
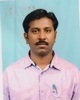
- Open Access
- Authors : Mahesh G , Hiregoudar Yerrennagoudar , Somanath Swamy R H M , B Basava Prakash
- Paper ID : IJERTV10IS020269
- Volume & Issue : Volume 10, Issue 02 (February 2021)
- Published (First Online): 04-03-2021
- ISSN (Online) : 2278-0181
- Publisher Name : IJERT
- License:
This work is licensed under a Creative Commons Attribution 4.0 International License
CFD Simulation of In-Cylinder Air Swirl by Modification in Piston Bowl
1Mahesh G
Assistant Professor, Dept. of Mechanical Engg.
RYM Engineering College Ballari, Karnataka, India
3 Somanath Swamy R H M
Assistant Professor, Dept. of Mechanical Engg.
RYM Engineering College Ballari, Karnataka, India
2Hiregoudar Yerrennagoudar
Professor, Dept. of Mechanical Engg.
RYM Engineering College Ballari, Karnataka, India
4B Basava Prakash
Assistant Professor, Dept. of Mechanical Engg.
RYM Engineering College Ballari, Karnataka, India
Abstract The purpose of study is to know the air swirl inside the combustion chamber through the CFD simulation of 4 stroke single cylinder Diesel engine. This helps to know the flow of air in the cylinder before conducting the experimental work. From this CFD simulation work, we can identify the behavior of air swirl. In this study, piston is modified to increase the physical phenomena inside the combustion chamber. The effect of redesigned bowl will have on CFD and the efficient operations of diesel engine for bulky applications. The configurations of modified piston bowl shall be the mainly significant component for the effect of air/fuel mixture. By changing the piston bowl like size, shape and area is well known to influence in chamber blending and number of cycles for better combustion process and engine performances. Model was designed by using CATIA and Configured AVL FIRE 2014.1 simulation in star ccm+.
Keywords Diesel Engine, modified Piston, CFD.
-
INTRODUCTION
Diesel engine is also called as C.I engine, which are generally used for transport, farming application and mechanical segments due to more fuel transformation efficiency with simple activity. The current C.I engine work with regular CN fuels got through raw petroleum. It is notable to world oil assets be constrained in addition to creation of unrefined petroleum is getting increasingly troublesome and costly. Then again, the pollutant includes unburnt hydrocarbon, CO, NOx with soot emission can be managed by regulation in numerous nations. Swirl atomizes the air fuel flow by optimizing inside the engine chamber due to which intake motion can create more energy of kinetic during the cycle of operating. In conventional engine, close to optimum flow values are essentially well-known and included, along with so called motion of tumble and swirl.
-
LITERATURE SURVEY
P.Venkatesh et.al [1] experiment was performed on how to minimize emissions by modifying piston geometry. In DI engines, swirl can affect the air-fuel mixing phase. Swirl mixing with compression mixing improves the mixing in the combustion bowl. The amount of influence geometry has on the intake stroke is negligible, and geometry has very little effect upon the early part of the compression stroke. The brake thermal efficiency at a compression ratio of 17.5:1, at a pressure of 220 bar and at maximum load was found to be maximized.
Praveen A. Harari et. al [2] The research is about how air swirl affects engine efficiency, combustion, and emissions performance to help better mixing without the need for the turbulence, and the fact that it is controllable by the shape of the combustion chamber. Innovation in combustion chamber architecture is in high demand as with the emergence of new developments in automotive engines and fuel types. Combustion chamber is important in CI engines, since they are used in a wide range of applications.
K.S.Karunakar et. al [3] have simulated a diesel engine by implementing tangential grooves on the piston in an effort to boost through combustion. The project aims to create spinning motion in the compressed air in the combustion chamber by modifying the piston. The swirl motion that occurs in the combustion chamber leads to better mixing of the fuel and air which enables more efficient combustion.
-
METHODOLOGY
Fig. 1 shows Methodology
-
ENGINE DETALIS
Fig. 2 Shows engine details
-
3D CAD MODEL DESIGN
The engine model studied by a typical single-cylinder diesel engine with combustion chamber on bowl shape piston. By using CATIA V-5 R18 software.
Conventional piston Modified piston
Fig. 3 shows 3D cad model
-
CFD SIMULATION
-
Velocity distribution for Conventional piston
Fig. 4 shows Velocity distribution for Conventional piston at different angles
-
Velocity distribution for Modified piston
Fig. 5 shows Velocity distribution for modified piston at different angles
-
-
RESULTS AND DISCUSSION
Air swirl Comparison of velocity distribution is made between conventional piston and modified piston at various crank angles such as 10,900, 1800 and 3600. Using FLUET tool star ccm+.
-
Velocity distribution at 900crank angle is high for modified piston when compare to conventional piston. Identified based on the color, red is more visible at 900 crank angle.
-
Velocity distribution at 1800crank angle is comparatively high for modified piston when compare to conventional piston. Behavior of air swirl is visible based on green color at 1800 crank angle.
-
Velocity distribution at 3600crank angle is comparatively high for modified piston when compare to conventional piston. Behavior of air swirl is visible based on green color when piston moving towards Top dead centre.
This proves that more air swirl is created in the cylinder leading to more proper air-fuel mixture for complete combustion of fuel.
REFERENCES
-
P.Venkatesh, G. Anand Rao, Reduction of emissions by changing piston geometry Department of MECH, MLR institute of technology, Ranga Reddy, Telangana, India. International journal of professional engineering studies, Volume VI /Issue 2 / DEC 2015.
-
Praveen A. Harari, S. S. Ghadg, Arun Pattanashetti, A Review on Effect of Combustion Chamber Geometry on the Performance Combustion and Emission Parameters of Compression Ignition Engine Fuelled with Biodiesel Department of Mechanical Engineering, SGOICOE, Belhe (Pune), Maharashtra, India. International Journal of Engineering and Management Research, Volume-6, Issue-3, Page Number: 304-316, May-June 2016.
-
K.S.Karunakar,Dr.C.VijayaBhaskarReddy,D.S. Jaheer Basha ,Design & analysis on a diesel engine by implementing tangential grooves on piston for combustion improvement through cfd Department of Mechanical Engineering, SVCET (Autonomous), Chittoor, A.P, INDIA 517127. International Research Journal of Engineering and Technology (IRJET), Volume: 03 Issue: 06, e-ISSN: 2395 -0056, p-ISSN: 2395-0072, June-2016.
-
Mahesh G, HiregoudarYerrannagoudaru, RHM Somanath Swamy, B Basavaprakash, Effect of Inlet Air Swirl in Ci Engines A Review International Journal of Scientific Research and Review (IJSRR), ISSN No.: 2279-543X, UGC Journal No.: 64650, Volume 07, Issue 05, May 2019.
-
Mahesh G, HiregoudarYerrennagoudar, Somanath Swamy R H M ,CFD Analysis of Air Swirl in Cylinder of CI Engine by Modification of Cylinder Head International Journal of Engineering and Advanced Technology (IJEAT) ISSN: 2249 8958, Volume-9 Issue-4, April 2020.