
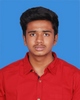
- Open Access
- Authors : Adhithya S , Bhuvanesh G , A Naren
- Paper ID : IJERTV10IS070090
- Volume & Issue : Volume 10, Issue 07 (July 2021)
- Published (First Online): 13-07-2021
- ISSN (Online) : 2278-0181
- Publisher Name : IJERT
- License:
This work is licensed under a Creative Commons Attribution 4.0 International License
Autonomous Handrail Sanitizing Bot
Adhithya. S |
Bhuvanesh. G |
Naren. A |
Department of Electronics & |
Department of Electronics & |
Department of Mechanical |
Communication Engineering |
Communication Engineering |
Engineering |
PSG College of Technology |
PSG College of Technology |
PSG College of Technology |
Coimbatore, Tamil Nadu. |
Coimbatore, Tamil Nadu. |
Coimbatore, Tamil Nadu. |
Abstract The Corona Virus has had an irreversible impact on both the health and economy of various countries, prolonged lockdowns are not an option as it has crippled people who are not economically sound. The public spread has to be curtailed, especially in places of major gathering such as theatres, markets, and places of worship. All of these places have handrails which can prove to be a major carrier of virus. Thus, the idea of a Handrail Sanitizing bot that can sanitize the railings in public places in fixed intervals of time is proposed here. This idea is materialized by the use of electronic components aided by a compact mechanical structure. The idea is flexible, cost efficient and can be used in handrails of any shape. It is implemented with the use of Arduino Uno microcontroller and other peripheral components such as Ultra Sonic sensors, Motor driver, etc. The mechanical structure is of less weight and complexity. This bot can reduce the spread of the virus, as handrails are a common contact area that can induce the spread of the virus to a considerable extent. A prototype that is cost efficient and straight-forward is proposed. The content focuses on its structure, building, and also the underlying software, methodology and hardware.
Keywords Automation, Corona, COVID, Railings, Sanitation
-
INTRODUCTION
WHO declared COVID-19 as a pandemic on 11 March 2020 due to its large-scale spread across the globe [1]. India has become the second worst affected country in terms of the number of COVID-19 cases after the USA. The Corona Virus is having a stronghold over the world and is expected to end its spree no time soon. Frequent lockdowns are not an option as the world has already taken a major economic hit. Places of public gatherings such as Malls, Theatres, Places of worship are expected to be opened once again when the impact of the virus begins to dip down. All of these places have handrails that the public use. Public places are considered to be spots of major spread, and handrails are structures millions of people use daily and can also contribute majorly to the spread of the virus as they are not sanitized frequently and can house the virus for elongated periods of time. Also, if the handrails are made of steel/metal, there is a much greater chance of stay and spread of the virus. So, it is necessary to sanitize the railings frequently. Some handrails are of large lengths and it is inefficient to sanitize it using manpower. So, this paper provides a plausible solution to the existing problem by automating the sanitation process, by the use of a bot, which primarily is controlled using Arduino Uno Microcontroller, its peripheral components and is adjustable to any kind of rail, making it flexible and uses a Li-Ion 3300 mAh battery for power.
-
LITERATURE SURVEY
During the first wave of the Corona virus, the various phases of lockdown were in practice for about 4 months, after which complete relaxation was brought into place. Consequently, the number of cases also began to surge up. During the last phase of lockdown in India, which is one of the worst hit countries by COVID-19, 94949 cases were recorded. After the complete relaxation of lockdown, 118955 cases were recorded [2].
In addition to this, a third wave is likely to hit several countries by October, and this is likely to remain a global public health threat for at least another year [3]. Thus, it is important to control the spread even after the relaxation of the lockdowns imposed in several countries throughout as well as during the third wave.
It was also found that SARS-CoV-2 was more stable on plastic and stainless steel than on copper and cardboard, and viable virus was detected up to 72 hours after application to these surfaces. The longest viability of both viruses was on stainless steel and plastic; the estimated median half-life of SARS-CoV-2 was approximately 5.6 hours on stainless steel and 6.8 hours on plastic [4]. It is also to be noted that most public handrails are made of the same material.
