
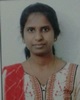
- Open Access
- Authors : Veena N , Chaithra C V , Kaveri , Bupesh Yadav, Sangamesh S Goudar
- Paper ID : IJERTV10IS080098
- Volume & Issue : Volume 10, Issue 08 (August 2021)
- Published (First Online): 20-08-2021
- ISSN (Online) : 2278-0181
- Publisher Name : IJERT
- License:
This work is licensed under a Creative Commons Attribution 4.0 International License
Experimental Investigation on Properties of Concrete by Partial Replacement of Bagasse Ash with Cement and Cupola Slag with Coarse Aggregate
Mrs. Veena N1, Ms. Chaithra C V2, Ms. Kaveri3, Mr. Bupesh Yadav4, Mr. Sangamesh S Goudar5
1Assistant Professor, 2Student, 3Student, 4Student, 5Student
Civil Engineering
Raja Rajeswari College of Engineering, Bangalore-74, Karnataka, India
Abstract- Concrete is being widely used for the construction of most of the buildings, bridges, etc throughout the world. Hence it is the backbone to the infra structure development of a nation. With the increase in demand for construction materials, there is a strong need to utilize alternative materials for sustainable development. Cupola slag and bagasse ash are the waste is an emerging issue posing serious pollution problems to the human and the environment. Waste from metal casting and as well from sugar mill industries is currently considered to be one of the fastest growing waste streams in the world, with an estimated growth rate going from 4% up to 7% per year. The disposal of which is becoming a challenging problem. For solving the disposal of large amount of cupola slag material, reuse of waste in concrete industry is considered as the most feasible application. Due to increase in cost of normal coarse aggregate and cement it has forced the civil engineers to find out suitable alternatives replacement materials for coarse aggregates and cement. Cupola slag waste is used as one such alternative for coarse aggregate. Owing to scarcity of coarse aggregate for the preparation of concrete, partial replacement of cupola slag waste with coarse aggregate was attempted. It was found that the use of cupola slag and bagasse ash waste aggregates results in the formation of light weight concrete. In this study the coarse aggregate and cement has been replaced by cupola slag and bagasse ash waste accordingly in the range of 5%, 10% and 15%by weight of coarse aggregate in terms of preparation of cubes, prism and cylinders. Concrete mixtures were produced, tested and compared in terms of compressive, flexural and split tensile strength and identified the suitable proportion of the replacement of coarse aggregate and cement with concrete.
Keywords- Bagasse ash, Cupola slag, Industrial Waste, Compressive Strength, Flexural Strength, Split Tensile Strength.
-
INTRODUCTION
-
General
Cement is one of the most used construction materials. It is the conventional building material that actually is responsible for about 5%-8% of global CO2 (a greenhouse gas) and with the ever-increasing demand it could significantly contribute to environmental pollution imposing detrimental effects. Researchers all over the world today are focusing on ways of utilizing industrial or agricultural waste, as a source of raw materials for many industries. Utilization of such wastes as cement and as aggregate replacement materials this may help reduce the cost of concrete
production and also minimize the negative environmental effects with disposal of these wastes. At present, development in India is mainly by implementation of infrastructure projects. Due to that construction projects are executed at very rapid rate. In the developing country like India, availability of natural resources is also an influencing factor apart from funding due to this rapid infra-structural growth it requires large amount of construction material like cement, aggregate, wood etc. R.R.C structures are preferred over steel structures in India which requires larger quantity of concrete. Since availability of natural resources of concrete is limited as we get it from natural deposits at present, there is a need to develop a new material that can effectively replace with conventional without compromising with strength and durability properties of concrete.
