
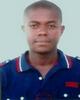
- Open Access
- Authors : Nnorom Obinichi , Alexander N. Okpala , Tolumoye J. Tuaweri
- Paper ID : IJERTV10IS050346
- Volume & Issue : Volume 10, Issue 05 (May 2021)
- Published (First Online): 11-06-2021
- ISSN (Online) : 2278-0181
- Publisher Name : IJERT
- License:
This work is licensed under a Creative Commons Attribution 4.0 International License
Impact of Flow Rate on Wax Deposit on Corrosion of Crude Oil Pipeline
Alexander N. Okpala
Mechanical Engineering,
Niger Delta University, Wilberforce Island, Bayelsa State, Nigeria
Tolumoye J. Tuaweri Mechanical Engineering, Nigeria Maritime University, Okerenkoko, Delta State
Nnorom Obinichi*
Mechanical Engineering, University of Port Harcourt, Choba, Port Harcourt, Nigeria
Abstract:- The aim of this research is to study the effect of flow rate on wax deposition on corrosion of crude oil pipeline at varying temperature with time. The waxy crude oil is pumped into the experimental flow-loop set up under different operating conditions. The effect of flow rate on corrosion at different flow rate of wax deposition during the corrosion inhibition were studied at varying temperature with time at 15, 20, 25, 30 and 35oC and at 3, 6, 9, 12, 15 and 18 min while keeping flow rate constant for each experimental run at 10.21, 20.37, 30.45, 40.28, 50.70 L/min, to investigate the corrosion rate against time. The results showed that at temperature of 15oC and time 18 min at constant flow rate of 10.21 L/min, the corrosion rate is 0.15 mpy. At temperature of 15oC and time 18 min at constant flow rate of 20.37 L/min the corrosion rate is 0.11 mpy. At temperature of 20oC and time 18 min at constant flow rate of 30.45 L/min the corrosion rate is 0.19 mpy. Based on the results, a significant reduction of corrosion rates and excellent corrosion protection is achieved while others provided only moderate or negligible protection to the crude oil pipeline. But the wax layer becomes thicker with time, if the temperature stays below the WAT for extended period of time, and can in the long run, cause partial or total blockage of the pipe. Hence, it is concluded that as the wax deposition increases the corrosion rate decrease. The protection of paraffins can be assumed to be due to physisorption caused by relatively weak intermolecular forces such as van der Waals forces. This proves that deposited paraffin wax act as a protective layer to inhibit corrosion on the crude oil pipeline. But most of the corrosion protection has been lost due to the long chain paraffin layer being physically removed from the surface during the periods of increased flow rate or temperature.
Keywords Flow rate, Corrosion, Pipeline.
-
INTRODUCTION
Transport processes in oil and gas pipelines play an important role in industry. There are a few phenomena- such as corrosion, scale and wax deposition or clathrate hydrate formation-which reduce the efficiency of these processes (Gjermundsen, 2006). In that, great portion is due to internal corrosion and wax deposition in transportation utilities. Moreover, CO2 corrosion can cause damage in the pipeline material by deteriorating the pipelines material. On finding the factors that cause corrosion and factors causing wax precipitation many experiments have been conducted individually. But relating both the problems together only a few research have been conducted. Much research work that studies the relationship between paraffin wax deposition and corrosion behavior have not been investigated (Petrowiki, 2015). Though flow in the pipeline can be restricted by paraffin wax, it acts as a corrosion inhibitor by covering the inner wall of pipeline. Many of the problems in oil and gas industry is caused by paraffin wax and CO2 corrosion. These problems mainly caused in the transportation and utilities where the pipelines are severely corroded. The paraffin wax on the surface provide excellent corrosion protection, while others provided only moderate or negligible protection in the crude oil pipeline, but most of the corrosion protection has been lost due to the long chain paraffin layer being physically removed from the surface during the periods of increased temperature or increased flow rates (Morales et al., 2000). The protection of paraffin can be assumed to be due to physisorption caused by relatively weak intermolecular forces such as van der Waals forces. Paraffin can precipitate and deposit on the pipe surface despite the lack of surface chemical activity, at low temperatures-below the so called wax appearance temperature (WAT). It can slow down corrosion processes by hindering the diffusion of corrosive species to the surface when the wax layer covers the steel surface. The wax layer becomes thicker with time if the temperature stays below the wax appearance temperature (WAT) for extended period of time, and can, in the long run, cause partial or total blockage of the pipe. Crude oils can generate corrosion inhibition based on reaserch, but the extent of inhibition varied from one crude oil to another.
