
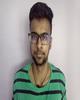
- Open Access
- Authors : Srivenkateshwar Sankaranarayanan , Yadav Pradeep Yogesh , Rajkumar Ashok Tekale Patil , Nehal Tandel, Rugved Raorane
- Paper ID : IJERTV10IS050350
- Volume & Issue : Volume 10, Issue 05 (May 2021)
- Published (First Online): 02-06-2021
- ISSN (Online) : 2278-0181
- Publisher Name : IJERT
- License:
This work is licensed under a Creative Commons Attribution 4.0 International License
Reverse Engineering of Bicycle
Srivenkateshwar Sankaranarayanan, Yadav Pradeep Yogesh, Nehal Tandel, Rugved Raorane
Student: Mechatronics Department, Terna Engineering College,
Nerul, University of Mumbai, India
Rajkumar Tekale Patil
Professor: Mechatronics Department, Terna Engineering College,
Nerul, University of Mumbai, India
Abstract:-In the automobile industry, Reverse Engineering is the process of collecting design data from automotive parts and reproducing it with modification. It can also be used to learn the process and subsequently improve the design. In the present work CAD model of an old unused Bicycle is created using the technique of reverse engineering and applying some conditions to the same model of bicycle to compare their behaviour in different scenarios. The framework of this work is to learn and apply the concept of reverse engineering, CAD modelling, FEA and to apply this to a bicycle and try to make it efficient.
I. INTRODUCTION
There are broadly two types of engineering, one is forward engineering and the other one is reverse engineering. These involve the process of designing, manufacturing, assembling, and maintaining products and systems. Reverse engineering (RE) is a vital brand especially in the geometrical design and manufacture application area, and this technique has been widely recognized as a key step in the product development cycle. It is the process by which an artificial object is deconstructed to reveal its design, architecture, code, or to extract knowledge from the object. It is similar to scientific research; the only difference is the scientific research occurs for a natural phenomenon.
It is applicable in fields of
-
Computer engineering
-
Mechanical engineering
-
Electronic engineering
-
Chemical engineering
This study tries to examine the stress response and displacement of bicycle frames using models and then analyze solid structures. The material used in this study is Steel AISI 1202.A structural analysis is an essential aspect for evaluating the strength and existence of the frame structure, which will be used for structural optimization
as quite just mathematical theory. These mathematical principles of FEA are useful in different sectors, like computational fluid dynamics or CFD. In this study we are focusing on structural analysis .To run a FEA simulation first a mesh is generated . This is a way of transcribing a 3D object into a series of mathematical points that can then be analysed. The density of the mesh can be changed based upon how complex or simple a simulation is needed. Calculations are run every single element or point of the mesh and so combined to form up the general outcome for the structure. Since the calculations are done on a mesh, instead of everything of an object ,it means some interpolation must occur between the points. These approximations are usually within the bounds of what's needed. The points of the mesh where the info is understood mathematically are mentioned as nodal points and have a tendency to be grouped around boundaries or other areas of change in an object's design.
III. METHODOLOGY
This project has been divided into 7 modules-
It is initiated with disassembling the bicycle followed by measurement of the parts ,later CAD model is created for the disassembled parts followed by assembling and FEA of model under different scenario.
