
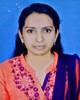
- Open Access
- Authors : Anu K , Kaikeyee A K
- Paper ID : IJERTV10IS060208
- Volume & Issue : Volume 10, Issue 06 (June 2021)
- Published (First Online): 22-06-2021
- ISSN (Online) : 2278-0181
- Publisher Name : IJERT
- License:
This work is licensed under a Creative Commons Attribution 4.0 International License
Optimization of Prestressed Precast Concrete Roof Truss by Varying Its Geometric Parameters
Anu K
-
ech Structural Engineering Dept. of Civil Engineering
Younus College of Engineering and Technology Kollam, Kerala, India
Smt. Kaikeyee A K
Assistant Professor, Dept. of Civil Engineering Younus College of Engineering and Technology Kollam, India
Abstract In this paper, pre-stressed precast concrete roof truss is proposed as an alternative to conventional roof trusses. As the concrete is weak in resisting tensile stresses, design of roof truss using reinforced concrete is very difficult. In order to resist the high axial tension in bottom chord, the concrete truss needs to be pre-stressed. Here, the modelling of different configurations of prestressed precast concrete roof trusses is done using ETABS 2018 software by varying its geometric parameters such as shapes, slope, span and spacing of the truss and analysis and optimization is carried out to find the most effective and best prestressed precast concrete roof truss configurations suited to various conditions.
Keywords ETABS 2018, Optimization, Precast Concrete, Prestressing, Roof truss, Wind analysis
-
INTRODUCTION
In In Structural Engineering, the title truss portrays a triangular design. A roof truss is basically a structural framework designed with single or numerous triangular units at a regular interval that comprises of straight slender members with their closes joined via nodes. The external loads conveyed by roof covering are carried out either as reactions to the walls or to the supporting stanchions. Basically, these loads are applied at the joints of the truss. In some instances, it becomes vitals to apply loads at intermediate points. Correspondingly, the members are resulted to bending action besides the direct forces.
Fig.1: A typical roof truss components
Steel roof trusses are most widely used type of roof trusses but it can melt in high temperatures and can cause necking of the steel and also steel can cause corrosion when it is exposed to marine regions. In such case, prestressed precast concrete trusses will be used as an effective alternative to it. e.Construct, an American based company has offered a state
of-art concrete truss girder that has been built and designed for a cement storage facility in Sharjah, UAE.
-
Objectives
The objectives are as follows,
-To find out the effectiveness of pre-stressed precast concrete roof truss and also to find its best truss configurations for different conditions
-To design the structure against dead load, live load and wind load.
-To get optimum truss configuration of pre-stressed precast roof trusses.
-To validate and check the possibilities of implementation of general computer program ETABS software for roof truss analysis and design.
-
-
METHODOLOGY
In this study, to perform the analysis in roof truss structure, datas like shapes, dimensions, material properties, softwares which are commonly used for analysis were collected from the literature survey and review. Models of prestressed precast concrete trusses are then designed, loads are assigned and analysed and optimization is done. In this study, ETABS 2018 software has been adopted to model, optimize and analyse the prestressed precast concrete roof trusses. ETABS stands for Extended Three dimensional Analysis of Building System which is a design oriented software program specially built for the analysis of building structures. Results were evaluated and conclusions were made.
-
MODELLING
Roof truss of size 12 x 24m is selected for modelling with height of the column 5m in five selected shapes (A type, Fan truss, Fink truss, Pratt truss and Howe truss). An asbestos sheet M20 grade having a thickness of 6mm is provided for roof covering. Later on modelling was done by varying slope (1 in 3, 1 in 4 and 1 in 5), spacing (4m, 6m and 8m) and Span (6m, 12m and 18m).
