
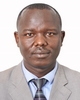
- Open Access
- Authors : Paul Christopher Kimali Kioko
- Paper ID : IJERTV10IS020018
- Volume & Issue : Volume 10, Issue 02 (February 2021)
- Published (First Online): 20-02-2021
- ISSN (Online) : 2278-0181
- Publisher Name : IJERT
- License:
This work is licensed under a Creative Commons Attribution 4.0 International License
Load-Deflection Behaviour Of Reinforced Concrete Slab Under Varied Axial Compressive Loading
Eng. Paul Christopher Kimali Kioko
Department of Civil Engineering,School of Engineering & Technology South Eastern Kenya University,Kitui-Kenya
Abstract:- This paper reports an experimental study on the behaviors and modes of failure of the test samples of two-way 125mm thick Reinforced Concrete Rectangular Slabs[1500mmx1000mm] with uniformly distributed load on along the centre-line of either axis plus a point load on the centroid.
Since this is destructive testing, only one loading was carried out for each slab making a total of three experiments.
Reinforced concrete slabs are used to form a variety of elements in building structures such as floors, roofs, staircases, foundations and some types of walls.
The major difference between slab and beams is that in slab design, the serviceability limit state of deflection is normally critical, rather than the ultimate limit states of bending and shear.
In many occasions, assumptions are made when partitions run along slabs as uniformly distributed loads without proper simulation of the actual behavior under the various load systems and this experiment sought to clarify the response given the types of load systems. The main variables were the compressive strength development after time periods of the concrete.Water cement ratio was 0.55 with concrete density being 2445Kg/m3 ,a slump of 8.2mm and compressive strength of 20N/mm2.
Loading was measured against deflection up to the point of failure and the test results recorded and graphs plotted. It was however, difficult to get strain gauges to determine strain variations in any direction for the experiment.
Finally, based on the results obtained, for the three load systems were compared based on transverse,longitudinal and on the point load
capacity and deflection of the slabs.
For the point load 5.3kN load produced a deflection of 252×10-6mm while for transverse loading 7.7kN produced a deflection of 224×10- 6mm and ultimately longitudinal loading 13.8kNproduced 221×10-6mm deflection.
Results showed that less load is required to produce high deflection with the trend reducing with the other systems of loading; that is, lesser load is required to produce similar load in the transverse direction than in the longitudinal direction.
INTRODUCTION
Reinforced concrete
CHAPTER 1
Fig.1.1 Philiphs Pavilion-Brussels(1958)
The novel shape of the Philips Pavilion was allowed by reinforced concrete.
Reinforced concrete is a composite material in which concrete's relatively low tensile strength and ductility are counteracted by the inclusion of reinforcement having higher tensile strength and/or ductility. The reinforcement is usually, though not necessarily, steel reinforcing bars (rebar) and is usually embedded passively in the concrete before it sets. Reinforcing schemes are generally designed to resist tensile stresses in particular regions of the concrete that might cause unacceptable cracking and/or structural
failure. Modern reinforced concrete can contain varied reinforcing materials made of steel, polymers or alternate composite material in conjunction with rebar or not. Reinforced concrete may also be permanently stressed (in compression), so as to improve the behaviour of the final structure under working loads. In the United States, the most common methods of doing this are known as pre-tensioning and post-tensioning.
For a strong, ductile and durable construction the reinforcement needs to have the following properties at least: High relative strength
High toleration of tensile strain
Good bond to the concrete, irrespective of pH, moisture, and similar factors
Thermal compatibility, not causing unacceptable stresses in response to changing temperatures. Durability in the concrete environment, irrespective of corrosion or sustained stress for example.
Use in construction
Fig.1.2
Rebars of Sagrada FamÃlia's roof in construction (2009) Behavior of reinforced concrete
Materials
Concrete is a mixture of coarse (stone or brick chips) and fine (generally sand or crushed stone) aggregates with a binder material (usually Portland cement). When mixed with a small amount of water, the cement hydrates to form microscopic opaque crystal lattices encapsulating and locking the aggregate into a rigid structure. Typical concrete mixes have high resistance to compressive stresses (about 4,000 psi (28 MPa)); however, any appreciable tension (e.g., due to bending) will break the microscopic rigid lattice, resulting in cracking and separation of the concrete. For this reason, typical non-reinforced concrete must be well supported to prevent the development of tension.
