
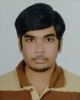
- Open Access
- Authors : M Sreekar , D. Govardhan , R . Sabari Vihar
- Paper ID : IJERTV10IS050473
- Volume & Issue : Volume 10, Issue 05 (May 2021)
- Published (First Online): 07-06-2021
- ISSN (Online) : 2278-0181
- Publisher Name : IJERT
- License:
This work is licensed under a Creative Commons Attribution 4.0 International License
Comparative Study of structural Analysis on Delta wings with and without Sweep Angles
M. Sreekar
Student, Aeronautical Engineering,
Institute of Aeronautical Engineering , Hyderabad , India .
D. Govardhan
Head of Department, Aeronautical Engineering,
Institute of Aeronautical Engineering, Hyderabad , Indian
R. Sabari Vihar
Assistant Professor , Aeronautical Engineering,
Institute of Aeronautical Engineering , Hyderabad , India .
Abstract – Delta wing aircrafts are the aircrafts which have large root cord aerofoil and thin tip aerofoil making it structurally efficient with strong structure and light weight. Larger root aerofoil can resist higher loads on the surface of the aircraft wing and also on the tip. The swept wing aircraft are the aircraft whose wings have a sweep angle with reference to the root aerofoil . There are two swept wing configurations, they are Forward swept and Backward swept. Same structural Load is applied on the three types of delta wings. The Delta wings are placed in the same streamline flow with same velocity and the pressure developed on the surface is taken as load for structural analysis . The concept of swept Delta wings were implemented from the time of World War II for their aerodynamic benefits. It is observed that delta wings have structural advantage due to their large root chord support which can help them to sustain higher loads even during the manoeuvres . The structural Analysis of the wing structures are performed by using ANSYS 2021 R1 software. The comparative study mostly focusses on the rate of deformation of the wings under the given load and the stresses developed on the wing surfaces on the whole . The study of the results are discussed in this paper.
Keywords : Delta Wing , Swept Wings , Root Aerofoil , Loads , Structural Analysis and Deformation
-
INTRODUCTION:
Many aircrafts that travel at Sonic and supersonic speeds have delta shaped wings . Particularly the Delta wing aircrafts and space crafts fly at superior angle of attacks as they have a better and desirable aerodynamic advantage , on the other hand they cannot fly at lower angles of attack . Understanding the essence of unsteady flows around delta wings, as well as related phenomena like vortex breakup and vortex-shock patterns, becomes more relevant as the manoeuvrability of such aircraft improves. It is common knowledge that in the steady state a shear layer separates from the leading edge during delta wing flight, resulting in two counter-rotating vortices. On the leeside of the wing, the leading edge is isolated from the trailing edge, resulting in two counter-rotating vortices. As a result, large suction
peaks are formed, resulting in the generation of lift. The secondary vortices are two much smaller vortices with the same sense of rotation as the main vortices. Under certain flow conditions, it can also shape. The delta wings have comparatively higher resistance to deformation and stresses than the conventional wings of normal aircrafts . The reason is that the root cord of delta wing is larger than the tip cord creating a larger wing span . The delta wings are comparatively light in weight and also due to large internal volume , will be able to store more fuel . Mostly these Delta wings are installed in Combat aircrafts as they can resist high pressure loads while manuvering in the combat situation.
-
METHODOLOGY:
The main aim of this project is to perform a comparative study on the structural analysis on the delta wings when they are placed in an airflow with 0.8 Mach speed and at the altitude of 6km above the surface of the earth . There are different types of delta wings namely Forward Swept , Normal Delta wings and Backward Swept Delta wing .These delta wings are mainly used in the combat aircrafts as they can have higher structural resistance even at high aerodynamic pressure developed due to quick turns in warfare . The forward swept wings were highly chosen at the time of world war II . These delta wings have different aerodynamic properties and also different structural resistance . If the angle of attack is varied in the delta wing then the pressure distribution also changes paving way for more structural pressure to get acted on the surface of the wings .These wings are modelled in CATIA V5 software . The aerofoil chosen for this project is NACA 64A206 . The deformation after the application of the aerodynamic pressure is calculated in the computational structural analysis method by using the software ANSYS 2021 R1 . The deformation on the wings is compared at variation of angle of attack along with the stress distribution across the wings . The material of the wing is chosen same for the three delta wing configurations , i.e , Aluminium Alloy .
III . MODELLING :
The Delta wing is modelled using the software CATIA V5 . The airfoil choosen for the wing model is NACA 64A206 . The root chord of the wing aerofoil is taken to be 10m and the tip of the wing aerofoil is 2m . The length of the wing is taken to be 5m . The same configuration is applied to the swept delta wings with certain sweep angle . The Swept Back Angle is given 20° . and also for the swept Forward wing with forward sweep angle of 20° .
