
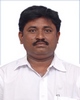
- Open Access
- Authors : Mahesh Gopal , Mohammed Kaso Sado , Asegid Tadesse
- Paper ID : IJERTV10IS060156
- Volume & Issue : Volume 10, Issue 06 (June 2021)
- Published (First Online): 18-06-2021
- ISSN (Online) : 2278-0181
- Publisher Name : IJERT
- License:
This work is licensed under a Creative Commons Attribution 4.0 International License
The Performance Study of Flexible Manufacturing Systems using Hybrid Algorithm Approach
Mahesh Gopal
Assistant Professor, Department of Mechanical Engineering, College of Engineering and Technology,
Wollega University, Post Box No: 395, Nekemte, Ethiopia.
Mohammed Kaso Sado
Lecturer,
Department of Mechanical Engineering, College of Engineering and Technology,
Wollega University,Post Box No: 395, Nekemte, Ethiopia.
Asegid Tadesse
Lecturer,
Department of Mechanical Engineering, College of Engineering and Technology,
Wollega University, Post Box No: 395, Nekemte, Ethiopia.
Abstract The goal of today's production strategy is to maximize the advantages of flexibility. Only when a manufacturing system is completely controlled by FMS technology is this possible. With the Process-Product Matrix in mind, it's feasible to see how an industry might achieve high flexibility via creative technological and organizational initiatives. A flexible cell is now defined as two or more CNC machines, while a flexible manufacturing system is defined as two or more cells. In computer science, system engineering, and many other areas, Petri nets are a strong modeling framework. Petri nets are a graphical description of the dynamic behavior of systems that combines a well-defined mathematical theory with a graphical representation of the dynamic behavior of systems. Because each of its aspects may be implemented in a number of ways and with varying degrees of complexity, the scatter search process is very adaptable. To handle scheduling challenges, the Petri Net idea is introduced and compared to the Scatter Search method. When the results of two case studies (9 machines X 2 jobs) are examined, it is shown that Petri Net outperforms Scatter Search in terms of machine usage.
Keywords Flexible Manufacturing System, Scatter Search approach, Petri Net, Machine utilization
-
INTRODUCTION
A flexible management system (FMS) is an automated production environment in which numerous processes may run at the same time. Different items may be made at the same time, and shared resources are often used to save costs. The system consists of machines that can perform a variety of tasks on a set of components. The machines are unreliable, and the control system's main difficulty is to satisfy production needs while the machines break down and need to be serviced at irregular intervals. Kimemia and Gershwin (1983). The Flexible Manufacturing System of a manufacturing business (FMS). An consistent framework is offered to make decision-making easy throughout the design and planning processes. The suggested framework includes an Analytic Hierarchy Process (AHP), a simulation module, and an accounting system. By applying weight flexibility
limitation and cross efficiency ways to remedy the impediment, this study finally picks the most efficient FMS system Shang and Sueyoshi (1995). Among the operational strategies investigated are policies for loading (assigning processes and tooling to machines) and real-time flow control. A detailed simulation was utilized to analyze the different choices. Stecke and Solberg (1981) results differ from those of standard job shop scheduling studies, illustrating the influence of loading and control strategies on system performance in this flexible manufacturing system. Due to its flexibility, a flexible manufacturing system (FMS) is concerned with the automated fabrication of numerous components in the medium range. It's a completely automated manufacturing system in a nutshell. This article gives a review of previous work in the field of FMS modeling, as well as research and development for a better knowledge of the subject. It is used to examine work done in FMS utilizing a variety of modeling methodologies, including mathematics, artificial intelligence, hierarchical, multi-criteria decision-making, Petri Nets, and simulation Yadav and Jayswal (2018).