If a material with high strength in tension, such as steel, is placed in concrete, then the composite material, reinforced concrete, resists not only compression but also bending and other direct tensile actions. A reinforced concrete section where the concrete resists the compression and steel resists the tension can be made into almost any shape and size for the construction industry.
Key characteristics
Three physical characteristics give reinforced concrete its special properties:
the coefficient of thermal expansion of concrete is similar to that of steel, eliminating large internal stresses due to differences in thermal expansion or contraction.
when the cement paste within the concrete hardens, this conforms to the surface details of the steel, permitting any stress to be transmitted efficiently between the different materials. Usually steel bars are roughened or corrugated to further improve the bond or cohesion between the concrete and steel.
the alkaline chemical environment provided by the alkali reserve (KOH, NaOH) and the portlandite (calcium hydroxide) contained in the hardened cement paste causes a passivating film to form on the surface of the steel, making it much more resistant to corrosion than it would be in neutral or acidic conditions. When the cement paste exposed to the air and meteoric water reacts with the atmospheric CO2, portlandite and the Calcium Silicate Hydrate (CSH) of the hardened cement paste become progressively carbonated and the high pH gradually decreases from 13.5 12.5 to 8.5, the pH of water in equilibrium with calcite (calcium carbonate) and the steel is no longer passivated.
As a rule of thumb, only to give an idea on orders of magnitude, steel is protected at pH above ~11 but starts to corrode below
~10 depending on steel characteristics and local physico-chemical conditions when concrete becomes carbonated. Carbonatation of concrete along with chloride ingress are amongst the chief reasons for the failure of reinforcement bars in concrete.[3]
The relative cross-sectional area of steel required for typical reinforced concrete is usually quite small and varies from 1% for most beams and slabs to 6% for some columns. Reinforcing bars are normally round in cross-section and vary in diameter. Reinforced concrete structures sometimes have provisions such as ventilated hollow cores to control their moisture & humidity. Distribution of concrete (in spite of reinforcement) strength characteristics along the cross-section of vertical reinforced concrete elements is inhomogeneous.
Mechanism of composite action of reinforcement and concrete:
The reinforcement in a reinforced concrete (RC) structure, such as a steel bar, has to undergo the same strain or deformation as the surrounding concete in order to prevent discontinuity, slip or separation of the two materials under load. Maintaining composite action requires transfer of load between the concrete and steel. The direct stress is transferred from the concrete to the bar interface so as to change the tensile stress in the reinforcing bar along its length. This load transfer is achieved by means of bond (anchorage) and is idealized as a continuous stress field that develops in the vicinity of the steel-concrete interface.
OBJECTIVES AND SCOPE OF STUDY
The overall objective of the experiment is to ascertain the load/deflection behaviour of reinforced concrete slab under varied axial compressive load as tabulated above.
Experimental tests were performed to investigate the behaviour of the slabs designed in a similar way to testing for the axial compressive loads acting on the top face. The slabs were loaded axially by loading frame in the laboratory until failure point evidenced by the cracks formed along the slab. From the analyses the load-deflection relationships until failure, failure modes and crack patterns were obtained.
Research Hypothesis:
Varying loads induce varying deflections on the slabs (same model).
That is, less load for point load (case1), higher load for transverse loading(case2), and the highest loading for longitudinal loading(case3).
CHAPTER 2 LITERATURE REVIEW
Reinforced Concrete Slab (A Composite Material)
Basic design philosophy
Design in construction has seen rapid adoption in countries possessing the necessary standards and design guidance. Methods for evaluating fire resistance were proposed in the1980s in the form of specific national authorizations. Subsequently, the appearance of the Eurocodes has led to a significant generalization of design methods, not only for normal service conditions but also under fire.
The general philosophy adopted for the Eurocodes is to moderate the loads and forces applied to a structure by using factors. The values of these load factors depend on the nature, and variation with time, of particular types of load. Each member within a structure, and the structure as a whole, must be checked for all potential combinations of loads. In addition, particularly for beams, the designer must verify that certain criteria are satisfied under the levels of loading expected during service.
These criteria concern deflections, vibration, and cracking of the concrete, which are known as serviceability limit states. Eurocode 4 Part 1.1 (ENV 1994-1-1) gives design methods for composite beams and composite columns under normal conditions. Part 1.2(ENV 1994-1-2) gives methods for calculating the resistance of these elements under fire loading.