Fig 1. Delta Wing Dimensions
Fig 2. Back Swept Delta Wing Dimensions
Fig 3. Forward Swept Delta Wing Dimensions
These dimensional configurations are drafted using AutoCAD software and then the process has started for 3D modelling of the wing .
The airfoil NACA 64A206 coordinates are downloaded from the airfoil tools website . The airfoil coordinates are then downloaded in the form of CSV file in MS Excel and then imported into the Catia V5 software . The airfoil spline points are joined and then another airfoil with 2m chord length is imported into the CATIA v5 software at a distance of 5 m from the root aerofoil . These aerofoils are joined with multi sections solid option and then a wing is formed in the Catia Software . Then the same airfoil coordinates are used for Swept back and Swept forward configurations with appropriate sweep angle and then solidified into one single wing.
Fig 4. NACA 64A206 Airfoil Tools
Fig 5. Importing Coordinates in CATIA V5
Fig 6. 3D Delta Wing
Fig 7.3D Backward Swept Delta Wing
Fig 8. 3D Forward Swept Delta Wing
-
CFX AND STRUCTURAL ANALYSIS: ANSYS 2021 software is used for CFX analysis of the delta wings . The FEA method is used to mesh the wing surfaces and the size of the mesh element is taken to be 1m . The CFX analysis is first done on Delta wing and an enclosure surface is created over the surface of the wing with 10m dimensions in the shape of cube . The surface of the wing is taken and united with the enclosure surface for Flow simulation and Analysis . The mesh is generated with the specified size of the element on the three delta wing configurations separately
.The shape of elements of the mesh is tetrahedron . An airflow of 0.8 Mach i.e 253.144 m/s at the altitude of 6km above the earth surface according to the ISA model . The flow properties are specified below :
TABLE 1. FLOW PROPERTIES
S.no
Variables
Value
1
Temperature
249.2K
2
Pressure
47217
3
Density
0.6601 kg/m
4
Viscosity
1.6047E-5 kg/ms
5
Speed of sound
316.4309 m/s
Fig 9. Delta wing CFX mesh
Fig 10. Backward Swept Delta Wing CFX mesh
Fig 11. Forward Swept Delta Wing CFX mesh
These elements are then used for CFX flow simulation analysis to find the pressure distribution across the wings to use the pressure as loads in structural analysis . The flow properties are then assigned to the flow and then Inlet , Outlet , Wall boundaries are created in the CFX . The flow is then generated in the enclosure geometry across the wing and thus pressure is created across the wing surface . Then the Angle of attack of the wings are changed from -5 to 5 and 0 degrees respectively in each of the three wings and the pressure distribution across the wings in each angle of attack is noted . Due to the change in angle of attack , the flow also changes creation a variation in the pressure . These angle of attack conditions are also considered for further structural analysis to find the deflection and stress developed in each case across the three wings .
Fig 12. Delta Wing Pressure contour at -5 AOA
Fig 13. Delta Wing at 0 AOA
Fig 14. Delta Wing at 5 AOA
Fig 15. Backward Swept Delta Wing Pressure Contour at -5 AOA
Fig 16. Backward swept delta wing at 0 AOA
Fig 18. Forward Swept Delta Wing Pressure Contour at -5 AOA
Fig 19. Forward Swept Delta Wing at 0 AOA
Fig 20. Forward Swept Delta Wing at 5 AOA
Due to this pressure distribution across the wings at 0.8 Mach velocity of air , deflection due to stresses is formed and the deflections in the wings are compared in this study . The structural Analysis is performed on the three wing configurations at different angle of attacks to find respective deflections . The Material Properties of the wings are given as below
Fig 17. Backward swept delta wing at 5 AOA
TABLE 2. MATERIAL PROPERTIES
S.No
Variable
Value
1
Material
Aluminum Alloy
2
Youngs Modulus
71 GPa
3
Density
2770 kg/m3
4
Bulk Modulus
69.6 GPa
5
Poisons Ratio
0.33
The above material properties are specified on the three delta wings and structural analysis is performed to find the equivalent stress distribution across the surface of the wing and the deformation produced due to it .
-
RESULTS:
The structural analysis is performed by the applying the pressure loads obtained due to the flow distribution across the surface of the three wings at different angles of attack . This pressure is applied on the upper and lower surfaces according to the values obtained . A fixed support is inserted at the mid of the wing structure in the structural Analysis . Now max deflections and Maximum equivalent stress developed are noted for comparative study .
