
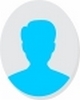
- Open Access
- Authors : D. Divya , Kvs. Ruthvik Sandilya , R. Sabari Vihar , D. Govardhan
- Paper ID : IJERTV10IS050469
- Volume & Issue : Volume 10, Issue 05 (May 2021)
- Published (First Online): 05-06-2021
- ISSN (Online) : 2278-0181
- Publisher Name : IJERT
- License:
This work is licensed under a Creative Commons Attribution 4.0 International License
Conceptual Design and Analysis of Dome for Underwater Application
D. Divya1, Kvs. Ruthvik Sandilya2, R. Sabari Vihar3, D. Govardhan4
1,2UG Student, Aeronautical Engineering Department, IARE, Hyderabad, India
3 Assistant Professor, Aeronautical Engineering Department, IARE, Hyderabad, India 4Professor, Aeronautical Engineering Department, IARE, Hyderabad, India
Abstract: There will be an enormous increase in pressure as we go to ocean depths. External pressure from the surrounding is exerted on the Underwater vehicles. For an Underwater Vehicle the Dome shields the hardware and is subjected to tremendous pressure at one time during operation. As a result, the dome must be qualified for the pressure. Dome models are developed based on mechanism, materials and geometric constrains. SolidWorks is proposed for the design, modeling and drawing generation of the dome. ANSYS Workbench, the finite element software to carry out the analysis. Considering stress criterion for design and analysis is carried out by the effect of changing the material type, properties and eventually the best dome is suggested. Suitable evaluating methodology is suggested.
Keywords: Dome, Pressure, factor of safety, Von-Moises Stress.
- INTRODUCTION
- UNDER-WATER BODIES
Vehicles or Missiles that are operated under water are called Under-Water Bodies. These includes submarines, Torpedoes. These vehicles are subjected to an enormous external pressure from the surrounding water. During emergency conditions these vehicles dive 300-450[m] deep from the water level, resulting increasing pressure. Water has high density in which it exerts high resistance to the movement of the body.
- DOME
Dome is the component of the vehicle that protects the hardware which acts as nose cap to the under-water vehicle. This dome shape can withstand the pressure required. As a result, a dome shape must be created with desired material. There are different sorts of heads, with the hemispherical head being the best fit for our needs. Before a structure is used, it should be studied experimentally.
- HEMISPHERICAL DOME (or) HEADS
The head depth is half the diameter of these heads, which has a radial geometry. Two pressure heads are arranged back-to-back in these storage heads, forming a storage sphere that efficiently stores materials under high pressure. Hemispherical heads are thinner than shell heads and have a standard code 3:1 that taper during the transition. Hemispherical heads are usually made from welded sheets rather than the flat sheets used in the other head varieties. This makes it the thinnest head on the market, as well as one of the most expensive. These heads are ideal for applications that need high-pressure storage or vessels with enormous diameters.
Figure 1 Hemispherical dome with 7mm thickness modeled using Solid works
To complete the structural qualification, the specimen should be tested in the actual environment. During testing, the test specimen must be able to withstand all forces exerted on it. Because, the dome has such a significant impact on the total body, a specific design is created using various materials. There is 1bar increase in pressure for every 10[m] of depth. At one point during its operation, the dome of an underwater vehicle is subjected to a pressure of 25-40[bar]. As a result, qualification of this dome for the pressure is required. Hence dome is designed to take up the pressure of 30 bar.
- UNDER-WATER BODIES
- VALUATION FOR INITIAL THICKNESS
Materials properties:
Product standards define the limits for composition, quality and performance and these limits are used or presumed by structural designers.
Aluminium 6061 alloy is originally called as Alloy61S. It is a precipitation-hardened alloy and the most commonly available and heat treatable alloy. It has a density of 2.7[g/cm3], Poisson’s ratio of 0.33, and a shear modulus of 26[Gpa]. It also having a good value of Young’s modulus which is about 68[Gpa]. Al6061 alloy can be easily formed and has excelled weldability. It is also having a minimum yield strength of 276[MPa] and Tensile strength of 310[MPa].
Titanium Grade-2 is another material which is light weight and exceptionally corrosion resistant. It has a density of
4.51[g/cm3], Poissons ratio of 0.34-0.40 and a shear modulus of 45[Gpa]. It is well suited for marine applications. Titanium Grade 2 has a minimum yield strength of 275[Mpa] (40 ksi), and relatively low levels of impurity elements, which places it between Grade 1 and 3in terms of strength and also youngs modulus of 102.7[Gpa]. It is having a minimum yield strength of 345[Mpa] and Tensile strength of 485[Mpa].
