
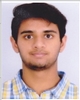
- Open Access
- Authors : Raihan Mohammed R , Kiran Teradal , Mukul Karwa , Nikhil N Kumar
- Paper ID : IJERTV10IS080044
- Volume & Issue : Volume 10, Issue 08 (August 2021)
- Published (First Online): 14-08-2021
- ISSN (Online) : 2278-0181
- Publisher Name : IJERT
- License:
This work is licensed under a Creative Commons Attribution 4.0 International License
Design and Simulation of MEMS based Capacitive Accelerometers for Crash Detection and Airbag Deployment in Automobile
Mr. Kiran Teradal, Mr. Mukul Karwa, Mr. Nikhil N Kumar, Mr. Raihan Mohammed R
PES Institute of Technology, Hosur Road, Bangalore 560100
Abstract:- This paper focuses on design and analysis of MEMS based accelerometer to detect accidents and for the deployment of airbags. In the case of a car accident, where there are sudden and strong accelerations, it is necessary to measure as fast as possible their intensity and direction with good accuracy and precision, aiming to reduce the injuries severity to passengers. With the continuous advancements in Micro Electro Mechanical Systems (MEMS) fabrication technology, inertial sensors like accelerometers and gyroscopes can be designed and manufactured with smaller footprint and lower power consumption. Capacitive accelerometers are the most popular and highly researched due to several advantages like high sensitivity, low noise, low temperature sensitivity, linearity, and small footprint. When sudden displacement occurs due to impact the comb gets shock loads or forces and that movement is observed by differential capacitance concept with dielectric as air. The simulations will be carried out on COMSOL while the design will be carried out on COMSOL, the actual theoretical calculation and the simulations are compared in order to get accurate results. The capacitance output obtained is carried to the electronic control unit which sends the impulse signal to air bag system and deployment of air bags takes place.
INTRODUCTION:
Automotive is one of the most emerging area since ages and is constantly under developments. These developments in technology and these advancements are not without responsibilities to assure that the end user is safe and satisfied. The industries primary concerns are improving the performance, safety, and comfort aspects which have become evident over the years with introduction of highly improved standards with every iteration. Passenger safety is a field highly researched on to ensure the survival of a passenger in a car crash. This brings us to the crash detection and air bag deployment systems in the automotive industry. Frontal airbags drastically reduce harm to driver in frontal crashes by almost 30 percent and fatalities of front-seat passengers of age 13 and older by 32 percent (Survey from 2015). NHTSA estimates that as of 2015, a total of 44,869 lives have been saved primarily by frontal airbags (Survey 2017). At the instant of a crash, sensors start to measure severance of the impact. When the crash occurs beyond a set intensity, the sensors signal control unit to inflate the bags with gas within fractions of a second. The reference work analyzes a capacitive accelerometer capable of identifying positive and negative levels of acceleration along three perpendicular directions. However, this project
is referred to a sensor capable of working with accelerations on an XY plane, on which it was built starting from a planar geometry. To understand this type of sensor the technological process with which modern semiconductor integrated circuits are manufactured is extensively used, thanks to which MEMS sensors are able to have dimensions in the order of nano meters. In case of a car accident, it is of utmost requirement that the airbag system reacts as fast as possible from the moment of the impact, in order to avoid fatal injuries. For this reason, it is necessary that the system analyses and give a response within the shortest possible time. The capacitive sensors are basically based on a moving solid body with a certain mass that will move when subjected to acceleration. The movement of the mass is the most important factor, because the small displacements of the structure leads (fingers and proof mass) to a variation of a capacity, as there are parts, called "fingers" that move closer or farther away depending on the direction of acceleration. These displacements are a direct effect of the acceleration on the system. When the capacity produced reaches a certain threshold value, it means that we are in a limit condition in the case under consideration; therefore, the system will react appropriately.
SYSTEM DETAILS
-
Proof mass: A proof mass or test mass is a known quantity of mass used in a measuring instrument as a reference for the measurement of an unknown quantity. A proof mass that deforms a spring in an accelerometer is sometimes called the seismic mass. This proof mass will have fingers attached to it on either side.
-
Spring: Thin beams placed in rectangular manner act as springs in the system. It facilitates movement to the proof mass, which in turn moves the fingers. The stiffness of these springs is the key parameter for displacement.
