
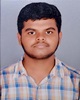
- Open Access
- Authors : Siddharaj Dabade , Prabhjyot Singh Mokha , Priti Maurya
- Paper ID : IJERTV10IS080157
- Volume & Issue : Volume 10, Issue 08 (August 2021)
- Published (First Online): 26-08-2021
- ISSN (Online) : 2278-0181
- Publisher Name : IJERT
- License:
This work is licensed under a Creative Commons Attribution 4.0 International License
Plastic Waste Management in COVID-19: A Review
Prabhjyot Singh Mokha
Dept. of Chemical Engineering D.J.Sanghvi College of Engineering
Siddharaj Dabade
Dept. of Chemical Engineering D.J.Sanghvi College of Engineering
Priti Maurya
Dept. of Chemical Engineering
D. J. Sanghvi College of Engineering
Abstract The corporeal attributes of plastics like durability, low density, tensile strength and minimal cost, makes them useful in various sectors. Regardless of their degree of operation and utilization, plastics deteriorate the environment and thus its disposal has gained critical attention. In addition to the already existing challenges, the COVID-19 scenario has made conditions worse. This paper provides an overview of different plastic disposal policies and discusses the readjustments of these policies amidst the COVID -19 pandemic along with their potential environmental implications. This paper has also emphasized the issue of plastic waste management policies, sustainable and green plastic solutions and development of dynamic and responsive waste management system which is followed by recycling of the plastic waste. Advances in technologies and systems for the collection, sorting and reprocessing of recyclable plastics are creating new opportunities for recycling, and with the combined actions of the public, industry and governments it may be possible to divert the majority of plastic waste from landfills to recycling over the next decades.
Keywords: Plastic Waste Management; Covid-19; Sustainable and green solutions.
Introduction
Plastic products have become a vital part of our lifestyle. Therefore, the production of polymers is increasing globally. There's an estimation that roughly 70% of plastic packaging products are transformed into plastic waste in a very short extent. The recycling rate in India is significantly better than the worldwide average of 20%.[3] However, over 9,400 tons of plastic waste that are either landfilled or left in the streams or groundwater resources, thus, polluting them. While some types of plastic don't even decompose at all, others might take hundreds of years to breakdown.
The disposal of plastics is one of the least recognized and most highly problematic areas of plastics ecological impact. Ironically, one of the plastics most desirable traits: its durability and resistance to decomposition, is also the source of one of its greatest liabilities when it comes to the disposal of plastics.
The solution to the waste management problem lies in the segregation of dry and wet solid waste at the source for which an effective mass awareness campaign is important. The creation of efficient solid waste management infrastructure coupled with encouraging the establishment of recycling centers would help address the MSW problem. Plastics can be recycled to produce articles for mass use
augmenting the concept of resource management. Many useful products have been developed with recycled plastics, and a large number of people are employed in these activities in small, micro, and informal sectors. Recycling ensures that the unwanted and discarded plastics waste does not remain on the roadside and is also not carried to the landfill. Apart from the conventional recycling, which is popular in India, alternate processes of plastic recycling are also required to be encouraged.
In India, the growth of the plastic market is higher than its GDP growth at 7%. The plastics industry has been an important contributor to the Indian economy, employing around 4 million people [7]. According to the reports for the year 2018-19, Central Pollution Control Board (CPCB) has estimated that India generates approximately 3.3 million metric tons per annum plastic waste [4], (which amounts to 26,000 tons of waste per day), and out of this approximately
5.6 Million tons per annum plastic waste is recycled (i.e. 15,600 tons of waste per day) and 3.8 Million tons per annum plastic waste is left uncollected or littered (9,400 tons of waste per day).[5]
The critical issue is the plastics pollution impact on human health, and especially during the pandemic, the situation was more critical, and more measures needed to be taken to prevent the spread of this infection.
Impact of Covid-19 On Plastic Waste Management
The commencement of the COVID-19 pandemic led to panic shopping of food, toilet papers, face masks, gloves, household products, and alcohol-based hand sanitizers. At this point, looking for basic protecting equipment, products, and groceries boosted rapidly. This conjointly inflated the disposal of perishable products and leftovers, that ultimately generated tons of waste. But, the question of how these tons of waste will properly be disposed of with the limited technological innovation and recycling methods available remains unsolved.
