
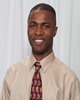
- Open Access
- Authors : Etim S Udoetok
- Paper ID : IJERTV10IS050010
- Volume & Issue : Volume 10, Issue 05 (May 2021)
- Published (First Online): 06-05-2021
- ISSN (Online) : 2278-0181
- Publisher Name : IJERT
- License:
This work is licensed under a Creative Commons Attribution 4.0 International License
Analysis of the Outer Region, Wall Region and Fluid-Solid Interface in Turbulent Pipe Flow
Etim S Udoetok
Mechanical Engineering Department University of Uyo
Uyo, Nigeria
AbstractTheoretical analysis along with empirical relations are used to split turbulent flow into two main regions; the outer region and the wall region. The location of the boundary between the outer region and wall region was found. Results fall within observed range and show the trend in the boundary location with respect to variation in Reynolds number and relative roughness. The study presented also shades much needed light on turbulent pipe flows.
Keywords Pipe flow; turbulence; friction; viscous sublayer; fluid flow
-
INTRODUCTION
The study of developed turbulent flows in pipes is of great
measurements [3], oil-film interferometry [2] [9] [10], and micro-pillar shear-stress sensors [11] [12]. All these experimental methods have limitations and challenges [2] which results in errors in their results. Empirical relations have been developed for the velocity profile in wall bounded turbulent flows for smooth walls and rough walls [1] [6]. The velocity profile for a smooth pipe is given as
+ = + for 0 + 5 (2)
+ = 2.44+ + 4.9 for 30 < +and < 0.15
(3)
+ + = 2.44 () + 0.8 for the outer region
interest, since all flows are turbulent in nature and laminar flows are just idealization based on suitable conditions for
(4)
simplification. In pipe flows, laminar flows can be assumed when Re 2000, and assumed to be turbulent when Re > 2000, though there is a transition regime of 2000 < Re < 4000 and under controlled laboratory condition, laminar flows have been observed in flows with Re up to 40000 [1]. Turbulent flows are characterized by fluctuations in velocity in all coordinate directions; however, the time averaged values are
where R is the internal radius of the pipe and umax is the maximum velocity. In the buffer zone (5 < + < 30), the two curves (equations (2) and (3)) are merged. For rough pipes, the viscous sublayer has less influence because the protruding
wall elements dorminate the generation of turbulence, so the velocity profile becomes a function of pipe roughness, e, and is given as [1]
usually used in turbulent flow analysis [1]. The turbulent flow may be divided into 3 main regions; viscous sublayer at 0 y+
5, buffer zone at 5 < y+ < 30 and outer region at y+ 30 [1] [2]. Where y+ is the normalized distance from the wall which
+
= 2.44 () + 8.5 for 30 < +
and < 0.15
(5)
is defined as
+
The maximum velocity is given as [1]
+ = 2.44 () + 5.7 for smooth pipes
=
(1)
(6)
Where u is the shear velocity defined by = 0, 0
is the shear stress at the wall, is the fluid density, y is the
and + = 2.44 () + 9.3 for rough pipes
linear distance from the wall and is the kinematic viscosity
-
[2]. The viscous sublayer has been identified as the region
(7)
critical for the understanding of wall bounded turbulent flow
- [3] [4] [5] [6], because experimental studies have shown that the nature of flow close to the wall has an important
The wall shear stress, if not measured directly for example by the new micro-pillar shear-stress sensor, can be found by using pressure sensors and the equation
influence on the wall shear stress and energy as indicated by eddies develop in the viscous sublayer and flow out to the
0
=
2
(8)
other regions [3] [4] [5]. Understanding the viscous sublayer may also be the key to understanding how Drag Reduction Agents work [7].
where dP/dx is the pressure gradient. 0 can also be found using the coefficient of friction, , with the equation [1]
Specifically, the velocity profile of the viscous sublayer
0
= 1 2 (9)
8
determines the wall shear stress 0 which is an important parameter for describing turbulent flows [2]. In experiments, it is not easy to obtain accurate velocity measurements within the viscous sublayer [2]. Though there is a wealth of
where V is the average velocity. Additionally, a simpler velocity profile which adequately describes the turbulent flow velocity in a pipe is the power-law profile given as [1]
experimental information on turbulence close to the wall. Experimental study of viscous sublayer has included visual observation using ultra microscope [3] [8], hot-wire
1
= ( )
(10)
where the maximum velocity is given as
1
(1 1) = ( ) + 2 + (19)
(+1)(2+1)
1 1
=
22 (11)
Applying BC 3 (equation (15)) gives
and n is an integer between 5 and 10 related to the coefficient of friction by the empirical relation
11
(1 1)
= + 2
(20)
1 1
= 1
(12)
Applying BC 4 (equation (16)) gives
The power law fails to adequately describe velocity in the wall region and would yield infinite shear stress at the wall [1].