Analytical solution:
For aluminum 6061 the available input parameters like internal pressure 30 bar (3 MPa), diameters 2500[mm], 3000[mm] and yield stress of 276[MPa] thickness of the hemispherical pressure vessel is calculated by
Pd
Thickness(t) =
4
3 2500
t = = 6.7[mm] 4 276
3 3000
For manufacturing allowance this value is concluded to 6[mm], 7[mm] based on this thickness dome is modeled using Solid works.
- Finite element analysis of the Dome:
Model is imported into Ansys workbench. In Static structural analysis Material is assigned as structural steel and meshing size as fine. Fixed support is applied along the base of the flange and internal pressure applied is 30[bar]. Solution is derived for total displacement, von Moises stress (equivalent stress) and equivalent strain. The values thus obtained are as follow.
To validate any design, it must satisfy minimum FOS of 2.5. Equivalent stress is found to be 126.13[MPa] which derives FOS of 1.982 which cannot be validated. Hence multiple iterations are carried out to meet safety factor of 2.5. Modelling and analysis are repeated for new iterated thickness. The respective values are stated in tables.
t =
4 276
= 8.15[mm]
For manufacturing allowance this value is concluded to 7[mm], 9[mm] based on this thickness dome is modeled using Solid works.
Figure 2 Hemispherical dome with 7mm thickness modeled using Solid works
For titanium alloy the available input parameters like internal pressure 30 [bar] (3 MPa), internal diameter 2500[mm] and yield stress of 345 [MPa] thickness of the hemispherical pressure vessel is calculated by
Hemispherical 7mm Thickness Dome (Aluminum) S. No Parameter Maximum 1. Von-Moises Stress 729.09[Mpa] 2. Deformation 3.390[mm] 3. Equivalent Strain 1.04*10-2 Hemispherical 7mm Thickness Dome (Aluminum) S. No Parameter Maximum 1. Von-Moises Stress 729.09[Mpa] 2. Deformation 3.390[mm] 3. Equivalent Strain 1.04*10-2 Pd
Figure 3 Von-Moises stress obtained for Aluminium 7mm thickness
Figure 4 Directional Deformation obtained for Aluminium 7mm thickness
Table 1 HEMISPHERICAL ALUMINIUM DOME 7mm THICKNESS
Thickness(t) =
4
3 2500
t = = 5.4[mm] 4 345
3 3000
t = = 6.52[mm] 4 345
Table 2 HEMISHERICAL ALUMINIUM DOME 9mm THICKNESS
Hemispherical 9mm Thickness Dome (Aluminum) S. No Parameter Maximum 1. Von-Moises Stress 547.37[Mpa] 2. Deformation 3.76651[mm] 3. Equivalent Strain 7.823*10-2 Table 3 HEMISPHERICAL TITANIUM DOME 6mm THICKNESS
Hemispherical 6mm Thickness Dome (Titanium) S. No Parameter Maximum 1. Von-Moises Stress 793.75[Mpa] 2. Deformation 2.1532[mm] 3. Equivalent Strain 6.902*10-2 Table 4 HEMISPHERICAL TITANIUM DOME 7mm THICKNESS
Hemispherical 7mm Thickness Dome (Titanium) S. No Parameter Maximum 1. Von-Moises Stress 753.09[Mpa] 2. Deformation 2.701[mm] 3. Equivalent Strain 6.533*10-3 Considering von Moises stress, factor of safety is calculated for two designs and their materials respectively and tabulated as in table 5.
von
FOS =
ys
FOS for Aluminium 7mm thickness is
729.09 = 2.64
276
Similarly, the factor of safety is calculated for all the four
cases.
Numerical Analysis (Satisfaction Criteria)
Von-Moises stress selection criteria (Energy of distortion theory) for a 2D structured body:
900
800
700
600
500
400
300
200
100
0
3
2.5
2
1.5
- RESULT OBTAINED
Graph 1: Von-Moises Stress Chart
Von-mises stress
7mm(Al) 9mm(Al) 6mm(Ti) 7mm(Ti) Von-mises stress
Graph 2: Factor of Safety Chart
Factor of Safety
1
1
y
y
2 2
+2
1 2
2
2
Where, 1 and 2 are the principal stresses so that, we need to find all three principal stresses to substitute into von Mises criterion. For a hemispherical shape 1 = 2= Pd/4t,
All the above four cases satisfied the Numerical Analysis with respective to Von-Moises criteria and hence meeting the criterion, thus failure would NOT have been expected on the basis of yield.