The pandemic of 2020 has only made matters worse: the use of plastic particularly single-use and disposable
has increased manifold, said Sunita Narain, director general, Centre for Science and Environment (CSE).[4]
During the pandemic, personal protecting equipment (PPE) kit was necessary for doctors and other people operating close to COVID victims along with this, the
production of masks also took place and all these led to an
Besides, the pandemic has
Vol. 10 Issue 08, August-2021
also affected the recycling
increase in plastic pollution. Individual choices throughout lockdown also increased plastic demand. Packaged take-out meals and home-delivered groceries contributed further thousands of loads of plastic waste. Thus, the lockdown increased the usage of plastics in many various ways. The lifecycle of plastics from cradle (extraction) to grave (disposal) is dangerous and has environmental value. Refineries for plastic are rumored to extend the exposure to toxic chemicals resulting in inflated health outcomes like mortality, morbidity, and disability-adjusted life-years.[1]
There was a drastic change in many disposal processes that were earlier done differently and as the coronavirus hit the country, it was implemented in a way that it doesnt lead to the spread of infection more. Safety measures were increased. These were like separating the waste that was used to protect from infection away from normal day-to-day waste, disposing of it more safely, and properly, also the timing was set to dispose of them and many more that can be seen in the fig-1 below.
Figure 1-Impact of Covid-19 on waste management.
In several places, face masks were reported to be piled up at natural surroundings and beaches due to improper disposal of plastic waste, that disrupted the setting. Life underwater was disturbed as marine life was unsafe as they would have incorrectly consumed the non-biodegradable plastics (polypropylene) from face masks as food. Likewise, land animals also would have consumed plastic considering it as their food. Thus, improper disposal of face masks to the natural surroundings possessed a great threat to every life. Also, if these infected masks and waste would have come in contact with animals, they might have become the source of infection spread to humans creating more problems for everyone.
The World Health Organization has requested a 40% step-up of disposable PPE production. If the worldwide population adheres to a regular of 1 disposable mask per day then by the time lockdown finishes, the pandemic might lead to a monthly global consumption and waste of 129 billion face masks and sixty-five billion gloves. [2]
market because of social distancing measures like lockdow, hence affecting livelihoods. As lockdown took effect to slow the effect of coronavirus disease, the worldwide demand for petroleum collapsed due to that the oil costs fell, creating the manufacture of virgin plastics from fossil fuels more cost-effective than recycling. This cost incentive, besides lifestyle changes that increase plastic use, has become difficult, therefore challenging to overcome plastic pollution.[2] A temporary ban on cross-border movements affected developing countries that rely upon foreign technology for waste recycling activities hence most of the waste generated throughout the pandemic was disposed of instead of recycling.
The different types of waste evaluated are listed down below:
-
Medical Waste Evaluation
Due to the novelty of the worldwide pandemic, modification to existing waste facilities to manage the unusual medical waste and its associated viral spread required a good amount of information, and knowledge to dispose of or recycle the waste generated in a way that is doesnt harm the environment as well as humans. Due to the use of masks and gloves becoming necessary to use for almost everybody, plastic pollution increased drastically with no option left for the reduction in plastic pollution. On account of the potential speedy expansion volumes of medical waste, many technical abilities on sorting, segregation, transport, storage, and property waste management technologies are needed to maximize existing infrastructures to accommodate the emergency. Improper management of medical waste has the potential to show patients, doctors, and waste managers to injuries, infections, toxic consequences, and pollution. Various styles of medical waste and its derivatives include non-hazardous waste, pathological waste, radioactive material, infectious waste, chemical waste, toxic waste, sharps waste, and pharmaceutical waste.
-
Non- Medical and home Waste Evaluation
In this lockdown, stay-at-home policy and alternative preventive measures to contain the spread of COVID-19 saw a rise in production and consumption patterns of a non- medical and household-related products like masks, gloves, thermometers, sanitizers and cleaning products, toilet papers, and foodstuffs. Sudden lockdown and worry of the virus caused the intensification of single-use products and panic shopping. Along with this, for more safety precautions everyone started covering every food product with plastic to keep it safe for people to consume, packaged foodstuffs were preferred and thus, increasing the use of plastic in every way.
Overall, the consumption of plastic increased with no solution to reduce or bring the amount to a minimum. But if we focus and think of something, we might be able to find out a way to keep everything safe and also at the same time decrease the consumption of plastic, we will be able to reduce plastic pollution.