-
Fingers: Attached to the proof mass, these components are responsible to obtain differential capacitance. They are placed in between di-electric plates, such that a finger-gap and an anti- finger gap exists between them.
-
Connecting beams: these are used to connect the proof mass to the springs. 4 connecting beams are used with 2 for each spring.
-
Di-electric medium: Air is taken as the di-electric
medium.
-
Anchors: A 100nm square cross section fixed joint, to which the springs are attached.
Density: 2320kg/m3
Fig .1.2.1 Parts of capacitive accelerometer Wa= Width of anchor
W= Width of connecting beam
lf= Length of fingers= Length of static plate l1=l2= Length of spring on either side
lb= Length of connecting beam
-
Material of component: Polysilicon is chosen as the material of design with following properties:
Working of the System with Key Parameters
It is based on the movement of a proof mass to which are attached mobile fingers whose movement makes a change in capacity, that is calculated between them and the fixed fingers. From the displacement it can be traced back the acceleration value and the capacitive system is used to calculate it.
The instantaneous change in velocity (acceleration) on impact is converted into force on the system by Newtons laws of motion. This force is then responsible for the proof mass to move, which results in the movement of the fingers. A differential capacitance is set up at the gaps between the fingers and the di- electric plates. This capacitance produces a voltage which is transferred to the electronic control unit of the vehicle and if it is within the acceptable range causes the airbag to deploy.
The system can be depicted by a spring-mass-damper setup.
A force F, generated by external acceleration acting on the mass, m, causes a displacement x. The differential equation describing the system response is given by equation:
()=2/2+/+
b is the damping coefficient and K is the spring coefficient, the stiffness.
Displacement
F is both the force that will be induced to the mass of the system by the external acceleration, both the force given by Hookes law that could be
associated to the action of the springs, considering the stationary conditions. K is the springs stiffness
Comparing the equations, displacement x can be given as: x=ma/k (1)
This is the displacement obtained in x-direction for x-axis analysis
The same equation will hold good for y-direction: Displacement y = ma/k. (2)
Capacitance
Capacitance of the system at a single finger between two dielectric plates(electrodes)n is given as
=0 × ×/
0 is the dielectric permeabiliy of the vacuum and is worth 8,85410-12 F/m, r is the dielectric permeability of the material that separates the armatures, in our case it is taken as 1F/m, considering that there will be only air, A is the total overlap surface between the electrodes and d is the gap from the finger. Finger gap-d1 and anti-finger gap d2 are taken in the ratio 1:2 respectively. This is done in order to discriminate the displacements in x and y axes. Thus, capacitance will be:
=oH(1/1+1/2)
-
axis
When acceleration along the x-axis occurs, the capacity between the mobile and fixed fingers varies, because on the right the surface will increase by a factor x, the displacement, which will be added to the overlap length L and on the other side it will decrease, by the same amount.
So, for the two capacities their magnitude is given by:
1=0H (1/1+1/2) (+) ×F
2=0H (1/1+1/2) () ×F
-
axis
When acceleration on the y-axis happens, the variation in capacity depends on the displacement that makes the distances d from the fingers vary. The change in capacity will depend on the displacement along the y-axis and further simplified substituting d1=2×d2
1=0H(1/(1) +1/(2+)) × F = 0H (31/(212+12))
×F
2=0H(1/(1+) +1/(2)) × F =0tH (31/ (21212))
×F
A factor F of 6 is taken when 12 fingers are present in total, with 6 fingers contributing to C1 and equally forC2.
A factor F of 8 is taken when 16 fingers are present in total, with 8 fingers contributing to C1 and equally forC2.
Voltage:
The system is initially given a fixed amount of supply voltage, and once the differential capacitance is obtained, an output voltage signal will be sent to the control unit of the vehicle.
Vout = ((C1-C2)/ (C1+C2)) ×Vs
The following section of the report addresses some of the research work carried out by various researchers in the field of capacitive accelerometers and their extensive utilization for crash detection and airbag deployment. The research papers that were referred to are listed below:
Jesse Kendall, P.E. et.al [1] this paper gives an insight on the airbag deployment criteria and process
D S Dima et.al, 2017[2] this paper provides insight on the crash tests that can help the experts to identify the ranges of accelerations that may appear in various collision types. The correct sensors and data acquisition devices used in crash tests depend by the type of collisions.