-
Cupola Slag
Cupola furnaces were built in China as early as the warring states period, although Donald Wagner writes that some iron ore melted in the blast furnace may have been cast directly into mould`s modern cupola furnace was made by French scientist and entomologist Rene-Antoine Frechault de Reaumur around 1720.Cupola slag, a by-product of cast iron manufacturing is produced during the separation of the molten steel from impurities in cupola furnaces. The slag occurs as a molten liquid melt and is a complex solution of silicates and oxides that solidifies upon cooling. Virtually all iron and steel are now made in integrated iron plants using an electric arc furnace process. The open-heart furnace process is no longer used. In the basic oxygen process, hot liquid blast furnace metal, scrap, and fluxes, which consist of lime (CaO) and dolomitic lime (CaMg (Co3)2), are charged to a furnace. The cupola slag in the form of fine and coarse aggregates is shown in Fig.1.
Fig.1 Cupola slag in the form of Fine aggregates and Coarse aggregate
-
Bagasse Ash
Bagasse is a by-product from sugar industries which is burnt to generate power required for different activities in the factory. The burning of bagasse leaves bagasse ash as a waste, which has a pozzolanic property that would potentially be used as a cement replacement material. It has been known that the worldwide total production of sugarcane is over 1500 million tons.
Sugarcane consists about 30% bagasse whereas the sugar recovered is about 10%, and the bagasse leaves about 8% bagasse ash (this figure depends on the quality and type of the boiler, modern boiler releases lower amount of bagasse ash) as a waste, this disposal of bagasse ash will be serious concern.
Sugarcane bagasse ash has recently been tested in some parts of the world for its use as a cement replacement material. The bagasse ash was found to improve some properties of the paste, mortar and concrete including compressive strength and water tightness in certain replacement percentages and fineness.
The higher silica content in the bagasse ash was suggested to be the main cause for these improvements. Although the silicate content may vary from ash to ash depending on the burning conditions and other properties of the raw materials including the soil on which the sugarcane is grown, it has been reported that the cement and results in a reduction of the free lime in the concrete. Bagasse ash in different form is shown in the Fig.2.
Fig.2 Bagasse and Bagasse ash
-
-
OBJECTIVE
-
To perform the following test and to compare the results with and without replacement of cupola slag and bagasse ash.
-
Compressive Strength Test.
-
Flexural Strength Test.
-
Split Tensile Strength Test.
Sl. No
Description
Result
Requirements As Per IS:12269-2013
1.
Specific gravity
3.15
Not specified
2.
Initial setting time
165minutes
Shall not be less than 30Minutes
3.
Final setting time
450minutes
Shall not be more than 600Minutes
Sl. No
Description
Result
Requirements As Per IS:12269-2013
1.
Specific gravity
3.15
Not specified
2.
Initial setting time
165minutes
Shall not be less than 30Minutes
p>3. Final setting time
450minutes
Shall not be more than 600Minutes
-
-
To reduce the overall environmental effects of concrete production using cupola slag and bagasse ash as partial replacement.
increased by 4% to 6% for replacements of both coarse & fine aggregates from 30% to 50%. However, in case of coarse aggregate the compressive strength increased by 5% to 7% and decreased in case of fine aggregate by 7% to 10% at 100% replacement over control mixes in M20, M30 & M40 grade of concrete. It could be said that 100% replacement of normal crushed coarse aggregate with slag aggregate, improved the flexure and split tensile strength by about 6% to 8% in all mixes. The improvement in strength was attributed to the rough surface texture which ensured strong bonding and adhesion between aggregate particles and cement paste. In case of natural fine aggregate replacement with slag fine aggregate the strength increased was for 50% by 5% to 6% but reduced at 100% replacements by 6 to 8%. The reason for reduction in strength for 100% replacement could be attributed to the presence of coarser particle sizes which could be overcome by addition of finer materials. They observed increment in strength.