() + 2 + = 0 (21)
Solving equations (19), (20) and (21) gives
1
2
11
There is insufficient theoretical analysis to interpret the
( )( 1)(2 1(1 1)
(1( 1) )(1 1) )
experimental observations of turbulence close to the wall [3].
=
1
1
2 2
(22)
Some authors have contributed theoretically [3] [13] [14] [15]
(1(1) +2(1) ln ( ))
[16] and the theory has been trying to catch up with experimental observation starting with assumption of laminar1
11
( )((1 1) ( 1)ln ( 1)(1 1) )
flow in the region to the assumption of turbulent flow in the region with the region being pointed as the key source of
=
2
1 2
1 2
1
(23)
turbulence. Some of the theories have used assumption that there is slip at the wall [5] [13].
In this paper, the outer region described by the power law is combined with a selected empirical friction model to develop
And
=
(1( ) +2( ) ln ( ))
1 1
1 1
1
1
1 1
1 1
2 1 2 3
a model for describing the viscous sublayer.
()((12( ) ln ())(1 )
+(( )
ln(1)( ) ln ())(1 ) )
-
[2]. The viscous sublayer has been identified as the region
-
METHODS
2 1 2 1
2 1 2 1
(1(1) +2( ) ln ( ))
Turbulent flows in pipes are dependent on the wall
(24)
condition which is either smooth or rough, so two cases will be treated in the analysis of turbulent flow in pipes.
-
Case 1: Turbulent flow in smooth pipes
Where r1 and umax are still unknown. umax can be found from the average velocity value as shown below
0
0
0()2+ 1()2
=
0 0 =
2
0
(1()2)2+
(1)12
The simplest form of the velocity profile for a turbulent flow is the power-law profile [1] which will be adopted for this
0
0
2
work, butdue to its limitation at the centerline and at the wall, appropriate equations from common solutions of the Navier Stokes equation will be used as presented below
() =
Here it is assumed that the error in using u1 to cover for u2 is negligible since integration is involved. Therefore, integrating and solving for umax gives
2
2
= 1.46110.8885 (25)
= (1 () ) 0
0
0 r1 is found by applying equation (19) at r = R
=
1
(1 )
= 1 2 = 2|
= ( + 2) (26)
1
0 1 0 8
=
{2 = () + 2 + 1
(13)
Equations (23) and (23) into (26) gives
Where u
max
is the maximum velocity, A and B are
1 2 =
8
constants, while r0 and r1 are the points where the centerline
1.46110.8885
1
2
11
1
1
( )( 1)(2 1(1 1) (1( 1) )(1 1) )
velocity and wall velocity matches the power-law profile respectively. The boundary conditions (BCs) are
( (
1 2
1 2
) +
1
0 = 1 @ = 0 (14)
(1( ) +2( ) ln ( ))
1
1 1
1 1
(1.46110.8885)((1
1)1( )ln ( )(1
1)1)
2 1 2
2 1 2
1
= 2
@ = 1
(15)
2
2 (
) )
1
2
(1(1) +2( ) ln (1))
=
@ = 1 (16)
2 = 0 @ = (17)
(27)
Applying the first BC (equation (14)) gives
0 = 1.20361.058 (18)
Applying BC 2 (equation (15)) gives
Equation (27) simplifies to
1 2 1
1 2 1
1
(1)(21(1 1)1(1( ) )(1 1) )
and is pipe roughness and is known for the pipe material.