A scheduling problem in a flexible manufacturing system (FMS) is made up of two interdependent tasks: loading and sequencing. The loading problem formulations are offered with two purposes in mind :
-
Minimizing system unbalance and the number of late tasks;
-
Decreasing workload imbalance in the system;
Consider constraints such as the number of tool slots with duplications, unique job routing, non-splitting of tasks, and machine capacity. For both aims, heuristic approaches are devised, and the results are compared to Shanker and Tzen's (1985) accurate mixed integer programming solutions. A Flexible Manufacturing System (FMS) is a computer- controlled network of automated material handling equipment and numerically controlled (NC) machine tools capable of simultaneously processing medium-sized quantities of a range of component types. This innovative manufacturing method
combines the efficiency of well-balanced, machine-paced transfer lines with the flexibility of flexible manufacturing systems Browne et al (1984). Flexible manufacturing systems were divided into two kinds by Groover (1980): specialized FMS and random FMS. A dedicated system processes a predetermined set of component types with well-defined production requirements over a certain time frame. The 'random FMS,' on the other hand, produces a greater variety of components in a random order. All FMSs have the same components. The quantity and kind of machine tools may vary. The flexibility of an installation is largely determined by how it is managed. The intended level of flexibility is a significant strategic option in the development and execution of an FMS. Zelenovic (1982) has outlined a framework for making such strategic decisions in this research. The study's main purpose is to figure out how these enablers interact with one another, as well as to identify "driving enablers" (those that have an influence on other enablers) and "dependent enablers." An ISM model was created in order to identify key critical enablers and their management implications in the implementation of FMS. The main purpose of this study is to learn more about how these enablers interact and to identify the "driving enablers" and "dependent enablers." These facilitators were discovered via research, rated using a questionnaire-based survey, and their reciprocal interaction was investigated using an interpretive structural modeling (ISM) methodology. An ISM model was developed by Raj et al. (2008) in order to identify key critical enablers and their management implications in the implementation of FMS. The paper proposes an object-oriented methodology for developing a virtual flexible manufacturing system (FMS) model. The proposed virtual FMS model includes the virtual device model (object model), the transfer handler model (functional model), the state manager model, and the flow controller model (dynamic model). A virtual device model is made up of two parts: the shell and the core. To enhance reusability, the shell component of a virtual device model is designed to adapt to various FMS settings. Stam and Kuula (1991). The paper proposes an object-oriented method for developing a virtual flexible manufacturing system (FMS) model. The four kinds of objects in the proposed virtual FMS paradigm are the virtual device model (object model), the transfer handler model (functional model), the state manager model, and the flow controller model (dynamic model). A virtual device model is divided into two sections: shell and core. To promote reusability, the shell portion of a virtual device model is designed to adapt to vrious FMS installations Park (2005). To deal with such complicated difficulties, new technologies provide more flexibility and automation. These aims targeted at enhancing the production environment have been the main rationales for the deployment of flexible manufacturing systems (FMSs). In this paper, a corporate case study is presented, as well as a contribution to suggest some ways for increasing performance in a flexible manufacturing system. The study is based on existing mathematical models that estimate performance characteristics such as maximum production rate, make span time, and total utilization. This study also aims to provide an improved design for the company's present flexible manufacturing system. After that, Blazewicz et al. (1991) evaluate and analyze a variety of
design and performance parameters for the current and updated FMS. To deal with such complicated difficulties, new technologies provide more flexibility and automation. These aims targeted at enhancing the production environment have been the main rationales for the deployment of flexible manufacturing systems (FMSs). In this paper, a corporate case study is presented, as well as a contribution to suggest some ways for increasing performance in a flexible manufacturing system. The study is based on existing mathematical models that estimate performance characteristics such as maximum production rate, make span time, and total utilization. This study also aims to provide an improved design for the company's present flexible manufacturing system. After that, Singholi et al. (2010) evaluate and analyze a variety of design and performance parameters for the current and updated FMS. In this study, a cuckoo search (CS)-based technique for flexible manufacturing system scheduling optimization is suggested, with the objective of lowering penalty costs owing to production delays and increasing machine utilization time. Because of the discrete nature of the solution, the proposed scheme was used with minor modifications in its Levy flight operator on a standard FMS scheduling problem with 43 jobs and 16 machines taken from the literature to demonstrate the application of a cuckoo search (CS)-based scheme to find the best job Burnwal and Deb (2013).
-
-
METHODOLOGY
The FMS is built for flexibility, and it includes four distinct features, including work arrival, machine process time, scheduling rules, and service priority. Because various tasks and processes need distinct machine sequences, the order in which jobs arrive varies depending on the process. In this paper, the Petri Net is offered as a solution to scheduling difficulties, and its performance is compared to that of Scatter Search in terms of computer usage.
