
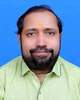
- Open Access
- Authors : Narayanan N I , Aravind Sarma V
- Paper ID : IJERTV10IS060348
- Volume & Issue : Volume 10, Issue 06 (June 2021)
- Published (First Online): 30-06-2021
- ISSN (Online) : 2278-0181
- Publisher Name : IJERT
- License:
This work is licensed under a Creative Commons Attribution 4.0 International License
Vibration Analysis of FG Plates with Circular Cutouts
Narayanan N I1, Aravind Sarma V2
1Assistant Professor, Department of civil Engineering, Govt. College of Engineering Kannur, Kannur, Kerala,
2Structural Engineer, Adoor, Pathanamthitta, Kerala,
Abstract – Functionally graded materials have received a lot of interest in recent days by their diversified and potential applications in aerospace and other industries. They have high specific mechanical properties and high temperature capabilities which makes them special over all the exiting advanced materials. The present work investigated free vibration analysis of functionally graded square plate. The material properties vary continuously from bottom surface to top surface. The effective material properties of functionally graded materials for the plate structures are assumed to be temperature independent and graded in the plate thickness direction according to a power law distribution of the volume fractions of the constituents. The present model is developed using finite element software ABAQUS. 4 noded shell element is used throughout the analysis which is a linear element. Parametric studies have been done for various power law indices by varying the diameter of circular cut out for different boundary conditions.
Keywords – FGM, Plate, ABAQUS, Vibration
-
INTRODUCTION
Functionally Graded Material belongs to a class of advanced material characterized by variation in properties with respect to the dimension. The overall properties of Functionally Graded Materials are exceptional and diverse from any of the individual material that forms it. Typically, Functionally Graded Materials are made from a mixture of metals and ceramics and are characterized in a way that composition of each one and the volume fraction of materials are changed gradually. By gradually changing the volume fraction of constituent materials, their material properties show a smooth and continuous change from one surface to another, and as a result eliminating interface problems and reducing thermal stress concentrations[1].
Functionally Graded Material (FGM) is combination of a ceramic and a metal. A material in which its structure and composition both varies gradually over volume in order to get certain specific properties of the material hence can perform certain functions [2]. The properties of material depend on the spatial position in the structure of material. The effect of inter- laminar stress developed at the laminated composite interfaces due to sudden change of material properties reduced by continuous grading of material properties. Generally microstructural heterogeneity or non-uniformity is introduced in functionally graded material. The main purpose is to increase fracture toughness, increase in strength because ceramics only are brittle in nature. Brittleness is a great disadvantage for any structural application. These are manufactured by combining both metals and ceramics for use in high temperature applications. Material properties are varies smoothly and continuously in one or many directions so FGMs are inhomogeneous. FGM serves as a thermal
barrier capable of withstanding 2000K surface temperature [3]. Fabrication of FGM can be done by different processing such as layer processing, melt processing, particulate processing etc. [4]. FGM has the ability to control shear deformation, corrosion, wear, buckling etc. and also to remove stress concentrations. This can be used safely at high temperature also as furnace liners and thermal shielding element in microelectronics and thermal protection systems for spacecraft, hypersonic and supersonic planes and in combustion chamber also.
B. Sidda Redddy et al. have studied the Free Vibration Behaviour of Functionally Graded Plates Using Higher- Order Shear Deformation Theory. They have developed analytical formulations and solutions for the free vibration analysis of functionally graded plates (FGPs) using higher order shear deformation theory (HSDT). The equations of equilibrium and boundary conditions were derived using the principle of virtual work. Solutions were obtained for FGPs using Naviers technique. M. N. Gulshan Taj et al. have studied free vibration of functionally graded material (FGM) skew plates under thermal environment. It was interpreted that the volume fraction index and skew angle plays significant role in predicting the vibration of FGM skew plate subjected to thermal load. Jyoti Vimal et al. carried out The free vibration analysis of functionally graded skew plates using the finite element method. The first-order shear deformation plate theory is used to consider the transverse shear effect and rotary inertia. The properties of functionally graded skew plates are assumed to vary through the thickness according to a power law. It is found that when the length to thickness ratio of functionally graded skew plates is increases beyond 25, the variation in the frequency parameter is very negligible and also found that a volume fraction exponent that ranges between 0 and 5 has a significant influence on the frequency. Mohammad Talha et al. conducted Study of the free vibration and static analysis of square and rectangular functionally graded plates, which is based on the higher order shear deformation theory with a special modification in the transverse displacement in conjunction with finite element models. They concluded that the frequency parameter increases with the increase in plates aspect ratio (a/b) and smaller side to thickness (a/h) ratio and the frequency parameter decreases with the increases of volume fraction index, n. J. N. Reddy studied theoretical formulation and FEM model based on TSDT for FGM plate. The formulation accounted for thermo mechanical effects combining change with time and geometric nonlinearity. In this higher order theory, transverse shear stress was expressed as a quadratic function along the depth. Hence this theory requires no shear correction factor. The plate was considered as homogenous
and material composition was varied along the thickness. The Young's modulus was assumed to vary as per rule of mixture in terms of the volume fractions of the material constituents.
