
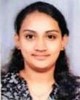
- Open Access
- Authors : Varsha J S , Sanjana R , Priyanka J , Manasa M, Dr. Sandeep R
- Paper ID : IJERTV10IS070174
- Volume & Issue : Volume 10, Issue 07 (July 2021)
- Published (First Online): 09-08-2021
- ISSN (Online) : 2278-0181
- Publisher Name : IJERT
- License:
This work is licensed under a Creative Commons Attribution 4.0 International License
Automated Waste Sorter with Robotic ARM using Arduino UNO
1Varsha J S
Student
Department of Electronics and Communication Eng.
VVCE, Mysore, India
2Priyanka J
Student
Department of Electronics and Communication Eng.
VVCE, Mysore, India
3Sanjana R
Student
Department of Electronics and Communication Eng.
VVCE, Mysore, India
4Manasa M
Student
Department of Electronics and Communication Eng.
VVCE, Mysore, India
5Dr. Sandeep R
Associate Professor
Department of Electronics and Communication Eng.
VVCE, Mysore, India
Abstract Due to population explosion and urbanization, annual waste generation is forecasted to increase by 70%. Current waste management systems are unable to cope with the volumes of waste generation. Intending to maximize waste segregation and recycling and minimize human interference, we propose a model, an automated waste sorter system that is implemented to segregate the waste into various categories like dry, wet, and metallic waste.
Keywords Conveyer belt, robotic arm, sensors, recycling, segregation, arduino, unhealthy atmosphere, waste management.
-
INTRODUCTION
Waste management is collection, segregation, recycling, and safely disposing the waste. In India, around 65 million tons of wastes are generated annually, and over 90 percent of them are Municipal Solid Waste that includes organic waste, recyclables like paper, plastic, wood, glass, etc. In that, 75- 80% of the waste gets collected and 22- 28% is processed and treated (web source). Therefore, waste segregation is the primal step in the waste management system and needs to be carried out efficiently to reduce the wastes at the source itself. Many people are unaware or negligent while disposing of the wastes by ignoring the labels marked on the appointed bins. In India, segregation and recycling processes are done manually which increases human interference.
-
LITERATURE SURVEY
In [1], the system implements waste segregation using a robot that picks up the waste from the conveyor belt. The waste is segregated into dry, wet, and metallic. Metal proximity, moisture and limit switch are the sensors employed. ARM is used to drop the waste into the designated bin. The location of
the bin is sent using a GSM module to the concerned authority once the bin is full. The conveyor belt used in this model is not portable and has very limited scope. Best applicable for small scale use.
In [2], the system segregates paper, glass, and metallic waste using an Automated Waste Sorter (AWS) and a Robotic Arm. To minimize human interference, the robotic system and collects the waste and is later sorter by the AWS. An array of sensors is used in company with the robotic arm to structure an automated waste sorter. To mechanically pick up the waste, a Mobile Robot Delivery System is employed to sort the waste and put it in their designated bin.
In [3], three pulleys are employed which runs with the help of a DC motor on a conveyor belt. Sensor system segregates the wastes using image processing. An actuator responds quickly using sensor system to segregate the waste. Classifier techniques segregates them into dry, wet, and metallic. The model can be used in both domestic and industrial level.
In [4], a municipal waste segregator is built using an Arduino Mega board. This system consists of three compartments, the first compartment is used to detect metal wastes, the second compartment detects if the waste is either wet or dry and the third compartment is the storage compartment which is further subdivided into three compartments as dry, wet, and metallic for storage purpose. Also, a NodeMCU is used to get feedback regarding the status of the bins and also used to send the information to the respective authorities.
In [5], A waste sorting system which uses the advancement of the information technology has been built.The main objective of this system is to differentiate wastes as organic, recyclable, and non-recyclable. Wastes are picked up and dumped onto a conveyer belt using a robotic arm controlled by a mobile application. A rotating surface is placed at the end of the conveyer belt to collect the segregated wastes. A database is developed to keep track of the number and type of wastes collected and is also saved in text format.
In [6], system is built to manage the wastes automatically using a programmable logic controller. Initially, the wastes are crushed using a crusher controlled by a separate system. These crushed wastes are further dumped onto a conveyer belt through a funnel-shaped structure. The wastes are identified as either dry or wet based on the output of the sensors that are placed along the conveyer belt. Thus identified wastes are pushed into the respective bins using hydraulic cylinders placed under them. The dust and other small particles are blown by fixing a high-speed fan in-front of the collecting chamber.