Geeta Bhatt et.al, 2019[3] this paper provides insight on the importance of MEMS in the automotive industry along with the various applications in vehicles along with MEMS fabrication.
Vijayakumar S. et.al 2011 [4] this paper depicts the design and analysis of a 2-axis MEMS capacitive accelerometer Divya et.aL, 2015[5] this paper provides insight on analysis of 3-axis accelerometers using COSMOL.
Gaurav Phulwari et.al, 2017[6] This paper provides insight on the importance of MEMS in the automotive industry and how they are cost effective, compact in size and help prevent major catastrophe.
Mourad Benmessaoud, 2013 [7] Optimization with respect to design parameters are done and variation are studied Giulio Puccioni, 2020 [8] this paper provides insight on the performance of a standard capacitor accelerometer at varying accelerations and also provides insight on the effect of variation of thickness of the capacitive accelerometer.
Zakriya Mohammed 2016 [9] this paper optimizes finger spacing and spring constant and simulation is carried out.
Research Gap
The literature of displacement and stress analysis with respect to 2-axis MEMS capacitor accelerometer is scarce and doesnt involve alterations to the accelerometer to improve efficiency. The objective of our project is to design a 2-axis MEMS accelerometer and analyze the displacement and stress along the x and y axis. Certain alterations with respect to the design of the accelerometer are done to study the difference in performance.
-
Objectives To determine the total displacement with respect to acceleration variation(0-100g)
-
To determine the stress on x and y-axis
Theoretical Analysis
-
W = VPM ÷ L×H
M12F =12×M1F
-
M2LB = 2×MLB
M2SB = 2×MSB = 4.64×10-18 Kg
-
M tot = MPM + M12F + V2LB + M2SB
Spring Stiffness K= (4×E×W×H3) / (6× (2L1)3+ (2L2)3)
C1=0H (1/1+1/2) (+x) ×6
C2=0H (1/1+1/2) (x) ×6
1. 1=0H(31/(212+12)) ×6
2. 2=0H(31/ (21212)) ×6
Table 4.1.1 Result for acceleration in x-direction for the standard design
Acceleration m/s2 |
Displacement x (fm) |
C1(*10-17 F) |
C2(*10-17 F) |
0g |
0 |
5.8941 |
5.8941 |
10g |
3.4 |
5.8941 |
5.89405 |
20g |
6.89 |
5.8941 |
5.89405 |
30g |
10.33 |
5.8941 |
5.89405 |
40g |
13.77 |
5.8941 |
5.89405 |
50g |
17.22 |
5.8941 |
5.89405 |
60g |
20.66 |
5.8941 |
5.89405 |
70g |
24.11 |
5.8941 |
5.89405 |
80g |
27.55 |
5.8941 |
5.89405 |
90g |
31 |
5.8941 |
5.89405 |
100g |
34.44 |
5.8941 |
5.89405 |
Displacement in y axis:
Displacement (y-direction) y = (M×10g)/Ky= (1.129×10-16×10×10)/9.74= 1.15 fm
Capacitance produced in y axis:
y-direction for the standard design
Acceleration m/s2 |
Displacement y (fm) |
C1(×10-17 F) |
C2(×10-17 F) |
0g |
0 |
5.896764 |
5.896764 |
10g |
1.32 |
5.896763806 |
5.896764194 |
20g |
2.64 |
5.896763611 |
5.896764389 |
30g |
3.96 |
5.896763413 |
5.896764584 |
40g |
5.29 |
5.89676322 |
5.89676478 |
50g |
6.61 |
5.896763026 |
5.896764974 |
60g |
7.93 |
5.896762831 |
5.896765169 |
70g |
9.25 |
5.896762636 |
5.896765364 |
80g |
10.58 |
5.896762441 |
5.896765559 |
90g |
11.9 |
5.896762246 |
5.896765754 |
100g |
13.22 |
5.896762051 |
5.896765949 |
Table 4.3.1 Result for acceleration in x-direction for thickness (20nm)
Acceleration m/s2 |
Displacement x (fm) |
C1(×10-17 F) |
C2(×10-17 F) |
|
0g |
0 |
2.9483820 |
2.9483820 |
|
10g |
24.02 |
2.9483822 |
2.948381808 |
|
20g |
48.225 |
2.9483824 |
2.948381616 |
|
30g |
72.34 |
2.9483826 |