Here prestressed tendons are placed at the bottom chord of the truss. Material properties and details are;
-
Concrete M30 grade
-
Longitudinal bars HYSD 415 grade
-
Tendons Fe250 grade (Tendon jacking stress 1120.05 N/mm2)
-
Tendon diameter 15mm
Table I. Structural members and its size
MEMBER
SIZE
Columns
250 x 250 mm
Truss Members
90 x 90 mm
Purlins
65 x 65 mm
Fig 2: A type truss
Fig. 3: Fan truss
Fig. 4: Fink truss
Fig. 5: Howe truss
Fig. 6: Pratt truss
-
-
ASSIGNED LOADS AND BOUNDARY CONDITIONS
The following loads are assigned for the analysis of the modelled roof trusses
-
Dead load
It is a constant load that acts on the structure due to the self-weight of the members, the supported structure, along with enduring attachments or other accessories. The study with dead loads is considered in the building design and simultaneously in the materials unit weight. These loads are calculated as specified in IS 875-1987 (part I).
-
Live load
In the case of roof truss, live load may be the load subjected by dust load, distributed, impact load and vibration, other factors such as wind, seismic, snow along with temperature variations, differential settlement, creep, shrinkage, etc. The study suggests assuming live loads in the design of buildings, for the purpose of structural safety of buildings. Live loads are calculated as per IS 875-1987 (part II).
-
Wind load
Wind motion is relative to the earth surface. The primary source of wind is sketched upon earths rotation and changes in terrestrial radiation. That further effects convection either upwards or downwards. Due to suction effect of the wind
blowing over the roof, wind loads are usually uplifted perpendicular. Wind load is a very important factor in the design of roof truss. In this study wind parameters are calculates as per IS 875- (part III) 2015.
TABLE II. Wind parameters
Basic wind speed (Vb)
39 m/s (Trivandrum)
Probability factor or risk coefficient (k1)
1.0 (for 50 years)
Terrain, height and structure size factor (k2)
0.98
(for terrain category 2)
Topography factor
(k3)
1.0 (for plain land)
Wind pressure Co-efficient
0.8(Windward) and 0.5(Leeward)
-
RESULTS AND DISCUSSIONS
This section includes the figures which shows the variation of each parameters in each of the models.
-
-
Load combinations
The corresponding load combinations between dead load, live load and wind loads are auto generated in ETABS software. As per the selected design code IS 875- 1987 (part v), the load combinations are;
-
1.5 (DL+LL)
-
1.2 (DL+LL+WL±X)
-
1.2 (DL+LL+WL±Y)
-
1.5 (DL+WL±X)
-
1.5 (DL+WL±Y) f) 0.9 DL+1.5WL±X
-
The bottom of the column is fixed and all other joints in the roof truss are assigned as fixed.
V. ANALYSIS
Structural analysis is used to determine the effects of loads on physical structure and their components. The present study incldes two different analysis namely wind analysis and buckling analysis.
Fig. 7: Graph showing the maximum displacement values for all the truss models
Fig. 8: Graph showing the maximum bending moment values for all the truss models
Fig. 9: Graph showing the maximum torsion for all the truss models
Fig. 10: Graph showing the maximum column load for all the truss models
Fig. 11: Graph showing the buckling load factor for all the truss models
ISSN: 2278-0181
Vol. 10 Issue 06, June-2021
Fig. 12: Graph showing base shear values for all the truss models
The analysis results shows that a direct proportional relation is exhibited by the displacement against slope, spacing and span. When the slope is varied from 1 in 3 to 1 in 5, displacement decreases by 56%, when spacing increases, displacement also increases by 78 % and as span increases, the maximum displacement also increases by 45%. Collating all truss types, maximum displacement is observed for models with slope 1 in 3, 6m spacing and span 18m. In the corresponding specification of maximum displacement, Slope and Spacing possessed minimum to moderate range of values mentioned in the study. With this deduction, it is clearly elucidated that Span is the most influential parameter, as the maximum value of Span adopted in the study induced extreme status of displacement for all truss types. The parametric specification of slope 1 in 3, spacing 4m and span 12m seemed more economical in having lesser displacement and Fan & Pratt trusses are observed as reasonable.