In [7], an ultrasonic sensor and metal sensor are used to separate the metal from the dustbin. An ultrasonic sensor is used to detect the existence of any metal or other waste. Based on the specific commands given by the metal sensor system is going to open the door properly. The inlet section consists of open and closed methods to control the waste that flows on the conveyor belt to detect when the metallic waste inductive detector sensor is used. The signal from the detector is to start and force a detector to throw out the metal waste. For the segregation process Conveyor belt is used. The door will open and close depending on the input from the metal detector and ultrasonic sensor.
In [8], the main aim is to detect the waste in the dustbin using sensor devices. Once the waste is detected, it will be segregated at the same time data is sent to the IOT and Cloud. Microcontroller is used on either side of the sensors and IOT module. Ultrasonic sensors are used to detect the near products of waste material. To examine and update the status of moisture present in the waste is detected by a moisture sensor, suppose there is a possibility of moisture present in the waste. Then the waste cannot be thrown into the dustbin. Image processing algorithm is used to identify the plastics and degradable products separated to other section bins. The dustbin data are uploaded to the cloud in real time.
In [9], the main aim is to separate the waste into four types: wet, metal, solid, glass waste. Arduino Uno is used as the main controller, inductive proximity sensor is to identify wet objects, and photoelectric sensor is to identify solid. Robotic arm is to segregate different types of waste dumped together. The stepper motor is controlled by the stepper motor drive. Once the waste is detected stepper motor rotates by the respective angle is set for each type of waste. This way the bin corresponding to the type of waste is placed in the dustbin. The bin will move back to the initial place once the waste falls into the respective bins and the bin closes.
In [10], this paper studies the workers find the bins to be overflowing and other times the bins aren't even filled to the brim. This causes one of the most reasons for inefficiency in proper collection of waste and is additionally harmful for the environment. Hence a smart bin is developed. The sensors present in it which screens what proportion waste has been amassed and consequently makes the waste compact. It detects what proportion waste is inside the compartment and remotely transmits fill level data to cloud server. This results in productive utilization of sometime an keeps the roads more hygienic.
In [11], the system starts its activation when the IR detects some sort of waste is being kept on the system tray. Then initially the weight sensor starts its work and find out the weight of the trash, then the metal sensor and other sensor starts their action. If metal sensor detects the waste as metal, then a servomotor will keep the trash in the bin3 using robotic arm. An automatic waste sorter model consists three bins. Each bin is used for unlike materials like dry, wet and metal, bin1 is for dry, bin2 is for wet and bin3 is for metallic elements. At first the waste is placed .The sensor applies its sensing activity to detect the material. Sensing signal is send to microcontroller and final output comes out from microcontroller given to the servo motor to a definite direction depending on the material that is being sensed.
In [12], ROBOT is mount using DC Motors and Motor Drivers. The ROBOT will segregate the waste and the sensor sense the presence of waste using IR Sensors this technique provides a robotic solution for Garbage segregation. A pick and Place mechanism is employed for separation. Use of sensors like Moisture and Proximity for waste separation like wet, dry and metallic etc. This checks the waste level over the dustbins by using Sensor. Once it detected immediately this technique aware of concern authority through GSM
TABLE I. Comparison with existing methods
The above Comparison table gives a clear comparison between the methods referred and proposed method.
Parameters
Existing Methods
Proposed Method
Technology
[1],[2], [9],[10] Android app [3],[4] Arduino Mega board
[7], [9] Arduino [8],[11],[12]-Microcontroller
a)Arduino uno is used b)Smart dustbin
monitors the status of the primary bin
c)waste sorter system with robotic arm is used to segregate the wastes
Segments
Wastes are segregated into three categories: a)dry ,
b)wet and
c) metal
Sensors
[1]Moisture, metal proximity. [2],[3]Array of sensor. [7]ultrasonic, metal. [2]ultrasonic, metal, moisture. [9]proximity, photo electric. [11] IR, weight, metal. [2]IR,moisture, proximity. [4][5],[6],[10] No sensors used. IRsensor,
Nickel coated sensor
Compatabili-ty
The above methods occupy large space and it is complex in nature.
a)Area occupied is less b)User friendly
c)Cost effective
-
Android app
-
PLC
-
Dry, wet, metal.
-
paper, glass, metal.
-
glass, metal, dry.
-
Dry, wet, metal. [5]organic, recyclable,non- recyclable.
-
Dry, wet.
-
metal
-
plastic, degradable.
-
wet, metal, solid and glass.
-
Dry, wet, metal.
-
wet, dry and metallic.
-
-
PROPOSED METHODOLOGY
After detailed study about smart dustbin, robotic arm, technology and other components required for this protocol to be developed are identified. This paper aims to create protocol that specifies how a waste sorter system can share their sensor data and use information to collaboratively optimize the segregation of wastes and also helps the recycling process.
Fig. 1. Block diagram of Automated waste sorter system
Figure 1 can be explained as follows:
-
The whole system is controlled by Arduino Uno based on ATmega328P which can be programmed using Arduino IDE software.