Consider the accessible statistics: A global study on this issue states that more than 75% of total plastic is produced and then disposed of as waste in the environment. While less than 10% of plastic is recycled. [4] While Indias plastic waste issue isn't as immense as that of the whole world but it's undoubtedly growing. Richer states like Goa and Delhi turn out the maximum as compared to the national average of grams per capita per day.
At the regional and national levels, prioritization of human health over environmental health has led to the delay or reversal of policies about to cut back single-use plastic. As a result, demand for recycled plastic material has dropped, the profit margins of recycling are reduced, and therefore the environmental footprint of plastics has redoubled. We want an imperative and coordinated commitment to circular economy approaches, as well as recycling practices and strict policies against plastic pollution. Corporations ought to continue efforts to curtail virgin plastic use and increase plastic recycling to measure up to their company social and environmental responsibilities while not a cooperative effort to guard the surroundings throughout might lead to the goals suggested by the United Nations Sustainable Development Goals.[2]
CURRENT GOVERNMENT POLICIES ON PLASTIC WASTE MANAGEMENT
The Government of India notified Plastic Waste Management (PWM) Rules, 2016 on 18th March 2016, superseding the Plastic Waste (Management & Handling) Rules, 2011. These rules were further amended and named as Plastic Waste Management (Amendment) Rules, 2018 Salient features of Plastic Waste Management (PWM Rules), 2016
-
These rules shall apply to all the Waste Generator, Local People, Gram Panchayat, Manufacturer, Producer, Importer, and Brand Owner.
-
Carry bags made of virgin or recycled plastic, shall not be less than 50 microns in thickness. The provision of thickness shall not be applicable to carry bags made up of Compostable plastic, complying IS/ISO: 17088.
-
Everyone shall not litter the plastic waste, shall segregate waste and handover to the authorized agency, and shall pay user fee as prescribed by ULB and spot fine in case of violation.
-
Local Bodies shall encourage the use of plastic waste for road construction or energy recovery or waste to oil or co- processing in cement kilns etc. It shall be responsible for the development and setting up of infrastructure for segregation, collection, storage, transportation, processing, and disposal of the plastic waste either on its own or by engaging agencies or producers
-
Gram Panchayat either on its own or by engaging an agency shall set up, operationalize and coordinate for waste management in the rural area under their control and for performing the associated functions; ensuring that no damage is caused to the environment during this process; creating awareness among all stakeholders about their responsibilities, and also ensuring that open burning of plastic waste does not take place.
Brand Owners, Producer, and Importers need to work out different modes for waste collection system for collecting back the plastic waste within a period of six months in consultation with local authority/State Urban Development Department and implement with two years thereafter.
-
State Pollution Control Board (SPCB)/ Pollution Control Committee (PCC) shall be the authority for enforcement of the provisions of PWM Rules, 2016, relating to registration, manufacture of plastic products, and multilayered packaging, processing, and disposal of plastic wastes.
-
Concerned Secretary-in-charge of Urban Development of the State or a Union Territory and concerned Gram Panchayat in the rural area of the State or a Union Territory shall be the authority for enforcement of the provisions of PWM Rules. (Rules relating to waste management by the waste generator, use of plastic carry bags, plastic sheets or like, covers made of plastic sheets and multilayered packaging.)
-
District Magistrate or Deputy Commissioner shall assist SPCBs/PCCs, Secretary-in- Charge, Urban Development Department, and Gram Panchayat under his jurisdiction, whenever required for enforcement of provisions of PWM Rules, 2016.[6]
MECHANICAL RECYCLING
Types of Plastic Resins and Recycling Potential:
Plastics have a wide variety of resins or polymers with different chemical characteristics. Mainly they fall under two groups: Thermoplastics and Thermoset plastics. 80% of which are Thermoplastics, that can be easily found in household plastics like: soft-drink bottles, clear film for packaging (PET), bags, containers, pipes (LDPE), industrial wrappings and film (HDPE), battery cases, straws and electrical components (PP), which are polyolefins, that can be recycled and be repeatedly formed to a new product by application of heat. In India, polyolefins constitute highest percentage of plastic consumption followed by PVC and PS. The following statistics opens a clear path to plastic waste management as its easy and efficient to recycle Thermoplstics. On the contrary, Thermoset plastics lost their ability to be reformed or remolded when subjected to heat or pressure and hence difficult to recycle.[8]
Overview:
Mechanical recycling, also known as secondary recycling, is the process of recovering plastic solid waste (PSW) and hence reusing it in the manufacturing of new plastic products via mechanical means . It involves the separation of plastic polymer from its associated contaminants and reprocessing through melting, shredding, floating and other processes. Due to variation in melting points of different batch and types of plastics, the most important aspect is the separation of it, as some batch of plastic resins at a definite temperature may fully transform while a different batch may have undergone
Table 1- Types of plastic and recycled product .
