
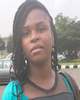
- Open Access
- Authors : I. M. Mobi , C. H. Achebe , C. E. Okafor
- Paper ID : IJERTV10IS070297
- Volume & Issue : Volume 10, Issue 07 (July 2021)
- Published (First Online): 07-08-2021
- ISSN (Online) : 2278-0181
- Publisher Name : IJERT
- License:
This work is licensed under a Creative Commons Attribution 4.0 International License
Optimization of Mechanical Properties of Palm Fruit Fiber Automobile Brake Pad
1I.M. Mobi, 2C.H. Achebe, 3C.E. Okafor
1,2Department of Mechanical Engineering, Nnamdi Azikiwe University, Awka Nigeria.
.
Abstract – This work investigates the optimization of mechanical properties of Palm Fruit fiber automobile brake pad. The use of natural fibers and Agro-based wastes has been eminent in the production of brake pads. For effective pad production, many factors should be considered in developing brake materials so as to fulfill requirement such as, a stable friction coefficient and a lower wear rate at various operating speeds, pressures, temperatures, and environmental conditions in the automotive sectors [17]; [1]. This study employs Split-optimal custom design of the Design Expert (11.0) for sample formulation. Hardness, Compressive strength, wear rate and coefficient of friction were determined. The Result of the Responses determines the optimum PFF content for the pad. This research will enlighten industries and local producers who intends to utilize Palm Fruit fiber for the development of the Automobile brake pads.
Keywords – Palm Fruit Fiber, Optimization, Brake pad, Brake,
-
INTRODUCTION
The braking system is composed of many parts, including brake pads on each wheel, a master cylinder, wheel cylinders, and a hydraulic control system. The core of the braking device is friction material, which is expected to continue its functioning reliably and efficiently for a prolonged time in adverse operating conditions [12]. Different types of brake pad materials are used in different braking systems. They are often categorized into four classes of ingredients: binders, fillers, friction modifiers, and reinforcements. Brake pads generally consist of asbestos fibers embedded in polymeric matrix along with several other ingredients. The use of asbestos fiber as reinforcement in the friction materials started in the beginning of the 20th century. Since asbestos fiber met major requirements of brake friction material, asbestos based friction composites became popular all over the world. Later on, medical reports regarding asbestos exposure to humans proved that asbestos is carcinogenic and can cause deadly diseases. This resulted in ban of asbestos based friction materials in the developed countries, and many developing countries are now on the same path. Sequel to that, several research works have been carried out in the area of development of asbestos-free brake pads. Current trend in the research field is the utilization of industrial or agricultural wastes as a source of raw materials for composite development [13]. This provides more economical benefit and also environmental preservation by utilizing wastes.
Friction materials used in the brake lining of automobiles, are required to satisfy a number of performance demands. They must provide a dependable, consistent level of friction,
excellent resistance to wear, adequate heat dissipation, and structural integrity, low cost and if possible, light weight. No single material can meet all of these often-conflicting performance criteria. The choice of materials is crucial in determining the performance attained, yet to date, braking material compositions have been developed largely on the basis of empirical observations. [7].
The design of experiment (DOE) method of approach, processes variables that are first screened to determine which are important to the outcome (excipients type, percentage, disintegration time (DT) etc. Optimization connotes when the best settings for the important variables are determined. It involves the use of Response Surface Methodology (RSM) to investigate an appropriate approximation relationship between input and output variables and identify the optimal operating conditions for a system under study or a region of the factor field that satisfies the operating requirements.
-
LITERATURE REVIEW
-
Brake Pad
Brake pads are steel backing plates with friction material bonded to the surface that faces the disk brake rotor. It is one of the important parts of an automobile braking system due to its vital role [5]; [10]; [3]. Friction between brake pad and disk converts the kinetic energy of automobile to thermal energy [3]. Two brake pads are contained in the caliper, with their friction surfaces facing the rotor. Brake pads were originally made with organic ingredients, such as asbestos and carbon, held together by a strong resin. The first frictional brake material composed of cotton material impregnated with bitumen solution was invented by Herbert Frood in 1879 [15]; [4]. This led to the establishment of Ferodo Company that still supplies brake pad materials up till now [4].
In disc brake applications, there are usually two brake pads per disc rotor, held in place and actuated by a caliper affixed to a wheel hub or suspension upright. Although almost all road- going vehicles have only two brake pads per caliper, racing calipers utilize up to six pads, with varying frictional properties in a staggered pattern for optimum performance. Depending on the properties of the material, disc wear rates may vary. The brake pads must usually be replaced regularly (depending on pad material), and most are equipped with a method of alerting the driver when this needs to take place.
