
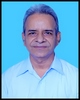
- Open Access
- Authors : Kalpana Vajpayee , Ashutosh Bajpai
- Paper ID : IJERTV10IS020244
- Volume & Issue : Volume 10, Issue 02 (February 2021)
- Published (First Online): 04-03-2021
- ISSN (Online) : 2278-0181
- Publisher Name : IJERT
- License:
This work is licensed under a Creative Commons Attribution 4.0 International License
Corrosion & Its Impact on Sugar Quality in Cane Sugar Industry
Kalpana Vajpayee1 &
Associate Professor, Department of Chemistry
D.A.V. Collage, Kanpur
Ashutosh Bajpai2
Professor Sugar Technology, National Sugar Institute, Kanpur
Abstract:- In sugar industry, Corrosion of process equipments not only causes increased expenditure on replacing worn out equipments but also adversely affects the clarification process owing to higher colour development due to reaction between iron and polyphenols. Experiments carried out in the Experimental Sugar Factory of the institute indicate mild to severe corrosion of mild steel in process liquors at different stages and a positive correlation between colour development and iron content of the process liquors.
INTRODUCTION
The menace of corrosion in sugar industry contributes significantly towards the national loss. With the growth and development of Indian sugar industry (at present 530 vacuum pan operating sugar factories and thousands of mini sugar plants, popularly known as Khandsari Sugar Units) and in the absence of serious efforts to prevent corrosion, the losses owing to corrosion, dry or wet, incurred by the Indian Sugar Industry alone are estimated to be more than Rs. 500 million per annum. In a sugar factory most of the process equipments are operated at elevated temperature, higher hydrostatic head, higher flow or circulation rates and either in acidic or alkaline medium. Due to continuous use under such operating conditions the wear of equipments increase gradually due to corrosion and erosion and after some time it becomes essential to replace it so as to avoid any mishap, break down and consequential losses. Further, since iron content of the process liquors, besides certain other factors, is very much dependent upon the corrosion rates at various stages, higher corrosion rates due to one or other reasons, may enhance colour development owing to its reaction with polyphenols present in the process liquors.
The present study has been carried out with a view to ascertain corrosion of mild steel at various stages of processing and also to determine possible quantitative relationship between iron content of the process liquors and colour developments during manufacture of sugar by Double Sulphitation process
REVIEW OF LITERATURE
In advanced countries (1,2) efforts have been made to identify the causes of corrosion and steps have been taken to minimize it through research and development. However, in developing countries like India, due importance has not yet been given to control it in proportion to the magnitude of the problem.
Like many other chemical and food processing industries, sugar industry also encounter the problem of corrosion. Many equipment or their parts wear out under operating conditions and necessitate frequent replacement. Scientists from various countries (3-7) have reported the corrosion problem station wise in cane sugar manufacture & suggested few preventive measures also. Vysolcova et.al8 & Kukota et.al9 in their study found that corrosion resistance of various equipments can be improved by applying various protective coatings.
In an interesting study Sethi et.al10 found a definite relationship between colour value & iron content in a given grade of sugar manufactured by Double Carbonation & Double Sulphitation process.
MATERIAL & METHODS
Preparation of Specimens
Rectangular samples of mild steel were cut to identical size and drilled at the centre of the upper edge so as to have suspension holes of I mm diameter. Final surface treatment included finishing with 0, 00 & 000 grade emery papers. These specimens were abraded first in the lengthwise direction, then across the width & finally using a circular motion. The specimens were wiped with cotton soaked in acetone and dried.
Experimental
The experiment was carried out in the experimental sugar factory of the institute to ascertain rate of corrosion of mild steel at various stages & to determine iron content and colour values of process liquors at various stages of processing. In the process
composite samples of mixed juice, clear juice, filtered juice, unsulphured syrup, sulphured syrup and final molasses were analyzed.
For determining intensity of corrosion at various stages, three specimens of mild steel were exposed for 72 hours in relevant process liquors. Prior to weighment of specimens after exposure they were rinsed for few seconds in running cold water & the adherent corrosion products removed by hard brushing & immersing in distilled water.