= 2 (
1 1
1 1
) +
The boundary conditions (BCs) are
23.3776
0.1115(1(1)2+2( )2ln ( ))
(
1
1 1
1 1
11
0 = 1 @ = 0 (34)
1 = 2 @ = 1 (35)
((1 1) (1)ln ( )(1 ) )
2 (
0.1115
1 2
1 2
)
1
(28)
1
= 2
@ = 1 (36)
(1( ) +2( ) ln ( ))
) 2 = 3 @ = (37)
Assuming that r1 falls in the wall region such that r1/R ranges from 0.805 to 1, equation (28) can be simplified to
3
= 0 @ = (38)
17.029 2 168.745 + 443.692
Applying the first BC 1 (equation (34)) gives
=
23.3776
1
1
1
(29)
0 = 1.20361.058 (39)
Therefore,
1 = 1 23.3776 (17.029 2 168.745 + 443.692)
Applying BC 2 (equation (35)) gives
1
1
1
(30)
(1 1)
= (1) + 2 + (40)
At this point all unknowns can be estimated for the velocity profile of turbulent flow in a smooth pipe as given by
Applying BC 3 (equation (36)) gives
11
equation (13), so that appropriate analysis can be performed
(1 1) = + 2
(41)
with it. Equation (30) can also be used to estimate r1/R by
1 1
using an equation for the friction coefficient for a smooth pipe. An equation similar to that of Petukov [17] was developed using more recent experimental data published in McKeon et al work [18]
Applying BC 4 (equation (37)) gives
( ) + ( )2 + = ( )2 + ( ) +
(42)
= 1
= 0.762 ln() 1.3328 (31)
Applying BC 4 (equation (38)) gives
(valid for 4000 36000000)
The value of y+ corresponding to r1 can be found from a further simplified form of equation (1)
2 + + = 0 (43)
2 3 4
2 3 4
Assuming that R >> , equation (42) can be expanded so that the method of matched asymptotic expansion can be applied:
2
()
(ln() (5)) + (2 2
+ =
0 =
8
= = =
2 2 2 2
22 33 44
(1)
= (1
)
(32)
2) + = (2 2 2) + ( ) + (44)
Equating coefficients
2 2 2
2 2 2
0: () + 2 + = 0 (45)
-
Case 2: Turbulent flow in rough pipes
1: 2 = 2 (46)
The simplest form of the velocity profile for a turbulent flow
2: 22
+ = (47)
is the power-law profile [1] will also be adopted for this case, and the common solutions of the Navier Stokes equation used in case 1 will also be used as presented below
2
Equations (40), (41) and (45) retains the terms from case one, so the solution for A, B and C are the same as that of case 1, but E and F needs to be found by solving equations (46) and
(47) simultaneously, we have
= (1 ( ) ) 0
0
0
1
2
11
( )( 1)(2 1(1 1)
(1( 1) )(1 1) )
() =
=
1
(1 )
=
(48)
1 0 1
2 1
2 1
(1(1)2+2(1) ln ( ))
2 = () + 2 + 1
{ 3 = 2 + +
1
11
1
1
(33) ( 2 )((1 )
( 1)ln ( 1)(1 1) )
=
2 2
(49)
Additionally, a parabolic velocity profile was adopted for (1 1) +2 1) ln (1))
the rough region since it very thin and Popovich and Hummel
(
(
2
1
2
3
11
[19] found in their experimental work that the thin layer of( )((12( 1) ln ())(1 1)
+(( 1) ln( 1)( 1) ln ())(1 1) )
fluid at the wall was characterized with a linear velocity
=
1 2
1 2
1
gradient, so a parabolic profile over an infinitesimal will look linear and the constant E will be small after the analysis. Compared to case 1, E, F and G are new constants to be found
(1( ) +2( ) ln ( ))
(50)
=
1
11 1
1
2
2
2
11
Equation (54) into equation (55) gives
( )((1 1)
( 1) ln( 1)(1 1)
( 1)(2 1(1 1)
(1( 1) )(1 1) )) 1
2
2
1
25 2
1
25 2
2(22 ) 2
1 2
1 2
1
( ) = (
) + ( )
(56)
(1( ) +2( ) ln ( ))
8
8
8
2
1
2
11
(51)
