
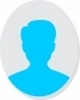
- Open Access
- Authors : D. Pranay Sai , Aaqib Farooq , Gunjan Kumari , K. Sai Priyanka, D. Govardhan
- Paper ID : IJERTV10IS050468
- Volume & Issue : Volume 10, Issue 05 (May 2021)
- Published (First Online): 05-06-2021
- ISSN (Online) : 2278-0181
- Publisher Name : IJERT
- License:
This work is licensed under a Creative Commons Attribution 4.0 International License
Computational Fluid Dynamics Analysis for Enhancing the Performance of Drone Frames
-
Pranay Sai1, Aaqib Farooq2, Gunjan Kumari3, K. Sai Priyanka4, D. Govardhan5
Research student1, Research student2, Research student3, Assistant professor4, Professor5 Department ofAeronautical Engineering, Institute of Aeronautical Engineering, Telangana, India.
Abstract: Drone is a profoundly progressed flexibility airplane that has a basic plan and construction. It has a high burden conveying limit and different qualities. Robot is one of the UAV (Unmanned Aerial Vehicle) which is utilized to lift, convey, notice, salvage, and gather information starting with one spot then onto the next in lesser time and without taking a lot of room and cost. Drones are classed at first according to their anatomy, operations, size, and weight. They are further categorized based on variables such as the number of rotors utilized, the position and orientation of the rotors, and the design of the frame. With the smallest size possible, the payloads of different drones (Monocopter, tricopter, quadcopter, and hexacopter) will be changed by changing the design, aerodynamics, structural weight, etc. of a particular drone. In case the drone type and size are not specific, the same can be done by increasing the number of rotors. The payload increases with the increasing number of rotors at the expense of the size and structural weight of the drone. The structural weight will be reduced by opting for any low-weight material and changing the design (or even size). This reduced weight will be added to the payload as increased efficiency. The possible material could be aluminum but because carbon fiber has a lighter weight than aluminum, we opted for carbon fiber. Moreover, carbon fiber has exceptional strength and rigidity and has a specific tensile strength of approximately 3.8 times that of aluminum and specific stiffness of 1.71 times that of aluminum. We will be describing and discussing the design of different drone frames i.e., Monocopter, tricopter, quadcopter and hexacopter. Firstly, we'll design the structure of a drone with dimensions and then analyze the frame, selecting the necessary material and structure that meets the weight, strength, and stiffness of the requirement of the system. Also, we'll be analyzing these drone frames using different software.
Keyword: Aluminum; Analysis; Carbon fiber; Design; Frames; Multirotor; Payload.
-
INTRODUCTION
An unmanned aerial vehicle (UAV) is an aircraft without a pilot or passengers on board. UAVs include both autonomously controlled vehicles (drones) and remotely operated vehicles (RPVs) controlled via radio transmitters. Drones are often employed in situations where the danger of dispatching human- piloted aircraft is high or when the utilization of manned aircraft is impractical. one in every one of the essential exercises of the UAV was the "aeronautical torpedo", planned and worked during essential fighting. Multi- engine drones are gaining popularity among us thanks to their wide selection of applications and structural integrity with perfect stability. Drone may be an UAV that may perform
multiple missions. Recently, there's increasing interest in drone
applications like surveillance, search and rescue and object detection to parcel delivery thanks to its high mobility because it can hover, takeoff, navigate and land in tight areas. Factors like size, range, capabilities, weight classify drones into different categories After we associate with aerial platforms, drones are available in four types: single propeller, multi-rotor, fixed-blade and fixed-wing hybrid. This review focuses on the look and analysis of drone frames which will support payloads as high as 5 kg. The sunshine weight and high thrust capacity of the Turnigy 4240 530Kv motor allow it to extend its lifting capacity, which is able to be higher with electronics and electronic components when placed thereon to control. Structural analysis is one of the important applications of the finite element method. The drone's motor and propeller are selected per the necessities of the drone's chassis. the planning and assembly of the chassis of the Monocopter, tricopter, quadcopter and hexacopter was dispensed within the CATIA V5 design software. The elements are finished by learning the texture properties of each casing, the strength of the fuselage and hence the inflexibility of the robot outline is investigated to help the computation of the extent of the push created. By each engine, the 15 "× 5.5" propeller and also the 530 KVA engines were accustomed analyze the thrust of every engine. This push is employed to see the structural analysis of varied drone frames.