partial transformation. Therefore, the mechanical recycling of waste plastics are mostly carried out with a single- polymer waste stream operated at a temperature of 200 300 and in order to achieve maximum efficiency and homogenous mechanical property of produced goods.[8] Mechanical recycling of PSW can only be performed on single polymer plastics, eg PS, PP, PE, etc. Since chemical reactions involved in formation of polymer are all reversible in theory, that means energy supply can cause photo- oxidation and/or mechanical stresses which occurs as a consequence. Due to the above reason, it is very important to have a customer ready to purchase the product.
Mechanical recycling of PSW has also become an important issue in R&D, a recent literature published has high emphasised on utilising polyolefins that ended up in PSW stream. Table-2 summarises direct relation to PSW mechanical recycling, utilising reclaimed and scrap in the studies schemes on bench and pilot scales.[9]
Technologies and Techniques used for mechanical recycling:
Mechanical recycling PSW, involves a number of treatments and being a costly and an energy intense process, mechanical recyclers try these steps and working hours as much as possible [9]. The first step in Mechanical recycling is Segregation or Separation of plastic, many states have setup segregation centres in entire city to facilitate secondary segregation of plastic waste into 25-27 categories in recycling plastic. Techniques used for Segregation of plastics are:
-
Air Classifier (also known as Zig Zag Separator): It is a technique used for separating of light films or paper/ foil, or for separating fine dust or other granular material. It is usually used after Granulation or Dry-Cleaning operations is very effective.
-
Air Tabling: Particles of mix shapes, sizes and densities are separated from each other due to the differential in an upward airflow with controllable velocity and under the influence of vibrating action. It is a density concentration technique.
-
Dry and Wet Gravity Separation (or Sink Float Tank): In this technique, different types of plastics are separated based on their density. The heavier plastic fractions sink to the bottom of the tank whilst the lighter fractions float to the surface. It is used in the recycling of plastic bottles and their caps. Mostly the lids and caps of these bottles are made from colored HDPE plastic and the bottles from PET plastic. Within the Sink Float Tank, the HDPE floats, whilst PET sinks.
-
Froth Flotation: It is an intensive rinsing process with the addition of either fluid or steam and it has the ability to extract large volumes of fluid making it an effective choice for recycling. Friction Separation dissolves and separates
Table 1-Summary of mechanical recycling studies.
impurities sticking to the product, utilizing a high level of rotation and friction. Often used to clean mixed plastics and for highly contaminated films. This technique is an ideal
Overview:
CHEMICAL RECYCLING
choice for soiled plastics to be treated in the recycling process.
-
Plastic Color Sorting: In this technique, ultra-violet light is used in combination with digital camera technology to identify materials as small as 0.04mm. This range of plastics colour sorting machines cover material throughputs of 300- 1800 kgs/hr. The machine throughputs are dependent upon material type and quantity of contamination. The sorting accuracy is typically up to 99.99%.
Near Infrared (NIR): When materials are illuminated, they mostly reflect light in the near infrared wavelength spectrum. The NIR sensor can distinguish between different materials based on the way they reflect light. This uses optical sorting to positively identify different resins. It is usually used for whole bottles & jugs and requires a minimum particle size of 50mm.
The next important step, is Extrusion & Palletisation of the raw material which we get after Separation process. The final product, depends on the physical and chemical attributes of the raw material intended from the separation process. Plastic extrusion is a high-volume manufacturing process of melting the raw material and formed into a continuous profile. Extrusion produces items such as pipe/tubing, rods, window frames, plastic film and sheeting and wire insulation. This process starts by feeding plastic material (pellets, granules, flakes or powder) from a hopper into a barrel of extruder. The material is gradually melted by mechanical energy generated by screws and heaters along the barrel. The molten polymer is then forced into a die, which moulds into a shape that hardens during cooling [3]. The diagrammatic representation of Mechanical recycling can be seen in the following Fig-2 below.