Using = 2 and = 2( ) = 2, and dividing through by common terms reduces equation (56) to
2 3 4
2 3 4
( )( 1)(2 1(1 1) (1( 1) )(1 1) ) 1 1
1 5 2
16(() 2() +( ) ) 2
= 2 2
(52)
1 2 (12)
1 1
1 1
(1(1) +2( ) ln ( ))
( ) = (
) + (
) (57)
=
1
11 1
1
0
0
2
11
In order to estimate the average velocity in the clear region
( )((1 1)
( 1) ln( 1)(1 1)
( 1)(2 1(1 1)
(1( 1) )(1 1) ))
0()2+ 1()2
1 1
1 1
2 2
(1(1) +2( ) ln ( ))
=
0 0 =
) )2+
) )2+
()2
1
1
1
1 1
1 1
2 11
0
2
1
2()(1)(21(1 )
(1( ) )(1 ) )
0 (1( 0
(1)
2
(58)
1 1
1 1
2 2
(53)
()2
(1(1) +2( ) ln ( ))
Just as was done for case 1, umax can be found from the average velocity value as shown below
Similarly, u2 overlaps over u3 for approximation and umax is used from equation (25) so integrating equation (58) gives
1
2.92221.8885 1+
0 ( )
( )
[0.96420.0122( ) ((2 )+1 )]
= 0
0 2+0 1 2 =
2
=
(1+2)(1+)
2
2
(1)
(59)
0
(1()2)2+
(1)12
0
0
2
= into equation (55) gives
Again, it is assumed that the error in using u1 to overlap u2 and u3 is negligible since integration is involved and (R-r1) and are much smaller than r1. Therefore, integrating and solving for umax gives
= 1.46110.8885 (25)
Finding r1 for case 2 is more challenging than case 1, since we have assumed that the fluid structure has been
= + (60) Which expands to
2 = ( )2 + (2 ( )2) (61) Therefore
(1)2
= =
2
(2 ( ) )
discontinued due to the protruding rough spikes. Therefore,
the friction coefficient has to be treated separately for the
1
2.92221.8885 1+
(10.96420.0122 ( ) ((2 )+1 ))
rough region and for the clear region. Consider the electrical analogy in Fig 1.
(1+2)(1+)
2
(2 ( ) )
fCl is estimated from
= 1
2 = 2|
= (
+ 2( )) =
8
=
(
(1)
+ 2 (1 )) (63)
As
=
=
12
(
(1)
+ 2 (1 )) (64)
Fig 1: Electrical analogy of separate friction effect in rough
8
1 1 1 1 1
1 1 1 1 1
1
(1.46110.8885)( )(2 (1 )1(1 )2)(1 ) 1)(1)3
region and clear region.
16
=
=
(
1 2 +
(1(1)2+2(1)2ln (1))[0.96420.0122 2.92221.8885()1+((2)+1)]
(
(1+2)(1+)
1.46110.8885
1
11
( )((1 1) ( 1)ln ( 1)(1 1) )
4
4
2
2
The pressure change is given by Darcy Weisbach equation as
2 2
1.8885
1+1
(1 )
2
2
[1] (1(1) +2(1) ln (1))[0.96420.0122 2.9222()
((2)+1)]
2 2
2 2
= = 8
(54)
(
(1+2)(1+)
)
)
(65)
2
25
Assuming that r1 falls in the wall region such that r1/R
Summing the two flow rates
= + (55)
ranges from 0.805 to 1, equation (65) can be simplified to
1 1.8
(1
(1
4
1 2
3
1
0.5(1 1)0.95
= (0.21632 + 6.4502 23.4472)
= 16
1.1284(1 )
) 0.6225(1 )
(1 )
0.00353 + 0.09822 0.8934 + 2.7457
1.8885
1+1 2
[0.96420.01222.9222 ()
((2)+1)]
(
fRo is estimated from
1
(1+2)(1+)
3
3
)
(66)
Therefore,
1 = 1
1
(73)
=
2 = ( |
| ) = 2
0.5263 2
3 2
1.0526
8
=
=
(67)
((0.2163 + 6.4502 23.4472) 0.0035 + 0.0982 0.8934 + 2.7457)
(74)
=
=
Therefore,
Equation (74) can also be used to estimate r1/R by adopting the total friction given by [20]
2
12
(68)
1 6.9
1.11
6.9
1.11
8
1.46110.8885
1.46110.8885
1
1
1
1 1
1
1 1
( )((1 1)
1
1
( 1) ln( 1)(1 1) ( 1)(2 1(1 1)
2
2
1
1
1
1
(1( 1) )(1 1) ))( )(2 ( ) )
2 2
2 2
=
= 1.8 Log [
+ ( )
3.7
] = 0.7817ln [
+ ( )
3.7
]
(75)
= 32
2
1
2 +
(1 1)2+2 1)2ln (1))(10.96420.0122 2.92221.8885( )1+((2)+1))
The value of y
corresponding to r1 and can be found from
(
(
(1+2)(1+)
equation (32).