Much advancements have been made in the domain of floor sanitation. In [5], the mint cleaning robot which is an automatic cleaning robot that sweeps and mops hardsurface floors using dusting and mopping clothes was developed. It investigates the products social impact with respect to the attitude of the customers towards a systematic floor cleaner and how such a robot influences their lifestyle. Systematic cleaning was an important feature, and modifications to the environment to support the navigation of robot. The robot employs a systematic cleaning strategy that maps the environment using a GPS-like indoor localization. [6] uses a similar approach for the cleaning of the floors. It uses a vacuum to suck the dust off of the ground. It uses an ultrasonic sensor to detect the obstacles on its path.
[7] incorporates both manual and automatic modes of operation in the task of floor cleaning. This robot is controlled by AT89S52 microcontroller. This robot detects the obstacles in its path by the IR sensor. It uses dual relay circuitry, one for pumping the water and the another for driving the motors. In the area of handrail sanitation, Svaras, an India based UV Technological company, has launched UV based sterilizers for the sanitation of escalator rails. The cost of product rangesaround 1.5- 2 lakhs in Indian rupees owing to the cost of UV technology used.
-
DESIGN
-
Outline of the model
The proposed model comprises of an ATmega328 microcontroller, two ultrasonic sensors to detect obstacles, a L293D motor driver in order to drive the motors, wheels for locomotion, a housing in which the sanitizing liquid is placed, a pump, a scrub/sponge and housing on which the above materials are placed.
The model is straight-forward, cost effective and can be used on any type of hand-railings irrespective of its size or shape. The model is mainly designed to sanitize the part of the railings where people are prone to touch repeatedly and sanitizing them at regular intervals of time.
-
Mechanical Structure
The components are housed on an acrylic board of length 16 cm and width 15 cm. On the top, the board houses a battery holder, a switch, the microcontroller, the sanitizer, its enclosure and two Ultra Sonic sensors at the ends. The container having the sanitizer consists of a pump that pumps the liquid. On one end of the sanitizer container, a tube is attached which goes through the acrylic board to its downside. The bot consists of four wheels for its mobility.
The four wheels are attached to the motor drivers which in turn is attached to spring-like clamper such that the bot can be adjusted to handrails of any dimensions. When the dimension varies, the tension on the spring also varies, thus the device tightly clamps itself to the handrail. The sponge which is used to clean the rail is attached to the bottom of the board. The tube that is conncted to the sanitizer container is attached to the centre of the sponge through which the sanitizer is sprayed on the rails and the cleaning is done by the sponge. The structure is depicted in Figure 1, Figure 2, Figure 3 and Figure 4 and the parts are depicted in Table I.
Fig. 1. CAD sketch of Structure of the Bot
Fig. 2. Structure of the Bot (Top View)
Fig. 3. Structure of the Bot (Front View)
Fig. 4. Structure of the Bot (Side View)
TABLE I COMPONENTS OF THE BOT
Key
1
Container
2
Acrylic board
3
Wheel
4
Spring
5
Ultrasonic sensor
6
Battery holder
7
Switch
8
Pipe
9
Sponge/scrub
10
Arduino Board0
11
Motor
-
-
IMPLEMENTATION
-
Hardware used
-
ATmega328/Arduino:
ATmega328 is the ATMEL Microcontroller on which Arduino board is based. The Atmel 8-bit AVR RISC-based microcontroller combines 32 KB In-System Programmable Flash (ISP) memory with read-while-write capabilities, 1 KB EEPROM, 2 KB SRAM, 23 general purpose I/O lines, programmable watchdog timer with internal oscillator, and five software selectable power saving modes. The device operates between 1.8-5.5volts. ATmega328 is commonly used in many prototypes and autonomous systems where a straight- forward, low-powered, low-cost microcontroller is needed.