2.948381424 |
|
40g |
96.50 |
2.9483828 |
2.948381231 |
|
50g |
120.50 |
2.9483830 |
2.948381040 |
|
60g |
144.50 |
2.94838315 |
2.94838085 |
|
70g |
168.8 |
2.94838335 |
2.948380655 |
|
80g |
192.9 |
2.94838354 |
2.948380463 |
|
90g |
217 |
2.94838373 |
2.948380271 |
|
100g |
241.135 |
2.94838392 |
2.948380078 |
Table 4.3.2 Result for acceleration in y-direction for thickness(20nm)
Acceleration m/s2 |
Displacement y (fm) |
C1(×10-17 F) |
C2(×10-17 F) |
0g |
0 |
2.9487 |
2.9487 |
10g |
9.285 |
2.948698229 |
2.948700684 |
20g |
18.57 |
2.948696445 |
2.948701369 |
30g |
27.85 |
2.948694667 |
2.948702053 |
40g |
37.135 |
2.948692886 |
2.948702738 |
50g |
46.42 |
2.948691117 |
2.948703422 |
60g |
55.705 |
2.94868935 |
2.948704106 |
70g |
65 |
2.94868756 |
2.948704792 |
80g |
74.25 |
2.94868578 |
2.948705474 |
90g |
83.65 |
2.94868401 |
2.948706167 |
100g |
92.845 |
2.94868223 |
2.948706844 |
Table 4.3.3 Result for acceleration in x-direction for thickness (80nm)
Acceleration m/s2 |
Displacement x (fm) |
C1(×10-17 F) |
C2(×10-17 F) |
0g |
0 |
11.793528 |
11.793528 |
10g |
0.5363 |
11.79352802 |
11.79352798 |
20g |
1.073 |
11.79352803 |
11.79352797 |
30g |
1.61 |
11.79352805 |
11.79352795 |
40g |
2.145 |
11.79352802 |
11.79352793 |
50g |
2.68 |
11.79352807 |
11.79352791 |
60g |
3.22 |
11.79352810 |
11.79352790 |
70g |
3.75 |
11.79352812 |
11.79352788 |
80g 90g 100g |
4.29 4.82 5.36 |
11.79352814 11.79352815 11.79352817 |
11.79352786 11.79352785 11.79352783 |
Table 4.3.4 Result for acceleration in y-direction for thickness (80nm)
Acceleration m/s2 |
Displacement y (fm) |
C1(*10-17 F) |
C2(*10-17 F) |
0g |
0 |
11.793528 |
11.793528 |
10g |
0.144 |
11.79352796 |
11.79352804 |
20g |
0.289 |
11.79352792 |
11.79352808 |
30g |
0.435 |
11.79352787 |
11.79352813 |
40g |
0.579 |
11.79352783 |
11.79352817 |
50g |
0.724 |
11.7935278 |
11.79352822 |
60g |
0.869 |
11.79352774 |
11.79352826 |
70g |
1.014 |
11.7935277 |
11.79352830 |
80g |
1.159 |
11.79352766 |
11.79352834 |
90g |
1.30 |
11.79352762 |
11.79352838 |
100g |
1.448 |
11.79352757 |
11.79352843 |
Table 4.3.5 Result for acceleration in x-direction for thickness(160nm)
Acceleration m/s2 |
Displacement x (fm) |
C1(×10-17 F) |
C2(×10-17 F) |
0g |
0 |
23.587056 |
23.587056 |
10g |
0.0936 |
23.58705601 |
23.58705599 |
20g |
0.187 |
23.58705601 |
23.58705599 |
30g |
0.281 |
23.58705602 |
23.58705598 |
40g |
0.375 |
23.58705602 |
23.58705598 |
50g |
0.47 |
23.58705603 |
23.58705597 |
60g |
0.562 |
23.58705604 |
23.58705596 |
70g |
0.656 |
23.58705604 |
23.58705596 |
80g |
0.75 |
23.58705605 |
23.58705595 |
90g |
0.843 |
23.58705605 |
23.58705595 |
100g |
0.937 |
23.58705606 |
23.58705594 |
Table 4.3.6 Result for acceleration in y-direction for thickness (160nm)
Acceleration m/s2 |
Displacement y (fm) |
C1(×10-17 F) |
C2(×10-17 F) |
0g |
0 |
23.5875 |
23.5875 |
10g |
0.036 |
23.58749998 |
23.58750002 |
20g |
0.072 |
23.58749996 |
23.58750004 |
30g |
0.108 |
23.58749994 |
23.58750006 |
40g |
0.144 |
23.58749992 |
23.58750008 |
50g |
0.180 |
23.58749989 |
23.58750011 |
60g |
0.216 |
23.58749987 |
23.58750013 |
70g |
0.252 |
23.58749985 |
23.58750015 |
80g |
0.288 |
23.58749983 |
23.58750017 |
90g |
0.324 |
23.58749981 |
23.58750019 |
100g |
0.360 |
23.58749979 |
23.58750021 |
4.4 Additional Fingers and Reduction of Di-electric Gap
Table 4.4.1 Displacement for acceleration in x-direction for additional finger and reduced gap