Eurocode 1 (ENV 1991) defines not only the loads to be considered during design, but also the safety factors to be considered under both normal conditions and fire. For an accidental fire condition the load factor is less than 1.0 for most imposed loads, because it is considered highly unlikely that an imposed load of maximum intensity would occur at the same time as a fire. These standards were completed in each country by a national application document for the Eurocode. Requirements for fire resistance also continue to be defined at a national level and, unfortunately, there is some disparity between different countries.
Quality of materials
Eurocode 4 permits the use of a wide range of steel and concrete grades for the materials combined in a composite member. The traditional range of steel grades (S235,
S275 and S355) is supplemented with higher strength grades S420 and S460. Steels of these higher grades are achieved using the Quenching and Self Tempering (QST) process high steel strengths (HISTAR sections), and are particularly useful for members subjected to substantial loads.
On the other hand, HISTAR steel grades allow a finishing without any preheating nor post heating during welding. Concrete should be either grade C20 till C50, with normal or lightweight aggregate. Any commonly available reinforcement may be used, S500 being the most common grade.
Common failure modes of steel reinforced concrete-
Reinforced concrete can fail due to inadequate strength, leading to mechanical failure, or due to a reduction in its durability. Corrosion and freeze/thaw cycles may damage poorly designed or constructed reinforced concrete. When rebar corrodes, the oxidation products (rust) expand and tends to flake, cracking the concrete and unbonding the rebar from the concrete. Typical mechanisms leading to durability problems are discussed below.
Mechanical failure
Cracking of the concrete section is nearly impossible to prevent; however, the size and location of cracks can be limited and controlled by appropriate reinforcement, control joints, curing methodology and concrete mix design. Cracking can allow moisture to penetrate and corrode the reinforcement. This is a serviceability failure in limit state design. Cracking is normally the result of an inadequate quantity of rebar, or rebar spaced at too great a distance. The concrete then cracks either under excess loading, or due to internal effects such as early thermal shrinkage when it cures.
Ultimate failure leading to collapse can be caused by crushing of the concrete, when compressive stresses exceed its strength; by yielding or failure of the rebar, when bending or shear stresses exceed the strength of the reinforcement; or by bond failure between the concrete and the rebar.
Carbonation
Fig.2.1 Concrete wall cracking(Wikipedia)
Concrete wall cracking as steel reinforcing corrodes and swells. Rust has a lower density than metal, so it expands as it forms, cracking the decorative cladding off the wall, as well as damaging the structural concrete. The breakage of material from the surface is called spalling.
Fig.2.2 Spalling(Wikipedia)
Detailed view of spalling. The apparently thin layer of concrete between the steel and the surface suggests, or similar problems of corrosion from external exposure
Carbonation:
Carbonatation, or neutralization, is a chemical reaction between carbon dioxide in the air with calcium hydroxide and hydrated calcium silicate in the concrete.
When designing a concrete structure, it is normal to state the concrete cover for the rebar (the depth within the object that the rebar will be). The minimum concrete cover is normally regulated by design or building codes. If the reinforcement is too close to the surface, early failure due to corrosion may occur. The concrete cover depth can be measured with a cover meter. However, carbonated concrete only becomes a durability problem when there is also sufficient moisture and oxygen to cause electro- potential corrosion of the reinforcing steel.
One method of testing a structure for carbonatation is to drill a fresh hole in the surface and then treat the cut surface with phenolphthalein indicator solution. This solution will turn [pink] when in contact with alkaline concrete, making it possible to see the depth of carbonatation. An existing hole is no good because the exposed surface will already be carbonated.
Chlorides
Chlorides, including sodium chloride, can promote the corrosion of embedded steel rebar if present in sufficiently high concentration. Chloride anions induce both localized corrosion (pitting corrosion) and generalized corrosion of steel reinforcements. For this reason, one should only use fresh raw water or potable water for mixing concrete, ensure that the coarse and fine aggregates do not contain chlorides, and not use admixtures that contain chlorides.
Fig.2.3 Rebar for foundations and walls of sewage pump station(Wikipedia).
Fig.2.4 Paulins Kill Viaduct
The Paulins Kill Viaduct, Hainesburg, New Jersey, is 115 feet (35 m) tall and 1,100 feet (335 m) long, and was heralded as the largest reinforced concrete structure in the world when it was completed in 1910 as part of the Lackawanna Cut-Off rail line project. The Lackawanna Railroad was a pioneer in the use of reinforced concrete.