Analysis of Process Liquors
The composite samples of relevant process liquors were analyzed using AR grade chemicals of Merck/Ranbaxy and A- Class glassware of Borsoil/Vensil make. The process liquors were analyzed for various parameters as per the prescribed procedures of ICUMSA ( International commission for Uniform methods of Sugar analysis), UV-VIS spectrophotometer ( model UV-2600), electronic weighing balance & microprocessor based digital temperature & Do analysis kit were used during the analytical study.
Results & Discussions
Data pertaining to experiments conducted for determining the intensity of corrosion has been recorded in table no.1 &
-
Average corrosion rates of mild steel in different process liquors have also been presented in Fig. 1. From these tables and Fig.1 following observations can be made:
Corrosion in Mixed Juice
Data with regard to corrosion of mild steel in mixed juice has been reported in table 2. It is evident from the table; corrosion rates of mild steel in mixed juice are around 1000 mg per decimeter square per day (mdd), which are appreciably higher than the corrosion rates of mild steel in any other process liquors. It may be primarily due to lower pH values (5.1-5.3), higher dissolved oxygen content (53.7-6.2 mg/liter) and significant amount of suspended solids present in mixed juice during the experiment (table 1).
Corrosion in Sulphited Juice
It is evident from the table 2 that mild steel corrosion is lowest in sulphited juice amongst all other process liquors barring unsulphured syrup and final molasses. Although the temperature and dissolved oxygen content of sulphited juice being in the range of 68-72 C and 3.2-3.9 mg/liters respectively are liable to increase corrosion rates but the pH of sulphited juice being around neutral (6.9-7.1) may be the main factor restricting the corrosion rate.
Corrosion in Clear Juice
Apart from various other parameters e.g. pH, dissolved oxygen content etc., it is the temperature which influences the corrosion rates. Since the temperature of clear juice remains much higher (94 – 95C) than any other process liquors, the mild steel corrosion was observed to be appreciable. The pH & dissolved oxygen content of the clear juice was found to be around 6.7-6.9 and 1.8-2.0 mg/litres respectively.
Corrosion in Filtered Juice
Mild steel corrosion was found to be considerably higher i.e. around 800 mdd mainly due to lower pH and higher temperature of the filtered juice. It can be observed that mild steel corrosion rates in filtered juice are higher than those in clear juice and somewhat lower than those in mixed juice. Moderate quantity of dissolved oxygen in the filtered juice also contributed towards higher corrosion.
Corrosion in unsulphured syrup
A perusal of the data contained in table 2, reveals that mild steel corrosion was determined to be much lower, around 150 mdd only, than corrosion inother process liquors. The main reason for such behavior may be due to higher solid concentration (Brix % 55-60) and pH approaching neutral (6.5-6.7).
Corrosion in Sulphured Syrup
In a sugar factory, prior to crystallization, syrup obtained from evaporators i.e. unsulphured syrup is bleached by passing. SO2 gas and in the process the pH of sulphured syrup is maintained around 5.0-5.2. The corrosion rates of mild steel in sulphured syrup were found to be around 375 mdd which are almost 125% higher than the corrosion rate of mild steel in
unsulphured syrup. Since, as evident from table 1 except for pH, there is no material change from unsulphured syrup, it may be inferred that corrosion rate has increased owing to lower pH values.
Corrosion in Final Molasses
The data obtained with regard to mild steel corrosion in final molasses has been presented in table 2. It can be observed from the table that corrosion rates in final molasses are considerably lower and comparable with those in unsulsphured syrup. Such behavior may be attributed only to the higher total dissolved solid content (85-87%) of the final molasses. It is accepted that at such a high dissolved solid concentration, the quantity of dissolved oxygen, which has prominent role in corrosion will be very low.
Further, an experiment was conducted in laboratory to precisely ascertain the increase in iron content in juices owing to corrosion and colour development due to reaction between iron & polyphenols. In one set of experiments samples of mixed juice collected after regular intervals were clarified in the usual manner i.e. using mild steel vessels, whereas in another set same sample of mixed juice was processed in glass vessels. Samples of mixed juice and resultant clear juice were analyses for iron content and colour values in a manner described by ICUMSA. The results of the experiment are given in table No. -3 and also presented in graph ( Fig.2).