Materials that make up the brake pad include; friction modifiers, powdered metal, binder, fillers and curing agents.
Friction modifiers such as graphite and cashew nut shells alter the friction coefficient. Powdered metals such as lead, zinc, brass and Al increase a material resistant to heat fade. Binders are the glues that hold the friction materials together. Phenolic resin is the most common binder in use. Fillers are added to friction materials in small quantities to accomplish specific purposes such as rubber chips to reduce brake noise. The brake pad material is bonded to a stamped steel backing plate with high temperature adhesive to which heat and pressure are applied to cure the assembly. A slit is provided on the face of the pad to indicate the allowable limit of pad wear and provide a path for brake dust and gas to escape. A metal plate or in some applications multiple plates called anti-squeal. Various springs and clips are used to reduce rattle as well as reduce brake noise. Shims and plates should be inspected for wear and rust and can be reused when replacing pads. Fresh approved grease should be applied to the shims prior to installation [9].
-
Related Reviews on BrakePad
layer formation in a polymer composite material for brake applications. Their work concentrated on the characterization of friction layer formation and correlation of friction layer properties to the performance of a recently developed family of polymer matrix composites. They demonstrated that character of the friction layer determines the friction performance of the investigated composite material. Structure and chemical composition of the friction layer generated on the friction surface significantly differs from the bulk. Mechano-chemical interaction occurring in the friction process is compared to a non-friction situation where an equivalent apparent temperature and compressive loading, respectively were applied to the same material. No simple relationship exists between composition of the friction layer and bulk material formulation. Phase stability and kinetics of interactions for friction and equivalent non-friction loading conditions differ significantly. [14], worked on the development of fly- ash based automotive brake linings. They developed friction composite using fly ash obtained from a specific power plant in Illinois. Additives such as phenolic resin, aramid pulp, glass fiber, potassium titanate, graphite aluminum fiber and copper powder were used in the composite development phase in addition to fly ash. The developed brake lining composites exhibited consistent coefficient of friction in the range of 0.35
-
and wear rates lower than 12 wt.%.
-
-
METHODOLOGY
-
Material
The materials used during the course of this work are: Epoxy resin, palm kernel fiber (PFF), Aluminum oxides, Iron Oxide, Silica, Graphite, Metal chips (Iron filings).
Table 1: the categories of the brake pad material.
S/N
Brake pad material
Material choice
1
Binder Matrix
Epoxy Resin
2
Reinforcement
Aluminum oxide and iron filings
3
Filler
Palm Fruit Fiber
4
Abrasive
Iron Oxides and Silica
5
Friction modifiers
Graphite
-
Palm Fruit Fiber Design Formulation
To develop an optimal mix for the sample, a split-plot optimal (custom) design which is a specialized form of the surface response method (RSM) was employed. three product attributes are measured as responses from the designed experiment and they are
-
Response 1: The Hardness (BHN)
-
Response 2: Compressive Strength (MPa)
-
Response 3: Wear Rate (J/m3)
Two primary components which are the PFF and Epoxy vary as shown:
10% A (Epoxy) 20%
30% B (PFF) 40%
These components represent a total of sixteen (50) weight- percent of the total formulation, that is: A + B = 50wt%.
Two grain/sieve sizes of 300 microns and 600 microns were also considered as one of the factors.
Other materials are kept constant throughout, making up the remaining 50wt% as shown in table 2 below
S/N
Grain Size (µm)
Epoxy (%)
PFF (%)
Iron oxide (%)
Silica (%)
Iron filings (%)
Alumina (%)
Graphite (%)
A
300
40
10
10
10
5
15
10
B
600
40
10
10
10
5
15
10
C
300
35
15
10
10
5
15
10
D
600
35
15
10
10
5
15
10
E
300
30
20
10
10
5
15
10
F
600
30
20
10
10
5
15
10
S/N
Grain Size (µm)
Epoxy (%)
PFF (%)
Iron oxide (%)
Silica (%)
Iron filings (%)
Alumina (%)
Graphite (%)
A
300
40
10
10
10
5
15
10
B
600
40
10
10
10
5
15
10
C
300
35
15
10
10
5
15
10
D
600
35
15
10
10
5
15
10
E
300
30
20
10
10
5
15
10
F
600
30
20
10
10
5
15
10
Table 2: Compositions of the brake pad material
-
-
Sample Preparation Procedures
For the purpose of this work, a total of six (6) samples designated with the sample ID as shown in Table 2 are to be prepared. The procedures for preparing these compositions are as follows;
-
Mechanical Tests of Sample
Hardness
The hardness test was carried out in accordance with ASTM A956 standards. In this dynamic test method, the ratio of rebound velocity to impact velocity of a moving impact body is used to determine the hardness.