-
IR sensor is used to measure the distance between the dustbin lid and the wastes dumped in order to check whether the dustbin is full or not.
-
Global system for mobile communication (GSM) module is used to establish communication with mobile device.
-
General positioning system (GPS) module is uses the data received by the satellite to calculate the position at which the object (here dustbin) is located.
-
A robotic arm is built with the help of three servo motors, which helps for movement for segregating the waste.
-
The robotic arm consists of nickel coated sensor which segregate the dry wet and metallic waste based on conductivity of electricity and their potential difference.
-
Thus, segregated wastes are dumped into different compartments of the dustbin.
-
-
CONCLUSION
In communities where appropriate sites are available, sanitary landfills usually provide the most economical option for disposal of solid waste. But, it is becoming increasingly difficult to find the sites that offer adequate capacity, accessibility and environment conditions. This project reports on Wastes segregation using robotic arm, the robotic arm will ready to map out the three different materials like dry, wet and metals. When the sensors are triggered the motor- powered arm is actuated and therefore the materials are dispensed onto its proper bins. The Trash management system may be a breakthrough to form the manual collection and detection of wastes automated in nature.
-
FUTURE SCOPE
The robotic arm is very limited when it comes to carrying the waste which are more in weight. Since the waste are given to the robotic arm for segregation, it may be time consuming. Mixed waste cannot be classified efficiently. The segregation between dry and wet waste may not be accurate, whenever
the dry waste accidently gets wet the sensor might not sort it efficiently. This system is only for small-scale application.
REFERENCES
-
Dr. Sumalya MN, Dr. Kavitha GR, Smart Robotic Arm Based Waste Segregation System, International Journal Science, Engineering and Management (IJSEM), 2020.
-
V.V.Joshi, Rohan Ghugikar, Bhagavat Bhise, Pradip Bhawar, Shivam Kakade, Waste Segregation Using Smart Robotic Arm, International Research Journal of Engineering and Technology (IRJET), May- 2017.
-
S. Lokesh, S. Kiran, B. Vijay, S. B. Yuvaraaj, S.Yuvaraj, Waste Segregation Management Using Object Sorting Robot, International Journal of Engineering & Technology (IJET), 2018.
-
T.Saminathan, Akash Musipatla, P.Manideep Varma , P. Shahid Khan, G.Mahesh Kumar "IoT based Automated Waste Segregator for Efficient Recycling", International Journal of Innovative Technology and Exploring Engineering(IJTEE),2019
-
Sadia Zahin Diya, Rifat Ara Proma,Muhammad Nazrul Islam, Tasmiah Tamzid Anannya, Abdullah Al Mamun, Rizvi Arefeen, Saifullah Al Mamun, Ihtiaz Ishmam Rahman, Md Fazle Rabbi, "Developing an Intelligent Waste Sorting System with Robotic Arm
: A Step towards Green Environment", International Conference on Innovation in Engineering and Technology (ICIET) 27-29 December, 2018
-
Rashmi M. Kittali and Ashok Sutagundar, "Automation of Waste Segregation System using PLC", International Journal on Emerging Technologies (Special Issue on ICRIET-2016).
-
G. Aahash, V. Ajay Prasath, D. Gopinath, M. Gunasekaran "Automatic Waste Segregator using Arduino",International Journal of Engineering Research & Technology (IJERT),Special Issue – 2018
-
Bhoomika P M, Sonika V, Suma B S, Vismitha S S, Mrs. Sangeetha V, "SEGREGATION OF WASTE-A SURVEY",International Research Journal of Engineering and Technology (IRJET), Volume: 07 Issue: 02 Feb 2020.
-
M. Rajeswari,Mandara B. L, Meghana.M. V, Meghana G, Vaishnavi.C "Automatic Waste Segregator", International Journal of Latest Engineering Research and Applications (IJLERA),Volume 04, Issue 06, June 2019.
-
Cherry Agarwal,Bhavesh Yewale, Chaithali Jagadish, "Automatic Waste Segregation and Management", International Journal of Engineerin Research & Technology (IJERT), Vol. 9 Issue 06, June- 2020.
-
Mahmudul Hasan Russel, Mehdi Hasan Chowdhury, Md. Shekh Naim Uddin,Ashif Newaz, Md. Mehdi Masud Talukder, "Development of Automatic Smart Waste Sorter Machine", International Conference on Mechanical, Industrial and Materials Engineering 2013 (ICMIME2013).
-
Santhosh Kumar B R, Rohit K , Varalakshmi N ,Manjunath,Sahana D N, "Eco-Friendly IOT Based Waste Segregation and Management", International Conference on Electrical, Electronics, Communication, Computer and Optimization Techniques (ICEECCOT) ,2017.