Acceleration (m/s2) |
Displacement (fm) |
0g |
0 |
10g |
3.5637 |
20g |
7.1274 |
30g |
10.691 |
40g |
14.254 |
50g |
17.818 |
60g |
21.382 |
70g |
24.946 |
80g |
28.509 |
90g |
32.0736 |
100g |
35.637 |
Table4.4.2 Displacement for acceleration in y-direction for additional finger and reduced gap
Acceleration(m/s2) |
Displacement (fm) |
0g |
0 |
10g |
1.368 |
20g |
2.736 |
30g |
4.105 |
40g |
5.473 |
50g |
6.842 |
60g |
8.210 |
70g |
9.578 |
80g |
10.94 |
90g |
12.31 |
100g |
13.68 |
Table 4.4.3 Capacitance for acceleration in x-direction for additional finger and reduced gap
Acceleration (m/s2) |
C1 (× 10-18 F) |
C2(× 10-18 F) |
0 |
1.5724704 |
1.5724704 |
10 |
1.572470415 |
1.572470438 |
20 |
1.572470430 |
1.572470437 |
30 |
1.572470445 |
1.572470435 |
40 |
1.572470461 |
1.572470434 |
50 |
1.572470476 |
1.572470432 |
60 |
1.572470491 |
1.572470431 |
70 |
1.572470506 |
1.572470429 |
80 |
1.572470521 |
1.572470428 |
90 |
1.572470536 |
1.572470426 |
100 |
1.572470551 |
1.572470425 |
Table 4.4.4 Capacitance for acceleration in y-direction for additional finger and reduced gap
Acceleration (m/s2) |
C1 (× 10-18 F) |
C2(× 10-18 F) |
0 |
1.5724704 |
1.5724704 |
10 |
1.5724702 |
1.5724705 |
20 |
1.5724701 |
1.5724706 |
30 |
1.5724700 |
1.5724707 |
40 |
1.5724699 |
1.5724708 |
50 |
1.5724698 |
1.5724709 |
60 |
1.5724697 |
1.5724710 |
70 |
1.5724696 |
1.5724711 |
80 |
1.5724695 |
1.5724712 |
90 |
1.5724694 |
1.5724713 |
100 |
1.5724693 |
1.5724714 |
CHAPTER 5
-
Design
[All designs are done with a scale of 1nm=1mm]5.1.1 3D model of fixed finger 5.1.2 3D model of proof mass
-
Design Of Standard Capacitance Accelerometer
The preliminary design was carried out on Solid edge . The design parameters of the standard capacitive accelerometer is taken from one of the research papers that were referred to. The fixed fingers and the proof mass along with fingers and springs were separately designed . The standard design has a total of 12 fingers on the proof mass. The thickness of both the proof mass and the fixed fingers are considered to be 40mm.
5.2.1 Standard capacitive accelerometer
-
Design Of Capacitance Accelerometer With Reduced Thickness Of 20mm
The thickness of both the proof mass and the fixed fingers are reduced by 20mm with respect to the standard design. There is no variation in any other parameters other than the thickness. The total number of fingers present in this model is 12. The proof mass and the fixed fingers are separately designed and assembled.
5.3.1 Capacitive accelerometer of thickness 20mm
-
Design Of Capacitance Accelerometer With Increased Thickness Of 80mm
The thickness of both the proof mass and the fixed fingers are increased by 40mm with respect to the standard design. There is no variation in any other parameters other than the thickness. The total number of fingers present in this model is
12. The proof mass and the fixed fingers are separately designed and assembled.
5.4.1 Capacitive accelerometer of thickness 80mm
-
Design Of Capacitance Accelerometer With Increased Thickness Of 160mm
The thickness of both the proof mass and the fixed fingers are increased by 120mm with respect to the standard design. There is no variation in any other parameters other than the thickness. The total number of fingers present in this model is 12. The proof mass and the fixed fingers are separately designed and assembled.