A very complex phenomenon is the paraffin wax deposition, which in pipelines and production equipment is one of the main unsolved challenges in Flow Assurance (Petrowiki, 2015). One of long standing problem in the oil industry is that of paraffin wax deposition. Crude oils often contain paraffin which precipitate and adhere to the liner, tubing, sucker rods and surface equipment as the temperature of the producing stream decreases in the normal course of flowing, gas lifting or pumping. Because they reduce the effective size of the flow conduits and restrict the production rate from the well, heavy paraffin deposits are undesirable (Petrowiki, 2015). The removal of the deposits by mechanical, thermal or other means is require,
resulting in costly down time and increased operating costs where severe paraffin deposition occurs. From treatments designed to remove waxy deposits from production tubing or squeeze treatments designed to inhibit wax deposition significant operating costs are incurred (Petrowiki, 2015). The formation damage and loss of production costs are increased further that may result from these treatments. Paraffin deposits in the production tubing, wellbores and flowlines. Paraffin deposition may occur also in the producing formation under certain conditions. Flow restriction is a problem caused by the wax deposits, which leads to increased flow line pressure, mechanical problems, and decreased production (Offshore-mag.com).
Corrosion in steel pipelines is another problem that is face by the oil and gas industry. Corrosion is an electrochemical process that occurs due to the presence of anode and cathode sites on the materials surface, originating from the heterogeneous nature of the bulk material and its surface. The presence of an electrolyte and electrical connection is also essential for electrochemical corrosion to occur. The bulk material and its surface provide the anode, cathode and the electrical connection, while for example, humid air, aqueous solution, etc., provide the electrolyte to complete the corrosion circuit. When it comes to corrosion of carbon steels in the oil industry, the main reason for its occurrence, is the presence of dissolved carbon dioxide CO2 (sweet corrosion), hydrogen sulfide H2S (sour corrosion) and oxygen in the oil, and sodium chloride dissolved in water injections, and due to the use of acids during the oil and gas well acidizing (Smith, 1999; Villamnar et al., 2007; Rodriguez-valdez et al., 2006; Kermani and Morshed, 2003). In other industries, corrosion occurs for example, during the materials acidization using acid solutions in pickling processes, during the industrial acid cleaning, in various aqueous electrolyte storage tanks, in boilers, and during the removal of rust, scale and corrosion products (Lebrini et al., 2007; Shein and Denisva, 2006; Bentiss et al., 2000; Morad and Kamal, 2006).
Removal of any one of the above mentioned corrosion factors (anode/cathode surfac sites, electrolyte) results in the termination of the electrochemical corrosion process. Unfortunately, in reality, it is impossible to fully achieve this, but there exist methods of reducing the influence of one or more of these factors, and thus reducing the kinetics of the corrosion process,
i.e. decreasing (slowing down) the corrosion rate. The most common way of mitigating the internal-walls corrosion in industrial facilities is by corrosion inhibition (pipelines, tanks, reactors, etc). Organic compounds containing nitrogen, sulfur and/or oxygen atoms are most of the well-known corrosion inhibitors (Alsabagh et al., 2006; Deyab, 2007). The modification of metal surfaces by the surface adsorption of these molecules and the subsequent formation of a protective (blocking) surface layer that minimizes access of the corrosive electrolyte to the surface is where the corrosion protection by these inhibitors is based. Of particular interest are those molecules that form self-assembled-monolayers (SAMs) on the metal surface, since these types of layers have been shown to offer better protection and tailoring (functionalization) properties than non-structured (amorphous) adsorbed layers. Over the years, the use and development of corrosion inhibitors have been continuously increasing.
