
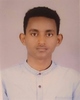
- Open Access
- Authors : Kebrebeal Addisu Belay , Dereje Engida Woldemichael
- Paper ID : IJERTV10IS070095
- Volume & Issue : Volume 10, Issue 07 (July 2021)
- Published (First Online): 16-07-2021
- ISSN (Online) : 2278-0181
- Publisher Name : IJERT
- License:
This work is licensed under a Creative Commons Attribution 4.0 International License
Modeling of Tangential Teff Threshing and Separation System
Kebrebeal Addisu Belay1, Dereje Engida Woldemichael1 1College of Electrical and Mechanical Engineering Addis Ababa Science and Technology University
Addis Ababa, Ethiopia
Abstract – Teff is a small size cereal that has its origin in Ethiopia. It is the major cereal grown on about 3million hectares annually which equates to 27% of the land. Seventy percent of the workforce in the country relies on small-scale agriculture, among this Teff accounts for about a quarter of the total cereal production and it is alone grown by 6.2 million farmers. This makes it the major staple food grain for over 50 million Ethiopian people. In terms of crop production, it stands third (after maize and wheat) by 18.57% coverage of the crop production which equals to 29.9 million quintals. But due to the traditional methods employed to harvest, the country did not get the most out of it. From the ploughing stage to the threshing process, harvesting is done using conventional techniques. Threshing is done using animals (livestock) walking on it or beating the plant on the ground. This process is primitive, inefficient, unhygienic and time consuming. There is 12% to 25% of Teff postharvest losses using this techniques. Due to this one of the biggest challenges facing the agricultural sector in Ethiopia right now is meeting the growing demand for Teff to feed its increasing population. To challenge the primitive way of Teff harvesting, modern technologies need to be employed and that is why this paper focuses on the design and validation of a tangential Teff threshing and separation system. By keeping the size variances similar, the design of Teff tangential threshing and separation system is validated in comparison with a published research. The threshing rate parameter, the threshing efficiency and the separation efficiency are the major threshing performance indices that are selected for validation. The validation was done at a threshing drum speed of 27m/s, threshing drum diameter of 0.48m, threshing drum length of 0.83m, wet basis Teff moisture content of 12%, Teff MOG bulk density of 35kg/m3 and MOG throughput (feed rate) of 0.13kg/s. The result showed, 5.4% error in the threshing rate parameter and 1.23% error in the threshing efficiency while 1.17% error in the separation efficiency at a drum speed of 1200rpm and feed rate of 275kg/s.
KeywordsTeff, Teff threshing machine, Tangential Threshing
-
INTRODUCTION
Teff (Eragrostis tef) is an ancient tropical cereal that has its center of origin and diversity in the northern Ethiopian highlands from where it is believed to have been domesticated [1]. In Ethiopia, seventy percent of the workforce relies on small-scale agriculture, among this Teff accounts for about a quarter of the total cereal production and it is alone grown by 6.2 million farmers [2], [3]. This makes it the major staple food grain for over 50 million Ethiopian people. It is indigenous to the country and is a part of the culture, tradition, and food security of the people [4], [5].
Teff is a minor cereal crop worldwide though it is spread in South Africa, Kenya, USA, Brazil, Canada, Australia and small
areas in Japan [6], [7]. Whereas in Ethiopia, it is a major food grain, mainly used to make Injera, a traditional fermented pancake. In fact it is the foremost crop that it is grown on about 3million hectares annually [8], which equates to 27% of the land. It is Ethiopias most significant crop not only by area planted but also by the value of production and it is the second largest cash crop (after coffee), generating almost 500 million USD income per year for local farmers [9]. In terms of crop production, it stands third (after maize and wheat) by 18.57% coverage of the crop production which equals to 29.9 million quintals [5]. Its Production in Ethiopia experienced an average growth of 11.28% per year between 2004 and 2011 and shows no sign of slowing [9]. The price of Teff tripled in 5 years to 855.8 birr per quintal in 2010 and it tripled again in 9 years to 2400 birr per quintal in 2018 and now it ranges from 4000 5000 birr.
Teff is possibly the smallest cereal grain with an average length of 1.17mm and average width of 0.61mm. Thousand grain weighs around 0.14g [10]. It is made of 77.6% carbohydrate, 12.9% protein and the rest constitutes minerals, fat, fiber and ash [11]. Other than the fact that very little knowledge is known about its nutritional composition and health benefits, the technological limitations in processing Teff is the main reason for its consumption not to wide spread globally as it is used in its center of origin. However, Kaleab baye [1] noted that, over the past decade, the recognition that Teff is gluten-free has spurred global research interest. Health benefits like it reduces iron deficiency, celiac disease and it prevents and control diabetes are the other reasons that prompted the researchers. Among the various varieties of Teff grain, Quncho is regarded as the variety with greater yield per unit of field and easily adaptable which helps in sustaining food security [12], [13].
With this amount of fascinating facts and figures, Teff farming is still done using traditional methods. For this widely used cereal, from the ploughing stage to the threshing process, harvesting is done using conventional methods which dated back when Teff was first introduced to the country. For sickling, extensive man power is used and threshing is done using animals (livestock) walking on it or beating the plant on the ground.
Traditional method of threshing are very slow, gives low output, the cost of operation is high and there is a huge loss of grains because of rodents, birds, insects, wind, and untimely rain and fire hazards [3], [5], [8], [9]. [14]Threshing operation and its subsequent loss followed is among points requiring proper attention and that generally accounts about 6% cereal crops loss in Ethiopia. According to the African Postharvest Losses Information System, postharvest losses for Teff were estimated
to be 12.3% which is really a big number. More than 12 quintal out of 100 is a loss which can feed a mid-sized family for 2-3 years. Other literatures studied that the threshing and other subsequent losses ranges from 12% to 25% [15][18]. This kind of fact is devastating for a country trying to reach food security. One way to tackle this kind of issue is to employ technology based agriculture one of which is using threshing systems.
Modern Teff harvesting technologies will help to transform the arduous, unsanitary and inefficient harvesting process in to a new level. To get the most out of Teff, an increase in productivity is required apart from the household consumption. This way it is possible to feed the emerging grain processing industries resulted from the change in lifestyle and the recently burgeoning global Teff market which will boost the economy directly or indirectly. From achieving food security to substituting imported foods, it has a lot to contribute to the growing economy of the country.
Other than the economical aspect, using modern technologies like Teff Threshing systems has its own social impacts which can be pronged in three. Creating more prosperous communities, more education opportunities, and healthier grain production. Firstly, the Teff Thresher boosts Teff production, increasing agricultural prosperity and self- sustainability and reducing poverty. The product will also spur the formation of local micro businesses that sell the machines or provide services for other farmers. Secondly, it will prevent children from being emoved from school during harvest periods. And thirdly, it will produce a safer, more hygienic grain, improving the health of a majority of the population in Ethiopia
-
MATERIALS AND METHODS
A Teff thresher is a machine that will thresh or detach grains out of the straw mat and sends the threshed Teff grain to the cleaning system for further cleaning and separation while the rest of MOG is flowed to the exit. So the main purpose of the machine is to detach, separate and clean Teff grains from the straw mat. In this way we can understand that the machine has different systems to form a complete threshing machine. The feeding system, the threshing system, the separation system and the cleaning system are all the major systems that comprises a Teff threshing machine. This paper focuses on the design and validation of a Teff threshing and separation system.