-
METHODOLOGY
Design of Drones
First, we'd like to spot many materials like components, avionics, and electronics-related variables that contribute to the mechanical and physical properties of the drone. Second, appropriate physical and mathematical models describe how the characteristics of the individual components of the drone are often combined to supply the properties of the fabric itself. It's, therefore, possible to style adrone specified it's the specified properties for a specific application. These properties may simply be having a specified hardness and strength, a desired thermal conductivity, or a specified minimum hardness at the most affordable possible cost per unit volume. Notwithstanding the determinations one can plan a particular robot. We must also note that there is also a high payload drone that's more suitable for the applying than our designed high payload drone. Our engineered drone must therefore offer a selected cost or performance
advantage over conventional alternatives. One amongst the needs of this resource is to indicate to you the logical steps required totravel through the planning process.
Approach Methodology
Selection of Drone Frame, propeller , motor and other avionics
Designing and Assembling of Drone parts using CATIA V5, 3-D Printing of various Parts of Drones
Static, Mathematical Analysis of Drone Frames
Dynamic Analysis of Drone Frames using ANSYS or MATLAB
Fig 2.1: Approach methodology flow chart
-
3D PRINTS AND CATIA DESIGNS
3D Printed Parts
We took 3D print extra components so that we may have spares in the case of an accident, notably additional landing gears. Because most of the components serve two roles and are not flat on both sides, certain components will require support material to print. To conserve weight, we chose an infill of 20 to 30 percent, which produced excellent results.
CATIA Designs
The drone frames are planned utilizing CATIA planning programming. CATIA Software: CATIA represents Computer-Aided Three-Dimensional Interactive Application. It is an arranging programming made by Dassault Systems. It is basically used for arranging, by various controls like Aeronautical planning, Mechanical planning, Civil planning, Architecture, Electrical planning, and some more. Numerous workbenches are accessible which can be utilized according to the necessity, similar to Part Design, Surface plan, Sheet metal plan and some more. The planned segment would then be able to be moved to different investigation programming by changing them over to various configurations like stp, igs, and so forth for the undertaking wireframe and surface workbench was utilized. A 2D sketch was drawn utilizing sketcher at that point changed over to surface in the wireframe and surface workbench.
FRAMES
Features of Designed Drones
Maximum Vibration Isolation – easier on the flight controller, smoother video, noise reduction, electronic longevity.
Light Weight Design – weight centralization, maximum payload, increased battery life, overall efficiency.
Structural Rigidity – strong airframe, but not overbuilt were unnecessary
Integrate or Combine as many parts as possible – perfection by simplicity, reduced part count, function over form
Modularity and Compatibility (i.e., Hackable) – dimensions bolt up to other common parts and accessories
For weight and rigidity, carbon fiber tubes are used for drone arms and legs.
-
ANALYSIS AND RESULTS
-
Monocopter
In mono-copter, one rotor is found inside. Another will be a rotor that essentially assists with making control to the heading. Monocopter may be the best decision for a speedier flight time with longer constancy alongside a mix of float having heavy weights. Mono-wing rotorcrafts are outfitted with framework and control actuators so they'll turn themselves and head to any ideal bearing. Monocopter is advantageous to produce and keep up on account of the direct and compact design. The highlights of rotorcraft endue itself the adaptability to in an upward direction start and land, and in this manner, the drifting soundness permits it to work inside the bound climate. Since mono-copters are generally conveyed in reconnaissance missions, the deception of the airplane is significant.
The essential design of a high payload limit Monocopter comprises of three sections: a mono-wing and two aeronautics bars which are connected by an inflexible pivot, appeared previously. Engines are set at the tip of flight bars and payloads are organized on the flying bars, so the center of mass for the total airplane may be made inside the space between the flying bars. Engines apply force to pivot the airplane, then, the turning mono-wing gives lift power to the airplane. during a standard flight, the Monocopter turns round the focal point of mass.
Mathematical Model
Blade element aerodynamics
Above Fig shows the inflow sketch at a delegate edge component on the single wing. At the point when the vehicle is turning at a pace of =[p,q,r]T, the neighborhood translational speed of the edge component can be portrayed as:
where lbe is the edge component's range vector and lbe =[lbe,0,0]T in the body-fixed casing T, Vcm is the vehicle's focal point of mass's translational speed, and Vcm=[u,v,w].. According to the relative movement theory, the sharp edge component's inflow speed is:
where wi is the computed induced velocity using momentum theory. It is provided by whilst hovering.
Because the effect of radial component, UR, on thelift is always ignored the resultant inflow velocity is, therefore,
-
Tricopter
In a tricopter, there are three various types of incredible engines, three regulators, four gyros and just 1 servo. The engines are just positioned at each outrageous finish of three arms and each one among these is holding an area sensor. to lift a tricopter the choke switch is started first then the gyro sensor gets its flag and can give the sign to the regulator that assists with dealing with the engine pivot. A tricopter is prepared to stay settled on its way since it is furnished with a great deal of exemplary sensors and hardware itself. no manual remedy is needed to be applied.