5.5.1 Capacitive accelerometer of thickness 160mm
-
Design Of Capacitance Accelerometer With Additional Fingers with same c/s
The fixed fingers and the proof mass along with fingers and springs were separately designed . The standard design has a total of 16 fingers on the proof mass. The thickness of both the proof mass and the fixed fingers are considered to be 40mm. The proof mass and the fixed fingers are separately designed and assembled.
5.6.1 Capacitive accelerometer with additional fingers 5.6.2 Gap between fingers CHAPTER 6 Analysis
-
Standard model:
Fig 6.1: Load and constraints under structural analysis
The model is scaled as per 1nm=1mm in the simulation process.
The stress analysis is done on the software called ANSYS. First the assembly created on solid edge is converted to a
.igs file which makes it compatible with ANSYS. The assembly is then transferred to ANSYS via the DesignModeler.
After importing the assembly the in the DesignModeler, a face split is performed to separate the proof mass from the fingers and the connecting rods.
The material is selected to be silicon anisotropic for the analysis. The design is then meshed with a size of 50mm.
Fig 6.2: Meshed model in Ansys
The acceleration is set to the proof mass for 10G in the x axis , and a displacement of 0mm is set in the x axis. The Fixed fingers are considered as fixed constraints. The larger springs are also constrained as the analysis is strictly performed for the x axis.
The total deformation analysis is performed and results are obtained for 10G , 30G ,50G ,70G and 100G respectively.
Fig: 6.3 Stress distribution for standard model x-axis simulation AND Fig 6.4: Displacement under x-axis simulation for standard model
Similarly the same procedure is followed for analysis of stress in the y axis. Instead of constraining the larger springs , the smaller springs are constrained. The acceleration is considered to be 10G and the displacement is considered to be 0mm in z axis. The total deformation is analyzed for 10G , 30G , 50G . 70G and 100G respectively.
Fig 6.5: Displacement in yaxis for standard model AND Fig6.6 : Stress displacements in y axis for standard model.
-
Model with thickness of 20mm: .
Fig 6.2.1 stress for x-axis simulation Fig 6.2.2Displacement for x-axis simulation
Fig 6.2.3 Displacement for y-axis simulation Fig 6.2.4 Stress distribution for y-axis simulation
-
Model with thickness of 80mm
Fig 6.3.1Displacement for x-axis simulation Fig 6.3.2 Stress distribution x-axis simulation
Fig 6.3.3 Displacement for y-axis simulation Fig 6.3.4 Stress distribution for y-axis simulation
-
Model with thickness of 160mm:
Fig 6.4.1 Displacement for x-axis simulation Fig 6.4.2Stress distribution for x-axis simulation
Fig 6.4.4 Stress distribution for y-axis simulation Fig6.4.3 Displacement for y-axis simulation
-
Model with Additional Fingers:
Fig 6.5.1Displacement for x-axis simulation Fig 6.5.2 Stress distribution for x-axis simulation
Fig 6.5.3 Displacement for y-axis simulation Fig 6.5.4 Stress distribution for y-axis simulation
-
Results:
-
Result for acceleration in x-direction for the standard design
Acceleration m/s2
Displacement x (fm)
10g 30g 50g 70g 100g
3.91
11.74
19.57
27.40
39.147
-
Result for acceleration in y-direction for the standard design
-
Result for acceleration in x-direction for thickness (20nm)
Acceleration m/s2
Displacement y (fm)
10g
33.8
30g
99.6
50g
167
70g
236
100g
338
-
Result for acceleration in y-direction for thickness (20nm)
Acceleration m/s2
Displacement y (fm)
10g
0.12
30g
1.2802
50g
3.8407
70g
6.4011
100g
8.9616
Acceleration m/s2
Displacement y (fm)
10g
6.7
30g
19.7
50g
33.5
70g
47
100g
68
Acceleration m/s2
Displacement y (fm)
10g
0.12
30g
1.2802
50g
3.8407
70g
6.4011
100g
8.9616
Acceleration m/s2
Displacement y (fm)
10g
6.7
30g
19.7
50g
33.5
70g
47
100g
68
-
Result for acceleration in x-direction for thickness
(80nm)
Acceleration m/s2
Displacement y (fm)
10g
0.78
30g
2.34
50g
3.6
70g
5.4
100g
9.78
-
Result for acceleration in y-direction for thickness (80nm)
Acceleration m/s2
Displacement y (fm)
10g 30g 50g 70g 100g
0.076
0.23
0.38
0.52
0.76
-
Result for acceleration in x-direction for thickness (160nm)