-
Design Considerations
The threshing machine is based on a tangential flow threshing system. It incorporates a tangential feeding system, a tangential threshing unit, a tangential separation unit, an extra straw walker separation system and a grain conveying system. First, Teff material is fed to the feeding system manually. Then, a threshing unit consist of active elements like rasp bar mounted on a threshing drum are rotated to drug Teff materials tangentially towards the threshing space. In the threshing space due to the friction and impact of active elements such as rasp bar and concave bar shown in figure 2.1, Teff grain is detached from the straw mat and flows to the cleaning unit through the concave openings.
Figure 2.1 Tangential threshing system
The concave will be designed in such a way to facilitate a tangential and smooth flow of materials towards the subsequent unit. While the portion of detached grains flows to the cleaning shoe, the rest of material move towards the separation unit for separation of grains and straw mat.
-
Working Principle
First an operator feeds Teff straw and MOG to the hopper leading the feed material to flow to the threshing unit. The threshing system contains a threshing drum, a rasp bar and a concave. When the feed material flows through the threshing space (the space between the lower tip of the rasp bar on the threshing drum and the upper tip of the concave) at a specific feeding velocity, the rotating threshing drum with mounted rasp bar detaches Teff grains. This is due to the friction and impact of the rasp bar and concave grate that wraps the drum underneath at a specific angle. The threshing space or concave clearance has a relatively wider space at the inlet of the material than at the exit. This increases the threshing action and results somehow a compressed straw mat to flow to the next stage. The detached grain will then pass through the concave opening while unseparated grain and the rest of the MOG flows to the separation unit.
The separation unit has two separation systems, a separator and a straw walker. In the separator, there is a rotating separation drum with mounted bucket like structures across the edges and a separation concave. The separation drum separates detached Teff grains that are segregated in the straw mat (MOG) which came from the threshing unit. Since the separator and concave has a similar structure and arrangement with the threshing unit, it serves as additional threshing mechanism for the unthreshed crop material that flows through this unit. After the Teff grains are separated and detached, it passes through the separation concave openings while the MOG (straw mat) is delivered to the last separation stage, the straw walkers. The straw walker serves as another separation unit where the last bit of Teff grain gets separated limiting the probability of detached and unseparated grains to exit the machine as a discharge.
The straw walker unit contains three independent straw walkers or shakers which are positioned along the length of the threshing drum length. Each straw walker is constructed from a sheet metal sidewalls of saw tooth profile (to push the straw to the rear side) and steps of screens. The walkers or shakers are mounted on a crank axle on the front and end sides at different angle. The screens on the shakers are inclined at a certain angle (10o 22o) to form a series of cascades. When the crank rotates, each straw walker reciprocates at different phase in a way when
one moves up the other moves down. This motion intensifies the separation action while forcing the MOG to the rear side. The separated Teff grain will pass through the screens to the straw walker sieve and then to the cleaning unit while the MOG flows to the rear and discharged at the exit.
The cleaning unit is the last stage of operation before Teff grains are conveyed to the storage. It comprises an oscillating grain pan, two stage of cleaning sieve mounted one above the other, a straw walker sieve and a radial flow fan that blows current of air from the bottom to the upward and rear direction of the sieves. The function of the cleaning unit is to separate free Teff grains from grain chaff and straw mixture, to forward cleaned grains to the auger and discharging MOG fragments to the ground due to the action of the fan and the reciprocating motion of the cleaning unit crank.
Teff grains, chaffs, small straws and MOG fragments separated from the threshing unit, the separator and the straw walker are delivered to the oscillating grain pan and the straw walker sieve through the threshing concave, separator concave and straw walker screens respectively. Then, as the result of the winnowing action of the grain pan, the straw walker sieve and the simultaneous effect of the fan, primary grain cleaning occurs since there is a space for Teff materials before reaching the top sieve from the grain pan and straw walker sieve.
Secondary grain cleaning happens due to the combination of the oscillatory motion of the top sieve and gravitational force while air is blown from the bottom. Finally Teff grain flows to the bottom sieve through the openings of the top sieve for further and deep cleaning. Again from the force generated from the
vibratory motion of the bottom sieve and gravity, the final cleaning occurs and the cleaned grain flows to an inclined sheet surface where it is conveyed to the feeding auger which feeds to the storage while the rest of the material is discharged to the exit.
-
mathimatical modeling of Teff threshing performance indices
For the modeling of the systems, the following parameters were considered.
-
Teff material to be processed is homogeneous and uniformly distributed
-
Threshing unit is feed with constant feed rate and amount
-
Effective Teff threshing starts at the entrance of the threshing zone
-
Material to be threshed moves continuously in the threshing space
-
Mass of the material is continuously distributed in the threshing space
-
Threshing performance evaluates the working conditions of the threshing system using various indices like MOG feed rate, percentage of threshed, unthreshed, separated and unseparated grain, grain damage, cleaning efficiency, specific power consumption and output capacity. Since this paper focuses on threshing and separation system of a Teff thresher, the threshing and separation performance indices are discussed below. To analyze Teff threshing performance indices, consider the physical properties of Teff grain and chaff in the following table.
Table 2-1: Physical properties of Teff grain [19]
Moisture content (Wet basis)
Thousand grain mass (TGM)
(gram)
Grain density (Kg/m3)
Average diameter
(mm)
Terminal velocity
(m/s)
Drag coefficient
(Cd)
11.94%
0.292
1361.8
<>0.74 3.24
0.76
15.1%
0.320
1358.2
0.76
–
–
21.1%
0.361
1314.9
0.86
–
–
24.2%
0.392
1283.7
0.87
–
–
27.1%
0.421
1252.9
0.88
4.04
0.66
Table 2-2: Physical properties of Teff chaff [19]
Straw length (mm)
Node free
Middle node
End node
Mass (gram)
Diameter (mm)
Mass (gram)
Diameter (mm)
Mass (gram)
Diameter (mm)
6
0.029
1.630
0.032
1.760
0.032
1.810
8
0.034
1.870
0.060
1.712
0.061
1.720
10
0.058
1.670
0.064
1.880
0.063
1.830
-
MOG Feed Rate
The threshing space between the threshing drum and the threshing concave as shown in figure 2.1 has a capacity of consuming more Teff straws based on the designed intake volume of the machine.
MOG feed rate or throughput is calculated considering Teff straw and grain weight, feeding velocity, concave clearance and threshing drum width and speed. Teff has different varieties across the country and their straw or the plant height ranges between 450mm to 900mm. The Teff threshing machine should be designed to process the highest straw height.
From table 3.6, the maximum value of the straw diameter in all cases is 1.88mm. This means the threshing drum along the
length of the threshing drum can house specified number of straws if the straw lay one next to another in a series. But this should consider the space needed so that no clogging occurs. Therefore the mass of MOG throughput QM is expressed as;
QM = Ws + Wg (2.1)
QM = (Ts x Sw) + (Ts x Tg x Gw) (2.2)
QM = (0.64Ts ) + (0.00032Ts.Tg ) ( 2.3)
Where, Ws – Total weight of straw Wg – Total weight of grain Ts – Total number of straws
Sw – Individual weight of highest straw (gram) Tg – Total number of grain in each straw
Gw – Individual grain weight
35xVc.e
( Qp + 15.1 Vc
Now the material throughput or MOG feed rate QP can be
= KT e Q 12
Qpx15.1
V ) (2.7)
determined based on the above equations. The MOG throughput is the product of the total mass of the MOG throughput QM and
Therefore, the probability of threshed grain GT(x) as a function of concave length x becomes
the number of rounds of total straw N processed per unit time.
