
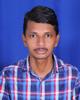
- Open Access
- Authors : Mallavarapu Arjun , Manjunath Soppin , Praveen Ahuja
- Paper ID : IJERTV10IS020253
- Volume & Issue : Volume 10, Issue 02 (February 2021)
- Published (First Online): 08-03-2021
- ISSN (Online) : 2278-0181
- Publisher Name : IJERT
- License:
This work is licensed under a Creative Commons Attribution 4.0 International License
Optimizing The Support Structures in Selective Laser Melting Process using Design for Additive Manufacturing (DFAM) Guidelines
Mallavarapu Arjun
Member Technical Staff ERS MMT-MMT-MCOE-CAE
HCL technologies, Bangalore
Manjunath Soppin
Technical Manager
ERS MMT-MMT-MCOE-CAE
HCL technologies, Bangalore
Praveen Ahuja
Global Program Manager ERS MMT-MMT-MCOE-CAE
HCL technologies, Bangalore
AbstractSelective laser melting (SLM) is one of the additive manufacturing (AM) technique based on the principle of powder bed fusion (PBF) process. In this process thermal energy is used to selectively fuses regions of powder bed to make objects. Like any manufacturing process AM technologies have their capabilities and limitations as well. The main challenges in SLM are distortions and high residual stresses in the components. In SLM process support structures are required to build the components, the main functions of support structures are to avoid collapse of molten materials in case of overhanging features, reduce the residual stresses and act as a heat sink. However, it increases build time, material waste and it needs extra post processing. Reducing the support structures is one of the major challenge in additive manufacturing. Support structures can be reduced by using design for additive manufacturing (DFAM) guidelines. AM Simulation software can be used to generate support structures and identifies residual stresses and distortions in the components. However, Support structures generated by AM simulation software are bulky compared to self-supporting designs which are created by using DFAM guidelines. This paper demonstrates the comparison study of automated support structures with that of self-supporting designs and highlights the advantage of DFAM guidelines for the support structures.
Keywords Powder bed fusion process, selective laser melting, design for additive manufacturing, residual stresses
-
INTRODUCTION
Additive Manufacturing (AM) is defined as the process of joining materials to build objects from 3D CAD data, usually layer upon layer, as opposed to subtractive manufacturing processes, such as traditional machining. In most of the AM processes, parts are manufactured layer by layer, using a source of thermal energy to fuse the different layers together. As a result, anisotropic material properties and residual stresses are common.
Powder bed fusion process is one of the popular metal additive manufacturing technique to build the components. The principle behind working of PBF is thermal energy selectively fuses regions of a powder bed. The powder bed is in inert atmosphere to provide shielding of the molten metal. An energy source (Laser beam) is used to scan each layer selectively melt the material according to the part cross section obtained from the digital part model. When one layer has been scanned, the piston of building chamber goes downward by defined layer thickness and roller deposits
powder across build chamber which is again scanned by the energy source as shown in the fig1. This cycle is repeated layer by layer, until the complete part is formed. Selective laser melting (SLM) is the most commonly used processes in metal additive manufacturing (AM). SLM is used to fabricating high complex but low-quantity products.
Fig. 1: Working of selective laser melting process
-
DESIGN FOR ADDITIVE MANUFACTURING (DFAM):
The most common reason for the parts are not being successfully manufactured are printability issues like residual stresses and distortions in the AM process. However simulation softwares and design guidelines are used to minimize the residual stresses and distortions in the components.
While the level of part complexity that metal printing is able to produce exceeds that of traditional manufacturing techniques, there are certain design rules that must be followed. Metal printed parts are anisotropic, can be produced from common engineering metals, such as stainless steel and titanium. However, the conditions under which metal printing is cost effective depends strongly on the geometry of a design. Many of the design constraints associated with metal printing relate to limiting the likelihood of warping or deformation and the use of support structures. One of the manufacturing restrictions inherent within AM is
the difficulty in fabricating overhanging features. Such features can be added through the use of supports. But adding Support Structures during printing leads to the problems of material waste, longer fabrication time and lower surface quality. But support structures can be minimized by applying design for additive manufacturing guidelines to the components.
