
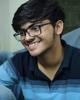
- Open Access
- Authors : Abhishek Sharma
- Paper ID : IJERTV10IS050070
- Volume & Issue : Volume 10, Issue 05 (May 2021)
- Published (First Online): 14-05-2021
- ISSN (Online) : 2278-0181
- Publisher Name : IJERT
- License:
This work is licensed under a Creative Commons Attribution 4.0 International License
Design Improvement of Disc Brake with Guided Pathways for Better Air-Flow
Abhishek Sharma
Department of Mechanical Engineering Delhi Technological University
New Delhi, India
AbstractThis paper is based on analyzing the airflow characteristics in conventional slotted and drilled disc brake rotors vs a virtual prototype with guided pathways extruded out of the main rotor body with cylindrical fins and curved vanes present between two plates of rotor. SOLIDWORKS 2018 and ANSYS 18.2 was used for modelling and running simulations on both conventional and prototype design. The FEA method is used to find out airflow patterns during spinning of wheels on different time steps. During a motorsport event cars run on a track with both sharp turns and long stretch of road and better braking action can be really advantageous. As brakes are generally air- cooled and with continuous braking through an event can raise temperature of rotors quite high which could result many possible circumstances like thermo-elastic vibrations, heating-up of brake fluids, wearing out of rotor surface and also it give rise to thermo- mechanical stresses which lowers the fatigue life of any component which eventually results in failing or inefficiency on braking system. Better air-flow characteristics potentially have better and faster cooling rate of rotors which will support the idea for this prototype. So, to test how guided pathways in brake rotors affect airflow I have carried out simulation studies on my prototype and compared it with rotors available to purchase. Results of the simulations turned out be better as compared one of most used type of rotor (vanned with slots and drilled holes) as brakes are sucking air themselves. So, this design will work better even if there arent brake ducts present in car as they are normally found in sports car.
KeywordsANSYS; Brake Rotor Design; Airflow; FEA; Conventional Design ; CFD Analysis
-
INTRODUCTION
Ever since automobiles have people want to take them as fast around race tracks and engineering masters are putting their lot of effort in making cars fast and fun to drive but if the vehicle cannot stop efficiently or in time its all worthless because safety of driver is topmost priority of any automobile manufacturer. Evolution of brakes had been done in previous years and from wooden brake pads then drum brakes and now disc brakes their design is continuously improving. In 1953 formula one race automobile experts used disc brakes in their car and won that race because when you can apply brakes later and still be able to take a perfect turn, it will reflect in the lap time. For any motorsport event where, braking conditions are very harsh it is very important for drivers safety that brakes should work properly and efficiently.
In a disc brake system, rotors provide the surface for absorption and dissipation of heat at the time of braking so besides brake caliper and type of brake pads a lot of factors of braking depend on rotor characteristics. During the event of braking as pistons
in the caliper squeeze the rotor and with that it comes under static and dynamic loads, thermal and fatigue stresses are generated and with them sometimes it also accompanies by inducing small vibrations on rotors. And when car takes a turn accompanied by braking action at the time both transient conduction and convection behavior of rotors comes into the picture where it is important how thermal load is distributed across the surface of rotors and how much time it will take to cool down to a optimum temperature because if temperature of brake is still high then brakes will not work efficiently and slowly will lead to thermo-elastic deformation which alters the contact pressure distribution when brakes are running very hot inducing vibrations in rotors due to uneven braking pressure.
-
Types of Brakes
As far as braking of a car is considered there are different types of brake rotors for different cars depending on lightweight or heavy weight, what kind of vehicle it is, a sports car or a family car and also depending on different types of weather conditions as per their optimum performance.
TABLE I. TYPES AND APPLICATION OF BRAKE ROTOR[1]
S.No.
Types of Disc Brake Rotor
Solid/Vented
Application
1.
Drilled only
Street, all-weather rotor
2.
Blank & Smooth
Street and light weight vehicles
3.
Slotted only
Street, Towing/Hauling, Off- Road
4.
Slotted or Grooved
Trucks and off-road vehicles.
5.
Dimpled
Sports car, weight reduction
6.
Waved
Race & Sports vehicles
Dissipation of heat through solid objects occurs with convective heat transfer and radiation but usually the amount of radiative heat transfer is low as compared with convective heat transfer so the designs mainly focus on the same.