Compressive Strength
This was done using a universal testing machine in accordance with ASTM D3410. The sample was locked securely in the grips of the upper and loer crossbeams of the testing machine. A small load was initially applied to seat the sample in the grips and then the load was increased until failure occurred.
Wear Rate
Wear measurement was carried out to determine the number of materials removed (or worn away) after a wear test Sample to be measured is carefully cleaned, and the weight is measured before and after a wear test. The difference in weight before and after test represents the weight loss caused by wear.
Palm Fruit Fiber (PFFs) Preparation
Palm Fruit fibers (PFFs) were collected from local palm oil
=
Coefficient of friction
. (1)
mill at Enugu. The fibers were suspended in a solution of caustic soda (sodium hydroxide) for twenty- four hours to remove the remnant of red oil left after extraction. The fibers were then washed with water to remove the caustic soda and sun dried for one week. The dried PFFs was grounded into powder form using a Double grinding mill.
Sample Formulation
Each of the powdered constituents were weighed and poured in a container. The contents were manually but thoroughly mixed for 15 to 20 minutes to obtain homogenous mixture. Then, desired amounts of epoxy resin were poured into a separate container and the required quantity of hardener was added to form the matrix. The quantity of epoxy resin was added in the ratio of 2:1. The mixture was thoroughly stirred for about 5 minutes to obtain uniform mixture. Thereafter, the matrix mixture was poured onto the powdered friction material mixture and stirred further to obtain paste-like homogenous mixture. The formed paste was poured into mold cavities that already had powdered talc applied for ease of component removal, the mixture was thereafter pressed with a hydraulic pressing machine at 100kN force for 2 minutes at room temperature and allowed to cure for 90 minutes and thereafter hardened by putting them under controlled temperature of 150oC for 3hours in an oven to ensure a complete curing of the resin.
The coefficient of friction between the linings and steel was determined using a steel inclined plane. The plane was kept at 180° (horizontal position). Each sample was attached to a string and placed on the plane. The string was passed through a pulley, which was connected to a mass hanger. Standard masses were added to the mass hanger until the lining began to slide along the surface of the steel plane. The coefficient of friction is the ratio of frictional force (equivalent to mass at hanger to initiate sliding) to the normal reaction (weight of break lining). Equation (3.2) was used to calculate the coefficient of friction (µ) between the linings and steel.
(2)
where Fr = friction force (N), Fn = normal reaction (N).
-
Response Surface Methodology (RSM)
The design expert 11.0 software was used to apply response surface methodology (RSM). The central composite design (CCD) of RSM was used to obtain the second order regression polynomial that optimizes the mechanical properties response of PFF. RSM tries to fit a polynomial function (Equation 3) to data.
= 0 + 11 + 22 + 312 + 42 + 52 (3)
1 2
Figure 1: Brake Pad made from PFF
-
-
RESULTS AND DISCUSSION
Coefficients in Terms of Coded Factors
The coefficient estimate represents the expected change in response per unit change in factor value when all remaining factors are held constant. The intercept in an orthogonal design
is the overall average response of all the runs. The coefficients are adjustments around that average based on the factor settings. When the factors are orthogonal the VIFs are 1; VIFs greater than 1 indicate multi-collinearity, the higher the VIF the more severe the correlation of factors. As a rough rule, VIFs less than 10 are tolerable.
Hardness = +97.00 2.75A 1.50C 1.75AB + 0.75AC
Compressive Strength = +134.86 22.50A 12.84C + 16.20AB 9.17AC
Wear Rate = +3.91 + 0.0425A + 0.0117C + 0.6425AB 0.0225AC
-
Predicted and Actual Results for the three (3) Responses
Hardness
Optimization conducted on experimental design table as shown in Fig. 2 shows the graphical representation of the predicted and actual values of the experiment. Predicted value was 96.99 while actual was obtained as 99HRB showing high similarity for the predicted and actual values for the hardness experiment.
Figure 2: Predicted and actual values for the Hardness
Compressive Strength
Figure 3 shows the graphical representation of the predicted and actual values of the Compressive strength experiment. Again, the graph confirms a high similarity for the predicted and actual values for the wear rate experiment.