It was once common for calcium chloride to be used as an admixture to promote rapid set-up of the concrete. It was also mistakenly believed that it would prevent freezing. However, this practice has fallen into disfavor once the deleterious effects of chlorides became known. It should be avoided whenever possible.
The use of de-icing salts on roadways, used to reduce the freezing point of water, is probably one of the primary causes of premature failure of reinforced or prestressed concrete bridge decks, roadways, and parking garages. The use of epoxy-coated reinforcing bars and the application of cathodic protection has mitigated this problem to some extent. Also, fibre glass reinforced panels (FRP) rebars are known to be less susceptible to chlorides. Properly designed concrete mixtures that have been allowed to cure properly are effectively impervious to the effects of deicers.
Another important source of chloride ion is from sea water. Sea water contains by weight approximately 3.5 wt.% salts. These salts include sodium chloride, magnesium sulfate, calcium sulfate, and bicarbonates. In water these salts dissociate in free ions (Na+, Mg2+, Cl-, SO42-, HCO3-) and migrate with the water into the capillaries of the concrete. Chloride ions are particularly aggressive for the corrosion of the carbon steel reinforcement bars and make up about 50% of these ions.
In the 1960s and 1970s it was also relatively common for Magnesite, a chloride rich carbonate mineral, to be used as a floor- topping material. This was done principally as a levelling and sound attenuating layer. However it is now known that when these materials came into contact with moisture it produced a weak solution of hydrochloric acid due to the presence of chlorides in the magnesite. Over a period of time (typically decades) the solution caused corrosion of the embedded steel rebars. This was most commonly found in wet areas or areas repeatedly exposed to moisture.
Alkali silica reaction
Main article: Alkali Silica Reaction
This a reaction of amorphous silica (chalcedony, chert, siliceous limestone) sometimes present in the aggregates with the hydroxyl ions (OH-) from the cement pore solution. Poorly crystallized silica (SiO2) dissolves and dissociates at high pH (12.5 – 13.5) in alkaline water. The soluble dissociated silicic acid reacts in the porewater with the calcium hydroxide (portlandite) present in the cement paste to form an expansive calcium silicate hydrate (CSH). The alkali silica reaction (ASR) causes localised swelling responsible for of tensile stress and cracking. The conditions required for alkali silica reaction are threefold: (1) aggregate containing an alkali-reactive constituent (amorphous silica), (2) sufficient availability of hydroxyl ions (OH-), and (3) sufficient moisture, above 75% relative humidity (RH) within the concrete. This phenomenon is sometimes popularly referred to as "concrete cancer". This reaction occurs independently of the presence of rebars: massive concrete structures such as dams can be affected.
Conversion of high alumina cement
Resistant to weak acids and especially sulfates, this cement cures quickly and reaches very high durability and strength. It was greatly used after World War II for making precast concrete objects. However, it can lose strength with heat or time (conversion), especially when not properly cured. With the collapse of three roofs made of prestressed concrete beams using high alumina cement, this cement was banned in the UK in 1976. Subsequent inquiries into the matter showed that the beams were improperly manufactured, but the ban remained.[10]
Sulphates
Sulfates (SO4) in the soil or in groundwater, in sufficient concentration, can react with the Portland cement in concrete causing the formation of expansive products, e.g. ettringite or thaumasite, which can lead to early failure of the structure. The most typical attack of this type is on concrete slabs and foundation walls at grade where the sulfate ion, via alternate wetting and drying, can increase in concentration. As the concentration increases, the attack on the Portland cement can begin. For buried structures such as pipe, this type of attack is much rarer especially in the Eastern half of the United States. The sulfate ion concentration increases much slower in the soil mass and is especially dependent upon the initial amount of sulfates in the native soil. The chemical analysis of soil borings should be done during the design phase of any project involving concrete in contact with the native soil to check for the presence of sulfates. If the concentrations are found to be aggressive, various protective coatings can be used. Also, in the US ASTM C150 Type 5 Portland cement can be used in the mix. This type of cement is designed to be particularly resistant to a sulfate attack.
MATERIAL CHARACTERISTICS IN THE CONCRETE MIX FOR SLAB
Aggregates
The aggregates used in concrete occupy about three-fourths of the concrete volume. Aggregates are considered for they increase volume of concrete; reduce shrinkage during setting of cement. Since they are less expansive than the cement, it is desirable to use as much of them as possible.
