
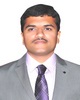
- Open Access
- Authors : Somanath Swamy R H M , Hiregoudar Yerrennagoudar , Mahesh G , B Basavaprakash
- Paper ID : IJERTV10IS020229
- Volume & Issue : Volume 10, Issue 02 (February 2021)
- Published (First Online): 02-03-2021
- ISSN (Online) : 2278-0181
- Publisher Name : IJERT
- License:
This work is licensed under a Creative Commons Attribution 4.0 International License
Swirl Type Retrofit CFD Simulation to Study Turbulent Kinetic Energy at Different Crank Angles
1Somanath Swamy R H M
Assistant Professor, Dept. of Mechanical Engg.
RYM Engineering College Ballari, Karnataka, India
3Mahesh G
Assistant Professor, Dept. of Mechanical Engg.
RYM Engineering College Ballari, Karnataka, India
2Hiregoudar Yerrennagoudar
Professor, Dept. of Mechanical Engg.
RYM Engineering College Ballari, Karnataka, India
4B Basava Prakash
Assistant Professor, Dept. of Mechanical Engg.
RYM Engineering College Ballari, Karnataka, India
Abstract Diesel engines are widely used because of its advantages like better efficiency over petrol engines. But toxic emissions released from these engines are made engineers to think about reducing it by various methods. Altering the spray pattern is one of the methods with which better air-fuel mixture can be obtained. Better air-fuel mixture leads to complete combustion which influences in reducing emissions. In order to achieve this a swirl type retrofit was designed and simulation was carried out using FLUENT software to study its turbulent kinetic energy at different crank angles.
Keywords Fuel spray, retrofit, turbulent kinetic energy
-
INTRODUCTION
The diesel engines are an important topic for researchers, due to the number of articles available which are concentrated mainly to improve efficiency and to reduce emissions. A number of research studies are underway to reduce emissions, especially those from cars and trucks. Many airborne diseases are caused by emissions from these engines. Fuel injected into the engine plays a key role in the efficiency of the engine. Examples of fuel injectors with different number of holes or sizes of nozzle holes with varying diameters. However, if the number of holes increases, this will increase fuel consumption and allow more fuel to be consumed at a higher rate. Spray characteristics play important role in air-fuel mixture. In the present work CFD simulation was carried out with a swirl type retrofit which was designed using SOLID EDGE V19 software and simulated with FLUENT software to study its turbulent kinetic energy at different crank angles.
-
CFD SIMULATION
-
Mesh Model
Mesh details for without retrofit
Mesh details for with retrofit
Mesh – Hexa
Mesh – Hexa
Element size 0.5mm
Element size 0.5mm
No. of Nodes 574039
No. of Nodes 489880
No. of Elements – 786010
No. of Elements 1122368
Fig. 1 shows mesh model for without retrofit
Fig. 2 shows mesh model for with retrofit
-
FLUENT solver setup
Solver
Pressure based
Time
Transient
Material
Diesel-Air mixture
Density
830 kg/m^3
Turbulence Model
K-Epsilon, RNG and standard wall function
Injection Model
Species and DPM modelling
Combustion Model
Volumetric reaction with finite rate combustion
Fuel injector
Cone type injection with 210 bar
Boundary conditions
Piston-bowl-wall, Top-head-wall
Initialization
Standard initialization
-
-
TURBULENT KINETIC ENERGY PLOTS (TKE)
Fig. 3 shows TKE at 337 crank angle without retrofit
Fig. 4 shows TKE at 337 crank angle with retrofit
Fig. 5 shows TKE at 345 crank angle without retrofit
Fig. 6 shows TKE at 345 crank angle with retrofit
-
RESULTS AND DISCUSSION
Turbulent kinetic energy shows the turbulence created inside the combustion chamber. Using FLUET tool simulation was carried out at two different crank angles 337 and 345. Crank angle 337 is the angle during which fuel not injected and 345 crank angles is the crank angle at which fuel was injected and combustion started. From the plots it was observed that at both the crank angles TKE value is more for with retrofit model when compared with without retrofit model. This proves that more turbulence is created in the cylinder leading to more proper air-fuel mixture. Complete combustion can be achieved with this and emissions can be reduced.
REFERENCES
-
Somanath Swamy R H M, Hiregoudar Yerrennagoudar, Mahesh G, Performance and emissions characteristics of CI engine with modification in fuel injector, IJEAT, Vol 9, issue 3, Feb 2020
-
H.H. Chiu, Advances and Challenges in Droplet and Spray Combustion, Progress in Energy and Combustion Sciences. Vol 26, pp. 381-416 2000.
-
Randall T. Imaoka, William A. Sirignano, Vaporization and combustion in three-dimensional droplet arrays, Proceedings of the Combustion Institute, Volume 30, Issue 2, pp. 19811989, January 2005.
-
Anand Kumar. T, J. M. Mallikarjuna and V. Ganesan, Effect of Intake PortConfiguration and Engine Speed on Flow Field Characteristics in a Four- Stroke Gasoline Engine CFD Approach Using KIVA-3V Code, Published in the Proceedings of National Conference on I.C Engines and Combustion, Annamalai University, Chidambaram, Tamil Nadu, INDIA, pp. 195-199, December 21-23, 2005.