M Vijaya Sekhar Reddy, I V Ramana Reddy studied the behaviour of high-performance concrete which is being the most used type of concrete in the construction industry. They replaced cement with supplementary cementing materials like fly ash, silica fumes and metakaolin. With 6% replacement of sugar cane bagasse ash, compressive strength increases 9.67% compare to normal concrete after 28 days of curing. The mix design adopted was M60, cubes were casted and cured. The optimum amount of sugar cane bagasse ash that can be replaced with cement is 6% to get maximum strength of concrete. After 6% replacement of sugar cane bagasse ash there is decrease in strength of concrete with increase of replacement of sugar cane bagasse ash. Also split tensile strength and flexural strength increase with 6% replacement of sugar cane bagasse ash compare to normal concrete. Also, sugar cane bagasse ash can be use as admixture in concrete due to high % of silica present in ash. Also, above results show a beneficial application of the use of sugar cane bagasse ash and reduce the environment problem and also minimize the requirement of land fill area to dispose sugar cane bagasse ash. They concluded that there was a considerable increase in service life of the concrete structure and reduction in heat of hydration.
-
MATERIAL AND PROPERTIES
-
Cement
Cement in concrete acts as a binding material that harden after the addition of water. It plays an important role in construction sector. In this study the Ordinary Portland Cement (OPC) of 53 grade is used according to IS: 1489- 1991. Various tests were performed on cement they are: Soundness test, Consistency test, Initial and final setting time
-
-
-
Workability of concrete.
3. LITERATURE REVIEW
Mohammed Nadeem and Arun D Pofale Replaced fine aggregate by using industrial slag of partial replacement of 0,30,50,70 and 100%. The compressive strength of concrete
Table-1: Cement Requirements as per IS:12269-2013
-
Fine Aggregate
The material which passes through BIS test sieve number 4 is termed as fine aggregate usually natural sand is used as a fine aggregate at places where natural sand is not available crushed stone is used as fine aggregates. In our region fine aggregate can be found from bed of Kaveri River. It conforms to IS 383 1970 comes under zone II.
Fig.3 Fine Aggregate
-
Coarse Aggregate
The material which is retained on BIS test sieve number 4 (4.75mm) is termed as coarse aggregate. The broken stone is generally used as a stone aggregate. Coarse aggregate used is locally available crushed angular aggregate of size 20mm and 10mm are used for this experimental work.
Fig.4 Coarse Aggregate
-
Cupola Slag
Cupola slag is by-product material which is gathered from cast iron manufacturing unit. It is produced during melting of cast iron in cupola furnaces. The slag occurs as a molten liquid which solidifies upon cooling. Cupola slag is a complex solution of silicates and oxides. Cupola furnace is cylindrical shaped melting device which is used in steel industries for melting of cast iron ranging from 0.5 to 4 m in diameter. Bottom of furnace having a door which can swing in and out. Top of the furnace is kept open. Air vent is arranged to supply the air in Furnace. Shells of furnace are made up of steel, refractory bricks. There is one slag hole from which slag comes out at higher temperature with low viscosity that solidifies in black coloured lumps upon cooling. Lumps size varied from 100 mm to 450 mm. Cupola slag is tends to be dense solid material that varies in colour from Grey to black. A physical property of cupola slags to be used as compared with natural coarse aggregates and IS 383-1970 requirements for material to be used as aggregates.
Chemical composition
Percentage of Materials
CaO
20-50
SiO2
25-55
Al2O3
5-20
MgO
5-30
MnO
1-4
FeO
1-15
Chemical composition
Percentage of Materials
CaO
20-50
SiO2
25-55
Al2O3
5-20
MgO
5-30
MnO
1-4
FeO
1-15
Table-2: Chemical Composition of Cupola Slag
-
Bagasse Ash
Bagasse is a by-product from sugar industries which is burnt to generate power required for different activities in the factory. The burning of bagasse leaves bagasse ash as a waste, which has a pozzolanic property that would potentially be used as a cement replacement material. It has been known that the worldwide total production of sugarcane is over 1500 million tons. Sugarcane consists about 30% bagasse whereas the sugar recovered is about 10%, and the bagasse leaves about 8% bagasse ash (this figure depends on the quality and type of the boiler, modern boiler releases lower amount of bagasse ash) as a waste, this disposal of bagasse ash will be of serious concern. Sugarcane bagasse ash has recently been tested in some parts of the world for its use as a cement replacement material. The bagasse ash was found to improve some properties of the paste, mortar and concrete including compressive strength and water tightness in certain replacement percentages and fineness. The higher silica content in the bagasse ash was suggested to be the main cause for these improvements. Although the silicate content may vary from ash to ash depending on the burning conditions and other properties of the raw materials including the soil on which the sugarcane is grown, it has been reported that the silicate undergoes a pozzolanic reaction with the hydration products of the cement and results in a reduction of the free lime in the concrete.