Figure 2-Mechanical recycling of plastic waste
Chemical recycling is also known as the tertiary recycling process which is used to refer to advance technology processes that convert plastic waste materials into liquid or gases. The product formed by chemical recycling is used as feedstock for the production of petrochemical and plastics.[11] The term chemical is used, due to the fact that an alteration is bound to occur to the chemical structure of the polymer. Products of chemical recycling are mainly used as fuel. Depolymerisation is one of the significant processes in plastic recycling, provides high yield product and minimum waste. Variety of chemical recycling processes such as pyrolysis, gasification, liquid gas hydrogenation, viscosity breaking, steam or catalytic cracking, and the use of PSW as a reducing agent in blast furnaces. Chemical recycling helps to overcome traditional recycling processes.
Recently much importance is given to processes like non-catalytic thermal cracking (thermolysis) and catalytic cracking which are used to produce fuel fractions from plastic solid waste. Polyethylene terephthalate (PET) and polyamides such as nylon-6 and nylon-66 effectively depolymerized. Polyethylene (PE) is the potential feedstock for fuel (gasoline) producing technologies. Currently, there is also growing interested in developing value-added products such as lubricants via PE degradation.[12] The main benefit of chemical recycling is the treating heterogeneous and contaminated polymer with limited use of pre-treatment. Taking consideration of mechanical recycling this recycling process is less expensive.
-
Pyrolysis (Plastic to fuel):
Pyrolysis is one of the growing chemical recycling processes for plastic waste. Thermal degradation processes allow obtaining a number of constituting molecules, combustible gases, and/or energy.[13] This processability to produce high calorific gas from a variety of waste plastic, produced gas can be utilized in other gas engines that are related to boiler application and electricity generation. The calorific value of produced gas is nearly 22-30 MJ/m3 depending on the type of waste used as feedstock. Solid char produced from the process which is rich in carbon and mineral content. The further process on char can be used to release the energy content from caron which can be further used in other thermal degradation processes. The general flowsheet of pyrolysis is depicted in figure-3
Benefits of Pyrolysis:
1] Transformation of heterogeneous and contaminated polymer into a valuable commodity.
2] Developing an alternative source of the energy from the low-cost feedstock.
3] Help to reduce the landfilling and greenhouse gases which are resulted in the conservation of
Ecosystem.
Steps in the pyrolysis process are as follows:
-
-
Separation and pre-treatment: Plastic waste is first separated. In addition to this, it pretreated for removal of moisture and cleaning purposes.
-
Conversion: Pyrolytic processes help to convert plastic waste into the gas, In this process plastic is heated in the reactor vessel at high temperature to convert it into a vapor state. Catalyst is added which requires less energy resulted in the formation of more branched products. Produced gas is reused as fuel in this process which helps to minimize air pollution.
-
Distillation: The gas collected in the condensation chamber converted into liquid fuel which is similar to light diesel oil.
-
Acid removal process: Acids formed during the breakdown of the polymer need to be removed because they are corrosive in nature.
-
Refining; As per the requirement refining of the fuel took place.
Figure 3- Pyrolysis of plastic waste
An engineering approach is used in the industries like Rudra Environmental Solutions, Pune has designed and developed a pyrolysis plant where 1 tonne of plastic waste can be
converted to 600650 liters of fuel with almost 60% conversion rate. M K Aromatics Ltd has set-up two plants in Goa to convert plastic waste to fuel. Hence in order to obtain a business model for converting plastic into fuel, need to develop infrastructure and creating awareness among citizens which step towards conservation of the environment.
-
Gasification:
For conservation of the environment and reduction of landfilling space encourage research and development in plastic waste recycling technologies, in which gasification falls into, producing fuels or gases. Gasification mainly consists of partial oxidation of plastic waste operated at high temperatures (>600-800 C). Air is commonly used as gasification agent in this process rather than O2 alone and the air factor 20%-40% of the amount of air needed. Firstly, feedstock oxidizes to produce the depolymerization heat, The primary product in the mixture of carbon monoxide and hydrogen. It is known as syngas which can be further used
in the chemical industry for theVopl.r1o0duIscstuioen08o, fAuvgaursito-u2s021 chemicals.[15,16,18] Hydrogen production efficiency 60- 70% from polymer waste.[19] Gasification used effectively because it utilizes all unsorted domestic waste, industrial waste capable of converting all waste material into usable raw material.[16]
Co-gasification of biomass with polymers has also been shown to increase the amount of hydrogen produced while the CO content is reduced.[20] Air is mostly used as a gasification agent: the main advantage of using air instead of O2 alone is to simplify the process and reduce the cost. But a disadvantage is N2 being present causing the reduction in the calorific value of resulting syngas due to the dilution.
