
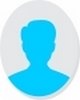
- Open Access
- Authors : Mehraj , K. Sai Priyanka , D. Govardhan
- Paper ID : IJERTV10IS050464
- Volume & Issue : Volume 10, Issue 05 (May 2021)
- Published (First Online): 05-06-2021
- ISSN (Online) : 2278-0181
- Publisher Name : IJERT
- License:
This work is licensed under a Creative Commons Attribution 4.0 International License
Aerodynamic Design of Missile Maintaining High L/D by Increasing Lift and Minimizing Drag
Mehraj *, K. Sai Priyanka**, D. Govardhan***
Research Student*, Assistant professor**, Head of the Department*** Department of Aeronautical engineering,
Institute of Aeronautical Engineering, Dundigal-500043
Abstract:- This paper is about the objective of the aerodynamic design is to maximize L/D by increasing the lift and minimizing the drag. For this the missile aerodynamics is studied. In missile the whole payload is carried in its nose, and to reduce the drag of missile its nose cone shape has to be changed. In general, the body of missile will have a nose section, a cylindrical section and a rear section in the shape of a boat-tail or flare. The shape of the nose may be a cone, a circular arc ogive, a parabola, an ellipse, a hemisphere, or one of a number of other shapes derived as per specific purpose. Drag is the main component in the design of missile. Keeping in mind that we have to reduce the missile is designed in such a way that it will produce high lift also. And also, the aerodynamic efficiency has to be high. So, a missile design is experimented in an aerodynamic design tool DATCOM. The commercial CFD solver ANSYS is utilized as the computational tool where as a research code developed by the authors is implemented as the semi-empirical tool. First the code is executed in CFD and further in DATCOM. The result is aerodynamic efficiency is high, lift is high and drag is reduced.
Keywords:- Missile aerodynamics, CFD, DATCOM, Wind tunnel, FLUENT, Aerodynamic efficiency, Bernoulli's principle, Newtons Laws.
INTRODUCTION
Aerodynamics is the flow of air through an object. It is divided as Aero and Dynamics. That is aero means air and dynamics is study of bodies under force. Fluid is allowed to flow through an object and its aerodynamic study is carried out. When any aircraft or missile is built first comes its aerodynamic study. It is designed on the basis of their aerodynamic study only. As in the case with aircraft, on the basis of its aerodynamic study there are four forces acting on an aircraft.
BASICS OF AERODYNAMICS
Lift is a force developed on wings gives rise to a carry over lift on body itself. Drag, which holds it back and thrust, which moves the airplane. The fourth one is its weight acting downwards.
Lift can be properly explained by using Bernoulli's principle. Bernoulli's principle states that the pressure of a moving gas decreases as its velocity increases. In case with aircraft the shape of the wing which airfoil, it is a curve. So, when the air flows through it the pressure above the surface is less and below the surface it is more. That results in high pressure at lower surface then the pressure at upper surface. So, because of high pressure the lift is produced.
A resistance force is produced when the body is in air and this force is called as drag. It is also called as wind resistance or fluid resistance. For laminar flow the drag is directly proportional to velocity. For turbulent flow the drag is proportional to square of the velocity.
NOSE CONE DRAG REDUCTION IN MISSILE
Nose cone is a drag reducing aerospike used to reduce forebody pressure aerodynamic drag of the blunt bodies at supersonic speeds. This creates a shock wave ahead of body where a recirculating flow occurs reducing the drag.
The blunt cone shape produces more drag when compared to cone shape and parabolic/ spherical shape. We can study the effect of shape on drag by comparing the values of drag coefficient for any two objects as long as the same reference area is used and the Mach number and Reynolds number are matched. A flat plate gives the highest drag and a streamlined symmetric airfoil gives the lowest drag.
LITERATURE SURVEY
A REVIEW ON NOSE CONE DESIGNS FOR
DIFFERENT FLIGHT REGIMES (Aditya Rajan Iyer, Anjali Pant)
In the paper it is discussed about the different nose cone designs for high performance vehicles that a designer to choose a nose cone with appropriate aerodynamic efficiency and geometry.
The nose cone is selected by considering its aerodynamic guidance and structure. The generally used aerospace applications are Conic, spherically blunted conic, bi-conic, tangent ogive, spherically blunted tangent ogive, secant ogive, elliptic, parabolic, power series and Haack series.
For the shape of nose cone, fineness ratio, bluffness ratio are the factors influencing pressure drag. Ratio of length of nose cone to its base diameter is fineness ratio. As the fineness ratio increases the wetted drag increases and then skin friction component of drag increases. As the fineness ratio and
Mach number increases overall drag decreases. Drag is compared based on skin friction drag, wave drag and base drag. The following plots and numerically generated contours help us understand the flow interaction with different nose cone profiles.
Velocity contour for ogive section Velocity contour for parabolic
at Mach 0.8
section at Mach 0.8
Velocity contour for elliptic section at Mach 0.8 2.2.4Conical at Mach 0.8
As angle of attack increases the adverse pressure gradient becomes more. A pair of vortices are formed, catastrophic yaw is developed as the vortices pair moves aft. As Cp local gets minimum or close to zero the adverse gradient weakens. Analytical method to calculate the three drag components: The equation makes use of the wetted area and viscosity to determine the drag and is measured at zero angle of attack.
For hypersonic regime only blunt nosecone is applicable, the sharp nose cone is prohibited due to adverse heat transfer characteristics. To reduce drag and heat flux the modifications in flow and shock structure is important.
For hypersonic regime only blunt nosecone is applicable, the sharp nose cone is prohibited due to adverse heat transfer characteristics. To reduce drag and heat flux the modifications in flow and shock structure is important.