-
Material Test Results
-
Specific Gravity
Table-3: Specific gravity of materials
PROPERTY
RESULT
SPECIFIC GRAVITY FOR COARSE AGGREGATE
2.68
SPECIFIC GRAVITY FOR FINE AGGREGATE
2.66
SPECIFIC GRAVITY FOR CEMENT
3.15
SPECIFIC GRAVITY FOR CUPOLA SLAG WASTE
2.58
-
Bulk Density
Property
Result
Bulk Density for Fine Aggregate
Loose
1.54kg/L
RODDED
1.67Kg/L
Bulk Density for Coarse Aggregate
Loose
1.53kg/L
RODDED
1.68Kg/L
-
RESULT AND DISCUSSION
-
Concrete Mix Design
Based on trial mixes for different proportions of ingredients, the final design mix was prepared for M35 grade of concrete as per IS 10262:2009. The concrete mix proportion and w/c ratio was considered as 0.4 and with varying percent of Cupola slag and bagasse ash and design was done. The different specimens as per the requirement for test were casted. The specimens were tested after 28 days of curing.
In each category the specimens to be tested and average value is reported in the form of graphs.
-
Compression Test
The compressive strength of concrete i.e., ultimate strength of concrete is defined as the load which causes failure of the specimen divided by the area of the cross section in the uni- axial compression, under a given rate of loading. To avoid large variation in the result of compression test, great care is taken during the casting of the specimens and loading as well. The test results conducted for 28 days is tabulated below.
fracture). The test results conducted for 28 days is tabulated below.
Table-6 Flexural Strength Results
Specimen Details
Flexural Strength (N/mm2)- 7 Days
Flexural Strength (N/mm2)-28 Days
Convention Concrete
1.63
2.50
5% of Partial Replacement with Cupola Slag and Bagasse Ash
1.95
3.00
10% of Partial Replacement with Cupola Slag and Bagasse Ash
2.08
3.20
15% of Partial Replacement with Cupola Slag and Bagasse Ash
1.76
2.70
Specimen Details
Flexural Strength (N/mm2)- 7 Days
Flexural Strength (N/mm2)-28 Days
Convention Concrete
1.63
2.50
5% of Partial Replacement with Cupola Slag and Bagasse Ash
1.95
3.00
10% of Partial Replacement with Cupola Slag and Bagasse Ash
2.08
3.20
15% of Partial Replacement with Cupola Slag and Bagasse Ash
1.76
2.70
Table-5: Compressive Strength Results
Specimen Details
Compressive Strength (N/mm2)- 7 Days
Compressive Strength (N/mm2)- 28 Days
Convention Concrete
23.40
36.00
5% of Partial Replacement with Cupola Slag and Bagasse Ash
24.38
37.50
10% of Partial Replacement with Cupola Slag and Bagasse Ash
25.35
39.00
15% of Partial Replacement with Cupola Slag and Bagasse Ash
21.45
33.00
Flexural Strength
Specimen Details
Compressive Strength (N/mm2)- 7 Days
Compressive Strength (N/mm2)- 28 Days
Convention Concrete
23.40
36.00
5% of Partial Replacement with Cupola Slag and Bagasse Ash
24.38
37.50
10% of Partial Replacement with Cupola Slag and Bagasse Ash
25.35
39.00
15% of Partial Replacement with Cupola Slag and Bagasse Ash
21.45
33.00
Flexural Strength
% Replacement of Cupola slag and Bagasse ash
% Replacement of Cupola slag and Bagasse ash
7 Days
7 Days
28 Days
0
28 Days
0
% Replacement of Cupola slag and Bagasse ash
% Replacement of Cupola slag and Bagasse ash
45
40
35
30
25
20
15
10
5
0
45
40
35
30
25
20
15
10
5
0
5%
5%
10%
10%
15%
15%
Compressive strength in N/mm2
Compressive strength in N/mm2
Graph-1: Compressive Strength Results
-
Flexural Strength
Flexural testing is used to determine the flex or bending properties of a material. Sometimes referred to as a transverse beam test, it involves placing a sample between two points or supports and initiating a load using a third point or with two points which are respectively call 3-Point bend and 4-point bend test.