Aggregates Types
-
Fine aggregate(sand or gravel crushed fine stones upto 4.75mm size). Fine aggregates assist in cement paste to hold the coarse aggregate in suspension. Thus increasing plasticity of concrete and prevent segregation of coarse aggregate
from cement paste. Any aggregate that passes No. 4 sieve (which has wires spaced ¼ in. on centres in each direction) is said to be fine aggregate.
Coarse aggregate (crushed rocks size between 4.75mm -60mm). Materials of larger sizes to sieve No.4 are coarse aggregate. Are used mainly for increasing the volume of concrete and the density of the resulting mix. The physical, thermal and chemical properties of aggregate greatly affect the quality of concrete.
Both the fine aggregate (fine sand) and coarse aggregate (crushed stones) are used. The use of larger sizes lies with the discretion of the Engineer for workability and consolidation to avoid development of honeycomb or voids.
A good quality aggregate must exhibit the following qualities, clean, strong, and durability. Should dust or other particles be present, they may interfere with the bond between the cement paste and aggregate. The strength of the aggregate has an important effect on the strength of the concrete, and the aggregate properties greatly affect the concretes durability. (A. M. Neville (1995))
Water-cement ratio
This is the ratio water to cement, by weight, in the fresh concrete. In slab construction, the ratio is usually between 0.4-0.6, very high w/c ratio say 0.7-0.8 make poor concrete, with low strength and high shrinkage. Low ratio produce stiff mixes which are hard to place and compact because stiff mixes are also hard to finish, they often produce floor surfaces with poor flatness and low resistance to wear. If we go very much below 0.4 there is a risk that the mix will not contain enough water to hydrate the cement fully. In Britain on a damp autumn day, a mix with a w/c ratio of 0.45 might produce a fine concrete floor. (A. M. Neville (1995)) Cements
Cement is substance made from crushed rocks with burnt lime as binder; a substance that sets and hardens independently to bind together the aggregate materials of concrete. Cement used in construction is characterized as hydraulic or non-hydraulic. Hydraulic cement for this case Portland Cement harden because of hydration, chemical reaction that occur independently of the mixtures water content; they can even harden under water or when constantly exposed to wet weather. The chemical reaction that results when the anhydrous cement powder is mixed with water produces hydrates that are not water-soluble. Cement is used to produce mortar and concrete-the bonding of natural or artificial aggregates to form a strng building material that is durable in the natural environmental effects. (A. M. Neville (1995))
Water
Quality of water plays a very important role: impurities in water may interfere with the setting of the cement, may adversely affect the strength of the concrete or cause staining on its surface, and may also lead to corrosion of the reinforcement. Therefore, the suitability of water for mixing and curing purposes should be considered in design. Mixing water should not contain undesirable organic substances or inorganic constituents in excessive proportions. However, no standards explicitly prescribing the quality of water are available, partly because quantitative limits of harmful constituents are not known, mainly because unnecessary restrictions could be economically damaging. In many project specifications, the quality of water is covered by a clause saying that water should be fit for drinking. Such water very rarely contains dissolved inorganic solids. (A. M. Neville (1995))
Compatibility of concrete and steel
Concrete and steel in reinforcing works mutually acts together in reinforced concrete structures. The advantages of each material seem to compensate for the disadvantages of the other. For instance, the great shortcoming of concrete is its lack of tensile strength; but tensile strength is one of the great advantages of steel. And the compressive strength of steel is improved by concrete section. The two materials bond together very well so there is no slippage between the two, and thus they act together as a unit in resisting forces. The excellent bond obtained is due to chemical adhesion between the two materials, the natural roughness of the bars, and closely spaced rib-shaped deformations rolled on the bar surfaces. Reinforcing bars are subject to corrosion, but the concrete surrounding them provides them with excellent protection.
CHAPTER 3 METHODOLOGY
Provides important details of the methodology used including illustrative diagrams, sketches and photographs. Limitations, drawbacks or variations have been highlighted.
Test Specimens and Test Setup
A total of 3 specimens, were tested under longitudinal, transverse and point loads applied directly to the top of the concrete slab.
Specimens were tested after 28th day. Figure 3.7 shows typical test slab specimen. The concrete was class 20 prepared from the laboratory; batching done by weights.