Fig. 5. Arduino Uno
-
L293D Motor Driver:
It has four H-Bridges and two L293D Motor driver chips. L293D is rated at 0.65A per bridge with thermal shutdown protection, Motor Voltages from 4.5VDC to 16VDC. It can drive up to 4 bi-directional DC motors with individual 8-bit speed selection. It can also drive up to 2 stepper motors. It has separate Logic and Motor power connections Terminal block connectors for motors and power.
Fig. 6. L293D Motor Driver
-
Ultra-Sonic Sensor:
At its core, the HC-SR04 Ultrasonic distance sensor consists of two ultrasonic transducers. The one acts as a transmitter which converts electrical signal into 40 kHz ultrasonic sound pulses. The receiver listens for the transmitted pulses. If it receives, then it produces an output pulse whose width can be used to determine the distance the pulse travelled. It has a ranging accuracy of 3mm.
Fig. 7. Ultrasonic Sensor
-
-
Implementation of the prototype
The prototype uses an Arduino microcontroller (Nano or Uno). It uses an LM293D motor driver module that can drive four motors and thus the four wheels used. A 3-6 V Mini Submersible Water pump is used to pump the sanitizing liquid, whose Operating Current ranges from 130 mA – 180 mA. Two Ultrasonic Sensors are utilized to detect the start and stop points. An acrylic board is used to mount the components owing to their rigidity and strength. Wheels of large diameters are used to hold the device together.
The battery requirement plays a vital part. A 3300mAh/3.7 V rechargeable Li-Ion battery renders a power of 3300*3.7=12,210 mWh, The Arduino runs on 5V, and L293D absorbs 300 mA of current on an average and 600 mA at maximum, the L293D module has two such drivers and thus 600mA. The pump absorbs about 150 mA on average and it is used only at intermittent intervals of time (once every 4 seconds), the ultrasonic sensors on a whole draw current of about 100 mA. Thus, the total current drawn can be totalled as 600+150+100 +~ 50 mA = 900 mA. Then the total hours for which the device will run on a charge is 12,210 mWh/ (5*900)
~ 3 hours. For a single charge, the device shall run for approximately 3 hours in theory.
Fig. 8. Hardware Layout
Fig. 9. Prototype of the bot on a Handrail
Fig. 10. Structure of the bot
Fig. 11. Front View of the Handrail Sanitizing bot
Fig. 12. Top View of the bot
The structure is of the prototype depicted in Figure 9, Figure 10, Figure 11 and Figure 12. The L293D Motor Driver is mounted on the ATmega328.The pins A1 and A2 are connected to trigger and echo of one Ultra Sonic Sensor whereas A3 and A4 are connected to trigger and echo pins of the other Ultra Sonic Sensor. The pin A5 is connected to the Motor Pump. The power and ground pins powering the board is connected to the battery holder.
The prototype of the bot replicates the mechanical structure depicted before. The challenge in materializing the bot is the balance, which mainly depends on the torque of the motor in use. The diameter and the weight of the wheels should also be in such a manner that the bot is in balance and makes sure that the bot does not rest on the rail on effect of gravity. The size of the tube must be in accordance with the length of the rail. Tubes of large size on a small rail will not be efficient and might result in excess usage of the sanitizing liquid. Similarly, the tube must be chosen in accordance to the width of the rail as rails with more width require the liquid to be spread over a larger area.
-
Software
The software used here to code the logic is Arduino IDE. The library that is of main use is AFMotor.h. The Arduino Integrated Development Environment – or Arduino Software (IDE) connects to the Arduino hardware to upload programs
and communicate with them. AFMotor.h comprises of all the commands that can be used to control and manipulate the various controls of the motor driver.
-
Methodology
When the power supply is switched on, the bot starts its motion in the forward direction. During this movement, the sanitizing liquid is pumped at regular intervals of time and is scrubbed with a sponge. This process is continued until any obstacle is detected.