Tri-rotor UAVs are regarded to be unbending items when the elements of tri-rotor UAVs are compared to the climate. For tri-rotor UAVs, the 6-degree opportunity (DOF) nonlinear movement conditions that are created for regular UAVs are used. The tri-rotor UAV is unable to turn and decode in three-dimensional
space, and Newton's principles are used to infer the inflexible body components). The 6-DOF unbending body conditions of movement for trirotor UAVs are conveyed based on the differential circumstances depicting translational movement, rotational movement, and kinematics as shown in Fig.
Were,
Fx, Fy, Fz are the outside powers, and (L, M, N) are the outer minutes following up on the focal point of gravity concerning the body-fixed edge. (u, v, w) are the translational speeds, (p, q, r) are the rotational speeds, and (, , ) are the rotational points. Ixx, Iyy and Izz are the rotational in activities of the tri-rotor UAV.
MATHEMATICAL MODEL
The chart above depicts the tricopter's unique situation, with the powerful condition of yaw control outlined on the lower right side. This is because the RC servomotor operates the tail pivot to modify the declination point of the tail hub in yaw control. The movement control of the tri-rotor may be broken down into height, move, pitch, and yaw. The control techniques for tri-rotors are shown in Fig: Tri-rotor Control Systems. The elevation control is shown in Fig. (a), and increasing the speed of each rotor increases the height, and vice versa. The mechanism for move control is that with a comparable rotor-1 speed, adjusting the rotor velocities of the two front rotors creates move control (see Fig. b). Pitch control is seen in Fig. (c); with identical rakish speeds for the front two rotors, changing the rotor speed of rotor 1 produces pitch control. Yaw control may be successfully established by employing the characteristic yawing second from the reaction force and also from the slant point. The slant point is especially useful when there is a sudden risk of collision since it allows for unexpected turning control by changing the rotor.
Simulation in MATLAB for Position Determination
Plotting three-dimensional locations against time outline in MATLAB reveals the relationship or dependency of location on the brisk speed of engine/s. The plot of location vs time is captured on the screen in Figure. Absolute speed is predictable when speed augmentation is zero. It's necessary to unravel an assessment between the tri-attempting copter's speed and also the prompt speed in order to figure out the condition of the tri-copter with time inside a reach. Careful speed is steady when speed addition is zero. The sassy speed is 50 as the speed addition is zero in the redirection result. Despite the fact that the happy speed is also 70, increase the pace. When the sassy speed is 100, speed augmentation may be zero at that moment. When speed augmentation is 0, the value of demanding speed is 150. Finally, the particular speed looks to be 200. With the aid of MATLAB, these results demonstrate 3D-position.
Case1. Angular velocity is constant, and accelerationis zero
-
Quadcopter
A quadcopter is a multirotor aircraft with four rotors that lift and maneuvers it. It is also known as a quad rotor helicopter or quadrotor. Quadcopters are rotorcraft, not fixed-wing planes, because they are propelled by a swarm of rotors (in a vertical bearing arranged propellers). Bundling on quadcopters may be classified into two categories based on their design: profiled edge and X bundling. In a profiled arrangement, the space is more visible, and the point of gravity connection is more difficult to locate. It can keep the machine arm and mount in place, giving you more time to concentrate on post-processing modifications. It takes up relatively little room when deflated and is easy to pass on. It might be used to hold apertures for the installation of ultrasonic modules. The X package is easier to set up, has a higher value, is more versatile, and is more practical for stunt flying.
we used 8 iterations for all estimations. We assume inlet velocity 130 m/s then by estimate the effect of the inlet velocity we get the shown in scaled residualsgraph.
The influence of the force on the plane's surface was investigated in order to verify that the plane's capacity to handle the weights that would be on it and that the design will be able to maintain its shape without deformations. For this, we estimate that the force acting on the quadcopte's top surface will be 1N. The maximum total deformation was found to be 0.00096759 mm, the maximum elastic stain was found to be 0.0011151 mm/mm, and the maximum stress was determined to be 1.1498 MPa. The frame is made of carbon fiber, which has the following properties: elastic modulus E=2.3e11Pa, Poisson's ratio =0.3, and density 1.5e 3 kg m.
To reduce high-frequency vibration disturbance during descent, a quadcopter should be used. We recommend the following two responses in this respect.
-
Reduce the rate at which loading and unloading equipment is used, and finish loading and unloading in a quasi-static condition.