Acceleration m/s2
Displacement y (fm)
10g 30g 50g 70g 100g
0.0768
0.211
0.384
0.53
0.768
-
Result for acceleration in y-direction for thickness (160nm)
-
Result for acceleration in x-direction for altered number of fingers
Acceleration m/s2
Displacement y (fm)
10g
3.9
30g
11.74
50g
19.56
70g
27.4
100g
32.67
-
Result for acceleration in y-direction for altered number of fingers
-
Acceleration m/s2 |
Displacement y (fm) |
10g |
0.69 |
30g |
2.07 |
50g |
3.45 |
70g |
4.8 |
100g |
6.9 |
Acceleration m/s2 |
Displacement y (fm) |
10g 30g 50g 70g 100g |
0.076 0.21 0.34 0.48 0.69 |
Conclusion
Capacitance relation to displacement obtained:
C = 0()
generally has a dimension of 40mm thickness.
The analysis conducted indicates that with increase in the thickness of the capacitive accelerometer, the displacement decreases which in turn increases the capacitance induced. With increase in capacitance induced the response time of the airbag control module is reduced, thus increasing the efficiency of accelerometer by increasing the thickness of the capacitive accelerometer also increases the stress induced in the accelerometer. So, we have to compromise with the efficiency of the accelerometer due to the stress produced. The basic standard of capacitive accelerometer available in market
Future Work
The entire work was carried out based on the fingers placed in the lateral position only (along x-axis) even for the y-axis simulations. Thus, one of the major improvements to the model can be the introduction of sensing fingers on the y- axis that is along the longitudinal direction as well. This will
Stress analysis:
Stress analysis was carried out to analyze critical points of failure under the action of loads. Thus, what can be inferred from this is that, for application of load in x direction, the maximum stress is concentrated at the point where the fingers are attached to the proof mass. For the y-axis analysis, the stress was observed to be concentrated at the point where the lateral connecting beams are attached to the proof mass.
further enhance the system efficiency particularly for longitudinal analysis.
The work carried out can further be improved and a more idealistic and justified results can be obtained taking into consideration the COMSOL software approach. The model can be taken its true scale and boundary conditions will remain the same as in case of the work carried out above.
Fig 9.1: COMSOL approach static structural
Two primary modules are taken into consideration. One is the solid mechanics module that deals with the static structural analysis of displacement and stress of the body. The next is the Electro Statics Module which deals with determination of differential capacitance at the terminals
required. A reference voltage of 1V is applied to the fixed terminals and the proof mass will be at ground charge condition. This is analyzed under electric potential probe analysis to determine output voltage and maxwell differential capacitances can be obtained in tabulated format.
Fig 9.2: Modules and conditions Fig9.3: System properties
In order to analyze the capacitance produced by the capacitive accelerometer an electrostatics study was conducted in COMSOL. The fixed fingers are given an terminal voltage value of 1V. The proof mass along with the
moveable fingers are grounded. A body load is defined with respect to volume on the proof mass. The fixed constraints are applied on the fixed fingers. A global probe is created to determine the Maxwell capacitance.
Fig9.4 : Electrostatic comsol approach
Thus, through this approach, both static structural and electrostatics can give conclusive evidence on the efficiency of the system, through both static analysis and electrical approach. Dynamic Analysis
Another Approach to obtain precise outputs is the dynamic analysis of te system in time dependent form. Due to lack of system requirements and license of software being limited to
use, this approach was not possible to be done. However, in future prospects, this will definitely enhance the results and give justified outputs for effective efficiency comparison between the models.