Drilled disc Rotors: As the name suggests there are holes drilled through the rotors which allows hot gases to pass and gives rotors more surface area to come in contact with atmospheric air to cool down. The holes also allow the water to get out easily when vehicle is running in rain and there is water around brakes
Vented Rotors: They provide more surface area as compared to drilled rotors because the more surface area of hot metal will come in contact with fluid more will be heat dissipation.
They currently use seventy different rib configurations in disc brake rotors. These are straight, vanned or segmented. These are some combinations the two types of rotors discussed. All these designs are focusing on increasing contact surface area keeping strength of rotors appropriate according to the vehicles.
-
Literature Review
Previous understanding of the basics of fluid mechanics and heat transfer coupled with knowledge of flows numerical modeling, CFD has significantly gained preference in the automotive industry design process as tool for predicting complex flow and heat transfer behavior in regions where otherwise very laborious and time consuming by a combination of nodetosurface and surfaceto surface contact elements [2].
Cycle braking with phase of idles after each braking can raise temperature up to 708.79oC and Driving cycle with fourteen repeated braking can raise temperature up to 1244oC [3]
Heat Transfer Coefficient: If the temperature profile T (x, y) in the thermal boundary layer is known, then the heat flux
where k is the thermal conductivity of the fluid.
In practice, a local heat transfer coefficient h(x) is defined as
by combining these equations, we get
& mean heat convective heat transfer as
[4] -
Objective
Various designs have been created to maximize the surface contact area to increase heat dissipation from brake rotors and there is still room for new and innovative designs. Even if we increase the surface area by adding extra vanes or making slots through rotors it doesnt mean that the whole area will come in contact with cold/atmospheric air. It is obvious that after some amount of heat is lost by rotors the air around will warm up the air and the temperature difference will reduce. So, the objective of this paper is to design a prototype rotor which will b able to pull air itself as it will rotate with the wheel. This will make
extra surface useful as it will be able to release heat from brakes to the air more efficiently.
-
-
METHODOLOGY
-
Inspiration of Design
FIGURE1 SCHEMATIC WORKING OF CENTRIFUGAL COMPRESSOR
In fluid machinery we have seen how a centrifugal compressor works. It increases the pressure of fluid by action of centrifugal force and creating a pressure difference between center and circumferential edge. A similar approach has been taken in this design, when vanned rotors rotate they also create pressure differences between outer and inner edges. This phenomenon creates motion of fluid (due to pressure difference) and actually helps to circulate the air but if we provide an opening and guided path for the air it will reach to the vanes more efficiently and will help to cool down rotors faster because it motion of air particles will decide the convection coefficient of the disc plates (as it depends more on geometric and fluid flow rather than material properties).
Figure 1 shows schematic diagram how fluid flow occurs in a centrifugal pump. This diagram provided a perception how things need to work in the prototype rotor
FIGURE 2 SCHEMATIC AIR-FLOW ACROSS ROTOR
In Figure 2 (standard vanned rotor with drilled holes and slots) it can be seen that to direct that flow of air to vanes there should be a guided path cut out from it.
FIGURE 3 FRONT VIEW OF PROTOTYPE
FIGURE 4 BACK VIEW OF PROTOTYPE
-
CAD Model of Prototype Rotor
The cad model is created in SOLIDWORKS 2018 and with using certain dimensions of brake rotors of Ferrari SF90 provided in their specification catalog [6]
Disc
Dimensions (mm)
Outer Diameter
Inner Diameter
Width
Front
398
223
38
Rear
360
233
32
Disc
Dimensions (mm)
Outer Diameter
Inner Diameter
Width
Front
398
223
38
Rear
360
233
32
TABLE 2 DIMENSIONs FOR ROTORs [6]
In cars 70% of weight shifts to front axle while braking also front brakes provide 70% of stopping power. So, this paper will focus on designing front rotor and will be considering only dimensions of front disc only. Also, the prototype design doesnt share any visual similarity with the rotors which are actually used by the car.
Figure 3 & 4 are showing the CAD model on which further analysis will be done to check whether it serves it purpose or not.
-
Design Characteristics
FIGURE 5 SECTIONAL VIEWS
As per the objective of the paper this design have certain geometric features to have better heat dissipation than standard rotors.