Concrete was placed in preformed formwork and compacted using a poker vibrator. The averaged compressive strengths of each type of concrete, tested according to ASTM C39, were found to be 13, 16.5, and 18 MPa, respectively.
Figure 3.11 shows a schematic view and the picture of the test setup. Specimens were hoisted using the crane in the lab to the Loading Frame in the laboratory and the whole assembly fitted with load cells, LVDT and Data Logger electronic read-out. The axial compressive load was applied at the top, at the centre of gravity and along centre-lines on the x and y axes core as shown below.
One linear variable differential transducer (LVDT) was attached on the underside of the slab to monitor the deformation under the slab.
Fig.3.1 Three compartment mould Fig.3.2 Batching by weight
Fig.3.3 Vibrating of 1:2:4/20mm Agg. Fig.3.4 Hand Mixing of concrete
Fig.3.5 Collaborative work on tying steel reinforcment
Fig.3.6 Load cell on slab before testing Fig.3.7 Slab on steel fabric stiffened by timber studs
Fig.3.8 Hoisting and placing of the R.C. Slab Fig.3.9 Manoeuvring the slab in position
Fig.3.10 Deflection cracks upon loading Fig.3.11 Subsequent placing of next slab
Fig.3.12 Data logger for printing out / load deflection Fig.3.13 Soffit of slab and deflection upon loading
CHAPTER 4
DATA COLLECTION AND TESTS RESULTS
The first set of tests carried out was to ascertain the quality of concrete used in the construction of the slab; achieving the right compressive strength by mix design for normal concrete of C20. The second set of tests carried out was axial compressive strength of the control two way rectangular slabs (1500mmx1000mmx125mm-two way spanning and restrained on all sides. The conventional slab was fully designed and prepared in the usual way fully solid with 12mm diameter ribbed bars at 200mm centres and with 25mm cover distance.
The workability of the fresh concrete as determined through slump test was 8.2mm
Table # 4.1: Results of concrete slump
1st batch
2nd batch
Final reading
8.6
7.8
Initial reading
0
0
Slump (mm)
8.6
7.8
Compressive Strength Results
Average slump=8.6+7.8=8.2mm
2
Compressive strength tests are made to determine the strength of concrete at transfer of prestress or at the time of removal of formwork. This is normally carried out because of the intrinsic importance of the compressive strength of concrete in structural design.
For a W/C ratio of 0.55 to obtain a slump of 8mm, the compressive strength results for 7 day,14 day and 28 day are as tabulated below;
Results of concrete compressive strength
Days
Strength (N/mm2)
7
11.33
14
14.54
28
17.86
The main objective of this experimental study was to attain class 20 concrete with a slump of 8-10mm.
On the basis of experimental results obtained, it can be seen that the target strength was not attained after 28 days of curing the cubes. The strength increased steadily from 14.54N/mm2 on the 7th day to 17.86N/mm2 on the 28th day and this was only 87% of the desired 20N/mm2 strength where the W/C ratio was 0.55.
The graph following shows the relationship of compressive strength against the number of days it took to attain that strength for the cubes was as shown;
GRAPH OF COMPRESSIVE STRENGTH AGAINST TIME IN DAYS
25
COMPRESSIVE STRENGTH
(N/mm2)
COMPRESSIVE STRENGTH
(N/mm2)
20
15
10
5
0
0 5 10 15 20 25 30
TIME
(days)
Figure 4.1, Compressive Strength against Time
From the graph it can be seen the rate of increase of the compressive strength of cubes with time as the concrete ages.
DISCUSSION
The average density of the concrete used in the mix design was found to be 2445kg/m3. The compressive strengths of 150mm concrete cube were determined at the age of 7, 14, and 28 days. It is shown the compressive strength development of the normal concrete for a period of 28 days. The concrete shows a high rate of strength development at an early age (7days) with a reduction in rate of strength development as the concrete ages (28days). The rate of increase of strength in the first 7days is 2.24N/mm2 per day giving a compressive strength of 14.54N/mm2. The rate decreases to 0.52N/mm2 in the succeeding 7days and 0.17N/mm2 per day in the next 14days upto 28 day, giving 28day compressive strength of 17.86N/mm2
DEFLECTION ANALYSIS OF THE SLABS
The tables and graphs given below show the experimental results of the relationship between the axial compressive strength- deflection of the test specimens.