However, A transient structural (time variant) approach was carried out in subsets for a time interval of 1s starting from 0.2
seconds in steps of 0.1 /0.15 seconds up to 16 subsets. It was observed that the deformation is more or less the same as in case of static structural, but a very small decrease in deformation was seen half way through the time interval and
the certain small variations of increase-decrease took place, after which, the value increases and maximum value is obtained. Acceleration, displacement and fixed constraints would remain the same as in static structural analysis.
Fig9.5: Transient analysis setup
Fig 9.6: Transient analysis 20nm y axis
Fig 9.7: Transient analysis 20nm x axis
Fig 9.8: Varied finger x axis transient analysis
Fig 9.9: 80nm model transient analysis (x-axis)
Fig 9.10: 160nm model transient analysis (x-axis)
Fig 9.11 Standard model transient analysis
REFERENCES:
-
Occupant Protection in Passenger Vehicles, Traffic Safety Facts 2017 Data
https://crashstats.nhtsa.dot.gov/Api/Public/ViewPublication/8126 91
-
Accelerometers: Taking the Guesswork out of Accelerometer Selection https://blog.endaq.com/accelerometer-selection
-
Niu, W. , Fang, L. , Xu, L. , Li, X. , Huo, R. , Guo, D. and Qi, Z. (2018) Summary of Research Status and Application of MEMS Accelerometers. Journal of
Computer and Communications, 6, 215-221. doi: 10.4236/jcc.2018.612021.
-
Accelerometer Sensor Working and Applications https://www.elprocus.com/accelerometer-sensor-working-and- applications/
-
Puccioni, Giulio. (11 February 2020). Design and Analysis of MEMS Capacitive Accelormeter
-
G. Vijila, S. Vijayakumar, M. Alagappan, and A. Gupta(2011) Design and Analysis of 3D Capacitive Accelerometer for Automotive Applications
https://www.comsol.co.in/paper/design-and-analysis-of-3d- capacitive-accelerometer-for-automotive-applications-1146
-
Vinay, P & Satya, Ch & Vamsi, Sri & Hemanth, M & Saiteja, A & Ali, .abid & Puli, Ashok & Satya, Venkata. (2017). Design and simulation of MEMS based accelerometer for crash detection and air bags deployment in automobiles. International Journal of Mechanical Engineering and Technology. 8. 424-434.
BIBLIOGRAPHY:
-
Benmessaoud, M., Nasreddine, M.M. Optimization of MEMS capacitive accelerometer. Microsyst Technol 19, 713720 (2013). https://doi.org/10.1007/s00542-013-1741-z
-
Z. Andrabi and K. A. Gupta, "Study and Analysis of Materials for Design of MEMS Capacitive Accelerometer," 2018 3rd IEEE International Conference on Recent Trends in Electronics, Information & Communication Technology (RTEICT), Bangalore, India, 2018, pp. 2183-2187, doi: 10.1109/RTEICT42901.2018.9012505.
-
Z. Mohammed and M. Rasras, "Optimization of finger spacing and spring constant in comb type capacitive accelerometer," 2016 IEEE International Nanoelectronics Conference (INEC), Chengdu, 2016, pp. 1-2, doi: 10.1109/INEC.2016.7589291.
-
Puccioni, Giulio. (2020). Design and Analysis of MEMS Capacitive Accelormeter.
-
Niu, W. , Fang, L. , Xu, L. , Li, X. , Huo, R. , Guo, D. and Qi, Z. (2018) Summary of Research Status and Application of MEMS Accelerometers. Journal of Computer and Communications, 6, 215-221. doi: 10.4236/jcc.2018.612021.
-
Vinay, P & Satya, Ch & Vamsi, Sri & Hemanth, M & Saiteja, A
& Ali, .abid & Puli, Ashok & Satya, Venkata. (2017). Design and simulation of MEMS based accelerometer for crash detection and air bags deployment in automobiles. International Journal of Mechanical Engineering and Technology. 8. 424-434.
-
J. Beitia, P. Loisel, C. Fell and I. M. Okon, "Miniature accelerometer for high-dynamic, precision guided systems," 2017 24th Saint Petersburg International Conference on Integrated Navigation Systems (ICINS), St. Petersburg, 2017, pp. 1-6, doi: 10.23919/ICINS.2017.7995641.
-
Szermer, M. et al. FEM analysis of a 3D model of a capacitive surface-micromachined accelerometer. 2017 14th International Conference The Experience of Designing and Application of CAD Systems in Microelectronics (CADSM) (2017): 432-434.