-
Petri net model
A Petri net is a graphical, mathematical modeling tool that may be used to a wide range of systems. It's a potential tool for describing and investigating information processing systems that are concurrent, asynchronous, distributed, parallel, nondeterministic, or stochastic. Petri nets, like flow charts, block diagrams, and networks, may be used as a graphical tool for visual communication. It is possible to create state equations, algebraic equations, and other mathematical models guiding the behavior of systems using this mathematical tool. It's a specific kind of directed graph having an initial state known as the initial marking. Tokens are also utilized in these nets to replicate the system's dynamic and concurrent actions. Both practitioners and theoreticians may benefit from using Petri nets. As a result, they serve as an effective means of communication between practitioners and theoreticians. Theoreticians may teach practitioners how to make their models more systematic, and practitioners may teach theoreticians how to make their models more realistic. To use the modeling method effectively, you must understand both the modeled phenomena and the modeling methodologies. The design, construction, and implementation of coordinating discrete-event control code for an operational
flexible manufacturing system based on Petri nets (PNs) are described in this paper (FMS). It is investigated how PNs may be used to model and control manufacturing processes. As PN synthesis methodologies for industrial control, top-down, bottom-up, and a hybrid strategy combining the two are briefly explored. The hybrid technique and mutual exclusion theory are summarized. This method of synthesis assures that the resulting net has the requisite liveness, roundedness, and reversibility properties. Zhou et al (1992). It is presented how to model and evaluate a flexible manufacturing system (FMS) cell using Petri nets. This cell's entire synthesis technique is presented to show how a Petri net with the needed properties may be created. Top-down refinement, system deconstruction, and modular composition concepts are used throughout the process to achieve the hierarchy and preservation of important system features. The system is stable, deadlock-free, and cyclic because of these traits, which include liveness, roundedness /safety, and reversibility. In addition, Zhou et al. (1993) provide a timed Petri net analysis for cycle time. The net that results from merging the modules with two minimal restrictions is conservative and so constrained. An algorithm that identifies two acceptable conditions finds the structural liveness of the net. The method focuses entirely on the network topology and initial marking, and it seems to be quicker than state enumeration methods such as the reach ability tree method. In this study, the required conditions for life are shown to be related to certain structural objects known as siphons. Jeng (1997) models and examines a small-scale flexible manufacturing system in order to demonstrate the theory's application. Deep reinforcement learning (DRL) is an excellent method for developing a self-optimizing scheduling strategy that takes use of the precise simulation and high- throughput data provided by today's smart plants' sophisticated digital twin technologies. Hu et al. (2020) employ the deep Q-network (DQN), a successful DRL
technique, to solve the dynamic scheduling problem of flexible manufacturing systems (FMSs) with shared resources, route flexibility, and stochastic raw product deliveries. The deep reinforcement learning (DRL) method is an excellent choice for with limited resources and a large number of products, a flexible manufacturing system (FMS) may come to a halt. The authors of this study address the subject of deadlock avoidance and present the concept of deadlock structure using the Petri net (PN) model for FMSs. The conditions that must be satisfied in order to prevent a deadlock are laid forth. The authors use a state feedback limiting technique to minimize system deadlock, which prevents certain enabled transitions from triggering Xing et al (1996). This paper provides a technique for building manufacturing systems that allows for the automated generation of controller logic from a high-level system design specification. The high- level system design specification was created using the SADT approach and the Design/IDEF software package. The interface is based on a collection of conversion rules for transforming an IDEF0 specification into a Petri net. Santarek and Buseif (1998) use a traditional qualitative analysis and Petri net simulation to determine if the production system will function well. In this paper, use Petri nets to present an approach for modeling and analyzing flexible manufacturing systems (FMSs). We build a bottom-up Petri net model (PNM) of the given FMS and investigate crucial qualitative elements of its behavior, such as the existence or absence of deadlocks and buffer overflows, using this technique. Narahari and Viswanadham (1985) technique is based on a theorem that we describe and demonstrate for computing the invariants of the union of a small number of Petri nets when the individual nets' invariants are known. In this paper, we describe a compositional methodology for
Fig.1. Petri Network model
modeling the concurrent execution of working processes in flexible manufacturing systems using a special class of Petri nets known as S/sup 3/PR (FMS). Ezpeleta et al. (1995) define this class as a collection of state machines that share a set of locations that reflect the availability of system resources. To compare and validate the simulation results, the bottleneck technique, which is another well-defined mathematical approach, was utilized. FMS was used as an example, and a Petri net model, AweSim model, and mathematical model were all created. A number of measures have been used to evaluate the system's performance. Simulative techniques have also been created to make studying the complex flexible manufacturing system easy Tamimi et al (2012).