The raw data below is the result of the experiment employing a strain gauge of gauge factor 2.15, and a load measuring device of rated output 1.5 mV/V (3000 x 10-6) and with a capacity of 20 tonnes, all connected to a TDS 302 data logger (with the coefficient set to 1). Conversion of the raw data to actual strains and loads is tabulated below: –
Conversion of raw data
Raw strains are multiplied by 2/2.15
20
Raw load data are multiplied by
x1000x10
3000 1000
TEST SPECIMEN/SLB NO.1 ( POINT LOAD)
Raw strain data (x 10-6)
Actual strain (x 10-6)
Raw load data (x 10-6)
Actual load (KN)
0
0
0
0
101
94
26
1.7
173
161
35
2.3
223
207
43
2.9
254
236
48
3.2
267
248
55
3.7
283
263
72
4.8
277
258
77
5.1
293
273
78
5.2
282
262
79
5.3
271
252
79
5.3
6
5
4
3 Series1
Series2
2
1
0
0 50 100 150 200 250 300
Load in kN
Deflection x10-6
Graphical representation of the above results
TEST SPECIMEN/SLAB NO.2 ( UDL TRANSVERSE [X-X DIRECTION])
On Plan
1000mm
1500mm
1500mm
UDL
*UDL(Uniformly distributed load)
Raw strain data (x 10-6)
Actual strain (x 10-6)
Raw load data (x 10-6)
Actual load (KN)
0
0
0
0
27
25
11
1
75
70
25
2
108
101
34
2.3
124
115
43
3
117
109
76
5
177
165
98
6.5
241
224
113
7.5
241
224
116
7.7
9
8
7
6
5
4 Series1
3
2
1
Load in kN
0
0 50 100 150 200 250
Deflection x10-6
1500mm
1500mm
Raw strain data (x 10-6)
Actual strain (x 10-6)
Raw load data (x 10-6)
Actual load (KN)
0
0
0
0
24
22
137
9
69
64
147
9.8
121
113
155
10
185
172
171
11.4
238
221
207
13.8
Raw strain data (x 10-6)
Actual strain (x 10-6)
Raw load data (x 10-6)
Actual load (KN)
0
0
0
0
24
22
137
9
69
64
147
9.8
121
113
155
10
185
172
171
11.4
238
221
207
13.8
TEST SPECIMEN/SLAB NO.3 ( UDL LONGITUDINAL [Y-Y DIRECTION])
On Plan
1000mm
Load in kN
UDL
Series1
Series1
6
4
2
0
6
4
2
0
0
50
100
150
200
250
0
50
100
150
200
250
16
14
12
10
8
16
14
12
10
8
Deflection x10-6
CHAPTER 5:
OBSERVATION, ANALYSIS AND DISCUSSION
The analysis and the discussion for this report were made from the result shown from the tables and graph in chapter four above.
CONCLUSIONS AND RECOMMENDATIONS
This chapter presents the conclusions reached in this study. It also provides some recommendations for further studies. Conclusions:
These are the results of an experimental investigation on the performance of reinforced concrete slab with varying load system. Results showed that less load is required to produce high deflection with the trend reducing with the other systems of loading; that is, lesser load is required to produce similar load in the transverse direction than in the longitudinal direction.
RECOMMENDATIONS
The following recommendations can advance following the preceding observations: –
-
The study recommends that for design considerations, assumptions for bigger loading should be skewed to conform to the load systems and response as shown in the above results.
-
That this experiment confirms my hypothesis and forms a precedent consistent with existing concepts and theorems that attempt to predict the behavior envisaged as such.
-
That increased funding is key for thorough tests as lack of sufficient apparatus including the strain gauges limit the study on cracks and poisons ratio strains which, incidentally were not covered in this test research.
-
REFERENCES
-
A.M.Neville , Properties of concrete(2013),5th Edition
-
EuroCODES 1 to 4
-
Guofan Zhao, Dejuan Zhang, Chengkui Huang (1996). Study of earthquake resistant behavior of high strength concrete column reinforced with concrete filled steel tube. Journal of Dalian University of Technology 36:6, 759-766.
-
US ASTM C 150
-
Zhihui Huang, Lirong Cheng, JiaruQian, Liyan Lin (2001). Experimental study and finite element analysis on shear behavior of steel tube fill high strength concrete composite column core area. Industrial Construction 31:7, 50-53.