35xVc.e
( Qp + 15.1 Vc
)
)
Therefore, QP becomes
(KT
GT(x) = 1- e
e Q 12
Qpx15.1
V )x
(2.8)
QP = QM x N (2.4)
Where, N number of rounds of total straw processed per unit time (s-1)
)
)
-
Percentage of threshed and separated Teff grain in the threshing drum
At the beginning of the inlet concave clearance where x = 0, the probability of threshed grain GT(x = 0) is 0 since there is no material in the threshing space to be threshed. However, at the end of the concave length (exit), the probability of threshed grain GT(x = L ) becomes,
The detachment of grains or generally a threshing system is
35xVc.e
( Qp + 15.1 Vc
described in terms of probabilistic laws as an exponentially
(KT
GT(x = L) = 1- e
e Q 12
Qpx15.1
V ).L
(2.9)
distribution function. The probability density function pdf of an exponential distribution function determines the probability of
The percentage of unthreshed grain GR(x) becomes,
( + )
( + )
Qp 15.1 Vc
the grain to detach from the ear/straw considering variables like the concave length and threshing rate parameter [20], [21]. For
GR(x) = ex = e
(KT 35xVc.e e Q 12 V )x
Qpx15.1
(2.10)
the threshing and separation unit analysis discussed in the following paragraphs, refer to Figure 2.1 to identify the terms used.
The pdf expresses the probability of grains to be detached or
At the end of the threshing space where x = L, the percentage of unthreshed grain GR(x) becomes the threshing loss TL in the threshing unit.
( + )
( + )
Qp 15.1 Vc
the percentage of threshed grain GT(x) along the concave length
TL = GR(x=L) = e
(KT 35xVc.e e Q 12 V )x
Qpx15.1
(2.11)
[22], [23]. It is mathematically expressed as,GT(x) = 1- ex ( 2.5)
Where, x threshing space/current position of straw inside the
Based on Miu petres studies [22], the fraction of separable and segregated grain GS(x), which is the amount of grain that are threshed but segregated in the straw mat that needs separation in the threshing space is given as:
Concave length (m)
threshing rate parameter (m-1)
GS(x) =
(ex ex ) (2.12)
To determine the value of GT(x), the corresponding value of the threshing rate parameter is required. According to Miu petre [22], is a function of MOG bulk density, threshing drum
Where, is separating rate parameter (m-1) which describes the rate of grain separation along the threshing and separation space. The value of is determined as
speed, exit concave clearance, MOG throughput, Wet basis MOG moisture content, optimum working MOG throughput,
= K
VcUQp
S (Qp+ U )
(2.13)
Wet basis maximum MOG moisture content, threshing drum peripheral speed, Optimum working threshing drum peripheral speed. The functions of threshing rate parameter is mathematically expressed as,
e Q Um
Where, KS coefficient that depends on crop type
Um Wet basis minimum MOG moisture content (%) Um represents the wet basis minimum moisture content that
Vce
( Qp + U
Vc )
= KT e Q UM V
QpU
(2.6)
results minimum grain damage at the MOG throughput of QP. Therefore, the separating rate parameter becomes,
Where, KT Coefficient that depends on crop type
MOG bulk density (kg/m3)
= K
VcUQp
(2.14)
S Qp 15.1
Vc Threshing drum peripheral speed (m/s)
e
e
35
( Q + 12 )
e Exit concave clearance (m)
QP MOG throughput (kg/s)
Thus, the fraction of separable and segregated grain GS(x) can now be determined as,
-
Wet basis MOG moisture content (%)
VcUQp
KS
( + )
( + )
VcUQp
( + )
( + )
Q Optimum working MOG throughput (kg/s)
Qp
15.1
KS
Qp 15.1 x
UM Wet basis max MOG moisture content (%)
GS(x) =
35 e Q 12 (e
( + )
( + )
VcUQp
35 e Q 12
ex ) (2.15)
-
optimum threshing drum peripheral speed (m/s)
KS
Q 15.1
Wet basis maximum MOG moisture content UM represents the wet basis moisture content that results minimum grain damage at the MOG throughput QP. Optimum working threshing drum speed V corresponds to the maximum threshing drum peripheral speed that result higher grain separation. In this case V will be same as Vc since it is the only selected working drum speed and let UM be 12% since it is the ideal working moisture content for minimum grain damage and using data studied by Geta Kidanemariam [24], the MOG bulk density of Teff straw is 35 kg/m3 at a moisture content of 15.1%.
Therefore, the threshing rate parameter becomes
35 e Q 12
At the end of the threshing space where x becomes the thresher concave length L, the fraction of separable and segregated grain GS(x) becomes the thresher (threshing drum) separation loss SL.
SL = GS(x=L) (2.16)
The percentage of grain separation TS at the end of the threshing space becomes
TS = 1 – GS(x=L) (2.17)
-
-
Percentage of threshed and separated Teff grain in the separation drum
As mentioned earlier, Teff materials enters the separation system after processed in the threshing drum. In the separator, unthreshed and threshed but segregated Teff grains are separated. The probability of grains to be detached in the separator GTS(Xs) along the separation space (separator concave length) XS is given as
GTS(LS) = 1- eXs (2.18)
At the end of the separation space where XS becomes the separator concave length LS, the probability of grains to be detached GTS(LS) becomes
GTS(Xs=LS) = 1- eLs (2.19)
At the end of the separation space, the percentage of unthreshed grain becomes the separator threshing loss STL.
STL = 1 GTS(LS) = eLs (2.20)
The fraction of separable and segregated grain GSS(XS), which is the amount of grain that are threshed but not separated instead segregated in the straw mat that needs separation in the straw walker is
-
Number of rasp bar is 6
-
Separating drum diameter is 400mm
-
Separating drum speed is 400rpm
-
Separating drum length is 700mm
-
Threshing drum concave wrap angle is 120o
-
Threshing drum concave length is 490mm
-
Threshing drum concave inlet and exit clearance are 20mm and 10mm respectively
-
Separating drum concave inlet and exit clearance are 22mm and 12mm respectively
-
Separating drum concave wrap angle is 100o
-
Separating drum concave length is 490mm
-
Threshing and separation drum concave rod diameter is 3mm
-
Threshing and separation drum concave bar thickness is 5mm
-
Threshing and separation drum concave bar depth is 50mm
GSS(XS) =
(eXs eXs ) (2.21)
-
Threshing and separation drum concave length is
At the end of the separation space, the fraction of separable and segregated grain GSS(XS) becomes the separation loss SSL.
700mm
-
-
There are three number of shakers (individual straw
SSL = GSS(XS=LS) =
(eLs eLs ) (2.22)
walker) of width 235mm each and length 1500mm
-
Straw walker crank shaft rotation is 200rpm
-
So the percentage of separated grain at the end of the separating space SS is
SS = 1 – GSS(LS) (2.23)
-
-
Percentage of separated Teff grain in the straw walker The straw walker is the last unit of separation. In this unit the last bit of unseparated Teff grain is separated before it is discharged in the rear. According to Miu petre [22], the fraction of remaining grains GW(y) as the function of the current position y along the length of the straw walker (LW) that still exist with
the straw mat is expressed as:
GW(y) = (Vt+Vs) {1 – 1 [ (1 ) (1 )] } (2.24)
Where, Vt Total threshing loss
Vs Total separation loss
a The specific rate of grain segregation (m-1) b The specific rate of grain separation through
the screen (m-1)
The values of a and b for most of the crops as published by Miu petre [25] are determined to be a = 1.94.54 and b = 0.9
2.26 m-1 for variety of crops.