Finding the factors that cause corrosion and wax deposition, numerous experiments have been conducted individually. There exist some studies on how to prevent the separate problems, but very little work on the possible synergism/competition between these different processes. However, such interplay can be very important. However, wax deposits can promote corrosion inhibition by formation of wax layers on the internal pipeline surface and hinder access of the corrosive water to the pipeline surface, reducing the loss of metal due to corrosion. Waxy crudes characteristics vary from location to location. Waxy crudes and its effect on corrosion of crude oil pipeline from Niger Delta oil fields have not received sufficient research attention compared to other crudes globally.
-
MATERIALS AND METHODS
2.1 MATERIALS
Experimental laboratory flow loop to investigate the effect of flow rate on corrosion of crude oil pipeline are shown in figure
2.1. Other materials used are waxy crude oil, a 0.5hp pump for re-circulating the waxy crude oil, flow meter with a temperature probe, ball valves for regulating the flow of the fluid, electronic weighing balance, electric cooker, handheld infrared thermometer for temperature measurement and MS1000 Corrosion Meter to measure the corrosion rate against time in the crude oil pipeline.
Figure 2.1: Schematic Diagram of the Experimental Laboratory Flow Loop
2 METHODS
To study the effect of flow rate on corrosion of crude oil pipeline, the waxy crude oil sample is pumped into the flow-loop set up under different operating conditions. The range of the inlet temperature of the waxy crude oil was (10-40oC). The experiment was conducted 5 times, at time interval of 3-18 minutes, temperature were varied between 15-35oC and flow rate were also varied between 10.21-50.70 L/min. The experiment was carried out at varying temperature with time while flow rate was kept constant. At temperature of 15, 20, 25, 30 and 35oC and time at 3, 6, 9, 12, 15 and 18 min while keeping flow rate constant for each experimental run at 10.21, 20.37, 30.45, 40.28, 50.70 L/min, to determine the corrosion rate against time. After testing the corrosion rate of the waxy crude oil to ascertain the effect of flow rate at varying temperature and time of the paraffin wax deposited on the crude oil pipeline. The results were recorded, the graph of corrosion rate (mpy) against time (min) was plotted and the results were analyzed.
-
RESULTS AND DISCUSSION
Table 1 to 3 and figure 1 to 3 illustrates the effect of flow rate on wax deposition on corrosion of crude oil pipeline which were examined and the results were analyzed.
Corrosion Rate (mpy)
Corrosion Rate (mpy)
Table 1: Effect of Flow Rate at 10.21 L/min on Corrosion Rate against Time on Wax Deposition
Time (min) |
Corrosion Rate (mpy) @15oC |
Corrosion Rate (mpy) @ 20oC |
Corrosion Rate (mpy) @ 25oC |
Corrosion Rate (mpy) @ 30oC |
Corrosion Rate (mpy) @ 35oC |
3 |
0.72 |
0.62 |
0.82 |
0.97 |
0.68 |
6 |
0.54 |
0.87 |
0.69 |
0.85 |
0.92 |
9 |
0.83 |
0.76 |
0.51 |
0.43 |
0.66 |
12 |
0.35 |
0.26 |
0.74 |
0.56 |
0.71 |
15 |
0.23 |
0.33 |
0.26 |
0.38 |
0.42 |
18 |
0.15 |
0.22 |
0.16 |
0.26 |
0.56 |