The detailed flow chart of the reverse engineering process is mentioned below-
Disassmebly of
bicycle Taking dimensions of
bicycle parts
II. BACKGROUND
Finite Element Analysis or FEA is that the simulation of a natural phenomenon employing a numerical
Creating CAD
model
caluclations of bicycle
assembling the models
mathematic technique named as the Finite Element Method, or FEM. This process is at the core of engineering , also as a range of other disciplines. It is also one among the key principles utilized in the development of simulation software. Engineers can use these FEM to scale back the quantity of physical prototypes and run virtual experiments to optimize their designs. This practical intention of the methodology meant that from the start , these methods were designed
parts different scenario FEA of Bicyle models
Comparing them and suggesting the modification
-
DISASSEMBLING OF BICYCLE:
The bicycle had taken to the bicycle shop for disassembling it. The tools that are used to disassemble are
-
D/F 12111 Collet/Tip Wrench
-
Long 5/16 Open Ended Wrench
-
Small Narrow Flat Head Screwdriver
The parts from bicycle after disassembling include-
-
Front and back sprocket
-
Chain
-
Frame body
-
Frame bar
-
Handle bar
-
Handle grip
-
Bearing
-
Rim
-
Wheel hub
-
Rubber tyre
-
Crank
-
Pedal with shaft
-
Brake lever
-
Brake pad
-
V brake
-
Axle
-
Seat with clip
-
Nut and bolt
-
-
-
TAKING MEASURMENT
The disassembled parts have been measured using vernier calliper and inch tape. The measurements were recorded and was used for creating the CAD model of bicycle. It had also been documented for further reference or studies.
-
CREATING CAD MODEL AND ASSEMBLING
Creating 2d
sketch of sprocket with the given dimensions.
Making extrusion of inner side
Creating second extrusion
Creating extrusion of teeth
Final model of
back sprocket
Creating 2d
sketch of sprocket with the given dimensions.
Making extrusion of inner side
Creating second extrusion
Creating extrusion of teeth
Final model of
back sprocket
Back sprocket
Front sprocket Crank
Creating 2D sketch of front sprocket using recorded data and
Extruding the sketch
Making circular pattern and extruding it
Creating sketches of
teeth and extruding it
Using pattern command to
create an extrusion pattern of teeth
Final model of front sprocket
Sketch of crank has been drawn by commands of circle, arc, trim etc
Extrusion of the sketch has been done.
Another sketch has been created on side of crank.
Extrusion of sketch has been done.
Fillet command has been used .
Creating 2D sketch of front sprocket using recorded data and
Extruding the sketch
Making circular pattern and extruding it
Creating sketches of
teeth and extruding it
Using pattern command to
create an extusion pattern of teeth
Final model of front sprocket
Sketch of crank has been drawn by commands of circle, arc, trim etc
Extrusion of the sketch has been done.
Another sketch has been created on side of crank.
Extrusion of sketch has been done.
Fillet command has been used .
Creating the 2d sketch of bicycle frame.
With the help of sweep function the frame tube has been created.
Extrusion has been done
With the help of sweep function back side tube has been created
Using sweep function to create a rod on backside
Creating the 2d sketch of bicycle frame.
With the help of sweep function the frame tube has been created.
Extrusion has been done
With the help of sweep function back side tube has been created
Using sweep function to create a rod on backside
Frame
Using sweep function to create the back seat
Making sketches of rear side
Handle
Sketching, sweeping and mirroring of cycle handle
Brake assembly
Chain assembly
Frame assembly
Wheel and rim assembly
Seat
Pedal assembly
Handle assembly
Main assembly
-
CALCULATION OF BICYCLE PARTS AT
DIFFERENT SCENERIO
Acceleration observed=16m/s2 Climbing speed obtain =26.3Km/h Total rolling air resistance=16N Weight of rider=784.8N ~784N Weight of bicycle =127.53N~127N
Total opposing motions and weight acting down on climb is 0.1136times the rider weight i.e., 89N
Therefore ,total resistance to motion 89+16=105N Tractive power =total resistance *forward velocity
=105N*(26.3Km/h)
=105N*7.305N
Tractive power=767N
Size of gear =chain wheel*wheel diameter/18
=54/18*24
=72in Angular velocity of crank=
forward velocity/effective driving wheel radius
=8rad/sec
=76rev/min
Mean torque= tractive power/angular
Velocity
=95.8Nm
Mean torque=/2*mean torque
=150.48Nm
Crank radius =200mm=0.2m
Pedal force=max torque/crank radius Pedal force =150.48/0.