-
Vibration isolation equipment with higher high- frequency filtering capability can be installed on the frame.
Design summary
This design uses star/e programming for the chasse's demonstration plan and AutoCAD to complete the 2- dimensional assembly drawing and part's plan. It increases standard plan interaction, competency, and reduces fabrication costs. To meet the look requirements, we must consider the resultant requirements and each aspect, as well as support the many situations and circumstances of using outline. Break down the edge's assortments of add the exact workplace first, then construct a three-dimensional model of the casing using ProE's three-dimensional showing programming. Second, select authorized materials to reduce prices and the casing's heap. Third, finish the limited component model by measuring the calculation model and lattice appropriately using limited component programming. Fourth, import the restricted component model into ANSYS to determine and break down the casing's strength and solidity. Fifth, read the results and enhance a section of the structure, upholding the results of the static examination so that we may enhance proficiency, primary strength, and texture firmness. We can get a wide range of nitty gritty anxiety shapes, modular examination arrangement graphs, and comparing information by dissecting the edge of the quadcopter with the 3D limited component to manage the advancement of plan and decrease the costs of configuration, plan, and investigation process duration, and thus the utilization of crude materials and capital, which is unfathomably advantageous.
-
-
Hexacopter
A hexacopter fills in whatever number possible applications as could be expected under the circumstances with its 6-engine system where 3 works the clockwise way and the other three moves the counter clockwise way. Subsequently, Hexacopter can acquire higher lifting power when contrasted with quadcopters. A Hexacopter is intended to fill in as an amazingly protected landing create regardless of having an intricate plan and system.
Hexacopter configuration
In a hexacopter, six motors drive six propellers. This hexacopter lifting increase uses the momentum transmitted by the propeller mix of hexacopter charts. The package design is separated into two categories, as illustrated in Fig: plus (+) and X. The six degrees of
freedom (DOF) of the Hexacopter are influenced by the rotational speed of each rotor; hence, the two lodgings will have verifiable improvement component models.
In this assessment, the Plus (+) outline chart is used. Each arm has a brushless DC motor and a fixed-pitch propeller, which allows the rotor to drive the wind current downwards to create t. Each arm is powered by a brushless DC motor with a fixed-pitch propeller, which allows the rotor to direct wind current downward to create lift force. The rotor rotation direction is made up of three counter clockwise rotors (CCW) and three undeniable clockwise rotors (Clock Wise; CW). From an overall perspective, it is evident that the hexacopter's unfathomable headway is only determined by the speed of the engine rotation.
The package should be made of lightweight materials that are capable of supporting its operational and vital weights. As a result, inspecting the adaptability and strength of the creating material out of the edge is crucial. As shown in Figure: Heavy-lift hexacopter schematic plan, this edge is arranged as a hexagram with six equivalent long arms attached to the point of convergence of a replicated hexagonal plate.
Analysis of hexacopter frames
Thrust and Motors
As the drive component for the hexacopter, the engine is the main segment. In any case, prior to deciding the limit of the engine applied in the plan, it is important to know the all-out weight that will be lifted and the push which is needed to lift the substantial heap of hexacopter. The estimation to decide the push per engine as in the accompanying condition:
In addition, static push can be determined by the accompanying condition.
In this situation, T represents the engine power, while D represents the propeller diameter, is the air thickness, and P represents the propeller diameter. This calculation will be used in combination with the following figures:
The propeller predictable is Kp, the distance across is D, and the engine rotational speed is RPM. The KV constant and the voltage utilized by the engine are utilized to compute the value of this RPM. As the primary source of power in the Hexacopter construction, a BLDC engine is used, which has the advantage of not requiring a brush or commutator. As a result, this type of engine will be more valuable than a DC engine. High RPM may be passed on by a BLDC engine (Revolutions consistently). KV (rpm/volt),
where KV is a cutoff that indicates the amount of rpm increase for each unit of voltage employed, is the most crucial pressure of a BLDC engine.
FRAME
The packaging should be worked from lightweight material yet adequately ready to help its operational weight and essential weight. From this time forward, it's critical to investigate the flexibility and strength of the making material out of the edge. the energy of this edge is hexagram with six identical long arms that attached to the focal point of a duplicated hexagonal plate of as exhibited in Fig: Frame and fragment.
-
Weight of each component ofdrones
-
Results Summary
With the replacement of aluminum with carbon fiber, we got a reduction in structural weight by nearly 42%. That reduced structural weight got added in thepayload as increased efficiency. Also, the designs weopted for helped us increase the efficiency of our drones.