FIGURE 6 GUIDED OPENING WITH CYLINDRICAL FINS ARE THERE TO INCREASE SURFACE AREA
Figure 5 shows the guided path profile which has been cut out in such a way that when rotors will rotate there will be low pressure zone near center at that time air will be sucked into it and directly go vanes more efficiently through the path created.
In this way it will move across larger surface area and more heat can be easily dissipated with more airflow across the brakes.
Air will go in axially and come out radially
For ensuring that air flows towards vanes ,small guiding fins have been added at the exit of guided paths which can be seen in figure.
Also, cylindrical fins have been added in space between vanes so that they can dissipate more heat and can also provide structural integrity against squeezing force of brake pads during the action of braking.
-
CFD Simulation
To check the validity of virtual prototype rotor simulating analysis is important to verify that modification in geomtries have any positive impact towards the objective.
For simulation purpose we have used ANSYS 18.2 Fluent for CFD analysis because of its proven capabilty in flow analysis similar to this one.
-
Following assumptions are made before analysis
-
Flow is transient and turbulent.
-
Properties of air are contant and are at standard temperature and pressure condition.
-
Velocity of air in sorrounding is taken zero (to check maximum ability to pull air)
-
-
Methodology is used for CFD analysis
-
Preproccessing
-
Geomtric Modelling
-
Grid Generation
-
Selction of Flow Model
-
Initial and Boundary conditions
-
-
Post processing
-
Streamline Plots
-
-
To create a comparison analysis will be done on both standard and prototype rotors. Both models are meshed using default curvature method with medium element size and all other factors at default (The finer mesh would take more computational time and resources, therefore medium-mesh sizing is used for simulation).
FIGURE 7 MESH DETAILS
In present simulation the flow fields are calculated by solving Realizable k-epsilon turbulence model beause it provides improved predictions for the spreading rate of both planar and round jets and in case of complex turbulent flows. [5]
FIGURE 8 MESHED PREVIEW OF VIRTUAL PROTOTYPE NODES- 555864
ELEMENTS- 2824861
FIGURE 9 MESHED PREVIEW OF STANDARD DESIGN NODES- 713300
ELEMENTS- 3643466
Initial and Boundary condition
-
Surrounding conditions are set to atmospheric with Temperature T(x,y,z,t)=27oC.
-
Pressure is atmospheric.
-
As vehicle moves with 340 kmph the rotational speed of rotors is 328.11 rads/s.
-
-
Structural Intregity
Safety aspect is at top most priority in automotive engineering. So, the new design should have strength equal or near to conventional design because it would be of no use if it fails early.
To find it static structural analysis is done and for that clamping force is calculated when car will go 350 km/hr to 0. Following data is from Ferrari SF90 specication catalogue [6].
TABLE 3 REQUIRED DATA ABOUT THE CAR
1.
Wheel Base
2650 mm
2.
Kerb Weight
1570 kg
3.
Top speed
350 km/hr
4.
Wheel Diameter
508 mm(20
inchs)
5.
Outer Dia of Brake rotor
398 mm
6.
Calliper Piston Dia
64 mm
7.
Coefficient of friction between road and tyre µR
0.4
8.
Coefficient of brake pads
µB
0.5
1.
Wheel Base
2650 mm
2.
Kerb Weight
1570 kg
3.
Top speed
350 km/hr
4.
Wheel Diameter
508 mm(20
inchs)
5.
Outer Dia of Brake rotor
398 mm
6.
Calliper Piston Dia
64 mm
7.
Coefficient of friction between road and tyre µR
0.4
8.
Coefficient of brake pads
µB
0.5
Calclations:
-
Kinetic Energy (K.E.) at top speed= 7*106 Joules
-
ii. Max. Frictional Force = µR mg=1.07812*104 Newtons
-
Stopping Distance (S.D.) = 649.4039 m
-
Braking Force (B.F) = K.E/S.D. = 1.076923*104 Newtons
-
Tangential Force on wheel (Ft) = B.F/4 = 2.6923*103 Newtons
-
Torque on wheel(w) = Ft*Radius of wheel=668.6042 Nm
-
Torque on Disc (B) = (w*R)/r = 853.324 Nm
-
B*Effective Radius = Friction Force (created by brake pads)
-
Friction Force = 4 *µB *N = 5110.145
-
N (Clamping Force) = 2555.0727 Newtons
Now to be at safe side value of clamping force is increased in analysis, which is 3211N and will be used for solving the analysis with rotation speed of 328 rad/s (as of 350 km/hr speed of car). Also, where bolts are used to fix the rotor in car is used as fixed support in analysis.