Pedal force=752.4N
Average acceleration=2.6m/s2 Total weight ~910N
Horizontal force at rear wheel=2.6/9.81*pedal force
=2.6/9.81*752
=199.4N~200N
The inertia produced is sufficient so ,choice a higher gear size
Now pedal force=2.75times rider body weight Pedal force =2156N
For normal speeding ,speed =37km/hr
Total resistance (rolling +aerodynamic)=25N Power output=drag force * forward velocity
=25*10.33
=258.32N ~260N
Mean crank torque=260/8=32.5N
*When rider is in seating position-
-
Vertical force is maximum
Pedal in horizontal and lever arm is maximum
-
Vertical force is minimum
Pedal in vertical and lever arm is zero Maximum torque=2*mean torque
=2*32.5
=65N
Maximum pedal force=65/0.2=325N Measured value L1 = 600 mm, L5= 1050 mm
The rider weighed 784 N and the horizontal force required to accelerate the rider at 2.6 m/sec2 was 200 N.
The weight and inertia of the bicycle itself are neglected. These forces are relatively small but could be readily incorporated in the analysis if required. The acceleration is produced by a horizontal force, T of 200 N acting at the rear wheel and this force is transmitted to the riders body by horizontal forces F3 F4., at the handlebars. Horizontal forces at the pedals are ignored.
Thus, for horizontal equilibrium of the bicycle F3+ F4 = 200 N
The vertical reactions at the wheels can be de-ermined by considering the equilibrium of the rider and bicycle together.
R1+R2=784N
Taking moments about B R1*1050+I*L5=784*L1
Hence R1=248N and R2=536N
Although the riders centre of gravity was well forward, the horizontal inertia force increased R1, the reaction at the rear wheel, and helped prevent wheel
spin. In this case wheel spin would occur only if the coefficient of friction between the wheel and the ground was less than 175/460 = 0.38.
The effective pedal force calculated previously was 2156 N.
The effective pedal force was taken as a
combination of a vertical push, P,, on the front pedal and a vertical pull, P2, on the rear pedal,
P1 + P2 = 2156.
Considering vertical equilibrium of the bicycle F1 – F2 P1 + P2 + R1 + R2 = 0
P2 = (0.56 times body weight);[5] P1 = (2.19 times body weight),[5] F1 -F2 =(0.64 times body weight).[5]
(Here P1,P2 are pedal forces ;F1,F2 are vertical forces on handle bar; F3, F4 are horizontal force on handle bar; SH ,SV are horizontal and vertical force on saddle)
The vertical forces applied to the two handlebars are not equal. Consider the front view in Fig. . The pedal loads produce a couple which is resisted by the hands. Taking moments about the line of contact of the wheels with the ground,
F1 x L1+ F2 x L1 = P1 x L9 + P2L10. 1.STANDING PEDALLING
P1 = + 1716.96 N , P2 = – 439.04 N SH = SV = 0
F1= + 846 N , F2= – 345 N F3= – 100 N ,F4= – 100N 2.CLIMBING
P1 = + 1448 N ,P2 = – 367 N SH = SV = 0N
F1= + 741N ,F2= – 293N F3= + 100N ,F4= + 100N 3.SEATING PEDALLING P1 = +732 N ,P2 = -54 N SH = 18N ; SV = 392N
F1= + 235N , F2= – 181N F3= 0N ,F4= 0
-
-
FEA OF MODELS IN DIFFERENT SCENERIO
-
Frame Seating pedalling
Force applied
SH =18N, SV =-392N, Fb=- 339N
Fh=-54N
Max stress
57.7MPa
Max deflection
0.1299mm
Factor of safety
15
Standing pedalling
Force applied
SH = SV =0, Fb=-339N Fh=-54N
Max stress
72.29MPa
Max deflection
0.160mm
Factor of safety
15
-
Crank Normal riding
Force applied
366N
Max stress
5.281MPa
Max deflection
0.0023mm
Factor of safety
15
Standing pedalling
-
Handle Normal riding
Force applied |
+846N,-345N |
Max stress |
58.25MPa |
Max deflection |
0.5046mm |
Factor of safety |
15 |
Force applied |
858N |
Max stress |
12.38MPa |
Max deflection |
0.005mm |
Factor of safety |
15 |
Force applied |
858N |
Max stress |
12.38MPa |
Max deflection |
0.005mm |
Factor of safety |
15 |
Force applied |
+235N,-181N |
Max stress |
245.7MPa |
Max deflection |
187mm |
Factor of safety |
15 |
Force applied |
+235N,-181N |
Max stress |
245.7MPa |
Max deflection |
1.87mm |
Factor of safety |
15 |
Standing pedalling
IV. RESULTS
Yield strength |
Normal riding |
Uphill riding |
Downhill riding |
Standing pedalling |
350 MPa |
57.7MPa; 5.281MPa; 58.25MPa |
12.38MPa |
245.7MPa |
72.29MPa |
The finite element method has been used to measure the stresses and deflections of a bicycle frame caused by loads applied while cycling.