Maximum stress and strain are calculated on the incremental load applied. Results are shown in a graphical format with tabular results including the flexural strength (for fractured samples) and the yield strength (samples that did not
Graph-2: Flexural Strength Results
3.5
3
2.5
2
1.5
1
0.5
0
3.5
3
2.5
2
1.5
1
0.5
0
7 Days
7 Days
28 Days
0
28 Days
0
5%
5%
10%
10%
15%
15%
Compressive Strength
Compressive Strength
Flexural strength in N/mm2
Flexural strength in N/mm2
-
Split Tensile Strength
Tensile strength is an important property of concrete because concrete structures are highly vulnerable to tensile cracking due to various kinds of effects and applied loading itself. However, tensile strength of concrete is very low when compared to its compressive strength. It is the standard test, to determine the tensile strength of concrete in an indirect way. This test could be performed in accordance with IS: 5816-1970.A standard test cylinder of concrete specimen is placed horizontally between the loading surfaces of compression testing machine. The compression load is applied diametrically and uniformly along the length of cylinder until the failure of the cylinder along the vertical diameter. The test results conducted for 28 days are tabulated below.
Table-8: Split Tensile Strength Results
Specimen Details
Split Tensile Strength (N/mm2)- 7 Days
Split Tensile Strength (N/mm2)- 28 Days
Convention Concrete
1.07
1.65
5% of Partial Replacement with Cupola Slag and Bagasse Ash
1.40
2.16
10% of Partial Replacement with Cupola Slag and Bagasse Ash
1.95
3.00
7. REFERENCES
15% of Partial Replacement with Cupola Slag and Bagasse Ash
1.72
2.65
-
R. Balaraman and S. Anne Ligoria Utilization of cupola slag in concrete as fine add coarse aggregate International Journal of Civil Engineering and Technology (IJCIET)-Aug 2015, Volume 6, pp. 06-14.
-
Joseph O. Afolayan, Stephan A. Alabi Investigation on the
Split tensile strength in N/mm2
Split tensile strength in N/mm2
3.5
3
2.5
2
1.5
1
0.5
0
Split Tensile Strength
0 5% 10% 15%
% Replacement of Cupola slag and Bagasse ash
7 Days
28 Days
potentials of cupola furnace slag in concrete International Journal of Integrated Engineering 2013, Volume 5, pp. 59-62.
-
A review paper on cupola slag waste as a partially replacement in coarse aggregate In Prof. Abrarahemad A Khalak, MR Jaykumar N Chaudhary, MR. Yashkumar J Chaudhary, MR Vijaykumar S Vanjara, MR. Yash B Shah, MR Hardikbhai J Parmar.
-
Concrete Partial replacement of cement with sugarcane bagasse ash in concrete: A review Pragalbha Khare1, Mohd. Afaque Khan2, Neeti Mishra3.
-
Partial replacement of cement in concrete with sugarcane bagasse ash Pallavi S. Kumbhare1, Shifa Tanwar2, Yogesh Thosar3, Yash Dudhe4, Gaurav Rudra.
Graph-3: Split Tensile Strength Results
-
-
CONCLUSION
Based on the experimental investigation carried out on the strength behaviour of Partial replacement of coarse aggregate with cupola slag and cement with Bagasse ash, the following conclusions are drawn.
-
Compressive strength increases up to 10% of replacement and then starts to decrease at 15% replacement.
-
Flexural strength increases up to 10% of replacement and then starts to decrease at 15% replacement.
-
Split tensile strength increases up to 10% of replacement and then starts to decrease at 15% replacement.