-
Shock structure and detachment for fitness ratios, on the left is spherically blunted nose cone and on the right is parabolic.
-
A QUANTITATIVE COMPARISION OF DRAG CHARACTERISTCS
Finally, the conclusion is for a subsonic flow regime, where Von Karman is preferred for slightly above subsonic to transonic. For supersonic flow more than the design it is a compromise between the different kind of drags and for hypersonic geometric parameters of the nose cone have to selected in accordance because of aerodynamic heating is a crucial problem.
METHODOLOGY
First the code is written in the MATLAB software then transferred to Missile DATCOM. This is also done first for the nose then for body. Later the same process is carried on with fins. For all Mach speeds the configurations are noted. Figure shows the flowchart for body alone axial force calculations and is marked with the processes that have been updated to increase the accuracy of the aerodynamic predictions. Three areas of related changes are apparent from Figure. They correspond to the purely subsonic, the transonic, and the supersonic regions.
Axial Force Methodology for Missile DATCOM 7/0
PROCEDURE
Various techniques are used in aerodynamic analysis
-
analytic,
-
empirical/semi-empirical
-
numerical
-
experimental. In this report, few techniques are illustrated. Analytic In the conceptual design steps, empirical and semi-empirical tools are implemented to provide quick yet less accurate results. As the design proces evolves towards the final design, higher fidelity tools such as computational and experimental techniques are applied for more accurate results. The findings of the experimental, computational, and empirical approaches are compared and presented as a contribution to the available database for researchers.
The commercial solver tool CFD is used and a code was developed or generated and executed in missile DATCOM. ANSYS FLUENT is a commercial CFD code which uses a cell-centered finite volume method and has been proven to work well for different flow regimes around missiles. Empirical/semi-empirical in this method the software used is MATLAB. They are divided into four groups. The first group handles geometrical inputs of missile.
The second set of subroutines estimate the missile drag. It estimates the drag components. The total drag is calculated as algebraic sum of drag components. The third group is lift and moments estimations. The overall drag estimation is done by summing the individual drag components. The final group includes the estimation of aerodynamic derivations with respect to flight parameters. Numerical method in this method all the formulation and calculations are done.
MATLAB solves some of part of calculations. These are further used in DATCOM to generate the result Experimental method Here the experiment is practically conducted and the readings are noted to calculate the result. like in wind tunnel the prototype is put and in presence of flow is fluid experiment is conducted and result is known. GEOMERIC MODELLING Missile DATCOM is an
aerodynamic design tool. It is used to produce useful and accurate aerodynamic characteristic of any missile. Through careful comparison between the wind tunnel/extrapolated data and that produced by Missile DATCOM, validation of the Missile DATCOM product became possible, thus furthering its use as a predictive tool in conceptual and preliminary design efforts.
DISCUSSION AND RESULT
The code is executed in missile DATCOM then the results were generated. And the result stated lift is high, drag is low and aerodynamic efficiency is high. Missile DATCOM was able to predict the force coefficient for finned projectiles at low angle of attack, but it could not predict the center of pressure location. The aerodynamic data sources were compiled to improve the accuracy of the aerodynamic database used in flight trajectory simulations. The optimizations in DATCOM and Fluent are compared and the result is in DATCOM, rectangular tails perform better than swept ones, in fluent it is opposite. The increasing the length of fin span produced more lift, the wing sweep angle resulted drag reduction. And distancing the wing and tails helped in improving the aerodynamic efficiency. The coefficient from DATCOM can give some errors. Impact drift errors are much smaller than impact range errors, the greater the elevation angle the more error in drift and range. simulated angle of attack, side slip angle, and spin rate are inaccurate.
CONCLUSION
The objective of the aerodynamic design is to maximize L/D by increasing the lift and minimizing the drag. For any missile or aircraft, the main aim is to decrease the drag and increase the lift. And also maintaining the aerodynamic efficiency high. Aerodynamic efficiency is nothing but lift- to-drag ratio (or L/D ratio). An airplane has a high L/D ratio if it produces a large amount of lift or a small amount of drag. An aircraft with a high L/D ratio can carry a large payload, for a long time, over a long distance. L/D ratio is also equal to the ratio of the lift and drag coefficients. So, the aerodynamic efficiency is maintained high. As the angle of attack increases the lift increases. Drag has to reduce for the aircraft to maintain its flight.
REFERNCES
-
Aditya Rajan Iyer, Anjali Pant A REVIEW ON NOSE CONE DESIGNS FOR DIFFERENT FLIGHT REGIMES Volume: 07 Issue: 08 | Aug 2020.
-
B.Kaleeswaran, S.Ranjith Kumar, Jeniwer Bimro.N An Aerodynamic Optimization of Supersonic Flow Over the Nose Section of Missiles Vol. 2 Issue 4, April 2013.
-
Joseph D Vasile, Joshua T Bryson, and Frank E Fresconi Aerodynamic Design Optimization of Long-range Projectiles Using Missile DATCOM ARL-TR-8936 APR 2020.
-
Xinghui Yan, Jihong Zhu, Minchi Kuang, Xiangyang Wang Aerodynamic shape optimization using a novel optimizer based on machine learning techniques.
-
Teo, Hoon Hong AERODYNAMIC PREDICTIONS, COMPARISONS, AND VALIDATIONS USING MISSILELAB AND MISSILE DATCOM December 2008.
-
Pawat Chusilp, Weerawut Charubhun, and Navapan Nutkumhang A Comparative Study on 6- DOF Trajectory Simulation of a Short-Range Rocket using Aerodynamic Coefficients from Experiments and Missile DATCOM19-21 October, 2011, Krabi.
-