In above comparison more deflection is observed in standing pedalling, uphill riding and downhill riding respectively. This deflection is occurred due to higher stress of models in above conditions. Since the deflections are in mm we arent able to see them with the naked eye.There may be other riding conditions which produce higher tube stresses than the cases considered here. In particular the influence of dynamic loading due to rough and bumpy roads could be significant.
When we compare yield strength and max stress obtain in bicycle model during FEA we can say that the bicycle is in safe condition but when we observe the breaking point in results we can say that ,the material will start to fracture in these breaking points over a period of time. We can observe the respectively. These factory of safety of bicycle is 15 so the bicycle will experience failure at 15 times the design load.
VI. REFERENCES
-
Reddy, G. Sreeram, Manzoor Hussian, and K. Srinivasa Rao. "Latest Research on Reverse Engineering Technology.
-
Doyle, T. E., B. W. Baetz, and B. Lopes. "First-year engineering bicycle dissection as an introduction to sustainable design." Proceedings of the Canadian Engineering Education Association (CEEA) (2009).
-
K. Chinna Maddaiah and Y Diwakar Reddy 2018 IOP Conf. Ser.:
Mater. Sci. Eng. 455 012123
-
International Journal of Advanced Mechanical Engineering.SSN 2250-3234 Volume 8, Number 1 (2018), pp. 55-62
-
Soden, P. D., and B. A. Adeyefa. "Forces applied to a bicycle during normal cycling." Journal of Biomechanics 12.7 (1979): 527-541.
-
Rowe, T., M. L. Hull, and E. L. Wang. "A pedal dynamometer for off-road bicycling." (1998): 160-164.
-
Covill, Derek, et al. "An assessment of bicycle frame behaviour under various load conditions using numerical simulations." Procedia engineering 147 (2016): 665-670.
-
8. Devaiah, B. B., et al. "Stress analysis of a bicycle frame." Materials Today: Proceedings 5.9 (2018): 18920-18926.
V. CONCLUSION
The bicycle has been disassembled and measured in a bicycle shop. These measured values have been used to create the CAD model of bicycle parts in AUTODESK INVENTOR. The bicycle models have been assembled on the same software and the whole bicycle has been created. Four loading conditions have been calculated in this project, i.e., normal pedaling, uphill riding, downhill riding and standing pedaling. This calculated value of loading has been imposed on bicycle model using Stress analysis in INVENTOR software. When we examine the results and compare them to the yield strength, we can conclude that the bicycle is safe; however, in the long run, there may have been some fractures, as evidenced by the results. The FEA simulation results show there are still many opportunities for optimization of this bicycle model design with the aim not only of reducing material used but also increasing the life of the bicycle. Optimization is required to reduce the amount of material used in bicycle models, but the importance is that the bicycle remains within a safe tolerance and provides comfort to users.