
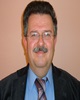
- Open Access
- Authors : Statharas J. C , Vlachakis N. W
- Paper ID : IJERTV10IS050398
- Volume & Issue : Volume 10, Issue 05 (May 2021)
- Published (First Online): 01-06-2021
- ISSN (Online) : 2278-0181
- Publisher Name : IJERT
- License:
This work is licensed under a Creative Commons Attribution 4.0 International License
Navier-Stokes Exact Solutions Morphologies “Behaviour” in Pipes and Coaxial Cylinders using Simple Closed Forms
Statharas J. C.
Professor, General Department of Engineering Science ,
National & Kapodistrian University of Athens , 34400 Psachna Evias, Chalkis Greece (corresponding author)
Vlachakis N. W. ,
Invited Researcher ,
AbstractIn this article, new morphologies of exact solutions of the full set of NavierStokes equations in the presence of porous boundaries of axisymmetric rotating geometries are presented. Such flows have significant industrial applications including filtration and particle separation.
KeywordsNavier-Stokes, porous cylinder, Bessel fumction, rotating pipes
-
INTRODUCTION
In the present investigation we have considered the flow in pipes and between porous rotating cylinders. The effect of suction and injection is studied on the walls of pipes and of the cylinders. Several authors have analysed [ 1,2,3,4,5,6,7,8 ] all these flows for the NavierStokes equations for incompressible flow, written in polar-coordinates. In a new attempt to resolve these equations strong analytically with closed forms, according to an Polyanin-Aristov assumption [9], it is assumed that the effect of the body force by mass transfer phenomena is the porosity of the porous boundary in which the fluid moves. The effect of porous boundaries on the viscous flow is examined for two different cases. The first one examines the flow between two rotated porous cylinders and the second one discusses the swirl flow in a rotated porous pipe.The developed solutions are of general application and can be applied to any swirling flow in porous axisymmetric rotating geometries.The exact solutions are obtained by employing the Bessel functions for the case of three dimensional unsteady flow between rotated porous cylinders and for the case of unsteady swirl flow in rotated porous pipes.
-
MATHEMATICAL AND PHYSICAL MODELLING
For the first case study we assume the flow of a Newtonian fluid within a rotating porous cylindrical pipe (Figure 1), and for the second case study the flow through an annulus formed between two rotating porous cylinders (Figure 2). . For the two cases, the basic equations are the mass conservation equation and the equations of motion (NavierStokes), in a cylindrical system of coordinates r,,z where the z axis lies
-
Conditions in a rotating pipe
Figure 1. Flow within a rotating porous pipe
-
Axial flow conditions in two rotating porous cylinders
Figure 2: Rotating porous cylinders
-
-
GOVERNING EQUATIONS
Considering that the flow modelling describes the motion of a homogeneous incompressible Newtonian fluid, the Navier Stokes equations have as follows:
ur + ur + uz + 1 u =0
along the centre of the symmetry, r is the radial distance and
is the peripheral angle.
r r
z r
(1)
u u u2
u 1 P
-
3b. Time-dependent flow between rotating coaxial
r +u r +u r = +
r z
r z
cylinders with suction-injection at the porous walls. (Version
t r r
2u 1 u
z r
u 2 u 2)
[ r +r r + r ]
r2
r r r2 z 2
(2)
The exact solutions The boundary conditions
u +u u + ur u +u
u = 1 1 P +
t r r r
z z r r
u = A +Cekt s in
2u 1 u u
2 u
r r
ur (r = )=V 1, ur (r =1)=V 2 (14)
[ ++ ]
r2
r r r2
z2
(3)
u = A +C ekt co s u
(r= )= W 1
, u (r =1)= W 2
uz +u
uz +u
uz = 1
P +
r
R1
R2 (15)
t r r
2
z z z
2
uz=0
(16)
[ uz + 1
uz + uz ]
r2
r r
z2
(4)
IV.4. One-dimentional flow in centrifugal pumps impellers
IV. EXACT SOLUTIONS SETS AND THEIR OWN BOYNDARY CONDITIONS .
The exact solutions The boundary conditions
-
Time-dependent swirling flow in a rotated porous pipe
u = J
e
e
bz
1
u (r= )= W 1
R1
, u
(r =1)= W 2
R2 (17)
The exact solutions The boundary conditions
bz k t 2
bz k t 2
uz =A J 0 e e + B (1r ) uz (r=0 )=Umax , uz (r=1)=0 (5)
ur =0 (18)
uz =0 (19)
0.5 ( J 2 + J 2) e2 b z=p
b z
kt u (r =0)=0 , u ( r=1)=V
0 1
p p
p J 2 e2bz
(20)
ur = A J 1 e e
r r
(6)
=0 ,
z =0 ,
= 1
r r (21)
u C ekt
u ( r=1)= W
= r
R (7)
From the pressure field described by (20) and (21) for z=0, one can derive the manometer head for any centrifugal pump. This
-
Time-dependent axial flow between two coaxial porous rotating cylinders
The exact solutions The boundary conditions
derivation will appear in the next publication of the authors.
-
-
REFERENCES
-
Basant K. Jha and Dauda Gambo, 2021, Hydrodynamic effect of slip
u = A J
eb z ek t +B( 1r2 ) u (r= )=0 , u (r =1)=0
boundaries and exponentially decaying/growing time-dependent
z
u = A J
0 z
eb z ekt + C
z (8)
pressure gradient on Dean flow, Journal of the Egyptian Mathematical Society 2021.