(69)
Assuming that r1 falls in the wall region such that r1/R ranges from 0.805 to 1, equation (69) can be simplified to
-
-
RESULTS
Numerical values for Reynolds number were selected and used to check the results obtained for the case of turbulent flow in a smooth pipe [See Table 1.] The calculation results
)(
)(
1 1.9
2 2
showed that y+ at r1 ranges from 21 to 295 for the Re range
32 (0.8619(1 )
=
=
)(2 ( ) )
1
covered by equation (31). Similarly, numerical values for Re
1+
1+
2
2
(10.96420.0122 2.92221.8885() ((2)+1))
and were selected for the case of turbulent flow in rough
(1+2)(1+)
(
)
(70)
pipe, and the resulting values r1/D and y+ are presented in Table 2. In order to obtain extreme values for turbulent flow in a rough pipe, Re = 4000 with low and high values of /D and Re = 108 with low and high values of /D. The values of
Equations (66) and (70) into equation (57) gives
1
1 2 2
/D were selected to keep n within 5 and 10 where most of the developed equations are valid.
(12 )5[0.96420.0122 2.92221.8885()1+((2)+1)]
=
2
1.8
(1+2)(1+)
4
2
+
+
3
Table 1: r1/R and corresponding y+
for a smooth pipe
16 1.1284(1 1) (1 ) 0.6225(1 1)
(1 )
( (
))
1
1+
1+
Re |
/D |
(31) |
r1/R (30) |
y+ @ r1 (32) |
4.00E+03 |
– |
0.040205 |
0.849896 |
21.28207 |
4.00E+04 |
– |
0.022001 |
0.953207 |
49.07798 |
1.00E+05 |
– |
0.018065 |
0.969406 |
72.69179 |
1.00E+06 |
– |
0.011829 |
0.992243 |
149.1419 |
1.00E+07 |
–> |
0.008341 |
0.998509 |
240.6645 |
3.60E+07 |
– |
0.007032 |
0.999446 |
295.6495 |
Re |
/D |
(31) |
r1/R (30) |
y+ @ r1 (32) |
4.00E+03 |
– |
0.040205 |
0.849896 |
21.28207 |
4.00E+04 |
– |
0.022001 |
0.953207 |
49.07798 |
1.00E+05 |
– |
0.018065 |
0.969406 |
72.69179 |
1.00E+06 |
– |
0.011829 |
0.992243 |
149.1419 |
1.00E+07 |
– |
0.008341 |
0.998509 |
240.6645 |
3.60E+07 |
– |
0.007032 |
0.999446 |
295.6495 |
1 2 2
at selected Re values
(( )22( )3+( )4)(10.96420.0122 2.92221.8885() ((2)+1))
2
2
2
(1+2)(1+)
2
1 1.9
2 2
(0.8619(1 ) )( )(2 ( ) )
( (
))
(71)
For the purpose of estimation, equation (71) can be reduced to a solvable equation
0.5(1 1)
0.5(1 1)
1
1
0.95 =
2
2
1
5 1.8885 1+
5 1.8885 1+
1 2
(1) [0.96420.0122 2.9222 () ((2)+1)]
1
16
(1+2)(1+)
4
3
+
+
1.12843(1 ) 0.62253(1 )
(
(
( )
)
1
2 2
2
3
4
1
2.92221.8885 1+
(( ) 2(
) +(
) )(10.96420.0122
( ) ((2 )+1 ))
1
2
2
2
(1+2)(1+)
2
2 2
(0.86193)( )(2 ( ) )
( (
))
(72)
Assuming that /D falls with the range of 0.0000001 to 0.1, equation (72) can be simplified to
Table 2: r1/R and along with corresponding y+ values for a rough pipe at selected Re and values
Re |
/D |
(75) |
r1/R (74) |
Y @ r1/D |
y+ @ r1 (32) |
y+ @ (32) |
1.00 E+04 |
0.01 |
0.043 |
0.976668 |
0.011666 |
8.558 |
7.336 |
4.00 E+04 |
0.006 |
0.034 |
0.984487 |
0.007757 |
20.23 |
15.651 |
6.50 E+05 |
0.0004 |
0.017 |
0.989747 |
0.005127 |
152.3 |
11.88 |
6.50 E+05 |
0.004 |
0.029 |
0.995294 |
0.002353 |
91.5 |
155.6 |
7.00 E+05 |
0.01 |
0.038 |
0.997164 |
0.001418 |
68.47 |
482.8 |
8.00 E+06 |
0.0000001 |
0.008 |
0.998186 |
0.000907 |
235.1 |
0.026 |
2.50 E+07 |
0.00001 |
0.009 |
0.999006 |
0.000497 |
405.0 |
8.145 |
Re |
/D |
(75) |
n |
r1/R |
(y@r1)/D |
y+ @ r1 |
y+ @ |
4.00 E+03 |
0.0000001 |
0.0404 |
4.97 |
0.9550 |
0.0225 |
6.4000 |
2.8435 E-05 |
4.00 E+03 |
0.001 |
0.0412 |
4.93 |
0.9568 |
0.0216 |
6.2088 |
0.2871 |
1.00 E+08 |
0.00003 |
0.0097 |
10.1 |
0.9995 |
0.0003 |
881.99 |
104.52 |
1.00 E+08 |
0.013 |
0.0416 |
4.90 |
0.9998 |
9.24 E-05 |
666.22 |
93735.0 |
Re |
/D |