Data presented in table no.-3 and Fig 2 indicated that for a given quality of juice, keeping other variable constant, the iron content is more in the juice which were processed in mild steel vessels than to the juices processed in glass vessels & so is the colour development. Thus it may be inferred that the formation of coloring compounds as a results of reaction between iron and polyphenols may alone increase the colour values of clear juice by 5-7%, which in turn on crystallization may enhance the sugar colour by corresponding value.
CONCLUSION
On the basis of studies carried out, it may be inferred that the mild steel process equipments in sugar industry suffer moderate to severe corrosion depending upon the characteristics of process liquors. In general low pH (below 5.0), temperature (above 70C), higher dissolved oxygen (above 5.0 mg/liter) & lower dissolved solid content (below 40 Brix) of process liquors enhances corrosion rates. Further there is a definite relationship between iron content in the process liquors & ultimate colour development. Since corrosion increases iron content in the process liquors which reacts with polyphenols present therein, it is expected that there will be substantial colour development owing to this reaction which may alone increase the colour values of sugar by 5-7% or even more depending upon the iron content and polyphenols present. As such, preventive measures need to be taken to minimize corrosion of process equipments at various stages so as to restrict iron content of process liquors.
ACKNOWLEDGEMENT
Authors wish to place on records their extreme thank to Shri Narendra Mohan, Director, National Sugar Institute, Kanpur for his keen interest and valuable guidance.
REFERENCES
-
Uhilg H.H. (1947) Corrosion Hand Book, Cambridge Massachusetts.
-
Shriev L.L. (1947) Corrosion Vol. I, Newnes Butter Worths, London.
-
Mohan N., Bajpai A (August 2020), International Journel of Science and Research, Vol. 9, Issue 8.
-
Vysokova G.M. et.al. (1985) Sakh Prom, 90, 47-51.
-
Kukota S.N. et.al ( 1984) FSTA, Vol. 16(4)
-
Shukla N.P. Bajpai (1996), Studies on Corrosive Behavior of Various Steels, Proc. Annual Convention of STAI M 107 M 116. [7] Doss K.S.G. (1979) Trans. SAEST, Vol. 14, 161-172.
-
-
Vysokova G.M. et.al. (1985) Sakh, Prom. 9, 47-51.
-
Kukota S.N. et.al. (1983) Pisch Prom. (Kiev Tekhmika), 1, 41-42.
-
Sethi Y.K. et.al. (1988) 60th Annual Conv. Sugar Technol. Ass. of India, M 35 M41.
Table1. Analysis of Process Liquors at Various Stages of Processing During Experiment in Vacuum Pan Sugar Factory
S. No. |
Process Liquor |
Brix % |
Sp. Gravity |
pH |
Temp. (C) |
Sulphated ash % |
DO (mg/ltr) |
1 |
Mixed Juice |
14.5-15.5 |
1.0575-1.0629 |
5.1-5.3 |
25-28 |
0.70-0.74 |
5.7-6.2 |
2 |
Sulphited Juice |
14.5-16.0 |
1.0575-1.0650 |
6.9-7.1 |
65-68 |
0.68-0.71 |
3.2-3.7 |
3 |
Clear Juice |
14.5-16.0 |
1.0575-1.0650 |
6.7-6.9 |
94-95 |
0.65-0.68 |
1.8-2.0 |
4 |
Filtered Juice |
12.0-14.0 |
1.0481-1.0565 |
6.3-6.5 |
65-68 |
0.66-0.70 |
3.2-3.8 |
5 |
Unsulphured Syrup |
56.0-60.0 |
1.2644-1.2876 |
6.5-6.7 |
55-60 |
2.35-2.41 |
– |
6 |