1.2
1
0.8
0.6
0.4
0.2
0
15
20
25
30
1.2
1
0.8
0.6
0.4
0.2
0
15
20
25
30
0 5
10
Time (min)
15
20
35
0 5
10
Time (min)
15
20
35
Figure 1: Graph of the Effect of Flow Rate at 10.21 L/min on Corrosion Rate against Time on Wax Deposition
Corrosion Rate (mpy)
Corrosion Rate (mpy)
Table 2: Effect of Flow Rate at 20.37 L/min on Corrosion Rate against Time on Wax Deposition
Time (min) |
Corrosion Rate (mpy) @15oC |
Corrosion Rate (mpy) @ 20oC |
Corrosion Rate (mpy) @ 25oC |
Corrosion Rate (mpy) @ 30oC |
Corrosion Rate (mpy) @ 35oC |
3 |
0.66 |
0.81 |
0.77 |
0.69 |
0.88 |
6 |
0.83 |
0.68 |
0.92 |
0.78 |
0.66 |
9 |
0.74 |
0.79 |
0.66 |
0.93 |
0.78 |
12 |
0.26 |
0.58 |
0.48 |
0.55 |
0.41 |
15 |
0.37 |
0.33 |
0.22 |
0.42 |
0.62 |
18 |
0.11 |
0.46 |
0.31 |
0.28 |
0.39 |
1
0.9
0.8
0.7
0.6
0.5
0.4
0.3
0.2
0.1
0
15
20
25
30
35
1
0.9
0.8
0.7
0.6
0.5
0.4
0.3
0.2
0.1
0
15
20
25
30
35
0 5
10
Time (min)
15
20
0 5
10
Time (min)
15
20
Corrosion Rate (mpy)
Corrosion Rate (mpy)
Time (min) |
Corrosion Rate (mpy) @15oC |
Corrosion Rate (mpy) @ 20oC |
Corrosion Rate (mpy) @ 30oC |
Corrosion Rate (mpy) @ 35oC |
|
3 |
0.82 |
0.94 |
0.85 |
0.94 |
0.71 |
6 |
0.79 |
0.88 |
0.66 |
0.57 |
0.92 |
9 |
0.96 |
0.73 |
0.59 |
0.82 |
0.68 |
12 |
0.43 |
0.54 |
0.38 |
0.46 |
0.81 |
15 |
0.31 |
0.29 |
0.22 |
0.33 |
0.51 |
18 |
0.41 |
0.19 |
0.32 |
0.24 |
0.36 |
Time (min) |
Corrosion Rate (mpy) @15oC |
Corrosion Rate (mpy) @ 20oC |
Corrosion Rate (mpy) @ 25oC |
Corrosion Rate (mpy) @ 30oC |
Corrosion Rate (mpy) @ 35oC |
3 |
0.82 |
0.94 |
0.85 |
0.94 |
0.71 |
6 |
0.79 |
0.88 |
0.66 |
0.57 |
0.92 |
9 |
0.96 |
0.73 |
0.59 |
0.82 |
0.68 |
12 |
0.43 |
0.54 |
0.38 |
0.46 |
0.81 |
15 |
0.31 |
0.29 |
0.22 |
0.33 |
0.51 |
18 |
0.41 |
0.19 |
0.32 |
0.24 |
0.36 |
Figure 2: Graph of the Effect of Flow Rate at 20.37 L/min on Corrosion Rate against Time on Wax Deposition Table 3: Effect of Flow Rate at 30.45 L/min on Corrosion Rate against Time on Wax Deposition
1.2
1
0.8
0.6
0.4
0.2
15
20
25
30
35
1.2
1
0.8
0.6
0.4
0.2
15
20
25
30
35
0
0
0
5
10
Time (min)
15
20
0
5
10
Time (min)
15
20
Figure 3: Graph of the Effect of Flow Rate at 30.45 L/min on Corrosion Rate against Time on Wax Deposition
The effect of flow rate on wax deposition on corrosion of crude oil pipeline were studied at varying temperature with time while keeping flow rate constant for each experiment and the results obtained were analyzed using table 1-3 and figure 1-3. The effect of flow rate on corrosion at varying temperature with time were conducted at temperature of 15, 20, 25, 30 and 35oC and time at 3, 6, 9, 12, 15 and 18 min while keeping flow rate constant for each experimental run at 10.21, 20.37 and 30.45 L/min, to determine the corrosion rate against time.
Based on the results of table 1, at temperature of 15oC and time 18 min at constant flow rate of 10.21 L/min, a significant reduction of corrosion rates and excellent corrosion protection is achieved while others provided only moderate or negligible protection to the crude oil pipeline.
The wax layer becomes thicker with time if the temperature stays below the WAT for extended period of time, and can, in the long run, cause partial or total blockage of the pipe.