Figure 10 shows how constraints are applied to the rotors.
Figure 11 shows stress generated in Prototype rotor
Figure 12 shows stress generated in Standard rotor
Figure 13 shows deformations in Prototype rotor
Figure 14 shows deformations in Standard rotor
-
-
RESULTS
In the following figures there are streamline patterns at different time step for both types of design.
For better visual comparison the figures have been put side by side at same time step of both analysis in table 4.
Also, the standard rotor is colored red so it gets easily differentiated.
We compared every 4th step for convenience because with 50 iteration in every step (total 20 steps) it would be difficult to in observe velocities of particles with so many images in small size.
With all these constraints the results of analysis are positive for the prototype design as the value of maximum stress induced in rotor is less of prototype design as compared to conventional rotor. The values of stress generated can be seen in figure 11&12, which are 76.586 MPa for new design and 265.39 MPa for standard design
Also, the maximum deformation occurred on the prototype rotor is less as compared to standard rotor. Values of deformation can be seen in figure 13&14, which are 0.068 mm for new design and 0.076 mm for standard design.
TABLE 4 FLOW CONTOUR AFTER EVERY 4TH STEP
Time Step
Prototype Disc
Standard Disc
1st
4th
8th
12th
16th
The speed across the rotors is more in created model as compared with conventional model which assures better heat dissipation through forced convection heat transfer.
Also, it can be seen that as time is advancing the lesser amount of air is coming out of vanes which means that air inside the vanes will get hotter and heat transfer to air will decrease because there will be less temperature difference between rotor and air in contact which will eventually increase the cooling time for brake rotors.
-
CONCLUSION
Every 4th time step calculated by simulation software of both models have been compared and from flow patterns of both models it quite clearly appealing that with guided path ways cut out from rotors with some slight modification in design features can have better airflow characteristics than normal brake rotors.
Also, with better airflow characteristics and higher speed of flowing air through vanes will help in faster cooling of brake rotors and help to avoid circumstances of over-heating of brakes under continuous application. This could also help in reducing thermo-elastic vibrations induces due non-uniform contact pressure which happens when brakes are at certainly higher temperature.
So, with more precise calculation of area of opening of guided pathways, angle by which they turn air optimized with more surface area and less weight they can used in sports car and even for endurance motorsport events where usually brakes fail due to excessive heat and not enough time to cool down this type design will work better than currently mass-produced disc brake rotors.
-
FUTURE SCOPE
This paper represents the benefits of having guided pathways through rotors for better air-flow through vanes inside it. With the help of this virtual prototype the difference between average convective heat transfer coefficients of both can be found and with them transient cooling behavior of brakes can be studied. If the model shows significant improvement it can be adopted for both family and sports car but for that a easy way to manufacture will be required. So. it will be a challenge to manufacture this type of rotor at considerable cost as the design is expensive for production
REFFERNCES
-
Atharva Kulkarni, Rohan Mahale, Impact of Design Factors of Disc Brake Rotor on Braking Performance ISSN: 2278-0181 IJERTV9IS060817 Vol. 9 Issue 06, June-2020
-
J. Abdo: Experimental Technique to Study Tangential to Normal Contact Load Ratio, Tribology Transactions, Vol. 48, No. 3, pp. 389
-
Ali Belhocine, Abd rahim abu bakar, Mostefa Bouchetara, Numerical Modeling of Disc Brake System in Frictional Contact Vol. 36, No. 1 (2014) 4966 Tribology in Industry
-
P.K. Nag Heat and Mass Transfer Forced Convection, The McGraw Hill Publicaion
-
Sanket Kothawade, Aditya Patankar, Rohit Kulkarni and Sameer Ingale, DETERMINATION OF HEAT TRANSFER COEFFICIENT OF BRAKE ROTOR DISC USING CFD SIMULATION, International Journal of Mechanical Engineering and Technology (IJMET) Volume 7,
Issue 3, MayJune 2016, pp.276284, Article ID: IJMET_07_03_025
-
https://corporate.ferrari.com/sites/ferrari15ipo/files/pr_ferrari_sf90
_stradale_gbr.pdf