This detection is done by the Ultra Sonic sensor. When any obstacle is detected, the Ultra Sonic sensor sends its signal to the motor driver and hence the movement stops. When the obstacle vanishes in a small interval of time, the movement in the particular direction is continued. This is where a time limit has to be set to distinguish this from the long-term obstacle that is encountered at the end of the rail. For example, if 600 seconds is set as t, then if the obstacle is present for 10 minutes, then it will identify that it has reached one end of the rail. If not, itll be considered as a temporary obstacle. When the obstacle is present for more than the specified time limit, then it is identified as the end of the rail and now the bot starts moving in the opposite direction.
The same process is repeated in the opposite direction also when it reaches back to the other end of the rail (the end from which it started). This detection is done by the Ultra Sonic Sensor present on the other side of the setup. This process repeats after a specified time limit again. Thus, repeated pumping and cleaning of the rail takes place at regular intervals.
Here, the time interval between pumping of the liquid, the time interval to detect the presence of the permanent obstacle can vary from one use to another.
Fig. 13. Flowchart depicting the methodology
-
LIMITATIONS
This can be implemented using any microcontroller such as Raspberry Pi, Node MCU, etc. This can be used on any railing irrespective of the dimensions since it uses a spring that can clamp itself tight to any railing. The setup and the logic can be altered concerning the specific purpose. It has a limitation that the structure will have to be modified depending on the weight housed on the board(increased amount of sanitizer). If the rails are of longer length, then to sanitize the entire railing, larger volumes of sanitizer will be required, thus wheels of varying diameter will be required to house he structure. The proposed structure works perfectly for straight rails and requires alterations in structure to suit handrails having curved and twisted structures. The battery life of 3300mAh/3.7 V is moderate and, should be improved for railings of larger lengths and, when large quantities of sanitizing liquid is required to be pumped which in turn increases the motor load.
-
FUTURE SCOPE
Further improvements can be done to decrease the weight of the bot, to make the bot suitable for rails of all sizes and for sanitizer housings of all volumes. Further development is required in the structuring of the bot so that it can be made to traverse on curved and twisted rails. Works and developments in these areas can serve as a vital tool to decrease the spread of the virus in crowded areas and provide an efficient solution to the problem of public spread. The bot must be made more rigid, as to withstand rough rails, which are not smooth as the ones in steel.
-
CONCLUSION
-
The bot is straight-forward in its construction and working. The usage of this bot in apartments, offices and places of public gathering such as places of worship, restaurants would reduce the risk of the spread of the virus to a greater extent. The bot is also cost effective thus making it affordable for people of all businesses and classes. Thus, the usage of this will play a commendable part in bringing the world back to its feet once the lockdown restrictions are lifted and when the people are up and moving, which is likely to happen very soon.
REFERENCES
-
WHO Director-General's opening remarks at the media briefing on COVID-19 – World Health Organization. 11 March 2020.
-
Balram Rai, Anandi Shukla, Laxmi Kant Dwivedi, Dynamics of COVID-19 in India: A review of different phases of lockdown, Popul.
Med. 2020;2(July):21
-
Covid-19 roundup: Third wave likely to hit India by October, The Times of India(June 18,2021).
-
Neeltje van Doremalen, Trenton Bushmaker, Dylan H. Morris, Aerosol and Surface Stability of SARS-CoV-2 as Compared with SARS-CoV- 1, The New England Journal of Medicine, March 17, 2020.
-
Jens-Steffen Gutmann, Kristen Culp, Mario E. Munich and Paolo Pirjanian, The Social Impact of a Systematic Floor Cleaner, IEEE international workshop on advance robotics an its social impacts,
Technische University Munchen, Germany May 21-23,2012
-
Manya Jain, Pankaj Singh Rawat, Assist. Prof. Jyoti Morbale, Automatic Floor Cleaner, International Research Journal of Engineering and Technology (IRJET), Volume: 04 Issue: 04 | Apr -2017
-
A. Vimala, S. Manikandan, T. S.Aravinth, S. Birundha Devi, S. Sathiya Gopika, Microcontroller Based Floor Cleaning Robot, International Journal of Innovative Technology and Exploring Engineering, Volume- 8 Issue-4S, February 2019.