Although FGMs are highly heterogeneous, it will be very useful to idealize them as continua with their mechanical properties changing smoothly with respect to the spatial coordinates. The homogenization schemes are necessary to simplify their complicated heterogeneous microstructures in order to analyze FGMS in an efficient manner [8]. It is worth noting that, the distribution of material in FG structures may be designed to various spatial specifications. A typical FGM represents a particulate composite with a prescribed distribution of volume fractions of constituent phases. The material properties are generally assumed to follow gradation through the thickness in a continuous manner. Two types of variations/gradations are popular in the literature which covers most of the existing analytical models.
The exponential law: This particular idealization for FGM modeling is very common in the fracture mechanics studies [9]. For a structure made of FGM with uniform thickness h, the typical material properties P(z) at any point located at a distance z from the reference surface is given by;
(1)
al. (2001) was used. In the present investigation, a 4 noded three dimensional linear shell element (S4R) have been used to model the functionally graded plate in ABAQUS.
Fig 2 Schematic diagram of plate
The material properties given by He et al. (2001) are used to develop the finite element model of FGM plate that ismade of the combined aluminum oxide and Ti-6A1-4V materials, and its properties are graded through the thickness direction according to a volume fraction power law distribution (Fig 3). Table 1 shows the material properties of the plate
Table 1 Material Properties
1 2 z
h
1 P
Material
E(N/m2)
(kg/m3)
Aluminum oxide
349.55 x 109
3750
0.26
Ti-6A1-4V
122.56 x 109
4429
0.2884
Material
E(N/m2)
(kg/m3)
Aluminum oxide
349.55 x 109
3750
0.26
Ti-6A1-4V
122.56 x 109
4429
0.2884
P(z) Pt e , where,
ln t
The power law: The p2owerPblaw is more common in the stress as well as frequency analysis of FGM [9] and given by;
t b
t b
P(z) (P P ) z
h
-
n
-
Pb
(2)
Here P(z) denotes a typical material property, viz., Youngs modulus of elasticity (E), shear modulus of elasticity (G), Poissons ratio (t), material density (q), etc. of the structures made of FGM. h is the total thickness of structure. Pt and Pb are the material properties at the top-most (z =
+h/2) and bottom-most (z = -h/2) surfaces. n in the exponential model, and n in the power model are the material grading indexes respectively. Working range of these material grading indexes depend upon the design requirements.
Since the material constituents of the FG material vary over the thickness, the numerical model is made into divisions consisting of a number of layers as shown in Figure 1. Each layer is assumed to be isotropic. The power law is employed to find the material properties in each layer. The laminated structure represents the stepwise variation in properties, and the gradation can be approximated by using a high number of layers.
Fig. 1 FG Material section and its equivalent laminated composite
section
-
-
METHODOLOGY
For validating the material model in finite element package ABAQUS, data available for the functionally graded plate test specimen 0.4m x 0.4m x 0.005m prescribed in He et
Fig 3 Variation of E with respect to Z/h for different n values
Free vibration analysis was initially carried out by using vibration procedure available in ABAQUS package to extract different modes as well as frequencies. Table 2 shows the fundamental natural frequencies of the plate with boundary condition CFFF for various power law indices.
Table 2 Power law exponent and Fundamental Frequencies
n
Fundamental
Frequency(Hz)
0
25.369
0.2
30.773
0.5
32.289
1
33.9
5
38.475
15
44.162
100
45.69
1000
46.1
The experimental result and finite element analysis result were listed as in Table 3. The FE analysis result is found to
2
508.0
622.9
648.2
680.6
777.0
879.8
926.8
927.7
3
508.2
623.1
648.6
680.7
777.2
880.5
927.6
927.8
4
759.6
927.4
966.2
1013.7
1153.5
1314.0
1372.7
1378.6
5
917.0
1121.5
1167.7
1224.5
1395.1
1586.5
1660.6
1666.3
6
1076.0
1295.8
1361.8
1430.2
1607.9
1908.4
1885.3
1941.4
7
1168.1
1425.5
1486.5
1559.5
1776.3
2028.8
2112.2
2122.7
8
1169.3
1426.0
1488.5
1560.6
1778.0
2031.7
2113.8
2123.2
9
1465.2
1785.7
1865.5
1957.7
2226.8
2562.3
2644.5
2665.6
10
1466.1
1786.4
1866.5
1958.6
2229.9
2566.2
2648.8
2666.0
2
508.0
622.9
648.2
680.6
777.0
879.8
926.8
927.7
3
508.2
623.1
648.6
680.7
777.2
880.5
927.6
927.8
4
759.6
927.4
966.2
1013.7
1153.5
1314.0
1372.7
1378.6
5
917.0
1121.5
1167.7
1224.5
1395.1
1586.5
1660.6
1666.3
6
1076.0
1295.8
1361.8
1430.2
1607.9
1908.4
1885.3
1941.4
7
1168.1
1425.5
1486.5
1559.5
1776.3
2028.8
2112.2
2122.7
8
1169.3
1426.0
1488.5
1560.6
1778.0
2031.7
2113.8
2123.2
9
1465.2
1785.7
1865.5
1957.7
2226.8
2562.3
2644.5
2665.6
10
1466.1
1786.4
1866.5
1958.6
2229.9
2566.2
2648.8
2666.0
be almost matching with experimental result. The result comparison concludes the validation of the material model in FE analysis package ABAQUS.