At the end of the straw walker length when y becomes the length of the straw walker LW, the fraction of remaining grains GW(y) becomes the straw walker separation loss WL.
WL = (Vt+Vs){1 – 1 [ (1 LW) (1 LW)] } (2.25)
-
Analysis of Threshing performance indices
Bearing in mind efficiency, affordability, simplicity and portability, the mathematical models are simulated and analyzed which resulted the following variables which are considered to define the threshing performance indices which consequently will fix the geometrical model of the Teff threshing and separation systems.
-
Crop material feeding velocity Vf to the threshing drum is 0.9m/s
-
Threshing drum diameter is 450mm
-
Threshing drum speed is 450 rpm
-
Threshing drum length is 700mm
-
2.4.1 MOG Feed Rate
According to the listed parameters above and equations discussed in section 2.3.1, the MOG feed rate for the designed machine is calculated as follows.
From table 3.6, the maximum value of the straw diameter in all cases is 1.88mm. This means the threshing drum along its 700mm length can house 372 number of straws if it lay one next to another in a series. But considering the space needed so that no clogging occurs, lets assume the straw diameter to be 3mm which will result 230 number of straws. On the other hand, the concave inlet clearance is 20mm, which means it can hold 5 number of straws considering 3mm of straw diameter. Therefore multiplying 230 by 6, the threshing space can house a total number of 1150 straws (straw with grain) at a time.
As Teff crop height is taken to be 900mm and the feeding velocity is defined to be 0.9 m/s, the threshing drum receives 1150 individual Teff straw every second. Though the concave wraps the threshing drum at an angle of 120o, lets consider the threshing drum discharges the straws every half revolution (1800) to the next zone which is the separation drum assuming the slippage between the crop material and the rasp bars. This means the first round of feed materials will stay in the threshing drum for only half of the revolution. From researches, each straw of Teff holds minimum of 500 number of Teff grains. With this data and values from Table 2-1 and 2-2, the mass of MOG throughput QM is expressed as follow.
QM = (Ts x Sw) + (Ts x Tg x Gw) (2.26)
Ts = 1150, Tg = 500 (2.27)
Sw = 9 x 0.064 = 0.576 (2.28)
Gw = 0.320/1000 = 0.00032 (2.29)
Substituting equation 2.27-2.29 into equation 2.26, the total mass of MOG throughput QM becomes
QM = Ws + Wg = 846.4 gram = 0.846 kg (2.30)
The MOG throughput is the product of the total mass of the MOG throughput QM and the number of rounds of total straw N processed per unit time. In this case since the feeding velocity is
0.9 m/s and Teff straw height is 0.9m, one round of 1150 number
35×10.6x10x103
( 0.14 + 15.1 10.6 )
of straws will be processed every second.
= KT
e 0.53 12
0.14×15.1
10.6
(2.33)
Therefore, QP becomes
QP = QM x N (2.31)
QP = 0.846 x 1 = 0.846 kg/s = 3 ton/hr (2.32) Considering affordability and design simplicity, manual feeding of Teff material is chosen at a feeding velocity of 0.9 m/s. This value can be changed to a higher value to match the threshing drum peripheral speed (10.6 m/s) so that larger amount of MOG is processed. If the feeding velocity is increased to 2.7 m/s, the mass of MOG throughput increases drastically to 2.54 kg/s or 9.1 ton/hr since the number of rounds of straw processed per unit time increases to 3. This requires a powered feeding mechanism like screw or conveyer method though it will inrease the cost of the machine questioning the machines
affordability to the majority of farmers.
Out of 0.846 kg/s of QP, Teff grain comprises 0.184 kg. Thus, without considering the separation and cleaning losses and assuming ideal threshing, the machine has an ideal threshed Teff grain output of 0.184 kg/s or 662.4 kg/hr.
2.4.2 Percentage of threshed and separated Teff grain in the threshing drum
According to section 2.3.2, the percentage of threshed and
= 4.4KT (2.34)
Because is proportional to threshing losses, lets take the value of KT to be 1.08 assuming 8% increase to analyze the threshing efficiency in worst case scenario. Thus, becomes
4.75 m-1. Now all the values to determine the probability of threshed grain GT(x) as a function of concave length x are known.
GT(x) = 1- ex = 1 e4.75x (2.35)
At the end of the concave length (exit), the probability of threshed grain GT(x = L = 490mm) becomes,
GT(x = L) = 1- e4.75L = 0.902 = 90.25% (2.36)
The percentage of unthreshed grain GR(x) becomes,
GR(x) = ex = e4.75x (2.37)
At the end of the threshing space where x = L, the percentage of unthreshed grain GR(x) becomes the threshing loss TL in the threshing unit.
TL = GR(x=L) = e4.75×0.49 = 0.0975 = 9.75% (2.38)
Separating rate parameter (m-1) which describes the rate of grain separation along the threshing and separation space is determined as
separated Teff grain in the threshing drum is as follows.
= KS 10.6×15.10.846
= 1.133 KS (2.39)
Qp U
Vc (0.846
15.1)
Vce ( + )
783 e 2.052+ 15.1
= KT e Q UM V
QpU
If it is considered that the threshing space will be filled with exactly the straw diameter assuming 2mm though the maximum diameter is 1.88mm from Table 2-2, the space will be filled with 350 number of straws along the length of the threshing drum
Lets assume the value of KS to be 0.7. Since the separating rate parameter is directly proportional to the separation process, reducing the value of will increase the safety factor of the outcome. So becomes 1.04. Thus, the fraction of separable and segregated grain GS(x) can now be determined as,
(700mm).
GS(x) = 1.04
4.75 1.04
(e1.04X e4.75X) (2.40)
Figure 2.2 Threshing and separation unit
Multiplying 350 number straws with 8 assuming the inlet concave clearance space (20mm) holds 8 number of straws, the optimum number of straws would be 2800. Using equation 2.26
2.29 results an Optimum working MOG throughput Q of 2.05 kg/s, but due to extra factors like human operator incapability and slippage between straws and rasp bar, consider an optimum throughput of 0.53kg/s. Since the designed Teff thresher is manually fed, the MOG throughput or feed rate is dependent on the operator. So consider minimum feed rate of 0.14 kg/s to be realistic and analyze worst case scenario.
Therefore, except KT all the other variables are known to determine the threshing rate parameter .
The thresher (threshing drum) separation loss SL becomes:
SL = GS(x=L) = 14.12% (2.41)
Therefore, the fraction of separable and segregated grain which is the amount of grains that are threshed but segregated in the straw mat that needs separation in the separator is 14.1%. Thus, the percentage of grain separation TS at the end of the threshing space becomes
TS = 1 – GS(x=L) = 85.88% (2.42)
In the threshing drum (threshing space), 90.25% of Teff grains are threshed (grains are detached) and out of the 90.25% threshed grains, 85.88% of Teff grains are separated (passed through the threshing concave openings). However, the threshing losses which are the remaining 9.75% of the MOG throughput and 14.12% of threshed but segregated grains are forced to flow to the next unit, separation drum, for further threshing and separation.
-
Percentage of threshed and separated Teff grain in the separation drum
As discussed in section 2.3.4, the probability of grains to be detached in the separator GTS(Xs) along the separation space (separator concave length) XS is given in equation 2.18. Thus, at the end of the separation space, the probability of grains to be detached GTS(LS) becomes
GTS(Xs=LS) = 1- e4.75Ls = 84.32% (2.43)
At the end of the separation space, the separator threshing loss STL becomes,
STL = 1 GTS(LS) = eLs = 15.68% (2.44)
At the end of the separation space, the fraction of separable and segregated grain GSS(XS) becomes the separation loss SSL.
t= 90.25% + 0.8432×9.75% = 98.47% (2.50)
In the separation process, other than the threshing drum, the
SSL = GSS(XS=LS) =
(eLs eLs ) = 14.31% (2.45)
separation drum and the straw walkers are involved. Out of
So the percentage of separated grain at the end of the separating space SS is
SS = 1 – GSS(LS) = 85.69% (2.46)
Thus, in the separator, from the remaining unthreshed and unseparated Teff grains that came from the threshing drum, 84.32% are threshed (Teff grains are detached) and 85.69% are separated. The remaining 15.68% unthreshed Teff grain and 14.31% unseparated Teff grain are send to the last unit of separator, the straw walker.
-
Percentage of separated Teff grain in the straw walker There are three shakers that constitutes the straw walker along the length of the separation drum. The length of each shaker (individual straw walker) is 1500mm and width 235mm. From equation 2.24, total threshing loss Vt is the total remaining unthrshed grain that enters the straw walker. There is 90.25% of threshed grain in the threshing drum and 85.88% of threshed grain in the separator. Which means out of the 9.75% threshing loss in the threshing drum, 84.32% which is 8.22% of Teff grains are recovered in the separating drum. Therefore, the total threshing loss Vt is 1.53% (100-90.25-8.22). With the same procedure, the total separation loss Vs which is the total remaining unseparated Teff grain that enters the straw walker is 2.03% (100-85.88-12.09). Take a=1.9 and b=0.9 since this values result the highest losses which will help to analyze the
worst circumstances.
So the fraction of remaining grains GW(y) that still exist with the straw mat at the end of the straw walker length LW is GW(y=LW) = (0.0153 + 0.0203) {1 – 1 [1.9 (1 0.9)
0.9
0.9 (1 1.9)] } (2.47)
Thus, the straw walker separation loss WL becomes,
WL = GW(y=LW) = 1.89% (2.48)
Therefore, the percentage of separated grain at the end of the straw walker SW is 98.11%. This implies 98.11% of the separation losses are recovered (Teff grains are separated) in the straw walker.
-
Model Based Threshing and Separation efficiency
The threshing and separation efficiency is one of the major performance indices that indicates the Teff thresher performance to thresh and separate Teff MOG throughput. This efficiencies are determined from the performance indices analyzed earlier. The threshing efficiency is defined as the ability of the machine to detach Teff grains from the MOG throughput whereas, the separation efficiency is the machines capability to separate Teff grains that were threshed but segregated in the straw mat. This tasks are done by the actions of the threshing drum, the separation drum and the straw walker in a continuous MOG flow.
Threshing efficiency is calculated from the individual threshing capacities in the threshing and separation units. The probability of threshed grain in the threshing and separation unit is 90.25% and 84.32% respectively as indicated in equation 2.36 and 2.43. This means 84.32% of the threshing drum threshing loss (9.75%) is rethreshed in the separator. Therefore, the overall model based threshing efficiency t of the Teff threshing machine becomes:
t = GT(L) + GTS(LS)xTL (2.49)
90.25% threshed Teff grains in the threshing drum, 85.88% got separated from the sraw mat and move to the cleaning system through the threshing concave openings. The remaining 14.12% flows to the separation drum. As discussed in equation 2.42, 85.88% of the threshing drum separation loss (14.12%) is recovered and passed through the separation concave openings. Out of the 14.31% separation drum separation loss, 98.11% are reseparated in the straw walker. So the overall model based separation efficiency s becomes:
s = TS + SSxSL + SW(SSLxSL) (2.51)
s = 99.96% (2.52)
Thus, only 1.53% of Teff grains from the MOG throughput are not threshed and from the 98.47% of threshed Teff grains, 99.96% of the grains are separated through the concave and screen openings and passed to the cleaning unit.
2.5 Geometrical modeling
Complete model of the Teff threshing machine is shown in the figure 2.6. To make the threshing, separation and cleaning systems visible, some parts of the machine housing is hidden.
2.5.1 Power consumption
The total power consumption for the Teff threshing machine can be identified after determining the power requirement of the threshing, separation and cleaning units. Since this paper focuses only on the threshing and separation systems, the power analysis will focus only in the two.
Figure 2.3 Threshing drum unit and separator
Threshing Unit
2
2
According to O.J Olaoye [26], the power PT required to drive the threshing drum is
PT = 2N Md ( g + Vc ) (2.53)
60 75 D
Where, N Drum speed (rpm)
Md Mass of threshing drum (kg)
g Gravitational acceleration (ms-2)
D Threshing drum diameter (m)
Vc Drum peripheral velocity (m/s) Substituting N = 450rpm, Md = 39.16kg, g = 9.81ms-2, D =
0.45 and Vc = 10.6m/s in equation 3.58 results,
PT = 6.39 kw (2.54)
Power per throughput of MOG PG required to detach grains from their panicle is calculated according to C.O.Osueke [27] and it is expressed as:
Therefore, the power consumption PW to drive the straw walker results
PW = 474.7 w = 0.47 kw (2.68)
2
2
PG = Ke [Vc Qp ] (2.55)
g C2
Where, Ke Grain size characteristics constant Qp MOG feed rate (kg/s)
g Grain bulk density (kg/m3)
C Average concave clearance (m)
Substituting Vc = 10.6m/s, Qp = 0.846kg/s, g = 1340 kg/m3 and C = 14mm into equation 3.60, the Power PG required to detach Teff grains becomes
PG = 28.88Ke w (2.56)
Considering the values of other grains, take the grain size characteristics constant Ke to be 0.20. This results
PG = 5.77w (2.57)
This implies the Teff threshing machine will consume 6.82kw to thresh ton of MOG throughput. The total power consumption P becomes the summation of PG and PT.
P = PG + PT = 6.395 kw (2.58)
Separation Unit
The power PS required to drive the separation drum is
Figure 2.4 straw walker separation unit
2
2
P = 2Ns MS ( g + Vs ) (2.59)
S 60 75 Ds
Where, Ns Separation drum speed (rpm) MS Mass of separation drum (kg) Ds Separation drum diameter (m)
Vs Separation drum peripheral velocity (m/s) Substituting Ns = 400rpm, MS = 26.07kg, g = 9.81ms-2, Ds
= 0.4 and Vs = 8.37m/s in equation 3.64 results,
PS = 2.69 kw (2.60)
Power per throughput of MOG PGS required to detach grains from their panicle is
Figure 2.5 cleaning unit
PGS
= Ke [Vs Qp ] (2.61)
2
2
g Cs2
Where, Cs Separation concave average clearance (m) Substituting Vc = 8.37m/s, Qp = 0.846kg/s, g = 1340 kg/m3,
Ke = 0.2 and C = 16mm into equation 3.66, the Power PGS required to detach Teff grains becomes
PGS = 3.5 w (2.62)
Therefore, the total power PTS required to drive the separation unit is
PTS = PS + PGS = 2.7 kw (2.63)
Straw walker unit
The power consumption of the straw walker PW can be determined as
PW = 2Nw Tw
60
Where, Nw Straw walker speed (rpm)
Tw Torque (Nm)
(2.64)
The torque is calculated from the weight on the straw walker WW and the crank radius Rc. Ww is the mass of the straw walker MW and the mass of the straw fragments and MOG materials received from the separator. Assuming maximum load of MOG on the straw walker which is mass of the material throughput QM, WW becomes
WW = QM.g + MW.g (2.65)
WW = 8.3 + 495.4 = 503.7 N (2.66)
The crank radius Rc is 45mm. Hence the torque Tw becomes
Tw = Ww x Rc = 22.66 Nm (2.67)
Figure 2.6 Tangential Teff threshing machine
-
-
RESULT AND DISCUSSION
3.1 Validation of Designed Threshing and separation systems
The designed Teff threshing and separation sytem is evaluated and validated in comparison with a developed Teff thresher designed by Geta Kidanemariam [24]. Evaluation of threshing performance indices of the newly designed system is done in comparisons with Geta kidanemariams [24] design, a
PHD thesis submitted to Addis Ababa university and a paper published by International Journal of Engineering.Vol.17 no3,
Q = 0.53kg/s, UM = 21%, V = 27m/s and KT = 1.08, the threshing rate parameter becomes,
May 2019. He evaluated and compared his design with another
35x27x8x103
( 0.13 + 12 27 )
existing thresher (Bahir Dar modified SG-2000 thresher).
As far as concerned with the validation, in order to eliminate
= KT
e 0.53
-
x12
= 3.68
21 27
( 3.2)
different results due to size variance, the size of major components of the threshing units are kept similar with Geta kidanemariams design. The threshing rate parameter , the threshing efficiency and the separation efficiency are among the major threshing performance indices that are selected to compare with Geta Kidanemariams design for validation.
For validation purpose, the following threshing drum and Teff crop physical parameters are changed to new values which are exactly the same with Geta kidanemariams design so that comparison is done on similar basis.
-
Threshing drum speed (peripheral velocity) Vc = 27m/s
-
Threshing drum diameter D = 480mm
-
Wet basis Moisture content of Teff U = 12%
-
MOG (Teff straw) bulk density = 35 kg/m3
-
Threshing drum length LD = 830mm
-
MOG throughput (feed rate) QP = 0.13kg/s
-
The above Independent parameters are taken from Geta Kidanemariams design which are kept similar for both designs that are going to determine the threshing performance indices listed in the above paragraph. If the values of this performance indices according to the newly designed model are similar with Geta Kidanemariams model or the error is within 15%, then this research will be validated. But if the error exceeds more than 15%, the newly designed model needs to be analyzed again till the error is below 15%. In the following sections, major threshing performance indices are compared with Geta Kidanemariams design.
-
Threshing rate parameter
Threshing rate parameter is one of the major factors that determines the performance indices of any thresher. Geta Kidanemariam [24] uses a model proposed by simonyan et al.
[28] to determine the threshing rate parameter G to be 3.49 m-1. For the newly designed Teff threshing and separation system, the threshing rate parameter is determined based on the models proposed by [22], [29][31]. So from equation 2.6,the threshing rate parameter is,
To validate the result, lets determine the error E between the two studies. Error E becomes,
E = E = 100% ( 3.3)
E = 3.68 3.49 100% = 5.4%
3.49
Therefore, the validation for the threshing rate parameter is a
good agreement.
-
Threshing Efficiency
Based on Geta Kidanemariams design, the threshing drum efficiency EG at threshing drum speed of 27m/s, feed rate of 0.13kg/s, threshing drum diameter of 480mm ad Teff moisture content of 12% is determined to be 82.5% [24]. With exact parameters, the threshing drum efficiency for the newly designed Teff threshing and separation system is as follows.
From section 2.3.2 and equation 2.5, the threshing drum efficiency GT(x) which is the percentage of threshed Teff grain along the threshing space length x is,
GT(x) = 1- ex
Substituting the value of threshing rate parameter calculated from equation 3.2 and taking the value of the threshing space (concave) length from the design considerations as 0.49m, the threshing drum efficiency GT(x = 0.49) becomes,
GT(x = 0.49) = 1 – e3.680.49 = 83.52%
Error E between the two studies becomes,
E = E = GT EG x 100% (3.4)
E G
E = 83.5282.5 x 100% = 1.23%
82.5
With the above result, the threshing drum efficiency is
validated with good terms.
-
Separation Efficiency
According to Geta Kidanemariams design, the separation efficiency is evaluated at different configurations of feed rate and drum speed. His design considers threshing drum speeds of 1200 rpm, 1000 rpm and 900 rpm. For MOG throughput (feed rate) a value of 400kg/hr, 325kg/hr and 275kg/hr is selected and the moisture content is kept constant at 12% [24]. With combinations of this variables, the separation efficiency is
Vce
( Qp + U
Vc )
analyzed. So using the exact values and configurations, below is
= KT e Q UM V
QpU
(3.1)
the separation efficiency analysis for the newly designed Teff
Substituting exactly same parameters defined from Geta Kidanemariams design discussed in section 3.1, i.e, = 35 kg/m3, Vc = 27m/s, U = 12%, QP = 0.13kg/s and take e = 8mm,
threshing and separation system. If Error between the two designs is below 15%, then the validation process will be on good agreement. The combinations of the independent variables is as follows.
Table 3-1: Drum speed and feed rate combinations for evaluating separation efficiency [24]
Test
Drum speed (rpm)
Feed rate (kg/s)
SGK (%)
1
1200
275
89.12
2
1200
325
94.35
3
1200
400
91.9
4
1000
275
95.62
5
1000
325
93.75
6
1000
400
92.5
7
900
275
94.5
8
900
325
92.45
9
900
400
94.98
SGK: Separation efficiency of Geta Kidanemariams design
Test 1 (1200rpm and 275kg/s)
From equation 2.23, the separation efficiency SS in the
= 4.59
From equation 2.13, becomes,
separation drum which is the percentage of the separated grain
in the separation space is expressed as,
= 0.8 30.15x12x0.0764
(3.7)
(0.0764 12
S = G
(X =L )= ( 1 –
Ls
L )) x 100% (3.5)
35 e
0.53 + 21)
S SS S S
(e e
= 2.3
Where, LS Length of separation concave length, 0.49m
The separation efficiency SS becomes,
L Length of the Threshing concave length, 0.6m
Separation rate parameter
SS = ( 1 – 2.3
4.59 2.3
(e2.3×0.65 e4.59×0.49 )) x 100% (3.8)
Threshing rate parameter
To determine the separation efficiency at a separation drum speed of 1200rpm and feed rate of 275kg/s, the value of and needs to be defined at the specified drum speed, feed rate and
SS = 88.07%
The error E for separation efficiency between the to studies at drum speed of 1200rpm and feed rate of 275kg/s becomes,
E = 88.0789.12 x 100% = 1.17% (3.9)
Teff moisture content.
Doing
89.12
the same procedure for all the other 8 tests, the
From equation 2.6, becomes,
separation efficiency and the error becomes as follows.
35×30.15x8x103
( 0.0764 + 12 30.15 )
= 1.08 e
0.0.0764×12
0.53 21 30.15
(3.6)
Table 3-2: Separation efficiency and error at various drum speed and feed rates
Test
Drum speed (rpm)
Feed rate (kg/s)
SGK (%)
SS (%)
Error (%)
1
1200
275
89.12
88.07
1.17
2
1200
325
94.35
88.56
6.13
3
1200
400
91.9
89.79
2.29
4
1000
275
95.62
87.24
8.76
5
1000
325
93.75
87.77
6.37
6
1000
400
92.5
89.12
3.65
7
900
275
94.5
86.81
8.13
8
900
325
92.45
87.38
5.48
9
900
400
94.98
88.78
6.52
SS: Separation efficiency of newly designed Teff thresher So from all the nine tests for validation, the maximum error
is found to be 8.76% at the minimum drum speed and feed rate of all the configurations and the minimum error is found to be 1.17% at the maximum drum speed and minimum feed rate of the variables. With an average error of 4.9%, it can be stated that the new Teff thresher design is validated with good agreement.
-
Effects of threshing parameters
To deliver a high performance threshing machine, the effects of different threshing parameters like threshing and separation drum speed, drum diameter, concave clearance, concave length, material throughput or feed rate and grain moisture content has to be study on the effects of the performance indices. In the following sections, this parameters and their effect on the threshing performance indices is analyzed. The graphs below are generated by analyzing the relation between the resulted equations of the corresponding indices in the above sections.
-
Effect of Teff threshing drum speed Vc on threshing rate parameter
The threshing rate parameter is one of the major parameter that determines the threshing performance and it is affected by many factors. One of hich is the threshing drum speed. The threshing rate parameter and the threshing drum speed has an inverse relation at a constant exit concave clearance and Teff moisture content. As shown in the graph below, when the threshing drum speed decreases, the threshing rate parameter increases and vice versa.
Figure 3.1 Effect of threshing drum speed on threshing rate parameter
As shown in the figure, the inverse relation is due to the fact that, when the threshing drum speed decreases, Teff materials will have more time to stay in in the threshing space. This will increase the rate of grain detachment from the straw mat which basically is the threshing rate parameter . Although, if the threshing drum speed is increased, then the time to stay in the threshing space will decrease which will result faster movement of materials without complete threshing which then will reduce the threshing rate parameter in a relation shown in the graph.
When Vc is increased from 300rpm (7.06 m/s) to 350rpm (8.24m/s) is reduced by 3.4% from 5.43 m-1 to 5.24 m-1. When Vc is increased from 400rpm (9.42m/s) to 500rpm (11.78m/s), is decreased by 10.37% from 5.02 m-1 to 4.49 m-1. The following table shows the value of at different values of threshing drum speed with in the range 300rpm to 600rpm.
-
Effect of exit Concave clearance on the threshing rate parameter
The exit concave clearance is crucial to the threshing performance indices. Directly or indirectly, all the threshing performance indices are dependent on the exit concave clearance. If the exit clearance is zero, no material will flow to the subsequent unit leading no work at all. And if clearance is very wide, all the straw mat will flow out without adequate grain detachment resulting low performance indices. This effect on the threshing rate parameter at a constant threshing drum speed and moisture content is well described in the figure below.
Figure 3.2 Effect of exit concave clearance e on threshing rate parameter
As shown in the figure, there is an exponential relation between threshing rate parameter and exit concave clearance. When the clearance is wider, because there will be more material flow, the rate of grain detachment increases until it reaches a maximum. When the exit clearance is reduced, since there will not be more material flow, the rate of Teff grain detachment or the threshing rate parameter is reduced significantly.
When e is increased from 4mm to 6mm, increases by 19.7% from 3.89 m-1 to 4.35 m-1. The value of at various values of exit concave clearance is shown in the table below.
-
Effect of Current Concave Position on the Probability of Threshed Teff Grain
In the above section, the current concave position and the probability of threshed grain at a constant moisture content, threshing drum speed and MOG throughput is related as;
GT(x) = 1- ex = 1 e4.75x
Figure 3.3 below shows the relation between the probability of threshed grain and the current position of the concave length or threshing space length. At the beginning of the threshing space length, the probability of threshed grain is zero since no material enters the threshing space yet. The maximum probability of threshed grain is found at the end of the threshing space length where the materials exit the threshing unit.
Figure 3.3 Effect of Current Concave Position on the Probability of
Threshed Teff Grain
At the middle of the threshing space length, that is when Teff materials travel 50% of the threshing space length, 69.5% of Teff grains from the input amount are threshed. It can be shown that the longer the concave length (threshing space length), the higher the probability of Teff grain detachment. The following table shows, the percentage of threshed grain at different concave positions.
The comparison between the probability of threshed and unthreshed Teff grain along the threshing space length is shown in the figure below.
Figure 3.4 threshed and unthreshed Teff grain along the threshing space
length
As shown in the figure, at the beginning of the threshing space length, the probability of unthreshed Teff grain is 100% since there is no material yet. But this value reduces along the threshing space length and it gets its threshing loss 9.25% at the end of the concave length where Teff material exits the threshing unit.
-
Effects of MOG throughput (Feed rate) on Threshing Efficiency
The effect of feed rate on the threshing efficiency in the threshing drum is described in the figure 4.5 below. When the feed rate is increased from 0.14kg/s to 0.26kg/s, the threshing efficiency drops by 2.2% from 90.28% to 88.29%. This is because the sudden increase in feed rate will clog the threshing space limiting the flow of crop materials. In this case, some portion of the crop will be segregated in the straw mat which will remain undetached from the straw. When the feed rate reaches 0.5kg/s, the threshing efficiency in the threshing drum
increases by 3.2% from 88.29% to 91.22%. This is due to the fact that after few revolutions of the threshing drum, the clogged straw will leave the threshing space allowing more impact on the straw mat.
Figure 3.5 Effect of feed rate on threshing rate parameter
The effect of feed rate at constant drum speed on the threshing rate parameter lambda and threshing efficiency is shown in figure 3.6. As it can be shown, the change in the threshing rate parameter due to feed rate has a small impact in the threshing efficiency.
Figure 3.6 Effect of MOG feed rate on threshing rate parameter and
threshing efficiency
-
Effects of MOG throughput (Feed rate) on Separation Efficiency
The Effect of MOG throughput on separation rate parameter and separation efficiency is shown in Figure 3.7. Due to the same reason as the threshing efficiency, the straw clogging due to feed rate will reduce the efficiency at first, but after drum develops continuous inertia, the clog will break which in turn increases the separation efficiency. In general, the separation efficiency increases by 0.8% when the feed rate is increased from 0.14kg/s to 0.5kg/s.
Figure 3.7 Effect of MOG throughput on separation rate parameter and
separation efficiency
-
Relations of Separation Efficiency Separation loss over the concave length
The separation efficiency has a maximum value at the beginning of the concave and reduces to a certain value at the end of the separation space as shown in figure 3.8. On the other hand the separation loss is zero at the concave inlet and it reaches the maximum value at the concave exit. This is due to the fact that at the concave inlet, there is no material inlet yet, hence there is no separation loss. But as the separation space advances to the concave exit, the separation loss increases to its maximum value 14.12% as shown in figure 3.9.
Figure 3.8 Relations of Separation Efficiency over the concave length
At the concave inlet, since there is no material inlet, unseparated grain is zero. Which means the separation efficiency is 100%. But as the concave length advances, unseparated grain will increase while the separation efficiency is decreased. At the end of the concave the separation efficiency reaches 85.76%. At 45% of the concave length, the separation efficiency is 88.08%. So the separation efficiency drops 2.6% after half of the concave length.
Figure 3.9 Relations of separation loss over the concave length
At the middle of the concave length, that is when the straw mat advances 0.225m, the separation loss is 12.49%. So in the remaining half of the concave length, the separation loss increases only 1.63% to reach 14.12%. To compare the separation efficiency and the separation loss, their relation over the concave length is shown in Figure 3.10.
Figure 3.10 Relations of separation efficiency and loss over concave length
-
Effects of Drum speed on Separation Efficiency
-
The effect of Drum speed is proportional to the Separation Efficiency. Increasing the drum speed will increase the separation efficiency at the cost of grain damage. Because over a certain drum speed, the impact of separation drum will be high resulting a grain damage. As shown in Figure 3.11, when drum peripheral speed is increased from 10.6m/s to 21.2m/s, the separation efficiency increases by 2% from 85.9% to 87.42%.
Figure 3.11 Effects of Drum speed on Separation Efficiency
3.2.7 Power consumption
The Effect of Drum speed on Drum power consumption is shown in figure 3.12. The relations shows, an increase in drum speed from the input power source will increase the power requirement. When the drum speed is increased from 450rpm to 650rpm, the power consumption increases by 6.28% from 6.38kw to 17.2kW.
Figure 3.12 Effect of Drum speed on Drum power consumption
-
-
CONCLUSION AND RECOMMENDATION
-
Conclusion and Recommendation
From this research work, the following conclusions were drawn.
-
The MOG feed rate, the threshing efficiency, separation efficiency in the threshing drum, separation drum and in the straw walker is determined.
-
The performance of the threshing unit is validated with a thresher designed and prototyped by Geta kidanemariam which is based on another model and the result shows the maximum and minimum separation efficiency error between the two studies were 8.76% and 1.17% respectively. Hence, all the performance indices mathematical functions were validated with experimental data obtained from Geta Kidanemariams design.
-
The evaluation was analyzed with various configurations of threshing drum speed and MOG feed rates. The drum speed used was 900rpm, 1000rpm and 1200rpm whereas the MOG feed rate used was 275kg/s, 325 kg/s and 400 kg/s.
-
The error generated between the two studies on the threshing rate parameter was determined to be 5.4%.
-
The designed model illustrates the relations of threshing parameters like drum speed, MOG feed rate, moisture content, concave clearance and concave length with performance indices.
-
The percentage of threshed grain in the threshing drum and in the separation drum is 90.25 and 84.32% respectively. The percentage of separated grain in the threshing space, separation space and straw walker is 85.88%, 85.69 and 98.11% respectively.
-
The above performance indices at different sections of the machine defines the Teff threshing machines overall threshing efficiency to be 98.47% and the overall separation efficiency to be 99.96%.
-
Any related research in the future should consider the value of portability and the countries land scape for agricultural activities so that the end users can move from field to field easily.
-
When designing or using a Teff thresher, the appropriate moisture content of the Teff should be noted. High moisture content will increase difficulties during MOG flow and very law moisture content will increase grain damage.
-
The inlet and exit concave clearances are crucial during designing and operation of the machine.
-
REFERENCES
-
K. Baye, Teff: nutrient composition and health benefits, 2014.
-
FAO, Post harvest lossses, Rome, 2013.
-
Abayineh Awgichew, Design And Development Of Tef Grain And Chaff Separating And Cleaning machine, Haramaya University, 2015.
-
Kamil Ahmed and Ayalew Bekele, Regional Review Workshop on Completed Research Activities, 2015.
-
M. W. Dula, Development and Evaluation of Teff Threshing Machine, Int. J. Eng. Res. Technol., vol. 5, pp. 420429, 2016, [Online]. Available: http://www.ijert.org.
-
H. Stoyanov, Development and characteristics of accessions of Eragrostis tef (Zucc.) Trotter in South Dobrudja, Agric. Sci. Technol., vol. 6, no. 1, pp. 8085, 2014.
-
S. Ketema, Eragrostis tef ( Zucc .) Trotter. Rome: Institute of Plant Genetics and Crop Plant Research, 1997.
-
C. B. et al Girma Chemeda, Adaptation and Generation o f Agricultural Technologies, Oromia Agricultural Research Institute, Adama, 2017.
-
W.E. DO GOOD and S. Zahn, A Low-Cost , Teff Thresher, 2011.
-
T. Evers and S. Millar, Cereal grain structure and development: Some implications for quality, J. Cereal Sci., vol. 36, no. 3, pp. 261 284, 2002, doi: 10.1006/jcrs.2002.0435.
-
N. Satheesh and S. W. Fanta, Review on structural , nutritional and anti-nutritional composition of Teff ( Eragrostis tef ) in comparison with Quinoa ( Chenopodium quinoa Willd .), Cogent Food Agric., vol. 4, no. 1, pp. 127, 2018, doi: 10.1080/23311932.2018.1546942.
-
R. D. Wake, A. H. Mesfin, and C. Yirga, Adoption and Perception of Farmers towards Attributes of Improved Teff ( Quncho ) Varieties: Evidence from Benishangul-Gumuz Region of Ethiopia, Curr. Res. Agric. Sci., vol. 6, no. August, pp. 6882, 2019, doi: 10.18488/journal.68.2019.62.68.82.
-
K. Assefa et al., Quncho: the first popular tef variety in Ethiopia Quncho: the first popular tef variety in Ethiopia, Int. J. Agric. Sustain., vol. 9, no. 1, pp. 2534, 2011, doi: 10.3763/ijas.2010.0545.
-
T. Tesfaye and D. Befikadu, Modification and Testing of Replaceable Drum Multi-Crop Thresher, Int. J. Sci. Basic Appl. Res., vol. 23, pp. 242255, 2016, [Online]. Available: http://gssrr.org/index.php?journal=Journal Of Basic And Applied sciences.
-
FDRE Ministry of Agriculture and Natural Resources, POSTHARVEST MANAGEMENT STRATEGY, 2018.
-
A. M. and A. Tadesse, REVIEW OF MAJOR GRAINS POSTHARVEST LOSSES IN ETHIOPIA AND CUSTOMIZATION OF A LOSS ASSESSMENT METHODOLOGY, Addis Ababa, 2018.
-
FAO, Food loss analysis: causes and solutions. Rome, 2018.
-
M. Ensermu, Teff Commodity Value Chain Analysis in Addis Ababa, Res. J. Soc. Sci. Manag., pp. 1522, 2015.
-
A. Mohammed, Investigation into Tef Grain, Straw and Chaff Mixture Separation and Cleaning, Adama University, 2010.
-
B. Dolani, what is probability density function, 2020. .
-
D. Q. Nykamp, The ideaof probability density function, 2020. .
-
M. Petre, Mathematical modeling of threshing process in cereal combine harvesters, Politehnica University of Bucharest, 1995.
-
B. C. Bill A. Stout, CIGR Handbook of Agricultural Engineering Volume III, III., vol. III. the American Society of Agricultural Engineers, 1999.
-
G. Kidanemariam, Theoretical and Experimental Investigation of Threshing Mechanism for Tef, Addis Ababa University, 2020.
-
P. Miu, separation process and operation of straw walkers, in
combine harvester theory, modeling, design, 2016, pp. 261269.
-
J. O. Olaoye, Development of a Treadle Operated Abrasive- Cylinder for Threshing Cowpea, Int. J. Eng. Sci. Technol., vol. 3, no. 12, pp. 123125, 2011.
-
E. C. O. Osueke, M. Engineering, and E. State, Simulation and Optimization Modeling Of Performance of a Cereal Thresher, no. June, 2011.
-
Simonyan, Mathematical modeling of the grain cleaning process in a stationery sorghum thresher, Int. J. Agric. Eng., 2006.
-
P. Miu and H. K. Agriculture, Modeling and simulation of grain threshing and separation in threshing unitsPart I, Elsevier, 2008, Accessed: May 10, 2019. [Online]. Available: https://www.sciencedirect.com/science/article/pii/S0168169907001 512.
-
Miu Petre, Models of Threshing and Separating Process Rates, in combine harvester theory, modeling, design, CRC Press, 2016, pp. 225226.
-
M. Petre, Concave separation in a tangential threshing unit, Am. Soc. Agric. Eng., no. 941544, 1994.