-
In Monocopter, by using the aluminum the frame weight was estimated to be 775gm. By replacing the material with carbon fiber, we got a weight of 450gm. Thus, with the replacement of aluminum with carbon fiber, we got a reduction in structural weight by 325gm.
-
In Tricopter, by using the aluminum the frame weight was estimated to be 760gm. By replacing the material with carbon fiber, we got a weight of 440gm. Thus, with the replacement of aluminum with carbon fiber we got a reduction in structural weight by 320gm.
-
In Quadcopter, by using the aluminum the frame weight was estimated to be 1120gm. By replacing the material with carbon fiber, we got a weight of 650gm. Thus, with the replacement of aluminum with carbon fiber, we got a reduction in structural weight by 470gm.
-
In Hexacopter, by using the aluminum the frame weight was estimated to be 1690gm. By replacing the material with carbon fiber, we got a weight of 980gm. Thus, with the replacement of aluminum with carbon fiber, we got a reduction in structural weight by 710gm.
-
-
-
CONCLUSION
-
This exploration has been empowered to style, dissect, and develop substantial lift Monocopter, Tri-copter, Quadcopter, and Hexa-copter that is equipped for flying and lifting the payload. Appropriately, with the reduction in hidden weight and with right size and style more payload was passed on by these multi-copters correspondingly. The results are given by the Result fragment game plan of the ANSYS workbench. Here the determined outcome from the appropriate response is imported for the post-preparing of the undertaking study. Shapes of shifted boundaries of the stream will be acquired and dissected to check the conduct of the stream. Different instruments like vectors, smooth out will be utilized to consider the bearing of the stream and different boundaries.
Future Trends
Armed with a good range of benefits, drones have a key role to play within the growing market in India. Drones have made an entry into diverse end-user segments and therefore the developmental efforts for locating newer drones for existing & novel applications are a part of top priority.
The new drone could likewise be liked for a few reasons: such are more grounded, lighter, or more affordable contrasted with conventional materials. Progressed drones are, generally utilized in Space innovation applications are a piece of main concern. The new robot could likewise be liked for a few reasons: such are more grounded, lighter, or more affordable contrasted with conventional materials. Progressed drones are, generally utilized in Space innovation.
BIBLIOGRAPHY
-
Ahmad Safaee, Seyed Zeinolabedin Moussavi, Mohammad Bagher Menhaj, Design and Construction of Monocopter and its Nonlinear Control Using Photo Diode Array, in U.Porto journal of engineering, Portugal, 2018.
-
Sai Khun Sai, Hla Myo Tun, Modeling and Analysis of Tri-Copter (VTOL) Aircraft, International Journal of Emerging Engineering Research and Technology, Volume 3, Issue 6, June 2015, PP 54-62.
-
Mathew Thomas, Albin A T, Christin Joseph, Amal Kurian Mathew Jerin Cyriac, DESIGN AND ANALYSIS OF A QUADCOPTER USING CATIA, International Journal of Scientific & Engineering Research, Volume 7, Issue 3, March- 2016.
-
S. Bhandari, S. Pathak, R. Poudel, R. K. Maskey,
P. L. Shrestha and Binaya Baidar, Design and Development of Hexa- copter for Environmental Research, Department of Mechanical Engineering, Department of Civil and Geomatics Engineering, 2016.
-
J Muhammad A. Muflikhun, Elmer R. Magsino, Alvin Y. Chua, Design of a Quadrotor UAV Aluminum Casting Frame, 9th & 10th October 2014, HUST, Hanoi, Vietnam.
-
Swapnil Yemle, Yogeshwar Durgude, Ganesh Kondhalkar, Ketan Pol, Design & Analysis of Multi-Frame for Octo & Quad Copter Drones, International Research Journal of Engineering and Technology (IRJET), Volume: 06 Issue: 06 | June 2019.
-
Sai Mallikarjun Parandha, Zheng Li, Design and Analysis of 3D Printed Quadrotor Frame, in International Advanced Research Journal in Science, Engineering and Technology, Vol. 5, Issue 4, April 2018.
-
Endrowednes KUANTAMA, Dan CRACIUN, Radu TARCA, QUADCOPTER BODY FRAME MODEL AND ANALYSIS, in ANNALS OF THE UNIVERSITY OF ORADEA, Fascicle of Management and Technological Engineering, ISSUE #1, MAY 2016.
-
Anand Kishor Verma, Neeraj Kumar Pradhan, Rajesh Nehra, Prateek, Challenge and Advantage of Materials in Design and Fabrication of Composite UAV, in Published under license by IOP Publishing Ltd, January 2005.