Sulphured Syrup |
56.0-60.0 |
1.2644-1.2876 |
4.9-5.2 |
54-58 |
2.38-2.44 |
– |
7 |
Final Molasses |
85.0-87.0 |
1.4263-1.4466 |
5.1-5.3 |
42-45 |
14.0-14.5 |
– |
Table 2. Mild Steel Corrosion in Process Liquors at Various Stages of Processing in Vacuum Pan Sugar Factory
S. No. |
Process Liquor |
Wt. Before Exposure(gm) |
Wt. After Exposure(gm) |
Wt. Loss (gm) |
% Corrosion |
Corrosion Rate(mdd) |
Average corrosion Rate mdd) |
1 |
Mixed Juice (MJ) |
74.0665 73.8875 73.9210 |
72.2545 72.0385 72.1160 |
1.812 1.849 1.805 |
2.45 2.50 2.44 |
1003.32 1018.73 994.49 |
1005.51 |
2 |
Sulphited Juice ( SJ) |
73.8724 73.9210 74.0081 |
73.4424 73.4850 73.5591 |
0.430 0.436 0.449 |
0.58 0.59 0.61 |
242.12 238.25 249.44 |
243.27 |
3 |
Clear Juice (CJ) |
73.8817 73.9542 73.9168 |
72.6257 72.7292 72.6958 |
1.256 1.225 1.221 |
1.70 1.66 1.63 |
692.01 674.93 665.56 |
677.5 |
4 |
Filtered Juice (FJ) |
73.9011 74.0178 74.0062 |
72.4611 72.5938 72.5172 |
1.440 1.424 1.489 |
1.95 1.92 2.01 |
797.34 788.48 820.39 |
802.07 |
5 |
73.7174 73.8211 74.0120 |
73.4474 73.5331 73.7460 |
0.270 0.288 0.266 |
0.37 0.39 0.36 |
150.00 162.16 152.09 |
154.75 |
|
6 |
Sulphured Syrup (SS) |
74.0128 74.1312 73.8976 |
73.3428 73.4322 73.2336 |
0.670 0.699 0.664 |
0.91 0.94 0.90 |
377.25 399.66 373.87 |
383.59 |
7 |
Final Molasses (FM) |
73.9173 73.8834 73.8907 |
73.6533 73.5784 73.6177 |
0.264 0.256 0.273 |
0.36 0.35 0.37 |
146.18 144.14 153.72 |
148.01 |
Table No. -3 Effect of Iron Content on Colour Development in Process Liquors
Sample No. |
Mixed Juice |
Clear Juice From MS Vessels |
Clear Juice From Glass Vessels |
|||
Iron Content ( ppm) |
Colour Value (ICUMSA Units) |
Iron Content ( ppm) |
Colour Value (ICUMSA Units) |
Iron Content ( ppm) |
Colour Value (ICUMSA Units) |
|
1 |
303 |
12414 |
188 |
7064 |
182 |
6605 |
2 |
278 |
12202 |
177 |
7136 |
164 |
6786 |
3 |
286 |
13006 |
184 |
7188 |
176 |
6685 |
4 |
261 |
12756 |
172 |
6984 |
160 |
6704 |
5 |
270 |
12678 |
165 |
7220 |
158 |
6715 |
1200
1000
Corrosion Rate (mdd)
Corrosion Rate (mdd)
800
1005.51
677.5
802.07
600
400
200
243.27
154.75
383.59
148.01
0
MJ SJ CJ FJ US SS FM
Figure: 1 Mild Steel Corrosion in Process Liquors at Various Stages of Processing in Vacuum Pan Sugar Factory
12202
12202
12756
12756
278
278
9000
9000
270
261
270
261
7064 7136 7188 6984 7220
7064 7136 7188 6984 7220
6704 6715
6605 6786 6685
6704 6715
6605 6786 6685
172
172
176
176
165
165
164
164
160
158
160
158
3000
Mixed Juice
3000
Mixed Juice
140
140
Clear Juice From MS Vessels
Clear Juice From MS Vessels
Clear Juice From Glass
Clear Juice From Glass
Figure: 2 Effect of Iron Content on Colour Development in Process Liquors
Colour Value (ICUMSA Units)
Colour Value (ICUMSA Units)
13000
12414
13006
12678
340
13000
12414
13006
12678
340
11000
303
286
290
11000
303
286
290
240
7000
240
7000
5000
188
177
184
182
190
5000
188
177
184
182
190
Very detailed & important study .
Long ,long back I made similar studies in association with SAIL and published papers in STAI Proceedings .
Corrosion Resistant copper bearing Steel and SS 409 were introduced specially for sugar Industry .