Figure 3: Predicted and actual values for the Compressive Strength
Wear rate
Fig. 4 shows the graphical representation of the predicted and actual values of the wear rate value from the experiment. Again, the graph confirms a high similarity for the predicted and actual values for the wear rate experiment.
Figure 4: Predicted and actual values for the Wear rate
-
Analysis of Variance
Analysis of variance (ANOVA) is a collection of statistical models and their associated estimation procedures used to analyze the differences among group means in a sample. This method was utilized to predict if there is any significant difference in the mean of the experiment. ANOVA for the responses are shown in Tables 3, 4 and 5 respectively.
Table 3: ANOVA for Response 1: Hardness
Term df
Error df
F-
value
P-
value
Whole-plot
1
Grain Size
1
Subplot
3
1.38
28.91
0.0775
not significant
A-PFF
1
1.00
40.33
0.0994
B-Binder (Epoxy & Hardener)
0
AB
1
1.42
5.44
0.1944
Ac
1
1.00
3.00
0.3333
Bc
0
A²
0
B²
0
Table 4: ANOVA for Response 2: Compressive Strength
Source
Term df
Error df
F-
value
P-value
Whole-plot
1
Grain Size
1
Subplot
3
1.01
292.35
0.0423
significant
A-PFF
1
1.00
651.06
0.0249
B-Binder (Epoxy & Hardener)
0
AB
1
1.01
112.44
0.0590
Ac
1
1.00
108.06
0.0611
Bc
0
A²
0
B²
0
Source
Term df
Error df
F-
value
P-
value
Whole-plot
1
Grain Size
1
Subplot
3
1.00
42.32
0.1124
not significant
A-PFF
1
1.00
1.64
0.4222
B-Binder (Epoxy & Hardener)
0
AB
1
1.02
124.86
0.0544
Ac
1
1.00
0.4594
0.6208
Bc
0
A²
0
B²
0
Source
Term df
Error df
F-
value
P-
value
Whole-plot
1
Grain Size
1
Subplot
3
1.00
42.32
0.1124
not significant
A-PFF
1
1.00
1.64
0.4222
B-Binder (Epoxy & Hardener)
0
AB
1
1.02
124.86
0.0544
Ac
1
1.00
0.4594
0.6208
Bc
0
A²
0
B²
0
Table 5: ANOVA for Response 3: Wear rate
-
Interaction of the Factors on the Response
From the result generated showing the contour diagram of relationship between three variables, i.e., Palm Fruit Fiber (A) and Binder (Epoxy Resin) (B), to the Hardness Value of the samples developed for the brake pad (Figure 5), it can be inferred that the value of the correlation coefficient (r) is about
0.57 for A while it is 0.53 at B. This shows that PFF contribute more in terms of wear resistance for the material developed. Figure 5 shows the 3D surface plot of relationship between three variables to the Wear rate of the Samples developed of the brake pad.
Figure 5: 3D surface plot of relationship between three variables to the Wear rate of the Samples developed of the brake pad.
Again, from the result generated showing the contour diagram of relationship between three variables, i.e., Palm Fruit Fiber
-
and Binder (Epoxy Resin) (B), to the Hardness Value of the samples developed for the brake pad (Figure 6), it can be inferred that the value of the correlation coefficient (r) is about
0.78 for A while it is 0.49 at B. This shows that PFF contribute more in terms of wear resistance for the material developed. Figure 6 shows the 3D surface plot of relationship between three variables to the Compressive Strength of the Samples developed of the brake pad.
Figure 6: 3D surface plot of relationship between three variables to the Compressive Strengh of the Samples developed of the brake pad.
Again, from the result generated showing the contour diagram of relationship between two variables, i.e., Palm Fruit Fiber
(A) and Binder (Epoxy Resin) (B), to the Hardness Value of the samples developed for the brake pad (Figure 7), it can be inferred that the value of the correlation coefficient (r) is about
0.29 for A while it is 0.80 at B. This shows that Binder (i.e., Epoxy Resin) contribute more in terms of Hardness value for the material developed. Figure 7 shows the 3D surface plot of relationship between three variables to the Hardness Value of the Samples developed of the brake pad.
Figure 7: 3D surface plot of relationship between three variables to the Hardness Value of the Samples developed of the brake pad.
V. CONCLUSION
A non-asbestos brake pad material using palm fruit Fiber as base material was developed. Various mechanical Tests were conducted on the produced samples and their results analyzed. The results related how the samples performed during testing. The following were deduced from this study:
-
The Hardness values result showed that the Hardness values of the samples which ranges from 94HRB to 104HRB are in close proximity with the commercial brake pad.