(75) |
n |
r1/R |
(y@r1)/D |
y+ @ r1 |
y+ @ |
4.00 E+03 |
0.0000001 |
0.0404 |
4.97 |
0.9550 |
0.0225 |
6.4000 |
2.8435 E-05 |
4.00 E+03 |
0.001 |
0.0412 |
4.93 |
0.9568 |
0.0216 |
6.2088 |
0.2871 |
1.00 E+08 |
0.00003 |
0.0097 |
10.1 |
0.9995 |
0.0003 |
881.99 |
104.52 |
1.00 E+08 |
0.013 |
0.0416 |
4.90 |
0.9998 |
9.24 E-05 |
666.22 |
93735.0 |
Table 3: r1/R and along with corresponding y+ values for a rough pipe with Re and values for extreme y+
IV. DISCUSSION
The results in Table 1 and Table 2 show that r1 is a separation between two flow regions. r1 clearly separates the outer region from the wall region. Table 1 shows that for turbulent flows in smooth pipes, the normalized distance from the wall at which the boundary between the two regions occur is always greater than 30 and increases logarithmically with increase in Reynolds number. Turbulent flow in a smooth pipe is therefore expected to have both a viscous sublayer and a buffer zone. Experimental investigators have reported that the wall/outer region boundary location is dependent on Reynolds number [1] [2], but not as detailed as the result presented here. For turbulent flows in rough pipes, the results of the analysis shows in Table 2 that the normalized distance from the wall at which wall/outer region boundary exists is a function of the relative roughness of the pipe. In more details, the normalized distance from the wall at which the wall/outer region exists may increase or decrease depending on the combination of variation of the Reynolds number and relative roughness. The distance y represented by non-dimensional values y/D and y/R decreases with either increase in relative roughness or increase in Reynolds number. The observed trends can be explained by the relation between the variables as presented in equation
(31) which shows that y+ is directly proportional to the product of Re and the square root of f and f reduces with increase in Re before the flow is completely turbulent but always increases with increase in /D. Extreme values of y+ obtained (see Table 3) shows that y+ can go as low as 6.2, so for a turbulent flow in a rough pipe, there may not always be a buffer zone (5 < y+ < 30).
Though y+() may be greater than y+(r1) of y+ =5, it should not be used as a criteria for determining whether the smooth pipe
friction coefficient equation should be used, rather the assumption should be made only when /D is extremely low such that
()(0.725) 0.5 (76)
in order to ensure that the error due to the assumption is less than 2.5%. It is assumed that empirical friction coefficient eqution such as equation (75) is developed from experimental data that absorbed the effect of whether y+() is greater or less than 5.
At the pipe wall, the turbulent flow is characterized by bursting from the rough wall [14] and sweeping from upstream [21] which all contribute to the turbulence production process. Enough information on the wall boundary condition is not yet available for a direct solution of the flow equations to find r1 and directly. Case 1 analysis for the smooth pipe is more accurate than case 2 analysis for the rough pipe, since the effect of required more work and approximation as presented. The equations obtained for case 2 could not be used to check that it drops to the equations of case 1 by writing /D = 0 since the validity of the empirical equations used did not cover /D = 0 in its range of validity without significant error.