1
0.5
0
7mm(Al) 9mm(Al) 6mm(Ti) 7mm(Ti)
FOS
500
450
400
350
300
250
200
150
100
50
0
Graph 3: Mass Comparison Chart
Mass
7mm(Al) 9mm(Al) 6mm(Ti) 7mm(Ti)
Mass
Table 5 Comparison Table for Dome
THICKNESS PARAMETERS 7 mm thickness (Aluminium) 9 mm thickness (Aluminium) 6 mm thickness (Titanium) 7 mm thickness (Titanium) VON-MOISES STRESS 729.09[MPa] 547.37[MPa] 793.75[MPa] 753.09[MPa] FACTOR OF SAFETY(FOS) 2.64 1.96 2.3 2.1 MASS 184.7[Kg] 341.86[Kg] 265.44[Kg] 446[Kg] - CONCLUSION
Based on input values 30 bar pressure, 2500mm &3000mm outer diameter and Aluminium 6061, Titanium as materials, dome thickness is calculated using pressure vessels concept. Using this thickness value modeling is carried out using Solid works and analysis is carried out using Ansys workbench.
Hemispheric Dome requires the least amount of material and has the smallest surface area to cover a specific volume and cost efficient too.
In aluminium dome model of outer diameter 3000[mm] and 9[mm] thickness, the value of FOS is 1.96, which cannot be validated. Iterations of this design with outer diameter 2500mm and 7mm thickness is designed and modeled. Analysis is carried out. It was observed that this dome design has the FOS value 2.64 which satisfies the minimum required criteria.
Similarly, in Titanium dome model of outer diameter 3000[mm] and 7[mm] thickness, the value of FOS is 2.1, which cannot be validated. Iterations of this design with outer diameter 2500[mm] and 6[mm] thickness design is modeled and analysis is carried out. It was observed that this dome design has FOS value 2.3, which does not satisfy the minimum required criteria.
From the above four cases it is observed that Aluminium 6061 material with 7[mm] thickness has required factor safety and can with stand the pressure applied on it. This dome can protect the hardware of the underwater vehicle. It is also observed that this designed model has less mass of 187.4[Kg] and cost efficient.
- FUTURE WORK
The characteristics of a material are mostly determined by the load acting on the surface, the type of environment in which it is being operated. Clearly, the analysis shows that Aluminium 6061 with a 7mm thickness outperforms Titanium Grade in terms of characteristic qualities. A proposed composite alloy containing Titanium alloy 6%, Aluminium 4%, and Vanadium is being investigated, with tensile strengths of 1000-1100 MPa and useful creep resistance of up to 300*C of about 570 MPa for 0-1 percent total plastic strain in 100 hours. It would be extremely resistant to fatigue and crack propagation. This composite material might help the engineers to manufacture the dome with high corrosion resistance and withstand all the loads and also plays a key role in protection of the hardware of the underwater vehicle.
This designed Dome with various thicknesses can also be used in the construction of sturdy fuel tanks for use in rockets under specific heat conditions. This Dome designed
with high standard materials and high withstanding capacity can control the fuel pressure in it without any failure.
- ACKNOWLEDGEMENT
We extend our thanks and gratitude to our Scientists (Mr.
- Gopi Krishna (Sc.D.) – DRDL Hyderabad) for his invaluable guidance for helping our project. We would like to convey our sincere thanks to them for their consistent noble guidance, continuous support and valuable suggestions which inspired us to make this report fruitful. There are many more who cannot be forgotten, and we whole heartedly thank each andevery one who graciously helped us directly when we were in need.
- REFERENCES
-
- David v Hutton, fundamentals of finite element analysis, the McGraw Hill publishers, first edition, 2004
- Edin unje, Emir Neziri, Analysis of Stress in Tori spherical Head of Pressure Vessels, 1st International Research/Expert Conference Manufacturing and Advanced Technologies, MAT 2010, Mostar Bosnia and Herzegovina, 18-20 November 2010
- Sourabh Lawate and B. B. Deshmukh Analysis of Heads of Pressure Vessel, International Journal of Innovative Research in Science, Engineering and Technology- Vol. 4, Issue 2, February 2015 ISSN(Online): 2319 8753
- C. Anil Kumar Reddy, T. KasiVaraprasada Rao, M. Joshi. “Design integration and analysis of nose dome for application of external pressure, Materials Today: Proceedings, 2020
- V.B. Bhandari, Design of Machine Elements, Tata McGraw Hill Publishing Co. Ltd, New Delhi, 2005
- X. Charles, Stress Analysis of Pressure Vessel Due to Load and Temperature, Middle East Journal of Scientific Research 20 (11): 1390-1395, 2014