Table 3 Comparison of present result with existing result
n
Fundamental Frequency(Hz)
FEM
He et al
(2001)
0
25.369
25.58
0.2
30.773
29.87
0.5
32.289
32.84
1
33.9
35.33
5
38.475
40.97
15
44.162
43.97
100
td>
45.69
46.12
1000
46.1
46.55
-
RESULTS AND DISCUSSIONS
The objective of this numerical experimentation is to understand the relationship between different variables sensitive to the dynamic behavior of functionally graded plates. Parameters of interest are the power law index n, boundary conditions and diameter of the circular holes or cut-outs. One parameter is varied, keeping the others constant to understand the nature of variations in dynamic responses, indicated by the changes in natural frequencies.
Table 4 to 6 shows the variation of natural frequencies with respect to the power law exponent n for the boundary conditions CFFF, CCCC and FFFF.
Table 4 Frequencies (Hz) of CFFF Plate
Mode No
Natural Frequencies (Hz)
n=0
n=0.2
n=0.5
n=1
n=5
n=15
n=100
n=1000
1
25.0
30.4
31.7
33.4
38.0
43.4
45.0
45.5
2
60.0
72.8
76.1
80.7
91.9
105.5
109.3
110.9
3
151.5
184.1
192.3
202.9
230.5
265.2
274.4
277.6
4
192.9
235.1
245.5
258.2
293.4
337.6
349.3
352.9
5
224.0
272.6
284.8
300.5
342.0
393.1
406.9
411.6
6
398.0
490.3
512.0
533.7
607.5
700.1
724.1
728.1
7
434.4
523.2
546.8
581.0
660.0
757.9
784.5
795.4
8
457.0
551.5
576.5
612.2
696.1
798.9
827.3
838.9
9
508.6
617.7
645.0
679.8
773.3
887.4
918.1
928.6
10
653.4
792.0
827.2
875.6
997.5
1142.7
1183.6
1199.8
Table 5 Frequencies (Hz) of CCCC Plate
Mode No
Natural Frequencies (Hz)
n=0
n=0.2
n=0.5
n=1
n=5
n=15
n=100
n=1000
1
275.6
333.5
350.1
366.9
414.8
487.4
489.1
499.3
Table 6 Frequencies (Hz) of FFFF Plate
Mode No
Natural Frequencies (Hz)
n=0
n=0.2
n=0.5
n=1
n=5
n=15
n=100
n=1000
1
94.2
115.1
120.9
126.9
145.5
168.0
173.9
175.0
2
135.4
165.3
173.7
182.2
209.1
241.5
250.1
251.3
3
165.3
201.0
210.5
220.6
251.6
289.6
299.6
301.2
4
252.3
308.5
322.8
338.8
386.8
445.0
460.6
464.6
5
252.4
308.5
322.8
338.8
386.8
445.0
460.7
464.6
6
431.0
524.0
550.2
576.9
660.0
760.3
787.0
790.6
7
431.1
524.2
550.3
577.0
660.0
760.5
787.1
790.8
8
471.9
579.1
602.4
632.8
718.2
823.3
851.9
863.0
9
507.1
620.7
648.3
680.6
775.6
891.6
923.0
931.7
10
549.9
669.0
699.7
733.7
836.0
960.9
994.3
1000.7
Variation of the natural frequencies of FG plate with the power law exponent n under different boundary conditions as well as variation of frequencies with respect to cutout diameter for different boundary condition was investigated. It was found that the natural frequencies increase with increase in the volume fraction power law exponent n for all the three types of boundary conditions considered here.
The initial ten natural frequencies of the FGM plate as a function of the power law exponent n are depicted for various boundary conditions. The dimensions of the FGM plate are the same. Three sets of boundary conditions were considered.