-
Supports and part orientation
Metal printing utilizes support in 3 different ways:
-
The support offers a platform for the next layer to be built upon. To achieve this, for sections that are not attached to the build plate, support structures are first printed, then the solid sections are built on top of these.
-
Support anchors the part to the build plate increasing stiffness, holding thinner features in place. They act mostly in tension to prevent the part from peeling upwards due to residual stresses that are generated during the laser melting process.
-
Support structures also provide pathway for heat to be carried away from thermally isolated areas of the part. This approach reduces the possibility of distortion of the parts from the extreme heat.
-
-
Build AM parts without supports
Support structures are important to avoid in any internal features, such as the holes, as this can be difficult to remove. Typically, any feature that is more than a certain angle from vertical, such as 45° will require support material. Part orientation on the build plate is an important factor to consider at this stage of the design for AM. When designing for metal AM, one should always design around the specific orientation in which the part will be printed. This is because part orientation impacts the direction of anisotropy, surface finish, roundness of holes and support material.
AM Simulation softwares are used to generate support structures, support material is generated between all the horizontal holes which are less than 10 mm and overhang parts having angle less than 450. Support structures for the components can be reduced by following principles. Overhang features are provided with 450 chamfer to eliminate the need for support material as show in the fig 2. Water droplet type holes are instead of circular holes used to reduce weight and eliminate the need for support material inside the holes as shown in the figure 3.
Fig. 2: Greater than 450 chamfer for overhang features to avoid support structures
Fig 3: Circular holes are accurate up to 8mm diameter and for greater than 8mm diameter holes recommend geometries are rhombus or water droplet shape
The result is a design in which support material is only necessary to attach the bottom of the part to the build plate.
Using DFAM guidleines the part geometry can change slightly and again extea post processing is required. However using DFAM guidelines, time taken for the printing the components, support structrues, material required for the componet builiding and processing cost can be reduced.
-
-
PROBLEM DEFINITION
Fig 4: Generating the support structures for the model without selecting the optimum orientation
Using AM, it is possible to manufacture any type of complex design which is not possible by ther conventional manufacturing process.
But complex designs like Topological optimized designs need large amount of support structures for powder bed fusion process resulting in increased manufacturing and post processing costs, material waste and also it increases build time. Reducing the Support structure is one of the major challenge in additive manufacturing.
The objective is to minimize the support structures required for the components in selective laser melting.
-
METHODOLOGY AND IMPLEMENTATION Support Structures required for the components can be
reduced by using design for additive manufacturing (DFAM) guidelines. Using DFAM approach, support structures can be reduced and it will minimize material and manufacturing cost. To effectively implement this approach. AM Simulation software is required for selecting the optimum orientation and DFAM guidelines for design modifications.
-
AM Simulation software :
Simufact Additive is one of the AM software for the simulation of powder bed additive manufacturing processes (SLM, DMLS, EBM). Software predicts the distortion and residual stresses in the parts. Distortion of parts during the manufacturing process is a major challenge in the additive manufacturing process. Simufact software suggests optimum orientation based on different parameters. Parts need to be modified based on DFAM guidelines after choosing the printing orientation from simulation software
-
Machine:
Selective Laser Melting (SLM) is one of the additive manufacturing process works based on the principle of powder bed fusion process. SLM is used to fabricating high complex but low-quantity products. The simulated component will be manufactured using SLM
-
Material:
The material used in SLM machine is Ti64AL4V, density
4.5 kg/m3 which is almost half the density of steel and it is stronger than normal Steel material. Which is used in high performance light weight mechanical components for aerospace, dental and human prosthesis applications
-
Selecting the optimum orientation:
Orientation assistant can be used to find the best build orientation based on support area, support volume, projected area, design height, local minima criteria parameters. During the calculation the part will be rotated around the global x- and y-axes and for each orientation the criteria will be calculated. AM Simulation software considers different parameters for optimum orientation. As per the orientation assistant best orientation to print this component is vertical direction as shown in the fig 5. Even though selecting the optimized orientation, the support structures generated by the software are bulky. After optimum orientation, the parts to be designed using DFAM guidelines.