The components are used in Petri Net modeling and the diagram is shown in Fig. 1. Figure 1 duplicates an example of parallel process, Where T1 and T2 represents the parallel activities. When transition T0 fires, it creates marks in both output pieces (P0 and P1) representing a concurrency. When T1 and T2 are enabled for firing, each one may fire independently. The firing of T3 depends on two pre- conditions (P1 and P2), improving that the system only continues if T1 and T2 have been fired. The figure presents a net in which each place has exactly one incoming arc and exactly one outgoing arc. Thus such model represents a sub- class of Petri Network known as marked graphs. Marked graphs allow representation of concurrency.
-
scatter search
Scatter search (SS), unlike other evolutionary processes, allows for a comprehensive examination of the search space via intensification and diversification. It also includes a unifying notion for connecting solutions, as well as adaptive memory to avoid duplicate solutions from being produced or integrated at various stages of the problem. In this work, several meta-heuristic methodologies are used to handle three different sizes of scheduling challenges that were gathered from the literature by Saravanan and Haq (2008). This research looks into group scheduling for manufacturing cells, in which components may travel across cells. The order of components within manufacturing cells is determined by intra- cell scheduling, while the sequence of cells is determined by inter-cell scheduling. We provide an unique mathematical model for a multi-criteria group scheduling problem in a cellular manufacturing system (CMS). The main objective is to lower the make span, intracellular mobility, timeliness, and sequence-dependent setup costs all at the same time. Due to the issue's intricacy, we developed a meta-heuristic strategy based on scatter search to address it (SS). This strategy has been put to the test, and the results demonstrate that our recommended SS is effective and efficient at producing great solutions, especially for medium and large situations. Moghaddam et al (2010). In this study, the dispatching rules are combined with PNs, as well as PNs and a hybrid Improved Scatter Search approach for FMS performance assessment. Several conventional hybrid approaches were used to compare and validate simulation results. Finally, for a better comparison, the test problems were chosen from the review paper, and when compared to dispatching rules and Petri net
with dispatching rule techniques, PN hybrids with Improved Scatter Search algorithm provide better results in terms of machine utilization, AGV idle time, and makespan when considering with and without breakdown condition Chinnusamy et al (2020). The cellular manufacturing system, which has been recognized as an effective method of increasing industrial efficiency, is a significant application of group technology (GT). As a consequence, Bajestani et al. (2009)provide a multi-objective dynamic cell creation problem in which the total cell load variation and the sum of incidental charges (machine cost, inter-cell material handling cost, and machine relocation cost) must both be minimized. Today's production systems operate in dynamic environments, where unanticipated real-time events may cause a change in the previously viable schedule, rendering it unworkable after it has been sent to the shop floor. In this research, the Scatter- Search (SS) meta-heuristic technique is utilized to improve the scheduling of flexible manufacturing systems with the objective of reducing the make span with machine failure. It enables a comprehensive study of the search space via intensification and diversification, as well as a unifying notion for connecting solutions, and it employs adaptive memory to avoid developing or integrating duplicate solutions at various stages of the problem. Krishnan et al. (2013) compare this technology to static scheduling in a comparative study. Scatter search (SS) strategy for optimizing make span for this problem in this paper. In flow shop settings, SS hasn't been employed extensively. In the recommended strategy, we use advanced techniques such as a reference set comprised of whole and partial responses, restarts, and local search. According to a rigorous computational campaign that comprised 10 existing algorithms and statistical analyses, the recommended scatter search algorithm surpasses existing algorithms by a considerable margin. Furthermore, Naderi and Ruiz (2014) have improved all 720 well-known solutions to this problem. These objectives are weighted according to their respective importance in this research, and then a new mathematical model is proposed. A scatter search (SS) approach is provided to solve this issue by selecting the cheapest process plan for each component while simultaneously generating the part family and machine grouping. In terms of performance, the recommended SS is compared to the Lingo 8.0 software. A variety of test tasks are conducted to determine that the ability is great. The SS delivers promising results, especially for large-scale issues, according to the computational findings of Moghaddam et al (2012). The single row facility layout problem (SRFLP) is the task of organizing facilities in a line with defined lengths in order to minimize the weighted sum of the distances between all pairs of facilities. Researchers have focused on heuristics to solve big instances of the problem since it is NP-hard. In this study, we propose a scatter search approach for resolving large SRFLP scenarios. Our computer experiments show that the scatter search strategy is the best alternative for dealing with large SRFLP situations in a short period of time Ghosh and Kothari (2014).