-
Plastic waste to road construction:
The application of plastic in roads opens new options for plastic recycling. Roads are entirely made up of plastic or of materials of composites of plastic with other materials. The types of plastic that can be used for the construction of roads are polystyrene, polypropylene, polyethylene.
Methodology:
Plastic waste is first collected, segregated, cleaned, and shredded. the size of the shredded plastic should normally be 2-3 mm for better spread and coating the aggregate.[14]
Types of bitumen:
1] Bitumen 80/100: This is the softest of all grades available in India. This is suitable for low volume roads and is still widely used in the country.
2] Bitumen 60/70: This grade is harder than 80/100 and can withstand higher traffic loads. It is presently used mainly in the construction of National Highways & State Highways.3] Bitumen 30/40: This is the hardest of all the grades and can withstand very heavy traffic loads. Bitumen 30/40 is used in specialized applications like airport runways and also in very heavy traffic volume roads in coastal cities of the country. The Bitumen to Plastic ratio shall be 10:1.[22]
b) Plastic as binder: Waste plastic is shredded into the required size and mixed with hot stone (150 to 170 °C) with uniform mixing. When heated to around 150 to 170 °C, plastic melts and spreads over the stone aggregate in its molten state, giving a thin coating at the surface and acting as a binder.[17]
Advantages:
1] Making roads with plastic mixture reduces the cost and frequency of maintenance.
2] The cost incurred in the construction of a Bitumen plastic road is significantly lesser than that of only Bitumen road. 3] Salt deposition on the pores of the stone which results in road degradation, is also prevented.
-
Plasma Pyrolysis technology:
Plasma pyrolysis is another emerging technology that is a complete solution to plastic waste. The extreme and versatile heat generation ability of plasma pyrolysis
technology enables it to dispose of all types of plastic waste. In this process, plastic is fed to the primary chamber which is at temperature 850 C. The waste material dissociates into carbon monoxide, hydrogen, methane, higher hydrocarbons, etc. Induced Fans drain the pyrolysis gases and plastic waste into the secondary chamber. In this chamber, pyrolysis gases combusted in presence of excess air. The temperature in this chamber is 1050 C. The hydrocarbon, hydrogen, and COare combusted into the water and safe carbon dioxide. Conditions are maintained such that it eradicates the possibility of formation of toxic gases. The conversion of organic waste into nontoxic gases (CO2, H2O) is more than 99%. Segregation of the waste is not necessary, since very high temperatures make sure the treatment of all types of waste without discrimination.[23]
FUTURISTIC APPROACH
We believe there ought to be a positive approach for a protracted time designing and implementation. With social, political will is of utter importance to develop an efficient plastic waste management system. Efforts ought to be created to boost waste storage and assortment. In India waste management might fall out as long as service delivery is connected to non-public sector participation. It is imperative that the private sector comes forward and enables the public sector stakeholders to devise appropriate frameworks that result in a win-win for both sides. though there are some initiatives taken by company, however there are sturdy needs that all company should come forward to take first step[10]. United Nations environment has drawn up a 10-step road map for governments that are trying to curb the increase use of single-used plastics. The subsequent steps are based mostly on experience of 60 countries round the globe:
-
Target the most problematic single-use plastics by conducting a baseline assessment to spot the foremost problematic single-use plastics, as well as the current causes, extent and impacts of their mismanagement.
-
Consider the best actions to tackle the matter (e.g. through
Vol. 10 Issue 08, August-2021
regulatory, economic, awareness, voluntary actions) given the countrys socio-economic standing and considering their appropriateness in addressing the particular problems identified.
-
Assess the potential social, economic and environmental impacts (positive and negative) of the preferred short- listed instruments/actions, by considering how will the poor be affected, or what impact can the preferred course of acton have on different sectors and industries.
-
Identify and engage key stakeholder groups retailers, consumers, trade representatives, authorities, environmental group and business enterprise associations to confirm broad buy-in. Evidence-based studies also are necessary to defeat opposition from the plastics industry.
-
Raise public awareness concerning the harm caused by single-used plastics, explaining the decision and any punitive measures that will follow.
-
Promote alternatives Before the ban or levy comes into force, the availability of alternatives need to be assessed, thus the government may:
-
Ensure that the preconditions for their uptake within the market are in place.
-
Provide economic incentives to encourage the uptake of eco-friendly and fit-for-purpose alternatives that don't cause additional harm.