It was observed that at time 3 min and at temperature of 15oC, the corrosion rate is 0.72mpy and 0.62 mpy at 20oC at the same time, 0.82 mpy at the same time and temperature of 25oC, 0.97 mpy at temperature of 30 oC, and 0.68 mpy at temperature of 35 oC. At time 6 min and temperature of 15 oC, 20 oC, 25 oC, 30 oC, and 35 oC, the corrosion rate were 0.54 mpy, 0.87 mpy, 0.69 mpy, 0.85 mpy, and 0.92 mpy respectively. At time 9 min corrosion rate were 0.83 mpy, 0.76 mpy, 0.51 mpy, 0.43 mpy, and
0.66 mpy in the order of the temperature respectively. At time 12 min in the order of the temperature were 0.35 mpy, 0.26 mpy,
0.74 mpy, 0.56 mpy, and 0.71 mpy respectively. At time 15 min corrosion rate were 0.23 mpy, 0.33 mpy, 0.26 mpy, 0.38 mpy, and 0.42 mpy in the order of the temperature respectively and at 18 min the corrosion rate were 0.15 mpy, 0.22 mpy, 0.16 mpy,
0.26 mpy, and 0.56 mpy respectively.
Based on the results of table 2, at temperature of 15oC and time 18 min at constant flow rate of 20.37 L/min, a significant reduction of corrosion rates is achieved while others provided only moderate or negligible protection to the crude oil pipeline. The wax layer becomes thicker with time if the temperature stays below the WAT for extended period of time, and can, in the long run, cause partial or total blockage of the pipe.
It was observed that at time 3 min and at temperature of 15oC, the corrosion rate is 0.66mpy and 0.81 mpy at 20oC at the same time, 0.77 mpy at the same time and temperature of 25oC, 0.69 mpy at temperature of 30 oC, and 0.88 mpy at temperature of 35 oC. At time 6 min and temperature of 15 oC, 20 oC, 25 oC, 30 oC, and 35 oC, the corrosion rate were 0.83 mpy, 0.68 mpy, 0.92
mpy, 0.78 mpy, and 0.66 mpy respectively. At time 9 min corrosion rate were 0.74 mpy, 0.79 mpy, 0.66 mpy, 0.93 mpy, and
0.78 mpy in the order of the temperature respectively. At time 12 min in the order of the temperature were 0.26 mpy, 0.58 mpy,
0.48 mpy, 0.55 mpy, and 0.41 mpy respectively. At time 15 min corrosion rate were 0.37 mpy, 0.33 mpy, 0.22 mpy, 0.42 mpy, and 0.62 mpy in the order of the temperature respectively and at 18 min the corrosion rate were 0.11 mpy, 0.46 mpy, 0.31 mpy,
0.28 mpy, and 0.39 mpy respectively.
Based on the results of table 3, at temperature of 15oC and time 18 min at constant flow rate of 30.45 L/min, a significant reduction of corrosion rates is achieved while others provided only moderate or negligible protection to the crude oil pipeline. The wax layer becomes thicker with time if the temperature stays below the WAT for extended period of time, and can, in the long run, cause partial or total blockage of the pipe.
It was observed that at time 3 min and at temperature of 15oC, the corrosion rate is 0.82mpy and 0.94 mpy at 20oC at the same time, 0.85 mpy at the same time and temperature of 25oC, 0.94 mpy at temperature of 30 oC, and 0.71 mpy at temperature of 35 oC. At time 6 min and temperature of 15 oC, 20 oC, 25 oC, 30 oC, and 35 oC, the corrosion rate were 0.79 mpy, 0.88 mpy, 0.66
mpy, 0.57 mpy, and 0.92 mpy respectively. At time 9 min corrosion rate were 0.96 mpy, 0.73 mpy, 0.59 mpy, 0.82 mpy, and
0.68 mpy in the order of the temperature respectively. At time 12 min in the order of the temperature were 0.43 mpy, 0.54 mpy,
0.38 mpy, 0.46 mpy, and 0.81 mpy respectively. At time 15 min corrosion rate were 0.31 mpy, 0.29 mpy, 0.22 mpy, 0.33 mpy, and 0.51 mpy in the order of the temperature respectively and at 18 min the corrosion rate were 0.19 mpy, 0.41 mpy, 0.32 mpy,
0.24 mpy, and 0.36 mpy respectively.
The protection of paraffins can be assumed to be due to physisorption caused by relatively weak intermolecular forces such as van der Waals forces. Morales et al. (2000)found that the paraffin wax film presence on the surface promotes a significant reduction of general corrosion rates, but although loss of integrity of the paraffin layer was observed relating to localized corrosion. But it can be concluded that most of the protection by corrosion has been lost due to the long chain paraffin layer being physically removed from the surface during the periods of increased temperature or flow rate.