Steps in Scatter Search Algorithm
-
Diversification Generation Method
-
Improvement method.
-
Reference set update method
-
Subset generation method
-
Combination method
-
There are case studies predicted to show the required result and the type of jobs arrival and machine sequence are shown in the Table 1.
-
-
CASE STUDY
The researcher Udhayakumar and Kumanan (2012), Noorul et al (2003), Krishnan et al (2009) developed a U shaped manufacturing model as shown in figure 2 of 9 machines, 2 product, load / unload stations are 2 and
TABLE I. CONFIGURATION OF FMS
Layout type |
U Loop |
No. of Machines |
09 |
No. of Parts |
02 |
Load/Unload stations |
02 |
No. of AGV |
01 |
Fig. 2 Layout of FMS
TABLE II. OPERATION SEQUENCE FOR CASE STUDY
Part Type |
Operation Sequence |
||||||||
1 |
2 |
3 |
4 |
5 |
6 |
7 |
8 |
9 |
|
P1 |
M2 |
M5 |
M3 |
M1 |
M8 |
M4 |
M6 |
M9 |
M7 |
P2 |
M6 |
M9 |
M5 |
M3 |
M1 |
M4 |
M7 |
M8 |
M2 |
TABLE III. OPERATION TIME FOR CASE STUDY
Part Type |
Operation Sequence |
||||||||
M1 |
M2 |
M3 |
M4 |
M5 |
M6 |
M7 |
M8 |
M9 |
|
P1 |
62 |
9 |
89 |
87 |
10 |
66 |
95 |
49 |
82 |
P2 |
30 |
95 |
58 |
61 |
58 |
60 |
17 |
8 |
5 |
Automated Guided Vehicle (AGV) used is 1 for the manufacturing process and are taken to a consideration and analysis. The configuration details are shown in Table 1.The operation sequence numbers of two parts are stated in Table 2. The operation time of the manufacturing model is shown in Table 3 for the individual machine.
-
RESULTS AND DISCUSSION
In order to test the effectiveness and performance of the proposed Petri Net and the Scatter Search and the analyses on
the case study of 9 machines 2 products. The result is given for the corresponding case study and their required parameter. The Petri Net shows the optimum sequence and the machine utilization for individual or whole system. From the above case studies, the performance result shows that the Petri Net is best when compared to Scatter Search algorithm. The Table 4 shows the results for Petri Net and Scatter Search in terms of machine utilization and their corresponding graphs as shown in the Fig. 3.
TABLE IV. PETRI NET AND SCATTER SEARCH RESULT FOR THE CASE STUDY
Details
M1
M2
M3
M4
M5
M6
M7
M8
M9
PETRI-NET
78
69
94
61
93
97
47
49
83
SCATTER SEARCH
51
56
86
68
63
81
41
39
41
Fig. 3 Performance of Petri Net and Scatter Search for the case study-II
-
CONCLUSION
This paper includes Petri Net and Scatter Search algorithm. From the above case study, the Petri Net shows better machine utilization than Scatter Search result and the performance of FMS was studied. In future work, the Petri Net approaches have a number of specific implications for the goal of designing improved optimization procedures. The result for different case study was taken and evaluating the Petri Net with different scheduling algorithms and give a comparison between them.
-
REFERENCES