-
Support can include tax rebates, analysis, and development funds, technology incubation, public private partnerships, and support to projects that recycle single-use items, and switch waste into a resource which will be reused.
-
Reduce or abolish taxes on the import of materials used to create alternatives.
-
-
Provide incentives to industry by introducing tax rebates or alternative conditions to support its transition. Governments can face resistance from the plastics industry, as well as importers, and distributors of plastic packaging. Provide them time to adapt.
-
Use revenues collected from taxes or levies on
Figure 4- Overview of Circular Economy
IJERTV10IS080157
www.ijert.org
338
single-use plastics to maximize the public good, thereby supporting environmental projects or boosting local recycling with the funds and creating jobs within the plastic recycling sector with seed funding.
-
Enforce the measure chosen effectively, by ensuring there's clear allocation of roles and responsibilities.
-
Monitor and adjust the chosen measure if necessary, update the public on progress.[3]
Adoption of Circular Economy: It aims is to eliminate waste, not just from recycling processes, but throughout the lifecycles of products and packaging. A circular economy aims to maximize value and eliminate waste by re-designing of materials, products and business models. The goal is not just to re-design for better endof-life recovery, but also to minimize the use of raw materials and energy through a restorative system. In a circular economy, the aim is to maintain the value of products and materials for as long as possible. Waste is minimized and resources are kept within the economy when a product has reached the end of its life, to be used again to create further value. [3]
list of acceptable shapes and sizes.VIofli.t1m0 Iastscuhees08t,hAe uligsut,stt-pe021 product would go down for either recycling or shredding, and the machine hands the consumer a voucher to be encashed at any of the store. The machines could be located
at strategic places, such as malls, hotels, multiplexes, shops, public places, etc. To make these easily accessible by citizens and encourage them to use the same.
Extended Producers Responsibilities (EPR): The producers are required to set out modalities for waste collection system based on Extended Producers Responsibility, involving State Urban
Model-2:
Figure 5-Model 1 ofEPR
Development Departments, either individually or collectively, through their own distribution channel or through the local body concerned. Below mentioned models suggesting producers responsibilities may be considered to improve recycling: [3]
Model-1:
State/ ULB to introduce Buy back Depository Mechanism with a predefined buy back price printed on plastic products, so that consumers will receive a specified amount while returning the used products. The manufacturers/ producers of these plastic products need to set up collection centres with reverse vending or crushing machines and recycling units of adequate capacity to collect such used plastic products/packaging and recycle these. This model not only incentivises consumers to not litter plastic products/ packaging post consumption but also encourages retailers/producers to recycle more. Following are some of the ways in which this model may be implemented:
-
The consumers may use the reverse vending machines which weigh and scan the plastic product to match against a
A national Framework on EPR is proposed where the producers/brand owners is required to contribute to the EPR corpus fund at the central level. This may be an escrow account managed by a Board where government, private and other stakeholders including producers/importer/brand owner can become members. The amount to be contributed by each of the producer will be decided based on the amount of plastic being introduced into the market by the producers. Under the National Framework, funding will be provided to three entities, 1) ULB 2) the assembler/recycler 3) through SPCB for conducting IEC Activities.
-
A committee will be constituted at the central level for overall monitoring the EPR implementations.
-
The State Level Advisory Boards (SLABs), under the Solid Waste Management Rules 2016 at the state level will manage appraisal of the proposals submitted by the ULBs and disbursement of funds to the ULBs, recyclers and for IEC activity.
-
Representatives of producers/ importer/ brand owner will be a part of SLABs.
-
Monitoring mechanism will be established for timely implementation of projects or allotment of pre- defined
IJERTV10IS080157
Figure 6-Model 2 of EPR
www.ijert.org
339
items to recyclers or assemblers. [3]
Plastic Credit:
-
A producer is not required to recycle their own packaging, but to ensure that an equivalent amount of packaging waste has been recovered and recycled to meet their obligation.
-
Producers are mandated to acquire evidence of recycling or recovery (Plastic Credit) from properly accredited processors (recyclers, W2E, plant operators, cement co- processors, users utilizing plastic in road).
-
Producers and processors or exporters may exchange plastic credits for a financial transaction at a price or other terms as negotiated between them.
-
The producers can exchange credits from processors that have been specifically accredited for this purpose by CPCB. The accredited processors therefore receive additional funding for every tonne of packaging waste they reprocess and have an incentive to acquire further tonnage, thereby driving up recovery rates.