The effect of constituent volume fraction VT = (z/h + 0.5)n on the natural frequencies is studied by varying the volume fraction of Ti-6Al-4V. This is carried out by varying the value of the power law exponent n. For example, n = 0 implies the FGM plate consists only of Ti-6Al-4V. As n increases, the volume fraction of Ti 6Al-4V is decreased. When n tends to , the FGM plate almost totally consists of aluminum oxide. Tables show that the natural frequencies
increase with increases in the volume fraction power law exponent n for all the six types of boundary conditions considered here.
In the following sets, the variation of natural frequencies of the FG plate with respect to the changes in hole diameter are investigated by keeping the power law index constant (n= 1).
Fig 4 Plate with holes of 0.05m, 0.1m and 0.2m diameter
Fig 5 Frequency (Hz) variation with cutout diameter of FG plate with CFFF boundary condition
Fig 6 Frequency (Hz) variation with cutout diameter of FG plate with CCCC boundary condition
Fig 7 Frequency (Hz) variation with cutout diameter of FG plate with FFFF boundary condition
It was also found that the variations of frequencies with respect to cutout diameter largely depend on boundary conditions. It was seen that the variations of frequencies were found to be mostly monotonically decreasing for all the cases but some modes show opposite behavior as the
boundary condition changes.
-
CONCLUSIONS
Investigations have been carried out for functionally graded plates with cutouts to determine the effects of diameter of the hole n the changes in frequencies of various modes. The material composition of the FGM structure is assumed to vary according to a simple power-law distribution through the thickness. The developed computer model is validated with the published results for natural frequencies of FGM plates.
It was found that for the functionally graded plate with circular cutout, the natural frequencies increase with increase in the power law exponent n for all the three types of boundary conditions considered. It was also found that the variations of frequencies with respect to cutout diameter largely depend on boundary conditions also. It was seen that the variations of frequencies were decreasing for almost all the cases but some modes show opposite behavior as the boundary condition changes.
REFERENCES
-
Jha, D.K., Kant, T. and Singh, R.K. (2013). A critical review of recent research on functionally graded plates. Composite Structructures; 96:83349.
-
Koizumi, M. (1993). The concept of FGM. Ceramic Transactions: Functionally Gradient Materials;34:310.
-
Udupa, G., Rao, S. and Gangadharan, K. (2014). Functionally graded composite materials: An overview, Procedia Materials Science 5. ( 2014 ) 1291 1299.
-
Gasik, M.M. (2010) Functionally graded materials: Bulk processing techniques. International Journal of Material and Production Technology;39(12):209.
-
Kiebeck, B., Neubrand, A. and Riedel, H. (2003). Processing techniques for functionally graded materials. Materials Science and Engineering. A;362:81-105.
-
Schatt, W. and Wieters, K.P. (1997) Powder Metallurgy Processing and Materials, EPMA, Shrewsburry, UK, p. 492.
-
Kumar, V. and Dutta, D. (1997) Solid Model Creation for Materially Graded Objects, Solid Freeform Fabrication Proceedings, 1113, Austin TX, USA, pp. 613620.
-
Mian, A.M. and Spencer, A.J.M. (1998) Exact solutions for functionally graded and laminated elastic materials. Journal of the Mechchanics and Physics of Solids;46(12):228395.
-
Eliasi, R. and Berlin, Y. (2006) Modelling of Functionally graded materials in dynamic analyses. Composites Part B 33(2002) 7-15.
-
Redddy, B. S., Kumar, J. S., Reddy, E. C. and Reddy, K. V. K. (2014) Free Vibration Behaviour of Functionally Graded Plates Using Higher-Order Shear Deformation Theory. Journal of Applied Science and Engineering, Vol. 17, No. 3, pp. 231_241.
-
Gulshan, M. N. A., Chakrabarti, A. and Prakash. V.(2014) Vibration Characteristics of Functionally Graded Material Skew Plate in Thermal Environment. International Journal of Mechanical, Aerospace, Industrial, Mechatronic and Manufacturing Engineering Vol:8, No:1.
-
Vimal. J., Srivastava, R. K., Bhatt, A. D. and Sharma, A. K. (2014) Free vibration analysis of moderately thick functionally graded skew plates. Engineering Solid Mechanics 2, 229-238.
-
Talha, M. and Singh, B. N. (2010) Static response and free vibration analysis of FGM plates using higher order shear deformation theory. Applied Mathematical Modelling 34. 39914011.
-
He, X. Q., Ng, T. Y., Sivashanker, S. and Liew, K. M. (2001) Active control of FGM plates with integrated piezoelectric sensors and actuators, Int. J. Solids Struct. 38, 16411655.
-
Reddy, J. N. (2000) Analysis of functionally graded plates,"International Journal for Numerical Methods in Engineering , 47: 663-684.