Fig 5: a) Different criteria for orientation b) Favourable direction c) Build direction based on orientation assistant
-
Modification of design using DFAM guidelines
After choosing the favorable orientation for printing, the components are modified based on DFAM guidelines. Circular holes are modified into water droplet shape and overhang features are avoided by providing chamfer at an angle of 450. In this figure as shown without design modifications need large amount of support structures and support structures are almost eliminated using design modifications are shown in the fig 6.
Fig 6: a) Without& With DFAM guidelines b) Difference in support structure
-
-
RESULTS AND DISCUSSION
-
Displacement comparison:
From the figure 7 the maximum surface deviation observed in the actual design is 1.49 mm and 0.52 mm in modified design.
Figure 7: shape deviation a) Without modified design b) With modified design
-
Weight comparision
The amount of material required for printing the components with & without DFAM guidelines are shown in below table. Without DFAM guidelines the material consumption for printing the component is 1.460 kg (component weight + support structures weight) and with DFAM guidelines material consumption is reduced to 0.614 kgs which is significant and is 57% reduction by weight compared to design without DFAM guidelines (Table 1). Results also indicate that the weight of the component is increased by 10% however, there is significant reduction in support structures weight.
TABLE 1:COMPARISON OF ACTUAL AND MODIFIED DESIGNS
S. No.
Design
weight of component
weight of support structures (50% dense)
Total weight (component weight + support structures)
1.
Without DFAM
410.234
1050.962
1.461 kg
2.
With DFAM
456.654
157.96
0.614 kg
-
-
CONCLUSION
Selective laser melting offers a unique freedom in design. However, there are some limitations like residual stresses, distortions and support structures. Minimizing these parameters while manufacturing the part is challenging task. By using design for additive manufacturing guidelines support structures can be reduced and minimize the shape deviation during manufacturing
In the above example, we can clearly see the advantages of modified design with DFAM guidelines over Initial design. In the modified design, holes greater than 8 mm in diameter have been modified to water droplet shape and also 45° angle chamfers are provided to overhang features to eliminate the need for support material. Based on above results, for printing the actual component is 1.460 kg (component weight + support structures weight) and for modified design using DFAM guidelines the material consumption reduced drastically to 0.614 kg which is significant and is 57% reduction in weight.
-
FUTURE SCOPE
Still research is required at microscopic level to predict the microstructure of the additive manufacturing parts to check the low relative material density, pores, insufficient powder building, surface quality, strength and durability etc.
-
REFERENCES
-
Simufact_Additive_Tutorial_en.pdf
-
Some aspects on designing for metal Powder Bed Fusion, Hällgren Sebastian, Orebro University, School of Science and Technology.
-
Design for Additive Manufacturing: Increasing part value through intelligent optimisation, Olaf Diegel and Terry Wohlers, Wohlers Associates, Inc.,Fort Collins, Colorado 80525,USA
-
Design for metal AM – a beginner's guide, Renishaw apply innovationSupport structure constrained topology optimization for additive Manufacturing, Amir M. Mirzendehdel, Krishnan Suresh, Computer-Aided Design
-
Can we build AM parts with supports? Marc Saunders, Director of AM Applications at Rensihaw.
-
Is topological optimisation really optimal? Marc Saunders, Director of AM Applications at Rensihaw
-
Design for Additive Manufacturing Worksheet, Journal of Mechanical Design. Joran W. Booth, Jeffrey Alperovich, Pratik Chawla, Jiayan Ma,
Tahira N. Rei, Karthik RamaniA
-
8. Review on Powder Bed Fusion Technology of Metal Additive Manufacturing, Valmik Bhavar, Prakash Kattire, Vinaykumar Patil, Shreyans Khot, Kiran Gujar, Rajkumar Sing.