-
U. K. Sarkar and Nirmalendu Biswas, 2021, Exact and limiting
r 1 r
C ekt
ur (r = )=V 1, ur (r =1)=V 2 (9)
W 1 W 2
solutions of fluid flow for axially oscillating cylindrical pipe and annulus, Applied Sciences 2021, https://doi.org/10.1007/s42452-021- 04192-5
u =
u (r= )=
r R2
, u (r =1)= R
2 (10)
-
Bchara Sidnawi, Sridhar Santhanam and Qianhong Wu, 2019, Analytical and Numerical Study of a Pulsatile Flow in a Porous Tube, Journal of Fluids Engineering, ASME DECEMBER 2019,
IV.3a. Time-dependent flow between rotating coaxial cylinders with suction-injection at the porous walls. (Version 1)
The exact solutions The boundary conditions
u = A +Cekt s in
Vol. 141, https://fluidsengineering.asmedigitalcollection.asme.org .
-
Alexander V.Koptev, 2020, Exact Solution of 3D NavierStokes Equations, Journal of Siberian Federal University. Mathematics &and Physics 2020, 13(3), 306313.
-
Dyck, Nolan J. and Straatman, Anthony G., 2020, "Exact solutions to the three-dimensional Navier-Stokes equations using the extended Beltrami method". Transactions of the ASME , Vol. 87, JANUARY 2020. https://ir.lib.uwo.ca/mechanicalpub/4
-
Irene Daprà , Giambattista Scarpi, 2015, Unsteady flow of fluids with
r r
ur (r= )=V 1, ur (r =1)=V 2 (11)
arbitrarily time-dependent rheological behaviour, Journal of Fluids Engineering. Received December 03, 2015.
u =C ekt co s
u (r= )= W 1
R1
, u
(r=1)= W 2
R2 (12)
uz=0 (13)
-
Konstantin Ilin and Andrey Morgulis, 2019, On the stability of the Couette-Taylor flow between rotating porous cylinders with radial
V 2
V 1 R
flow, European Journal of Mechanics. B/Fluids.December 2, 2019.
-
Eric C. Johnson and Richard M. Lueptow, 1997, Hydrodynamic
1 1
1
1 t a n
stability of flow between rotating porous cylinders with radial and axial
flow, Phys. Fluids 9 (12), December 1997.
-
A. D. Polyanin and S. N. Aristov, 2011, A New Method for Constructing Exact Solutions to Three_Dimensional NavierStokes and Euler Equations, Theoretical Foundations of Chemical Engineering,
V V 2
=
=
W 1
-
R2
(32)
2011, Vol. 45, No. 6, pp. 885-890.
2 1 1
t a n
APPENDIX
FLOW FIELD BETWEEN ROTATING COAXIAL CYLINDERS WITH SUCTION-INJECTION AT THE POROUS WALLS (Figure 3).
Figure 3. Rotating coaxial cylinders
C K rekt s in + A2 + A C ekt s in =p 2 r2 r |
C K ek t s in A2 AC ekt s i n p = r3 r2 r |
C K rekt co s AC ekt co s p + r = |
Version 2.
u = +C e s in
u = +C e s in
(33)
(34)
(35)
(36)
A
A
kt
kt
r
r
r
r
(37)
Version 1.
u = +C e s in
u = +C e s in
A
A
kt
kt
r
r
r
r
(22)
ur (r =)=V 1 (38)
t=0
ur (r=1)=V 2 (39)
ur (r =)=V 1 (23)
t=0
A +C s in =V
1
(40)
ur (r =1)=V 2 (24)
A +C s in =V
A A
=V 2V 1
A= V 2V 1
1 1
(41)
1
(25)
V V
A+C s in =V
2 (42)
1 1
1 1
V 2A
V 2A
A A =V V A= 2 1
2 1
2 1
V V 2
2 1
2 1
A+C s in =V 2 (27)
( 1 )
1
1
1
V 2V 1
V 2V 1
1
1
1
1
(26)
V
V
V
C= s in = s in
V 2 1
= s in 1
(43)
C= V
2A
= 1 (V
2
2
V 2V
1 )= 1
2
1
u = A +C ekt co s
u = A +C ekt co s
s in
s in
1 1
u =C ekt co s
u =C ekt co s
s in
1 1
(28)
(29)
r
r
u (r= )= w1
R1
w
= A + C c os , t =0
(44)
(45)
u (r = )=
w1
= C co s , t =0
u (r=1)=
2
R2
= A+ C co s , t =0
(46)
R1
(30)
W =( A + C co s )R
, t =0
w 2 1 1
(47)
u (r =1)=
R 2
= C co s , t =0
(31)
W2=( A + C co s ) R2
, t =0
(48)
C K rekt s in + +
kt
=p
C K rekt s in + +
kt
=p
A
A
2
2
r2
r2
A Ce (cos+ s in )
r
A Ce (cos+ s in )
r
(49)
2
2
C K e s in
C K e s in
kt 2A
kt 2A
A C e
A C e
kt
kt
r3
r3
(cos+sin )= p
(cos+sin )= p
r2
r2
r
r
(50)
C K rekt c os +
C K rekt c os +
A C ekt (sin +co s )
r
A C ekt (sin +co s )
r
=
=
p
p
(51)