TABLE 3. Structural Analysis Results at 0° Angle of Attack :
Sno |
Type of Wing |
Maximum Stress |
Maximum Deflection |
1 |
Delta Wing |
1.77e+06 |
0.00292m |
2 |
Swept Back Delta Wing |
2.38e+06 |
0.0056m |
3 |
Swept Front Delta Wing |
5.9603e+06 |
0.0073m |
Fig 21. Delta Wing Deflection
Fig 22. Delta Wing Stress Distribution
Fig 23. Backward Swept Delta Wing Deflection
Fig 24. Backward Swept Delta Wing Stress Distribution
Fig 25. Forward Swept Wing Deflection
Fig 26. Forward swept Delta wing Stress distribution
TABLE 4. Structural Analysis Results at 5° Angle of Attack :
Sno |
Type of Wing |
Maximum Stress |
Maximum Deflection |
1 |
Delta Wing |
4.78e+06 |
0.00805m |
2 |
Swept Back Delta Wing |
4.2034e+06 |
0.0096m |
3 |
Swept Front Delta Wing |
3.21e+06 |
0.0035m |
Fig 27. Deflection on Delta Wing at 5° Angle of Attack
Fig 28. Stress Distribution on delta wing at 5° Angle of attack
Fig 29. Deflection on Swept Back Delta Wing at 5° Angle of attack
Fig 30. Stress Distribution on Swept Back Delta Wing at 5° Angle of attack
Fig 31. Deflection on Swept Forward Delta wing at 5° Angle of attack
Fig 32. Stress Distribution on Swept Forward Delta Wing at 5° angle of attack
TABLE 5. Structural Analysis Results at -5° Angle of Attack :
Sno |
Type of Wing |
Maximum Stress |
Maximum Deflection |
1 |
Delta Wing |
4.89e+06 |
0.008m |
2 |
Swept Back Delta Wing |
3.52e+06 |
0.0076m |
3 |
Swept Front Delta Wing |
1.68e+06 |
0.001 |
Fig 33. Deflection of delta wing at -5° of angle of attack
Fig 34. Stress Distribution on Delta wing
Fig 35. Deflection on Backward Swept Delta Wing at -5° of angle of attack
Fig 36. Stress Distribution on Backward Swept Delta Wing at -5° of angle of attack
Fig 37. Deflection on Forward Swept Delta Wing at -5° of angle of attack
Fig 38. Stress Distribution on Forward swept Wing at -5° of angle of attack .
-
. CONCLUSION :
There are several structural advantages with the delta wings and these make them more selective in the Combat aircrafts
. The larger wing span enables the distribution of stress more effectively and helps to reduce the deflection comparatively
. A delta wing blends low relative wing thickness with a sufficiently thick wing spar for a lightweight construction due to the broad root chord. Delta wings are particularly attractive for supersonic aircraft because their low relative thickness reduces wave drag (a drag component that only occurs in supersonic flow). The delta wing's broad root chord allows it to have a large internal fuel volume despite its thin relative thickness. The long root chord also offers a large surface area, which aids in lowering the aircraft's minimum speed which means it can fly easily at minimum initial speed quickly in case of warfare .
But , the normal delta wing also has some advantages compared to Swept wings . The delta wing has structural benefits as well as high-speed and low-speed flight capabilities. The delta wing aircraft can travel at 0 angle of
attack effectively with higher structural resistance for faster transportation during emergencies .
Fig 39. Bell X1
This project has discussed about the comparative study of the structural parameters that define the resistance and stress distribution on the delta wings at different sweep angles and at different Angles of Attack. The results show that at 0° angle of attack the deformation of the delta wing is lesser than the swept Back and swept forward delta wings , i.e , 0.00292m and also the stresses developed across the surface was comparatively low . When the angle of attack is increased at 5° , the flow distribution created more pressure on the upper surface than the lower one . In this case , the deflection on Forward swept Delta wing is much less i.e , 0.0035m , depicting more structural resistance than the other two configurations . In the case of lower angle of attack , i.e
-5° , the flow over the lower surface has increased creating high pressure region in the lower surface . The lowest deflection was observed on the forward swept wing wit just 0.001m . This proves that at higher angle of attacks , the forward swept wing has offered more structural resistance comparatively . High manuvering aircrafts mostly equip with Forward swept wings for this reason . Some of the great maneuverable aircrafts like Convair XB-53 and Sukhoi su- 47 have forward swept wings . Convair XB-53 was a US airforce aircraft which was made in 1945 . History also says Forward swept aircrafts were experimented during the World War II .
So , we can conclude that the delta wings with Sweep angles are highly efficient aerodynamically and structurally at higher angle of attacks and while manueuvering in the air at higher altitudes , where as the Delta wing aircraft without sweep angle is efficient both at higher speed as well as lower speeds and angle of attacks . Due to the sweep angles the aera of the wing is expanded which gives them an advantage for more stress distribution and less Deflection comparatively and especially at Higher angle of attacks .
-
. REFERENCES: