
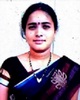
- Open Access
- Authors : Kotla Aswini , Jillidimudi Kamala , Lanka Sriram, Bhasuru Kowshik , Bugatha Ram Vara Prasad, Damaraju Venkata Sai Bharani
- Paper ID : IJERTV10IS070226
- Volume & Issue : Volume 10, Issue 07 (July 2021)
- Published (First Online): 26-07-2021
- ISSN (Online) : 2278-0181
- Publisher Name : IJERT
- License:
This work is licensed under a Creative Commons Attribution 4.0 International License
Design and Analysis of Bidirectional Battery Charger for Electric Vehicle
Kotla Aswini1
Department of Electrical and Electronics Engineering Lendi Institute of Engineering and Technology Vizianagaram, India
Jillidimudi Kamala3
Department of Electrical and Electronics Engineering Lendi Institute of Engineering and Technology Vizianagaram, India
Bugatha Ram Vara Prasad2
Department of Electrical and Electronics Engineering Lendi Institute of Engineering and Technology Vizianagaram, India
Lanka Sriram4
Department of Electrical and Electronics Engineering Lendi Institute of Engineering and Technology Vizianagaram, India
Bhasuru Kowshik5
Department of Electrical and Electronics Engineering Lendi Institute of Engineering and Technology Vizianagaram,India
Damaraju Venkata Sai Bharani6
Department of Electrical and Electronics Engineering Lendi Institute of Engineering and Technology Vizianagaram, India
Abstract The increase in the electric vehicle mobility has encouraged the growth of vehicle to grid technology. The vehicle to grid technology allows bidirectional power flow between the battery of electric vehicle and grid. This allows peak load shaving, load levelling voltage regulation and improvement of power system stability. In this project we developed onboard bidirectional battery charger for Electric Vehicles (EVs) targeting Grid-to-Vehicle (G2V), Vehicle-to-Grid (V2G), and Vehicle-to-Home (V2H) technologies. During the G2V operation mode batteries are charged from the power grid with sinusoidal current and unitary power factor. During the V2G operation mode the energy stored in the batteries can be delivered back to the power grid contributing to the power system stability. In the V2H operation mode the energy stored in the batteries can be used to supply home loads during power outages, or to supply loads in places without connection to the power grid. Along the paper the hardware topology of the bidirectional battery charger is presented. Some considerations about the sizing of the AC side passive filter are considered to improve the performance in the three operation modes. The adopted topology and computer simulations and validated by experimental results achieved
Keywords Bidirectional Battery Charger; Grid-to-Vehicle (G2V); Vehicle-to-Grid (V2G); Vehicle-to-Home (V2H)
INTRODUCTION
Electric Vehicles (EVs), represents a new concept in the transports sector around the world [1]. As a result, the interest in technologies for EVs has significantly increasing from the last few years. In this context, the EVs battery charging process (Grid-to-Vehicle, G2V) must be regulated to preserve the power quality in the power grids. Nevertheless, with the proliferation of EVs a considerable amount of energy will be stored in their batteries, arising the opportunity of the energy flow in opposite direction (Vehicle-to-Grid, V2G). In the future smart grids, the interactivity with the EVs will be one of the key technologies, contributing to the power grid
autonomous operation. Nowadays, several projects related with smart grids are under development across the globe. Regarding this new approach, especially in homes equipped with charging points for EVs, besides the G2V and V2G operation modes the EVs can also operates as voltage source capable to feed the home loads. As example of this new approach, Nissan presented the LEAF-to-Home system. This is a technology that uses energy from the Nissan Leaf batteries to supply the home loads through the EV Power Station unit [2]. Effectively, smart homes with energy management and efficiency solutions will be the first step to the smart grid evolution. However, solutions like the LEAF- to-Home only allows deliver the stored energy in the batteries back to the home in the place where the equipment is installed. In this paper a Bi-directional battery is designed that enables the V2G operation mode in the place where the EV is parked. This battery charger allows receive energy from the power grid (G2V), and deliver back to the power grid part of the stored energy in the batteries (V2G). From the point of view of the power grid, EVs can bring benefits to ancillary services, compensation of the renewable energy sources intermittency (providing both backup, storage and load-shift).
This new approaches are more relevant when looking that private vehicles are parked on average 93-96% of their lifetime and most of the vehicles [3] are at home between 8 pm and 7 am. The concept of the bidirectional charger with V2G and G2V technologies is introduce in Fig. 1. When the EV is connected to the power grid the energy can flow to or from the EV batteries (G2V and V2G) [4]. In the absence of power grid or power outages, the EV can operates as voltages source to feed the desired loads. The system is not intended for a real-time energy backup, but has an auxiliary energy storage system. Thus, the transitions between the modes can be seamless.
Fig:1 Bidirectional charger Technology
-
BIDIERCTIONAL BATTERY CHARGER
A. Charger Topology
The presented battery charger is composed by two power converters that share a DC link. One is to interface the power grid and the other is to interface the traction batteries [5]. In order to interface the power grid is used a full-bridge AC-DC bidirectional converter which is shown in fig 2. This converter can operate as active rectifier with sinusoidal current and unitary power factor during the G2V operation mode [6]. During the V2G and V2H operation modes this power converter operates as inverter. In the V2G mode the converter operates as controlled current source to inject the required power in the power grid. In the V2H mode, the converter operates as a controlled voltage source with true sine-wave output to feed the home loads. In order to interface the batteries is used a reversible DC-DC converter. In the G2V operation mode this converter operates as buck converter to control the current and voltage during the current and voltage batteries charging stages, respectively.
Fig:2 Single-phase bidirectional battery charger topology
-
CONTROL ALGORITHMS
The control algorithms of the two converters is different in each of the three possible operation modes (G2V, V2G and V2H) are described as:
-
Grid-to-Vehicle (G2V) Operation Mode
During this operation mode the full-bridge AC-DC bidirectional converter operates as active rectifier with sinusoidal current and unitary power factor. The reversible DC-DC converter operates as buck converter.
In order to accomplish with the maximum amplitude of the individual current harmonics specified by IEC 61000-3-2 standard, it is mandatory that the full-bridge AC-DC bidirectional converter controller must be synchronized with the power grid fundamental voltage [7]. Therefore, a single- phase Phase-locked Loop (PLL) is the first algorithm implemented by the digital controller. To accomplish with this requirement a single-phase PLL in the – coordinates is used. This algorithm produces two sine-waves with unitary amplitude shifted by 90º: pll and pll. When the PLL is synchronized with the power grid, the signal pll corresponds to the direct component of the power grid fundamental voltage. This signal is used as input to the subsequent digital control algorithms.
The second control algorithm is responsible to calculate the reference current for the full-bridge AC-DC bidirectional converter. The amplitude of the reference current is achieved through the division of the reference active power by the power grid voltage, affected by the pll signal The reference active power is obtained through a PI controller designed to keep the DC link voltage regulated. In Fig. 3 it can be seen the control block diagram to generate the current reference (iS*). This current control uses the circuit model parameters and the information from previous samplings to calculate the voltage that the full-bridge AC-DC bidirectional converter must produce in each switching period, k, and can be resumed by:
Fig:3 Control block diagram to generate the current reference of the full- bridge AC-DC bidirectional converter.
Fig:4 Control block diagram of the current control technique
The reversible DC-DC converter is controlled in both constant
current and constant voltage stages as shown in Fig. 5. During the constant current stage the reference current (iTB*) is compared with the actual current (iTB). The obtained current error feeds a PI controller that adjusts the output duty- cycle through a PWM modulator with a triangular carrier of 20 kHz. When the maximum voltage value recommended by the batteries manufacturer is reached the control algorithm changes to the constant voltage stage. In this stage a second PI
controller is used to maintain constant the output voltage (vTB) of the reversible DC-DC converter according to the voltage reference (vTB*).
-
Vehicle-to-Grid (V2G) Operation Mode
The full-bridge AC-DC bidirectional converter operates as inverter with sinusoidal current and unitary power factor, and the reversible DC-DC converter operates as a boost converter [8].
As in the G2V operation mode, in the V2G mode the full-bridge AC-DC bidirectional converter must be synchronized with the power grid fundamental voltage. As aforementioned the synchronization is obtained through a single-phase – PLL in – coordinates. The active power to be delivered to the power grid is established as external input parameter received from a serial communication port in order to enable the collaborative integration of the EV in a smart grid context. Therefore, the control algorithm employed in the V2G operation mode is similar to the one used in the G2V operation mode. Aiming to synthesize the reference current correspondent to the active power to be delivered it was also used a predictive current control [9].
In order to the full-bridge AC-DC bidirectional converter
deliver back to the power grid the energy stored in the traction
batteries, the DC link voltage must be slightly greater than the
peak value of the power grid voltage. For such intent, the reversible DC-DC converter has to operate as a boost converter, once the traction batteries voltage is smaller than the required to the DC link voltage. The traction batteries voltage does not suffer significant variation during short time periods, consequently the regulation of the active power delivered back to the power grid can be done by the absorption of a constant current from the traction batteries [10]. However, as the batteries voltage decreases along the discharging process it is necessary to increase the reference current to maintain the active power constant. The division of the reference active power (P*) by the traction batteries voltage (vTB) results in the traction batteries reference current (iTB*). The error between this current (iTB*) and the actual current (iTB) feeds a PI controller that adjusts the duty-cycle for a 20 kHz PWM modulator, as shown in Fig. 6.
Fig:5 Control block diagram of the reversible DC-DC converter digital controller: (a) Constant current stage; (b) Constant voltage stage.
Fig:6 Control block diagram of the reversible DC-DC converter digital controller during V2G operation mode.
-
Vehicle-to-Home (V2H) Operation Mode
During the V2H operation mode the full-bridge AC-
DC
bidirectional converter synthetizes a sine-wave voltage with the desired amplitude and frequency to feed the home loads. As in the V2G operation mode the reversible DC-DC converter operates as a boost converter in order to maintain the DC link voltage with adequate amplitude for the proper operation of the full-bridge AC-DC bidirectional converter [11].
As the power absorbed by the loads is not constant and changes along the time, the power absorbed from the traction batteries must follow this load variation in order to maintain the DC link voltage regulated. Since the full-bridge AC-DC bidirectional converter only controls the output voltage amplitude and frequency, the regulation of the DC link voltage
has to be done by the reversible DC-DC converter [12].
The control algorithm of the full-bridge AC-DC bidirectional converter applied in this operation mode is presented in Fig. 7. The reference voltage is obtained from a sine table stored in the internal memory of the digital controller. In a voltage source inverter controlled in voltage mode, the control of the output voltage is done directly by adjusting the duty-cycle value of the PWM modulator [13].
In order to enhance the quality of the produced waveform it is important to compensate the IGBTs dead-time effect and the voltage drop in the inductance of output filter, L1. So, the voltage that the full-bridge AC-DC bidirectional converter must produce is the reference voltage minus the inductance voltage. In this control algorithm the inductance voltage is expressed with minus signal due to the signal arbiter as positive for the AC side current (positive from the
grid to the power converter) [14]. In order to maintain the DC link voltage regulated is used the control algorithm presented in Fig. 8. The reference of the DC link voltage is compared with the actual voltage and the resultant error feeds a PI controller that adjusts the duty-cycle for a 20 kHz PWM modulator [15].
Fig:7 Control block diagram of the full-bridge AC-DC bidirectional converter digital controller during V2H operation mode.
-
-
SIMULATION OF THE BIDIRECTIONAL CHARGER
Fig:8 Simulink model of Bidirectional electric charger
Fig:9 Proposed Simulink model of AC/DC converter with controller circuit
Fig:10 Proposed Simulink model of DC-DC converter with battery controller
-
RESULTS AND DISCUSSIONS
Simulation is conducted to test the performance of the proposed bidirectional controller under, Grid to vehicle and Vehicle to grid operation. The battery initial SOC is set to 50 percent. This value is chosen to ensure that the battery is able to receive or supply power when necessary.
Initially, the simulation requires some times to start up and stabilize. This procedure takes around 1 minute.
-
G2V:
To operate in G2V (Grid to Vehicle) mode switch has to be set to 0.
-
SOC gradually increasing from point 58 because we have to set the initial state of charge to 60%.
-
Current = -22 A to -28 A (Negative value referring that the battery is charging state).
-
Grid voltage (Vgrid)will be positive and 249 V (+_3V) and Inverter voltage (V_inv) have to be 0 but there is a likage voltage is flowing on of (0.2- 0.5) but if we observe the 3rd waveform combination, the V_inv is at 0.
-
V_inv can be made 0, by substituting the perfect filter circuit value after rectification process.
Fig:11 Simulation results of Battery graph for Grid to Vehicle Operation
-
-
-
ANALYSIS OF BIDIRECTIONAL CHARGER
Fig:12 Simulation Voltage graph for Grid to Vehicle Operation
-
V2G:
During V2G operation, SOC will decrease and battery current and battery voltage will be positive.
To operate in V2G mode the switch has to be set to 1.
-
SOC gradually decreasing from point 58 because we have to set the initial state of charge to 60%.
-
Current = 22 A to 28 A (Positive value referring that the battery is discharging and been utilized by grid, motor, home or Emergency Purposes).
-
Voltage =249(+_3V).
-
V_grid and V _inv need to synchronous because we are snding back the power to grid so, the voltage magnitude should be equal and need to be in Phase. (Similar concept when we try to perform two transformer in parallel, we need to check for the synchronous between them).
-
Fig:13 Simulation Battery graph for Vehicle to Grid Operation
Fig:14 Simulation Voltage graph for Vehicle to Grid Operation
With reference to the simulation results, the measured battery current is able to follow the reference battery current throughout the simulation process. This shows that the design and analysis of bidirectional battery charger has successfully controlled the direction and magnitude of current flow
Mode of operation
SOC
VOLTAGE
CURRENT
G2V (Grid to vehicle mode)
60%(increasing)
249.4 V
-22 A
V2G
(Vehicle to Grid mode)
60%(decreasing)
247.2V
24.72 A
-
-
CONCLUSIONS
This project presents the development of an on-board bidirectional battery charger for Electric Vehicles (EVs) capable of work in the operating modes Grid-to-Vehicle (G2V), Vehicle-to-Grid (V2G) which consist in important technologies for targeting the future smart grids scenario. The hardware topology and the control algorithms of the presented battery charger are validated through computer simulations, using the MATLAB software, and also through experimental results, achieved with a developed laboratory prototype. Since this work only intends to validate the topology and the control algorithms, the developed prototype that supports this work is intentionally oversized. The experimental results obtained with the three operation modes (G2V, V2G) are in accordance with the expected, validating the viability of the proposed topology.
Bidirectional technology (allowing electricity to flow into and out of EVs) has only just become advanced enough for more people to use it. As the tech gets better with time, so will its potentialities. As an EV owner, you only stand to gain by going for a bidirectional charger. From making extra income by selling energy back to the grid to becoming energy self- sufficient going bidirectional comes with clear pay- offs.
The bidirectional charger is developed which is to be used for the V2G and G2V power flow. It means a charging and discharging with one unit are possible, with the design proposed. It operates in constant current; constant voltage battery charging methods are happening in unit power factor changing. The operating parameters can be adjusted by varying the control signal from the controller. This design allows the charging and discharging operation at the different power level.
REFERENCES
[1] |
A. Shukla, K. Verma, and R. Kumar, Impact of EV fast charging station on distribution system embedded with wind |
PFC and Torque Ripple Reduction using BL Buck- Boost Converter fed HCC BLDC Drive, vol. 02, no. 11, pp. 895901, |
|
generation, J. Eng., vol. 2019, no. 18, pp. 46924697, 2019, |
2015. |
||
doi: 10.1049/joe.2018.9322. |
[9] |
Bugatha Ram Vara prasad, K. M. Babu, K. Sreekanth, K. |
|
[2] |
Bugatha Ram Vara prasad T.deepthi n.satyavathi v.satish varma r.hema kumar, Solar charging station for electric vehicles, Int. |
Naveen, and C. V. Kumar, Minimization of Torque Ripple of Brushless DC Motor Using HCC with DC-DC Converter, vol. |
|
J. Adv. Res. Sci. Commun. Technol., vol. 7, no. 2, pp. 316325, |
05, no. 12, pp. 110117, 2018. |
||
[3] |
2021, doi: 10.48175/IJARSCT-1752. BUGATHA RAM VARA PRASAD, C. PRASANTHI, G. |
[10] |
C. Bai, W. Gao, J. Li, and H. Liao, Analyzing the impact of electric vehicles on distribution networks, 2012 IEEE PES |
JYOTHIKA SANTHOSHINI, K. J. S. V. KRANTI KUMAR, |
Innov. Smart Grid Technol. ISGT 2012, 2012, doi: |
||
and K. YERNAIDU, Smart Electrical Vehicle, i-managers J. Digit. Signal Process., vol. 8, no. 1, p. 7, 2020, doi: |
[11] |
10.1109/ISGT.2012.6175645. H. Shareef, M. M. Islam, and A. Mohamed, A review of the |
|
10.26634/jdp.8.1.17347. |
stage-of-the-art charging technologies, placement |
||
[4] |
Y. Huang, J. J. Ye, X. Du, and L. Y. Niu, Simulation study of system operating efficiency of EV charging stations with |
methodologies, and impacts of electric vehicles, Renew. Sustain. Energy Rev., vol. 64, pp. 403420, 2016, doi: |
|
different power supply topologies, Appl. Mech. Mater., vol. |
10.1016/j.rser.2016.06.033. |
494495, pp. 15001508, 2014, doi:
10.4028/www.scientific.net/AMM.494-495.1500.
-
A. Hussain, V. H. Bui, and H. M. Kim, Optimal Sizing of Battery Energy Storage System in a Fast EV Charging Station Considering Power Outages, IEEE Trans. Transp. Electrif., vol. 6, no. 2, pp. 453463, 2020, doi: 10.1109/TTE.2020.2980744.
-
D. Sbordone, I. Bertini, B. Di Pietra, M. C. Falvo, A. Genovese, and L. Martirano, EV fast charging stations and energy storage technologies: A real implementation in the smart micro grid paradigm, Electr. Power Syst. Res., vol. 120, pp. 96108, 2015, doi: 10.1016/j.epsr.2014.07.033.
-
Bugatha Ram Vara prasad, Solar Powered BLDC Motor with HCC Fed Water Pumping System for Irrigation, Int. J. Res. Appl. Sci. Eng. Technol., vol. 7, no. 3, pp. 788796, 2019, doi: 10.22214/ijraset.2019.3137.
-
R. A. Dolly and Bugatha Ram Vara prasad, Enhancement of
-
Bugatha Ram Vara prasad, D. V. S. J. Poojitha, and K. Suneetha, Closed-Loop Control of BLDC Motor Driven Solar PV Array Using Zeta Converter Fed Water Pumping System, vol. 04, no. 17, pp. 27952803, 2017.
-
Bugatha Ram Vara prasad, HIGHWAY MONITORING SYSTEM AND POWER SAVING, vol. 8, no. 4, pp. 2270 2274, 2020.
-
Bugatha Ram Vara prasad, T. S. Babu, K. A. Jose, and M. Satish, A Novel Performance Evaluation of Power Quality Features Using Hybrid FACTS Device with Induction Motor, vol. 04, no. 17, pp. 32813287, 2017.
-
Y. Zheng, Z. Y. Dong, Y. Xu, K. Meng, J. H. Zhao, and J. Qiu, Electric vehicle battery charging/swap stations in distribution systems: Comparison study and optimal planning, IEEE Trans. Power Syst., vol. 29, no. 1, pp. 221229, 2014, doi: 10.1109/TPWRS.2013.2278852.