Additionally, selected equations which were presented in small fonts to fit the half page columns in section II have been expanded in font size and present in a full page column in the appendix.
CONCLUSION
Theoretical analysis of turbulent flow profile in pipes has been made. Equations, which include the power-law and other forms of solution to the Navier-Stokes equation, were fitted to sections of the flow field to eliminate the limitations of the power-law at the center and at the wall. The outer region and outer region boundary or interface location was found for both cases of turbulent pipe flow in a smooth pipe and in a rough pipe. The boundary layer location trend and variation with Reynolds number and relative roughness was presented. The normalized distance from the wall to the outer/wall region boundary was found to occur at 21- 295 for smooth pipes and 6 882 for rough pipes with the combination of Re and /D determining its exact location.
This work calls for further experimentation and measurements in the near-wall region and at the wall that will provide information for further analysis. The result of this work can also be used as a guide during experimentation to know where to focus on for measurements.
REFERENCES
[1] M. C. Potter, D. C. Wiggert and B. Ramadan, Mechanics of Fluids, Stamford: Cengage Learning, 2010. |
[2] P. H. Alfredsson, R. Orlu and P. Schlatter, "The Viscous Sublayer Revisited-Exploiting Self-Similarity to Determine the Wall Position and Friction velocity," Experimental Fluids, vol. 51, pp. 271-280, 2011. |
[3] J. Sternberg, "A Theory for the Viscous Sublayer of a Turbulent Flow,"
Journal of Fluid Mechanics, vol. 13, no. 2, pp. 241-271, 1962. |
[4] P. A. Chevrin, H. L. Petri and S. Deutsch, "The Structure of Reynolds Stress in the Near-wall Region of a Fully Developed Turbulent Pipe Flow," Experiments in Fluids, vol. 13, pp. 403-413, 1992. |
[5] J. Sternberg, "A Theory for the Laminar Sublayer of a Turbulent RUNSTADLER, "The Structure of Turbulent Boundary Layers," Flow," Ballistic Research Laboratories, Arberdeen PG, 1961. Journal of Fluid Mechanics, vol. 30, no. 4, pp. 741-773, 1967. |
[6] J. Laufer, "The Structure of Turbulence in Fully Developed Pipe Flow," [15] A. A. Townsend, The Structure of Turbulent Shear Flow, London:
N. B. S. Rep, 1954. Cambridge University Press, 1976. |
[7] C. Lee and J.Kim, "Control of the Viscous Sublayer for Drag [16] P. Chevrin, "The Structure of Reynolds Stress in the Near Wall Region Reduction," Physics of Fluids, vol. 14, no. 7, pp. 2523-2529, 2002. of a Turbulent Pipe Flow," The Pennsylvania State University, 1988. |
[8] T. I. Taylor, "Note on the Distribution of Turbulent Velocities in a [17] B. S. Petukhov, "Heat Transfer and Friction in Turbulent pipe Flow Fluid near a Solid Wall," vol. 164, p. 476, 1932. with Variable Physical Properties," Advances in Heat Transfer, vol. 6, |
[9] H. Klages, "An Experimental Investigation of a Probe Interference in pp. 503-564, 1970.
the Near Wall Region in a Turbulent Channel Flow," NASA/ADS, [18] B. J. McKeon, C. J. Swanson, M. V. Zagarola, R. J. Donnelly and A. J. 1981. Smits, "Friction Factors for a Smoooth Pipe Flow," Journal of Fluid |
[10] J. Naughton, J. Robinson and V. Durgesh, "Oil-Film Interferometry Mechanics, vol. 511, pp. 41 – 44, 2004.