-
The system is designed to ensure funding may be directed to remove bottlenecks in the material recovery chain through market corrections. Market would correct itself and guide funding to sources such as material collection, sorting, reprocessing or supporting end use markets. Hence, businesses will have incentive to support long term investments to support their efforts.[3]
India. This paper gives an overvieVwol.a1b0ouIstsucuer0r8e,nAt upgoulisct-ie2s021 and its insufficiency to meet the over-exploitation and consumption of plastic. The various recycling technologies of Plastic solid waste (PSW), treatment and recovery, one of which constitutes mechanical recycling which has certain disadvantages considering the cost, dependency on type of polymer-based plastic, its condition and suitability as well as intense energy consumption. Hence it paves the way to adopt chemical recycling process looking upon the cost effectiveness, eliminates sorting of waste plastic, recovery of valuable petrochemicals feedstocks and produces reusable energy in the form of heat, steam, etc. It is sufficed to say we require a more stringent integrated and strategic waste prevention framework to effectively address wastage related issues. We not only have to create a system, but also implemen major policies with a futuristic approach to curb the increase of single use plastics. The paper has even briefly mentioned the roadmap of the government, that will be practiced to minimize dumping of plastic, rather recycle plastic and motivate private and public organisations to adopt such policies. Policies which will consolidate the waste management system in India, which is still lacking by great margins. Plastic as a whole cannot be eradicated, but better waste management systems, government policies and recycling techniques, can help us and the environment in the long run.
REFERENCES
CONCLUSION :
Figure 5-Plastic credit
-
P. A. O. Samuel Asumadu Sarkodie, Impact of Covid- 19 on waste management, Environment, Development and Sustainability, 2020.
-
T. M. Adyel, Accumulation of plastic waste during COVID- 19, Science, vol. 369, pp. 1314-1315, 2020.
-
V.K.Jindal, Ministry of urban affairs, March 2019. [Online]. Available: www.mohua.gov.in.
-
Centre for Science and Environment, September 2020. [Online]. Available: www.cseindia.org.
-
D. Mohanty, Plastic recycling in Indian perspective, UNIDO.
-
Vikaspedia, 2016. [Online]. Available: https://vikaspedia.in/energy/environment/waste- management/plastic-waste-management-rules-2016.
-
N. G. Tripathi, Stratigies for controlling plastic pollution, in
Researchgate, 2019.
-
D. R. K. S. Tirthankar Banerjee, Plastics waste management in India: An integrated solid waste management approach, 2014, pp. 978-981.
-
P. L. J. B. S.M. Al-Salem, Recycling and recovery routes of plastic solid waste (PSW): A review, Waste Management, p. 26252643, 2009.
-
M. C. S. Dr. Raveesh Agarwal, Waste management initiatives in India for human well being, European Scientific, 2015.
-
M.L.Mastellone, Thermal tratments of plastic wastes by means of fluidized bed reactors, 1999.
-
N.Hovarat, Study of polyethylene thermolysis and polyethylene oil hydogenation, 1996.
The sudden struck of Covid-19 pandemic, has exponentially increased the consumption of single use plastics which has deeply impacted the environment and wholly deteriorated the plastic waste management system in
Vol. 10 Issue 08, August-2021
-
C. J.F.Mastral, Theoretical prediction of product distribution of the pyrolysis of high density polyethylene, Analytical and Applied Pyrolysis, pp. 427-428, 2007.
-
K. C. M. V. D. P. R. R R N Sailaja Bhattacharya, Challanges and Opportunities in Plastic Waste Management.
-
P. S.M.Al-Salem, The valorization of plastic Solid waste by primary to quaternary routes, pp. 103-129, 2010.
-
M. U.Arena, Fluidized bed pyrolysis of plastic waste, 2006.
-
j.Scheirs, Polymer Recycling, 1998.
-
J. C. I.Vermeulen, Automotive shredder residue, Hazardous material, pp. 8-27, 2011.
-
C. a. J. W. P.H.Wallmann, Hydrogen production from waste, pp. 271-278, 1998.
-
C. R. F.Pinto, Co-Gasification study of biomass
-
G. P. Javeriya Siddiqui, A Review of Plastic Waste Management Strategies, vol. 2, pp. 84-88, 2013.
-
R. Amit Kumar Sahu1, Application of Waste Plastic Materials in Road, 2016.
-
M. U. B. D. H. B. P. Dr. D.S.Vyas, Plasma Pyrolysis : An Innovative Treatment, 2011.