The variations in Slope doesnt induce any impact on bending moment. The maximum bending moment is experienced for slope 1 in 3, spacing 6m and span 6m, whereas the minimum bending moment is experienced by model having slope 1 in 3 spacing 4m and span 12m. When spacing varied from 4m to 8m, bending moment increases to 72%, revealing the ideology, larger the spacing, more will be the bending. Moderate span length served as economical for the bending moment to be minimum (for plan aspect ratio 1:2). Fink truss possess comparatively lesser Bending moment Truss is subjected to torsion irrespective of the span length, rather say very negligible level of variation is induced in torsion when span length is changed. Even the maximum and minimum torsion are experienced in the same slope that is, 1 in 3, the modifications in slope is associated with notable changes in torsion, and low slope always favored economy in terms of torsion. Torsion suffered a reduction pattern on decreasing the spacing, disclosing Spacing as the most interpreting parameter for torsion. Overall, almost all types of trusses shown satisfactory result in minimum torsion except
for Fink truss
The parametric specification corresponding to the boundary values of Buckling Load Factor (BLF) shows the variation of only one parameter that is span length, thereby indicating its dominant influence on BLF. Maximum value is
attained for a span length of 6m and for minimum, it is 18m, disclosing the inverse proportionality of BLF against Span length (more the Span length, lesser will be the BLF). An increment of 26% of BLF had been observed on decreasing the span length. While, the other two parameters remained as such for the boundary values, but Spacing generally established a quite noteworthy reduction in BLF on its enhancement. Fink type truss again observed as economical among the types of truss.
The parametric specification once again divulged the modification value of span length in causing the major variation of base shear. This is the parameter of concrete truss where extraordinary deviation in magnitude had been observed. Slope modifications induced somewhat a fair variation in base shear and a minute variation is executed with the spacing modifications. Another specialty of this parameter is that, this is the only one parameter where all types of trusses had shown similar magnitudes in maximum value. The maximum bending moment is experienced by parametric specification of slope 1 in 3, spacing 6mm and span 6m and minimum bending moment is experienced with models having slope 1 in 3, spacing 6m and span 18m.
While considering the total column load, same pattern of observations and deductions as seemed for the parameter base shear had repeated.
-
CONCLUSION
-
-
Designing using steel has been the sole practice when it comes to long spanned roofs. The ease of handling and erection, geometric flexibility, and light-weight of the steel structural components are all advantages of steel structures. But now a days the rate of structural steel is really going high (especially in India). Now-a-days cold formed steel trusses, concrete infilled steel trusses are evolving but concrete has not been introduced into the field of roof trusses as concrete is weak in resisting tensile stresses, in order to resist the high axial tension in bottom chord, the concrete truss needs to be prestressed From the study, following conclusions was made;
-
Prestressed precast concrete roof truss can be used as an alternative to steel roof truss, it is applicable to structures which are exposed to high temperatures and also for trusses in marine areas.
ISSN: 2278-0181
Vol. 10 Issue 06, June-2021
-
ETABS software is simple and convenient for the modeling and analysis of roof trusses. Optimization of roof trusses in this softwares appears to be very fast and easy.
REFERENCES
-
Mohd Azaz, Abhay Walke and Mohd. Samir Ansari, Comparative study of trusses using staad pro and etabs software, International Journal of Creative Research Thoughts, Volume 5, Issue 35, 2017, pp.70-78.
-
Sirisha Nidadavolu and Dr.D.Venkateswarlu, Design of Pre- Stressed Precast Concrete Truss and a Comparative Study with Steel Truss, International Journal for Modern Trends in Science and Technology, Volume 03, Issue 11, 2017, pp.107-118
-
W. T. Carroll, F. W. Beaufait, and R. H. Bryan, Prestressed concrete trusses, ACI Journal, Volume 75, Issue 8, 1978, pp. 367 373.
-
P. H. Shah and H. R. May (1977). Precast vierendeel trusses provide unique structural facade for parking structure Precast/Prestressed Concrete Institute, Journal, vol. 22, no. 4, pp. 2439.
-
SP 38 (S &T):1987-Handbook of typified designs of structures with steel roof trusses (with or without cranes) Based on IS Codes.
-
IS: 1893-2002: Criteria for earthquake resistant design of structures
-
IS: 875 (Part1)-1987: Code of Practice for Design Loads
-
IS: 875 (Part 3)-2015: Design loads (other than earthquake) for buildings and structures code of practice.