Measurement of Skin Friction – Analysis, Summary and Description of [19] A. T. Popovich and R. L. Hummel, "Experimental Study of the Viscous Matlab program," in 20th International Congress on Instrumentation in Sublayer in Turbulent Pipe Flow," AIChE Journal, vol. 13, no. 5, pp. Aerospace Simulation Facilities, 2003. 854 – 860, 1967. |
[11] S. Grobe and W. Schroder, "Mean Wall-Shear Stress Measurement [20] S. E. Haaland, "Simple and Explicit Formulas for the Friction Factor in Using the Micro-Pillar Shear-Stress Sensor MPS3," Measurement Turbulent Flow," Journal of Fluids Engineering, vol. 105, no. 1, pp. Science and Technology, vol. 19, 2008. 89-90, 1983. |
[12] S. Grobe and W. Schrode, "The Micro-Pillar Shear-Stress Sensor [21] C. R. Corino and R. S. Brodley, "A Visual Investigation of the Wall MPS3 for Turbulent Flow," Sensors, vol. 9, pp. 2222-2251, 2009. Region in Turbulent Flow," Journal of Fluid Mechanics, vol. 37, pp. 1- |
[13] L. M. Hocking, "A Moving Fluid Interface. Part 2. The Removal of the 30, 1969.
Force Singularity by a Slip Flow," Journal of Fluid Mechanics, vol. 79, no. 2, pp. 209-229, 1977. |
[14] S. J. KLINE, W. C. REYNOLDS, F. A. SCHRAUB and P. W. |
APPENDIX
A. Expanded form selected equations which were compressed to fit the required two column pages
1.46110.8885
1
2
11
1.46110.8885
1
11
( )( 1)(2 1(1 1)
(1( 1) )(1 1) )
( 2 )((1 1)
( 1)ln ( 1)(1 1) )
1 2 = (1 (
) + 2 (
) ) (27)
8
(1(1)2+2(1 2ln (1))
(1(1 2+2(1 2ln (1))
)
) )
1
2
11
1
11
( 1)(2 1(1 1)
(1( 1) )(1 1) )
((1 1)
( 1)ln ( 1)(1 1) )
= 2 (
) + 2 (
) (28)
23.3776
0.1115(1(1 2+2(1 2ln (1))
0.1115(1(1)2+2(1)2ln (1))
) )
(
)
1
11 1
1
2
11 1
( )((1 1)
( 1) ln( 1)(1 1)
( 1)(2 1(1 1)
(1( 1) )(1 1) ))
2()(1)(21(1 1)1 (1(1)2)(1 1)1)
=
2
(53)
(1(1 2+2(1 2ln (1)) (1(1)2+2(1)2ln (1))
) )
1.46110.8885
1
2
11
3
1.46110.8885
1
11
( )( 1)(2 1(1 1)
(1( 1) )(1 1)
)(1 )
( )((1 1)
( 1)ln ( 1)(1 1) ) 4
= 16
1 1 2.9222
1 1 2.9222
2 2
1.8885
1+1
2 + 2
2 2
1.8885
1+1
(1 )
2
2
(1(1) +2( ) ln ( ))[0.96420.0122 ( )
((2)+1)]
(1(1) +2(1) ln (1))[0.96420.0122 2.9222 ()
((2)+1)]
(
(1+2)(1+)
(
(1+2)(1+)
>
) )
(65)
1.46110.8885
1
11 1
1
2
11
2 2
( )((1 1)
( 1) ln( 1)(1 1)
( 1)(2 1(1 1)
(1( 1) )(1 1)
))( )(2 ( ) )
= 32
2
1
2
(69)
(1(1 2+2(1 2ln (1))(10.96420.0122 2.92221.8885()1+((2)+1))
) )
(1+2)(1+)
5
1
2.92221.8885 1+
1
2 2
2
3
4
1
0.0122 2.92221.8885 1+
1
2 2
0.0122
0.0122
(122) [0.9642 (1+2)(1+) ( )
((2 )+1 )]
1
1
(( ) 2( ) +( ) )(10.9642
2 2 2
(1+2)(1+) ( )
((2 )+1 ))
16
16
=
1
1
1.8 4
2 3
+ 2
1.1284(1 )
(1) 0.6225(1 )
(1) 2
(0.8619(1 1)1.9)()(2()2)
( (
)) ( (
))
(71)
5
1
2.92221.8885 1+
1
2 2
2
3
4
1
0.0122 2.92221.8885 1+
1
2 2
1 = 1
(1 ) [0.96420.0122 ( )
4 3
4 3
(1+2)(1+)
((2 )+1 )]
) 2( ) +( ) )(10.9642
2 2 2
((
((
+ 1
(1+2)(1+) ( )
((2 )+1 ))
(72)
0.95
0.5(1 1)
16
1.12843(1) 0.62253(1)
2
2
3 2
(0.8619 )( )(2 ( ) )
( ( )) ( (
))