-
The compressive Strength varies from 74.66MPa to 148MPa, with Sample B having the least strength, while
sample C has the highest compressive strength. The wear results range from 3.21mg/m to 3.96mg/m which conforms with that of commercial brake pad (3.8mg/m).
-
The optimal sample for the brake pad material is sample F (30wt% of PFF, 600µm) which is the closest to the predicted value.
-
The best particle size of Palm Fruit fiber for brake pad production is 600µm.
-
The pad samples were thermally stable with no loss in weight up to 2500C to 5500C
-
The relationship between the formulated Palm Fruit Fiber (PFF) brake pad and commercial brake pad has a correlation coefficient R = 0.80.
ACKNOWLEDGMENT
We specially acknowledge Scientific Equipment Development Institute, Akwuke, Enugu State and NUTABOLTS Technologies LTD, Enugu for the technical assistance they offered which was a key factor in the success of this project..
REFERENCES
-
Adebisi, A. A., Maleque, M. A. & Shah, Q. H. (2011). Surface temperature distribution in a composite brake rotor, International Journal of Mechanical and Materials Engineering 6 (3): 356-361.
-
Aigbodion, V.S., Akadike, U., Hassan, S.B., Asuke, F., Agunsoye, J.O. (2010). Development of Asbestos – Free Brake Pad Using Bagasse. Tribology in industry, Volume 32, No. 1, pp 12-18.
-
Akramifard, H.R. and Ghasemi, Z. (2016). Friction and Wear Properties of a New Semi-Metallic Brake Pad According to SAE J 661: A Case Study in PARSLENT Complex (Iran). International Journal of New Technology and Research (IJNTR), Volume-2, Issue-3, Pages 96-99.
-
Bashar, D.A., Peter, B.M., and Joseph, M. (2012). Material Selection and Production of a Cold-Worked Composite Brake Pad. World J of Engineering and Pure and Applied Sci. 2(3):92
-
Blau, P.J. (2001). Compositions, Functions, and Testing of Friction Brake Materials and Their Additives. Tennessee: Oak Ridge National Laboratory.
-
Dagwa, I.M. and Ibhadode, A.O.A. (2005). Design and Manufacture of Experimental Brake Pad Test Rig. Nigerian Journal of Engineering Research and Development, Basade Publishing Press Ondo, Nigeria,
Vol. 4, No. 3. 15-24
-
Elzey, D.M, Vancheeswaran, R, Myers, SW, McLellan, RG, (2000), The intelligent selection of materials for brake Lining. Proceedings of the 18th Annual brake Colloquium & Engineering Display, P-358: pp, 181- 192.
-
Filip, P., Weiss, Z., & Rafaja, D. (2002). On friction layer formation in polymer matrix composite materials for brake applications. Wear, 252(3- 4), 189-198.
-
Gachoki, J. J. and Kathenya, M. D. (2011). Design of brake pad friction material. Final year project. Department of Mechanical and Manufacturing Engineering. University of Nairobi.
-
Jaafar TR, Selamat MS, Kasiran R, (2012). Selection of best formulation for semi-metallic brake friction materials development. J. Powder Metall., 1-30.
-
Kim, S. J., & Jang, H. (2000). Friction and wear of friction materials containing two different phenolic resins reinforced with aramid pulp. Tribology international, 33(7), 477-484.
-
Kumar k. & Bijwe, J. (2010), NAO friction materials with various metal powders: tribologcal evaluation on full-scale inertia dynamometer, Wear, vol. 269, no. 11-12, pp. 826837.
-
Leman Z., Sapuan, S.M. Saifol, A.M. Maleque M.A. and Ahmad, M.M. (2008 Moisture absorption behaviour of sugar palm fibre reinforced epoxy composites Short Communication, International Journal of Materials and Design 29 (8): 1666-1670.
-
Mohanty, S., & Chugh, Y. P. (2007). Development of fly ash-based automotive brake lining. Tribology International, 40(7), 1217-1224.
-
Nicholson, G. (1995). Facts about Friction. Croydon, PA: P&W Price Enterprises
-
Vijay, R., Janesh, M.J., Sai Balaji, M.A and Thiyagarajanm V. (2013). Optimization of Tribological Properties of Non asbestos Brake Pad Material by Using Steel Wool. Advances in Tribology, volume 2013, pp 1-9.
-
Wannik et al., 2012; Wannik, W.B., Ayob, A.F., Syahrullail, S., Masjuki, H.H., Ahmad, M.F., 2012. The effect of boron friction modifier on the performance of brake pads. Int. J. Mech. Mater. Eng. 7, 31