frictional brake pads are frictionally in that the brake pads and making a
car go slow or stop. However, such known contact brakes in are problematic in that the brake pads with the brake disc. Another problem experienced in the known brake the wheels while driving a car at high speed.
ADVANTAGES
-
No contact, therefore no wear or tear.
-
No noise or smell.
-
Adjustable brake force.
-
High brake forces at high speeds.
-
Also used as service brake.
-
It uses electromagnetic force and not friction Non- mechanical (no moving parts, no friction).
-
Can be activated at will via electrical signal
-
Low maintenance
-
Light weight
-
No grating misfortune.
-
Less warmth misfortune.
-
Less wear of segments.
-
Fully electronically controlled.
-
Great braking proficiency potential to recover vitality lost in braking.
-
Potential to recapture vitality lost in braking.
-
Potential danger of tire crumbling and blasts because of grinding is disposed of.
-
No need to change brake oils consistently.
-
No oil spillage.
-
Problem of brake liquid vaporization and solidifying is dispensed with.
-
Less support cost.
-
Longer life traverse contrasted with ordinary brakes.
-
Can be utilized as a part of industry to stop or decelerate turning parts.
-
MODELLING OF DIFFERENT COMPONENTS
Before making any machine, that is very important step to design that machine and decide dimensions of the components and decide weight of the whole machine. For the modelling of our Eddy Current and Electromagnetic Brake. we use SOLIDWORKS. Following are the images of that components which are we made in SOLIDWORKS.
.
-
Copper Disc 3.Small Pulley
-
Motor 4.Big pulley
.
-
Shaft
ASSEMBLY OF SYSTEM
-
copper coil
.
-
permanent magnet
FIGURE.1
-
Pillow block
-
CONCLUSION
An eddy current (magnetic)and electromagnetic braking mainly use to stop or slow down the heavy and high- speed vehicle like train etc. And also, for automobiles like hike, car has an effective braking system. In addition, by using the electromagnetic and magnetic brake, we can increase the life of the braking unit. The working principle of this system that when the eddy current (magnetic) and electromagnetic and flux cut by the rotating wheel or disc the eddy current is induce in rotating wheel or rotter. This eddy current flows opposite to the rotating wheel. This eddy current tries to stop the rotating wheel at rotor. This results in the rotating wheel or rotor comes to rest. The Electromagnetic braking system is found to be more reliable as compared to other braking systems. Electromagnetic braking system is found to be more reliable as compared to other braking systems. In friction or mechanical braking system or air baking system, even a small amount of leakage may lead to complete failure of brakes. By using combination of electromagnetic brake and eddy current (magnetic) brake we can overcome some drawback of electromagnetic brakes as well eddy current (magnetic) brakes like electromagnetic brakes are depended on battery power to energize the brake system. Because of that battery is drains down much faster. So here we use both magnetic and electromagnetic brake. In magnetic brakes in magnetic brakes there is no requirement of current. So by applying both we can produce desired amount of braking torque and also reduce the dependency on battery. Electromagnetic and eddy current (magnetic) braking is superior to conventional frictional braking as there is no friction and heat in electromagnetic braking. So, the conventional disc and drum brakes can be replaced with electromagnetic and magnetic brakes. In addition, it is found that, electromagnetic brakes make up approximately 80% of all of the power applied brake applications
REFERENCES
-
https://www.researchgate.net/publication/266246472_The_ design_of_eddy current_magnet_brakes
-
2018 5th International Conference on Electric Vehicular Technology (ICEVT)
-
Enhancement of Braking System in Automobile Using Electromagnetic Braking.
published in IOSR Journal of Mechanical and Civil Engineering (IOSR- JMCE), in 2009,
-
electromagnetic brake. United States Patent Date of Patent:
Feb. 16, 1993 Patent Number: 5,186,286
-
on contactless eddy current brake for cars. United States Patent, Date of Patent: Sep. 11, 2001, Patent No.: US 6,286,637B1,
-
https://www.google.com/url?sa=i&url=https%3A%2F%2F www.slideshare.net%2FNiteshPrasad9%2Felectromagnetic- braking-system-group- 14&psig=AOvVaw1zCMorR5uToVkiQizTQ9s&ust=16049 25864838000&source=images&cd=vfe&ved=0CAIQjRxqF woTCIipifb88uwCFQAAAAAdAAAAABAD