CONCLUSION
Most of the problems in oil and gas industry is caused by paraffin wax and CO2 corrosion. These problems mainly caused in the transportation and utilities where the pipelines are severely corroded. The effect of paraffin wax on the corrosion of steel would allow a higher knowledge on the prevention CO2 corrosion in the steel pipelines. A laboratory flow loop system was designed and fabricated to investigate the factors affecting wax deposition on corrosion of crude oil pipeline. Based on this target experiments were conducted using a waxy crude oil. The linear polarization resistance method was used to investigate the corrosion rate against time. Based on the experiment conducted and results analyze, the paraffin wax act as a protective layer on to the steel and can provide minimal protection on the steel pipelines. The protection of paraffin can be assumed to be due to physisorption caused by relatively weak intermolecular forces such as van der Waals forces. The study shows that at room temperature, the effect of paraffin wax deposition on the corrosion of crude oil pipeline is that paraffin wax act as layer that protects the pipeline from corrosion.
REFERENCES
-
Alsabagh, A. M, Migahed, M.A, HayamAwad, S. (2006). Reactivity of polyester aliphatic amine surfactants as corrosion inhibitors for carbon steel in formation water (deep well water), Corrosion Science, 48, 813
-
Bentiss, F, Lagrenée M., Traisnel M. (2000). 5-Bis(n-Pyridyl)-1,3,4-Oxadiazoles as Corrosion Inhibitors for Mild Steel in Acidic Media, Corrosion, 56, 733.
-
Deyab, M.A. (2007). Effect of cationic surfactant and inorganic anions on the Electro-chemical behavior of carbon steel in formation water, Journal of Corrosion Science
-
Gjermundsen, I. (2006). State of the art: Wax precipitation deposition and aging in flowing hydrocarbon systems, Internal Hydro report, October,
Porsgrunn. International Journal of Petroleum Engineering
-
Kermani, M. B, Morshed A. (2003). Carbon Dioxide Corrosion in Oil and Gas Production A Compendium, Corrosion, 59, 659
-
Lebrini, M, Traisnel M, Lagrene M, Mernari B, Bentiss F. (2007). Inhibitive properties, adsorption and a theoretical study of 3,5-bis(n-pyridyl)-4- amino-1,2,4-triazoles as corrosion inhibitors for mild steel in perchloric acid, Journal of Corrosion Science, 50, 473.
-
Morad, M.S. Kamal, El-Dean A.M. (2006). 2,2'-Dithiobis(3-cyano-4,6-dimethylpyridine): A new class of acid corrosion inhibitors for mild steel,
Journal Corrosion of Science, 48, 3398.
-
Offshore-mag.com, (2015). Deepwater Challenges Paraffins:', 2015. [Online]. Available: http://www.offshore-mag.com/articles/print/volume- 57/issue-3/departments/technology-focus/deepwater-challenges-paraffins.html.
-
Petrowiki.org. (2015). Wax problems in production -',.[Online]. Available: http://petrowiki.org/Wax_problems_in_production.
-
Rodrguez-Valdez, L. M, Villamisar W, Casales M, Gonzalez-Rodriguez J. G, Martnez-Villafane A, Martinez L, Glossman-Mitnik D. (2006). Computational simulations of the molecular structure and corrosion properties of amidoethyl, aminoethyl and hydroxyethylimidazolines inhibitors,
Corrosion Science, 48, 4053
-
Shein, A. B., Denisova A. V. (2006). Choice of Effective Corrosion Inhibitors for Acid Treatment of Wells, Protection of Metals, 42, 34
-
Smith, L. (1999). Control of corrosion in oil and gas production tubing, Br. Corrosion Journal, 34 (247)
-
Villamizar,W. Casales, M. J. Gonzalez-Rodriguez, G. Martinez, L. (2007). CO2 corrosion inhibition by hydroxyethyl, aminoethyl, and amidoethylimidazolines in wateroil mixtures, Journal of Solid State Electrochemistry, 11, 619